The carbonated beverage and petrochemicals industries are just some areas in which the analysis of volatile sulfur-containing compounds in process streams is a critical quality-control step. Failure to quickly detect and accurately assess or quantify these compounds can lead to contaminated products, damaged equipment, poisoned catalysts and process downtime. This article presents a fast, reliable and robust method for the determination of individual volatile sulfur-containing compounds in gaseous fuels by gas chromatography coupled with pulsed flame photometric detection.
Introduction
Natural gas and other gaseous fuels contain varying amounts and types of sulfur compounds, which are odorous and corrosive to equipment, and can inhibit or destroy catalysts used in gas processing. Between 1 and 4 ppmv of sulfur odorant compounds are typically added to natural gas and other liquefied petroleum gases for safety purposes. These compounds may include ethyl mercaptan (EtSH), methyl mercaptan (MeSH) and tetrahydrothiophene (THT). Some odorant compounds can be reactive and may oxidize, forming more stable compounds with lower odor thresholds. Because even trace amounts of sulfur can be destructive, accurate measurement of sulfur compounds is essential to ensure proper gas processing and monitor odorant levels for public safety.
Analysis of sulfur compounds is challenging due to their reactivity and instability during sampling and analysis. Laboratory equipment must be inert, well-conditioned and passivated with a gas containing the sulfur compounds of interest to ensure reliable results. Another challenge can be the separation of some sulfur compounds from their hydrocarbon matrix. Hydrocarbons can produce a quenching effect on sulfur detection as a result of the formation of carbon monoxide (CO). The subsequent reaction of CO with free sulfur (S) atoms in the flame generates carbonyl sulfide (COS). Formation of COS in the flame reduces the amount of available sulfur in the flame and reduces the production of the excited state S2* dimers. The emission from the excited state S2* dimer is measured by a pulsed flame photometric detector. Quenching can be minimized by choosing the right analytical column and by optimizing the chromatographic conditions to separate the sulfur compounds of interest from the large volume of hydrocarbons present in a gaseous sample.
Several ASTM methods exist for the determination of sulfur in gaseous fuel using gas chromatography with a sulfur selective detector. Although method operating conditions are similar, the primary difference is the type of selective detector used to identify and quantify the sulfur compounds. The instruments most commonly used for this analysis are the flame photometric detector (FPD), pulsed flame photometric detector (PFPD) and sulfur selective chemiluminescence detector (SCD).
Instrumentation
Figure 1 – 5383 PFPD.Data were acquired using the S-PRO Select GC equipped with the 5383 PFPD (Figure 1) (OI Analytical, College Station, Texas). Samples and standards are introduced into the GC column via an automated air-actuated six-port valve housed in a heated oven through a low-dead-volume split/splitless volatiles interface. The sample pathway resides inside a heated valve oven and is treated with Sulfinert coating (Restek, Bellefonte, Penn.) to minimize adsorption of sulfur on the system surfaces.
An air/hydrogen mixture at a flow rate that does not produce continuous combustion is used by the PFPD. The combustor is filled with a gas mixture; the flame is then ignited and propagates through a combustor until all the fuel is consumed. This cycle is repeated continuously at a rate of 3–4 Hertz. The differences in specific emission lifetimes combined with the kinetics of the flame provide information on time and wavelength that can be used to improve the PFPD’s selectivity and decrease the observed noise to enhance selectivity and sensitivity. The propagating flame uses low combustible gas flow rates, increasing the relative analyte concentration. Constant pulsing of the flame also produces a “self-cleaning” effect that reduces system maintenance, decreases downtime and eliminates coking problems commonly encountered with other sulfur selective detectors.
In comparison to standard FPDs, the PFPD offers unambiguous sulfur recognition as a result of improved selectivity against hydrocarbon matrices, lower detection limits and equimolar sulfur response. Since it gives an equimolar response for sulfur compounds, any unknown or uncalibrated peak in the chromatogram can be quantitated using the S response of a calibrated compound. This permits total sulfur content in a sample to be calculated from the total of individually quantified components.
Standards are generated using permeation tubes held at constant temperature in a permeation tube oven. These tubes contain a pure compound sealed inside a wafer or tube device that diffuses across the permeation membrane at a defined rate and uncertainty range at a given temperature. The permeation tube oven is held at a constant temperature to produce a constant diffusion rate. Standard concentration is varied by changing the gas-diluent flow through the permeation tube oven.
Experimental
Instrument operating conditions are shown in Table 1. The PFPD was tuned for optimum sulfur response, configured for sulfur and hydrocarbon detection, and was run in the linearized mode (square root on). Simultaneous, mutually selective sulfur and hydrocarbon chromatograms are produced from a single detector using the dual gate capability of the 5383 PFPD. A FlexStream gas standards generator (KIN-TEK, La Marque, Texas) was used to calibrate the instrument. Standards were generated using hydrogen sulfide (H2S), carbonyl sulfide (COS) and methyl mercaptan (MeSH) permeation devices and a permeation tube oven held constant at 35 °C. Concentrations were varied by changing the nitrogen flow through the permeation oven from 200 mL/min to 3600 mL/min. Eight calibration points were generated. For H2S the calibration range was 0.104 to 1.882 ppmv, for COS 0.116 to 2.081 ppmv and for MeSH 0.040 to 0.723 ppmv. GC software was used to generate calibration curves for the compounds listed. Two natural gas samples were analyzed (Figures 2 and 3).
Table 1 – Instrument configuration and operating conditions S-Pro Select GC
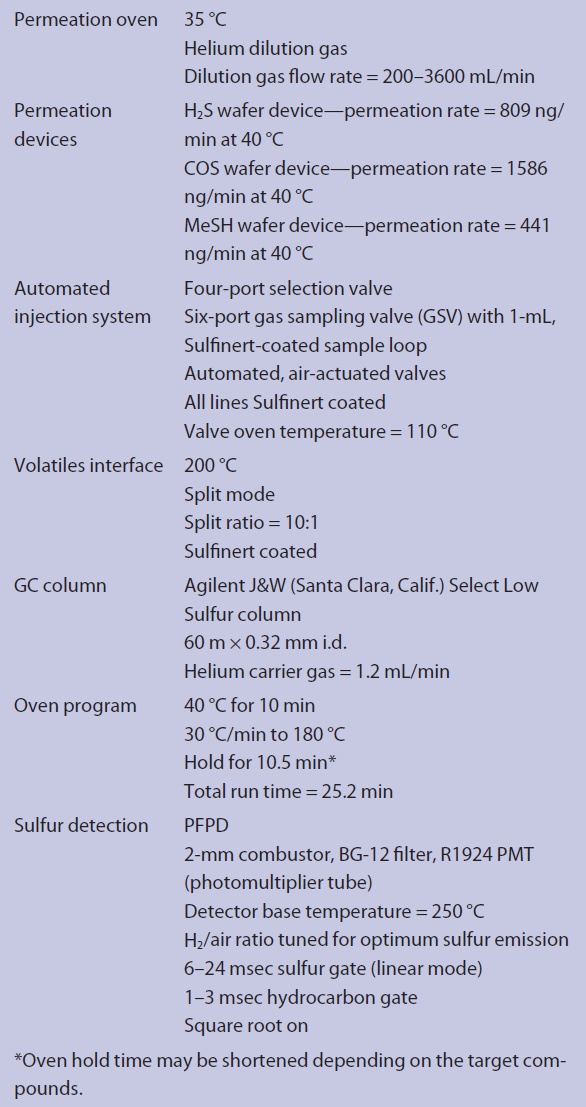
Figure 2 – Natural gas sample 1 (obtained from DCG Partnership, Pearland, Texas).
Figure 3 – Natural gas sample 2 (obtained from DCG Partnership, Pearland, Texas).Results and discussion
The S-PRO-Select GC with 5383 PFPD and Select Low Sulfur column provide a fast, reliable method for the analysis of sulfur in natural gas and other gaseous fuels. All key sulfur compounds were well separated from the methane hydrocarbon matrix (Figures 2 and 3). Two samples of H2S and COS were also analyzed. One sample was in a 50/50 ethylene/ethane mix and the other was in a 50/50 propylene/propane mix. The difficult separation of H2S from ethylene/ethane was achieved using the Select Low Sulfur column.
An H2S peak typically elutes between the ethylene and ethane peaks for many matrix concentration levels found in gaseous fuels. Some coelution of H2S may occur as the matrix concentrations increase above 50% ethylene. COS was well separated from the propylene peak. These separations are important because they demonstrate that the column is flexible enough to be used in several matrices, with no need to make significant changes to the chromatographic conditions. Ultimately, the matrix concentration ranges can be balanced with the required sulfur sensitivity and GC split ratios to optimize performance for various types of analyses. Calibration was performed with the FlexStream gas standards generator (Figure 4). Linearity was established with a correlation coefficient of 0.999.
Figure 4 – Linear calibration curve for three sulfur compounds.Repeatability study
A repeatability study was performed by analyzing 20 replicate injections of the same sulfur standards used for the calibration, with a flow rate of 1000 mL/min through the permeation oven.
Concentrations and %RSD were as follows:
- H2S at 0.376 ppmv—%RSD of 3.88%
- COS at 0.418 ppmv—%RSD of 3.34%
- MeSH of 0.145 ppmv—%RSD of 5.84%
Additional reading
- ASTM Standard D6228, Standard Test Method for Determination of Sulfur Compounds in Natural Gas and Gaseous Fuels by Gas Chromatography and Flame Photometric Detection.
- OI Analytical Application Note #3671, Determination of sulfur in natural gas by ASTM Method D 6228-11 using a pulsed flame photometric detector (PFPD).
Cynthia Elmore is GC product specialist, and Michael Duffy is director of operations and former GC product manager, OI Analytical, P.O. Box 9010, College Station, Texas 77842-9010, U.S.A.; tel.: 979-690-1711; e-mail: [email protected]; www.oico.com. The authors wish to acknowledge the following: Agilent Technologies—analytical column; DCG Partnership—natural gas samples; and KIN-TEK—permeation diluter and permeation devices. Sulfinert is a registered trademark of Restek Corporation.