Traditionally, the de rigueur source of gas supply for most laboratory and process equipment has been the high-pressure gas cylinder. In today’s cryo/bio laboratory, however, significant inefficiencies generated by the need to continuously change out these cylinders are no longer acceptable. In light of this development, a shift toward using cryogenic liquid cylinders is under way. The move is rapidly gaining favor for several de facto reasons—increased performance, safety, and cost efficiency among them.
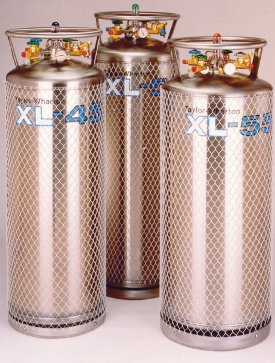
Figure 1 - Changing from high-pressure gas to cryogenic liquid cylinders reaps benefits in terms of increased capacity and higher purity.
The primary justification for the change from high-pressure gas to cryogenic liquid cylinders (Figure 1) rests with payback in two important arenas: increased capacity and higher purity. Because liquid is characteristically more dense than gas, cryogenic liquid cylinders have a capacity that is 20 times greater than that of high-pressure gas cylinders. Cryogenic liquid cylinders also maintain the higher purity associated with vaporizing liquefied gases such as nitrogen, argon, oxygen, and carbon dioxide.
However, the simple shift to cryogenic liquid cylinders does not necessarily eliminate all of the inefficiencies associated with using high-pressure gas cylinders. As a matter of fact, the use of cryogenic liquid cylinders individually can introduce additional inefficiencies based on the gas losses they typically incur. Using a properly designed automatic switchover such as the IntelliSwitch (CONCOA, Virginia Beach, VA) (Figure 2), however, can virtually eliminate these inefficiencies and provide optimum gas usage from liquid cylinders, while providing a continuous gas supply to the laboratory or process application.
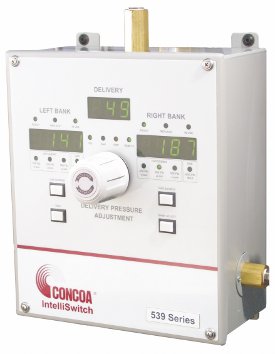
Figure 2 - The IntelliSwitch, equipped with a selectable economizer to accommodate all styles of liquid cylinders, reduces residual gas return considerably to a miniscule 2–3%.
Before moving on to the next phase of discussion, let us first take a closer look at the advantages of shifting to cryogenic liquid cylinders. The primary reason, as mentioned earlier, is gas capacity. The typical 180-L liquid cylinder can replace 16–20 standard high-pressure cylinders. That alone greatly improves efficiency and performance within the laboratory by significantly reducing the need to change out cylinders.
The second reason to change from a gas to a liquid mode is purity. Gases in their liquid state are already in their purest form, and the internal vessel of a cryogenic liquid cylinder is stainless steel. When liquid product is filled into the cryogenic cylinder, there is virtually no chance that the container will add contamination.
The more a gas is transferred, however, the greater the potential for collecting contamination. A stainless steel vessel wall that is smoother than its counterpart high-pressure cylinder wall has less surface area to which contamination can adhere.
The third consideration is safety. With base diameters of 20–26 in., cryogenic liquid cylinders are far more stable than high-pressure gas cylinders with 9- to 95⁄8-in. base diameters. The wider base renders the cryogenic liquid cylinders less likely to be knocked over and result in potential damage or injury.
Now let us take a look at a few of the potential problems associated with using cryogenic liquid cylinders. As mentioned earlier, there can be gas losses. Because they are cryogenic fluids, liquid nitrogen, liquid oxygen, and liquid argon exist at temperatures below –300 °F. Though cryogenic liquid cylinders are extremely well insulated, there is a natural tendency for heat to leak into the vessel in order to warm the cryogenic liquid. As the liquid temperature rises, however, the pressure in the headspace of the cylinder also rises. Because of this pressure rise, a relief valve protects the liquid cylinder. There are three pressure ratings for liquid cylinders: 230 psig, 350 psig, and 500 psig.
The IntelliSwitch is equipped with a selectable economizer to accommodate all styles of liquid cylinders. If the gas supplier delivers a 230-psig liquid cylinder one week, a simple touch of a button sets the proper economizer settings. If a 350-psig liquid cylinder arrives the following week, another button touch changes the economizer setting with no degradation of performance, virtually eliminating vent losses from overpressurization.
Once the relief valve pressure setting is reached, the relief valve will open and release gas to the atmosphere. Assuming that the insulation system is in good condition, the normal evaporation rate for a liquid cylinder is between 1.2% and 2% of remaining product per day. This gas is lost and cannot be used by the system.
A second problem is the inability of the liquid cylinder to maintain pressure because of overdrawing its capacity. To draw gas from the cryogenic liquid cylinder, liquid product must pass through a vaporizer to be converted to gas. The flow capacity from a single liquid cylinder is approx. 350 scfh. If the flow requirement is above this, the internal pressure-building circuit may not be able to maintain the pressure in the liquid cylinder, which can result in a drop in pressure that causes a switchover. Such a situation can lead to prematurely taking the liquid cylinder out of service and returning it to the supplier containing residual product. This is product that has been paid for and not used in the system.
Both the vent losses and the pressure drop that result from overdraw make designing an automatic switchover system for cryogenic liquid cylinders very difficult. Most switchover systems work on the principle of pressure differential, meaning that when the pressure in the primary side drops below a certain preset pressure, the system will automatically switch to the reserve side of the system. This would be fine if the low pressure in a liquid cylinder were an accurate indication of remaining contents.
Because of potential overdraw or lack of pressure-building capability, however, most systems leave 15–20% residual product at the time the system switches to reserve. A smart switchover such as the IntelliSwitch will look back at the apparently depleted cylinder after a period of time to determine if it has rebuilt pressure, indicating that it is not empty. If the depleted cylinder has built adequate pressure, the smart switchover will switch back to draw more product into the system and reduce residual losses. A typical smart switchover can reduce residual return considerably to a miniscule 2–3%.
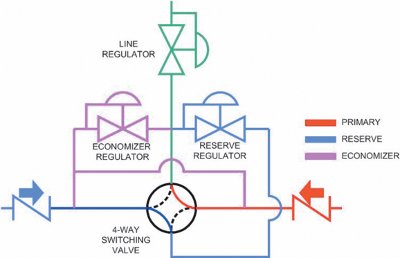
Figure 3 - Conventional systems are set up for a specific style of liquid cylinder; if a cylinder of a different pressure rating is delivered, the economizer will not work. The IntelliSwitch software and the push of a button overcome this problem.
With regard to vent losses, some conventional systems have a backpressure regulator built in to act as an economizer. An economizer is intended to draw gas from the headspace of the reserve bank, preventing the pressure from building to the relief valve setting. Conventional systems (Figure 3) will be set up for a specific style of liquid cylinder (230, 350, or 500 psig). Unfortunately, if a cylinder of a different pressure rating is delivered, the economizer will not work.
An intelligent system such as the IntelliSwitch is designed to compensate for both of the situations that generate gas losses. An intelligent system incorporates a look-back system so that when the primary bank drops to a predetermined pressure, the system switches to the reserve bank to feed the system. After a period of time, the system will look back at the apparently depleted primary bank to see if pressure has built above the switching point.
This is an indication that there is still usable product left in the primary bank. The system then switches back to the primary bank to feed the system. When the primary bank is no longer able to build pressure, the primary bank is deemed empty. Additionally, the reserve bank changes to “primary,” and the depleted bank changes to “replace.” An alarm sounds, if the system is so equipped, only when the system fully determines that the empty primary cryogenic liquid cylinder is in fact truly empty.
In the final analysis, reducing the need to frequently change out cylinders greatly improves efficiency, performance, and safety, all of which validate the smart switchover in the laboratory gas delivery system.
Increasing gas cost efficiencies is also a key advantage. The cost for the typical 180-L cryogenic liquid cylinder that replaces 16–20 standard high-pressure cylinders is only a fraction of the cost of 16–20 high-pressure gas cylinders. Additionally, while each delivery mode routinely has a rental charge associated with the container, the rental costs for a cryogenic container are not 16–20 times that of the high-pressure gas cylinders, adding to the cost savings. Buying in bulk and economies of scale at work here can justify mode and equipment change in the cryo/bio laboratory. It is one that clearly has its rewards.
Mr. Carlucci is Vice President, Sales and Marketing, and Mr. Durkin is Manager of Product Enhancement, CONCOA, 1501 Harpers Rd., Virginia Beach, VA 23454, U.S.A.; tel.: 800-225-0473 (U.S.), +31 30 2672 303 (Europe); fax: 757-422-3125; e-mail: [email protected].