Selecting a centrifuge and rotor can sometimes feel like the easy part when faced with choosing the consumables in which to centrifuge samples. There are many suppliers of centrifuge tubes to choose from, along with many types of tubes (such as round-bottom or conical) in a range of materials (see Figures 1–5). Choosing the right vessel for an individual protocol can therefore be challenging. There are several factors to consider when selecting the correct vessel for each application:
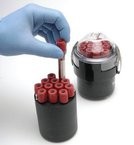
Figure 2 - Vacutainer® blood collection tubes (BD, Franklin Lakes, NJ) loaded in a swinging bucket.
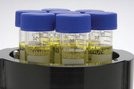
Figure 1 - Nunc (Rochester, NY) 15-mL disposable conical tubes in a swinging bucket rotor.
- Sample compatibility with tube materials
- Volume
- Relative centrifugal force (RCF) required
- Protocols to be used for loading and sample recovery
- Cleaning, sterilization, and decontamination steps between runs.
Understanding individual requirements before a tube or bottle is selected makes product selection much easier, ensuring that the user ends up with exactly the right tube.
Tube chemical compatibility
It is important to evaluate the sample and be aware of each of its components, especially those of a chemical nature. Each container material offers different levels of performance during centrifugation when exposed to different chemicals. The key performance differences between the various vessel materials are as follows:
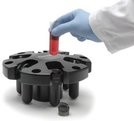
Figure 4 - Polyallomer thin-walled tube with open top.
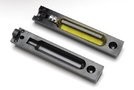
Figure 3 - Ultracrimp ultracentrifuge tube (Thermo Fisher Scientific, Asheville, NC).
- Polycarbonate: a harder material that can therefore typically withstand higher g-forces, but is not compatible with common laboratory chemicals such as alcohol and acetone. If a polycarbonate vessel is exposed during centrifugation to these chemicals, it could potentially fail.
- Polypropylene: compatible with alcohol and acetone, but softer and therefore not always rated to the higher g-forces.
- Glass: a good alternative when using organic solvents, but does not withstand the very high g-forces.
- PTFE: also a good alternative when using aggressive solvents, but has speed limitations based on temperature and rotor configuration.
All major centrifuge manufacturers and vessel manufacturers provide chemical compatibility guidelines, and it is always advisable to check these before buying. The Appendix provides a more detailed comparison of vessel materials.
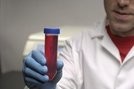
Figure 5 - Nunc 50-mL disposable conical tube.
Volume
The desired working volume should be determined up front. This is limited by the rotors the user has access to and is sometimes dictated by the protocol being used. The general rule for safe centrifuge vessel use is that the tube or bottle should be filled at least 75%. In some cases, such as with ultracentrifuge tubes, it is required that the tubes be filled completely to prevent failure. Using a bottle less than half-filled to capacity can lead to high levels of material stress and can result in bottle failure. The user should know the recommended fill levels as advised by the tube supplier, and should comply with those levels. If the sample volume is smaller than the available rotor capacity, reducing adapters are available for most rotors from the manufacturer. Adapters allow a smaller-volume tube to be run at the appropriate fill volume, thus preventing accidents.
RCF required
Closely related to volume and chemical compatibility is the g-force at which the bottles and tubes will be centrifuged. All bottles tested for centrifugation have a maximum speed rating. Vessels run at speeds higher than the recommended rating can fail, resulting in sample loss and potential damage to the centrifuge and rotor. Most protocols specify a speed either in revolutions per minute (RPM) or relative centrifugal force (RCF), measured in “×g.” It is extremely important to understand the difference between the two, since RPM changes with the specified rotor and is dependent upon its radius. RCF is a constant and represents the actual gravitational force being applied independent of the rotor. Therefore, users should verify the maximum speed for their vessels and ensure that the required speed does not exceed this rating. The material of the vessel provides some indication as to its speed capability.
Protocol
Table 1 - Sample recovery
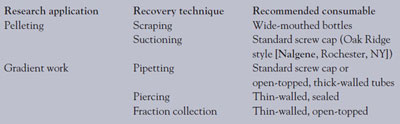
A protocol plan for sample loading and unloading should be made. Important questions to ask include: Will the user be layering sample with a pipet or pouring in large volumes from a beaker? There are several types of bottle openings, from wide-mouth (~70 mm) for large volumes to very small openings (~3 mm). More important is sample recovery (see Table 1). What is the method for sample recovery: pouring off, scraping out, suctioning off, pipetting off, or drawing off the sample with a syringe? The techniques for sample recovery are varied, but many tubes are designed to accommodate specific techniques. Wide-mouth bottles are excellent for scraping out pellets after the supernatant is poured off or suctioned out. Pipetting is commonly used for smaller volumes (50 mL or less). Standard screw-cap or open-topped tubes, such as thick-walled tubes, are ideal for pipetting. Sample removal via a syringe is typically applied when performing gradient work; therefore, collection of the band somewhere in the sample is very important. This requires a thin-walled tube that can be punctured. Knowing the steps in the process not only simplifies the number of products to select from, but also ensures success.
Cleaning, sterilization, and decontamination
Sometimes, the manner in which vessels are treated between centrifugation runs is more relevant to the selection of centrifugeware than what is happening during the run. It is important that the user clearly identify what is needed between runs:
- Basic cleaning with a mild detergent
- Autoclaving (at what temperature and for how long?)
- Chemical decontamination utilizing commercially available disinfectants.
In all cases, vessel manufacturers provide chemical/treatment resistance guidelines. It is important to check these before a final decision is made.
Preventative measures
After all of the necessities have been identified, a buying decision has been made, and the product is in the laboratory and is being put into use, how can the life of the product be maximized? The number one cause of damage to adapters, rotors, and centrifuges is vessel failure. Most frequently, the root cause of the failure is overuse or misuse. To prevent this from occurring, there are several best practices that can be implemented:
- Always inspect the bottles before use and remove from service anything that looks suspect (i.e., discoloration, crazing, spots that do not come off, scratches, etc.).
- If the vessel has O-rings in the lid, always check them for cracks or compression. A worn-out O-ring will leak and could result in sample loss as well as potentially damage the vessel and, in extreme cases, cause centrifuge damage.
- If the vessel has a lid, always read and follow the instructions for assembly. Ensure that all of the parts required to seal and use it properly are present.
- If the vessels are shared, know who is using them and that they are being used properly.
- Replace vessels routinely, and remember: Centrifuge vessels are consumables and must be replaced regularly or failure is imminent. Some vessels are single use, and some are good for multiple uses, but using any vessel until it fails is unsafe.
A centrifuge is a serious investment, and it is critical that users understand their individual needs before they purchase their consumables. Once the selection has been made, it is vital to understand the product and implement best laboratory practices to enhance the life of the product and reduce potentially hazardous situations.
Appendix: Tube and bottle material summary
- Polypropylene
- Resistant to many common laboratory chemicals but not all organic solvents
- Cannot withstand the high g-forces that polycarbonate can
- Can withstand repeated autoclaving at 121 ºC for 20 min without significant material degradation
- Semitranslucent
- Polypropylene copolymer
- Resistant to many common laboratory chemicals but not all organic solvents
- Cannot withstand the high g-forces that polycarbonate can
- Can withstand repeated autoclaving at 121 ºC for 20 min without significant material degradation
- Semitranslucent
- Polycarbonate
- Nonresistant to bases, ketones, and hydrocarbons
- Can withstand higher g-forces than polypropylenes
- Cannot withstand repeated autoclaving at 121 ºC for 20 min without some material degradation
- Clear
- Glass
- High level of chemical resistance, even to many organic solvents
- Cannot withstand as high g-forces equal to plastics as a general rule
- Can withstand repeated autoclaving at 121 ºC for 20 min without significant material degradation
- Clear
- PTFE
- High level of chemical resistance, even to many organic solvents
- Cannot withstand the high g-forces that other plastics can
- Can withstand repeated autoclaving at 121 ºC for 20 min without significant material degradation
- Semitranslucent
- Temperature-sensitive during centrifugation.
Ms. Goodman is with Thermo Fisher Scientific, 308 Ridgefield Ct., Asheville, NC 28801, U.S.A.; tel.: 866-9THERMO; e-mail: [email protected].