Laboratory scientists have a finite number of work hours to accomplish their required research. The annual cost of a scientist and laboratory space for this research in today’s modern, instrument-intensive laboratory may exceed $250,000 or $120/hr. Due to the high cost and limited time for completion of research, many factors need to be considered to achieve optimal utilization of the scientist’s time. Using a case study from Lundbeck Research USA, Inc. (Paramus, NJ), this article discusses some of these factors, including work flow in the laboratory; quality of solvents used for HPLC separations and how they avoid rework; and how the use of simple, automated devices for status monitoring can eliminate steps and reduce task frequency to save scientists’ time. The potential financial and efficiency impact of saving small pieces of time can be significant when the total of all of these pieces is considered.
The traditional use of solvents in the laboratory involves purchasing and using the least expensive solvents with suitable specifications packaged in 4-L amber glass bottles. At the Lundbeck Research facility in Paramus, NJ, this practice was followed in Analytical (mobile phase) and in Compound Management (pipetting robot tip wash). The solvents were used by HPLC or other instruments by directly connecting the bottles to instruments or pouring the solvents into instrument reservoirs, which was necessary if the reservoir needed to be larger than 4 L. Waste solvents from these instruments were collected in 3-gal containers approved for use with flammable/hazardous liquids in laboratories, but not for the transport of flammable/hazardous liquids by the Department of Transportation (DOT). Waste solvent containers were required to be transported from laboratories, to a centralized waste handling room where they were emptied into DOT-approved containers to be shipped to a regulated hazardous material waste disposal site.
This traditional type of solvent use has inherent inefficiencies. Solvent quality from many manufacturers has lot-to-lot variability and can cause excessive analysis background noise, even though the solvents meet published specifications. This excessive background noise can obscure peaks of interest in chromatograms and necessitate that samples be rerun. Four-liter bottles are typically used as reservoirs for instruments. A scientist must regularly monitor solvent levels to make sure the instrument does not run out of solvent. Pouring solvents into reservoirs larger than 4 L may decrease the frequency with which a scientist has to change the reservoir, but increases the chance of bottle breakage or solvent spillage, and the scientist still needs to regularly monitor reservoir solvent level. Three-gallon waste containers without level monitors require frequent monitoring to eliminate overflow of the waste containers (the container must be lifted because there is no way to see the level). Use of the approved 3-gal waste collection containers means that the scientist has to carry the container to the centralized waste handling room according to company policy. Since the waste collection containers were not DOT approved to ship the hazardous waste, Lundbeck had to pay two waste disposal company employees $60/hr apiece to pour the solvents into DOT-approved containers. These employees also rinse, break, and package 4-L glass bottles for disposal at the same rate.
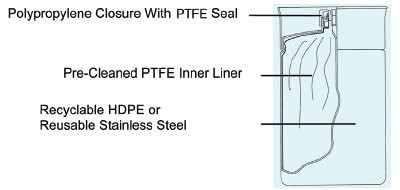
Figure 1 - High-density polyethylene (HDPE) NOWpak.
To address these inefficiencies, Lundbeck decided to purchase organic mobile phase solvents and wash solvents from Honeywell Burdick & Jackson® (Muskegon, MI) to ensure that the required quality is always achieved. The packaging for these solvents was switched from the traditional 4-L amber glass bottles to 20-L plastic NOWpak® containers (Figure 1). A recyclable packaging alternative to glass bottles, NOWpak containers maintain solvent purity (they do not add back group 1A salts as glass can), increase laboratory safety, and maximize efficiency. High-purity solvent is contained in a specially cleaned, inert PTFE liner that is placed inside a rigid HDPE or 304 stainless steel overpak. Both configurations provide virtually breakproof secondary containment for the storage and handling of solvents as recommended by OSHA laboratory standards (29 CFR 1910.1450). The HDPE NOWpak overpak is used in dispensing applications that need intermittent pressurization of less than 10 psig or if the solvent is withdrawn by an HPLC pump or bottletop dispenser. The stainless steel NOWpak II container is designed for applications requiring continuous pressure of less than 15 psig. Solvents packaged in NOWpak containers are suitable for high-purity applications including DNA/RNA processing, LC-MS, peptide synthesis, and pharmaceutical manufacturing.
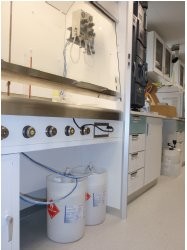
Figure 2 - SDM pushbutton dispensing for solvents from 20-L NOWpaks.
For applications that require solvent reservoirs of less than 20 L, Solvent Dispense Modules (SDMs) from Honeywell Burdick & Jackson were installed to transfer solvents from the NOWpaks. The SDMs provide rapid, unmetered solvent delivery at the touch of a button. They are constructed of inert, solvent-compatible materials for contaminant-free operation. Figure 2 shows a pair of SDMs set up in a laboratory hood for pushbutton, nitrogen-assisted dispensing of acetonitrile and methanol in an analytical laboratory. This approach is clearly less laborious than pouring solvents from 4-L glass bottles.
The NOWpak containers are used in conjunction with the SCAT level sensing system and mobile phase safety caps (Analytical Sales and Products, Inc., Pompton Plains, NJ). The SCAT electronic level sensing system monitors the level of the existing solvent (Figures 3 and 4) with an adjustable sensor in glass or any nonconductive plastic reservoirs without touching the fluids. The critical fluid level is indicated by a beeper and light emitting diode (LED) lamp on the signal box. In the application shown (Figure 3), a low mobile reservoir level is detected by the sensor, and the flashing blue light is turned on to alert personnel inside or outside of the room.
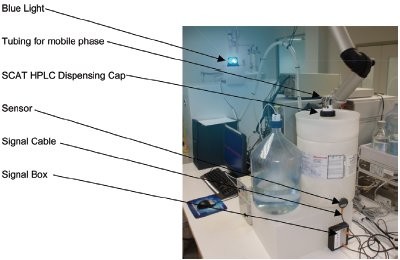
Figure 3 - Electronic level sensing (SCAT) can be combined with NOWpak use.
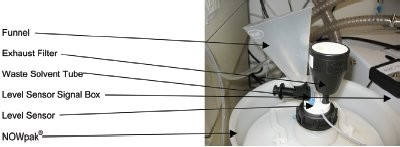
Figure 4 - NOWpaks are converted to DOT-approved disposable waste containers using the SCAT safety cap and connected directly to waste-generating instruments.
After the hazardous material DOT-approved NOWpak containers are emptied, the PTFE liners are removed (and, once dry, are discarded in the regular trash), and the HDPE overpaks fitted with SCAT safety caps are used for the collection of hazardous waste. This 20-L size provides a 70% increase in capacity relative to the usual 3-gal waste can. The SCAT electronic level sensing system is again employed. The adjustable sensor is placed near the top of the 20-L containers. When the fluid level reaches the critical point, the sensor beeps and the LED light turns on. This enables employees to avoid level-checking via lifting the container. The waste-filled NOWpaks are well sealed when recapped and can be safely handled by personnel with minimal training. This allows waste pickup at satellite locations and eliminates the requirement for scientists to transport the full flammable waste safety containers to the central waste collection room. With the waste in NOWpaks, waste disposal employees no longer need to transfer the waste from non-DOT-approved waste collection containers to DOT-approved containers for shipment. The plastic NOWpaks can be incinerated with the hazardous waste at no additional cost.
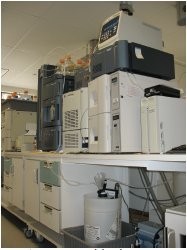
Figure 5 - A NOWpak-based waste container
used in combination with an UltraPerformance LC® (UPLC®, Waters Corp., Milford, MA) with a mass spectrometer and other detectors.
SCAT safety caps are constructed of pure PTFE and PE for high chemical resistance against aggressive organic solvents. The safety caps may be used on solvent reservoirs or containers to collect liquid waste from laboratory instruments. In both cases, the safety caps prevent the escape of hazardous vapors. Integrated air valves with filters, exhaust filters, sealed funnels, and fixed tubing connected to the safety caps keep the containers sealed, even during extraction or filling with liquids. The caps rotate freely without having to twist the tubes when attaching or detaching them from the containers.
As shown in Figure 4, SCAT safety caps used for waste containers at Lundbeck are configured with ports for waste solvent tubing for the collection of waste. In many cases, these parts are used to connect the waste containers directly to the instruments, as illustrated in Figure 5. Exhaust filters contain a multicomponent carbon granulate to absorb materials evaporating from solvents. Safety funnels are available for transferring noninstrument sources of waste and only open when disposing of waste fluids (when the opening mechanism is released, the waste container closes automatically). A larger funnel is available for rapidly pouring larger quantities of waste solvent; this feature permits the waste containers to be used in more general settings such as the synthetic laboratory, as shown in Figure 6. SCAT fluid-level monitoring equipment is integrated with the safety waste cap to eliminate the periodic manual monitoring of fluid levels by laboratory scientists to prevent overfilling waste containers. Full containers are simply labeled by scientists for transport to the central waste collection room. Since the waste is contained in DOT-approved packaging, it can be transported to the waste collection room by minimally trained cleaning personnel.
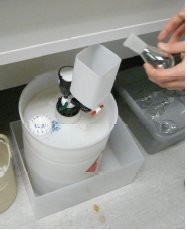
Figure 6 - General bench chemistry waste collection.
Conclusion
Among the keys to success of Lundbeck’s program are quality, automation, and development of human work flows that are both friendly and efficient. The program utilizes high-quality solvents, SCAT safety-sealed caps and level-sensing systems for solvent reservoirs and waste containers, NOWpaks for solvent packaging and subsequent use of overpaks for organic waste disposal, Solvent Dispense Modules for dispensing solvents into glassware, and a labeling system for alerting laboratory cleaning personnel as to which waste containers are ready for transport to the central waste collection room. Overall, the program promotes:
- Safety
- Solvent vapors are not able to escape and enter room air.
- Waste container overflow is eliminated.
- The risk of dropping and breaking 4-L solvent bottles is prevented.
- There is no hazardous waste spillage during transfer from non-DOT-approved containers to DOT containers.
- Improved employee job satisfaction
- Scientists no longer need to frequently monitor reservoirs and waste containers.
- Scientists are not required to transport full waste containers to the central waste collection room.
- Highly trained scientists can better focus on converting data to high-impact results, thereby creating more opportunity for themselves and hence value for the company.
- Less risk of analysis or equipment failure
- Refilling is reduced, as is the risk of solvent reservoirs becoming empty during analysis.
- Background noise is decreased during analysis.
- Human time and money saved
- Reservoirs and waste containers no longer have to be monitored frequently.
- There is no need to transfer waste to DOT-approved transportation containers for shipment to a disposal site.
- The cost of purchasing some DOT-approved transport containers is eliminated.
- The cost of 4-L bottle disposal and the packaging for those bottles is removed.
- Scientists can discontinue many laborious tasks, allowing them to spend more time converting data to critical research results.
- Cost analysis using Lundbeck Research USA as an example suggests that approximately 50% savings in the price of solvent can be achieved using the combination of techniques described above. For the more expensive end of the range of common solvents, it is estimated that 30–35% results from reduced cost of solvent (relative to 4-L bottles) and 15–20% from human time saved due to the streamlined work flow. For the least expensive solvents, most of the savings result from streamlined work flow. With these levels of savings, the investment in solvent dispensers, level monitoring sensors, and custom waste caps can be readily recouped in 2–6 months, depending on the solvents chosen.
Mr. Westra is Technical Service Chemist, Honeywell Burdick & Jackson®, 1953 S. Harvey St., Muskegon, MI 49437, U.S.A.; tel.: 231-725-6262; fax: 231-728-8226; e-mail: [email protected]. Mr. Han is Senior Research Scientist, Analytical Chemistry; Mr. McCoy is Principal Scientist, Laboratory Automation; and Dr. Hayward is Director, Analytical Chemistry and Laboratory Automation, Lundbeck Research USA, Inc., Paramus, NJ, U.S.A. Ms. Isom is Vice President, Analytical Sales and Products, Inc., Pompton Plains, NJ, U.S.A. The information in this article has been thoroughly shown to be reliable at Lundbeck Research USA, but only in its unique drug discovery laboratory environment. Information provided herein does not relieve users from the responsibility of carrying out their own tests and experiments to demonstrate fit for purpose in their own unique laboratory environments. Users assume all risks and liability (including, but not limited to, risks relating to results, performance, patent infringements and health, safety, and environment) for the results obtained by the use of this information.