Oligomers and monomers that react and polymerize to form a rigid network with elevated temperatures are called thermosets. Thermosetting oligomers have been used for several decades to produce composite materials that have superior strength and reduced weight in comparison to metals. A question often heard is: "What is the fastest curing profile that I can use and still get superior polymer properties, i.e., complete cure?"
The curing reaction
Cross-linking reactions are exothermic.
In general, the temperature of the reaction,
the reaction rate, and the reaction
enthalpy (heat of reaction) are the main
points of interest. During the reaction, the
viscosity, density, and the modulus of elasticity
increase due to an increase in the
molar mass and cross-linking.
The cross-linking process is complex
because different reaction steps are
involved. Basically, the growth of the
polymer structure can be divided into two
mechanisms of chain formation: 1) stepwise
growth through elementary reactions
of two functional groups, and 2) chain
growth through the attachment of monomers
to the cross-linking polymer.
In the first process, a covalent bond is
created through the reaction of two
coreactive centers and thus joins monomers,
oligomers, and macromolecules
together. The structure of the polymer is
mainly determined by the functionality
of the monomers and the molar ratios of
the coreactive centers. In the second process,
only monomers are attached to the
chain, and the structure of the polymer
is determined by the functionality of the
monomer, by the ratio of the reaction rates
between initiation and growth, and by the
concentrations of monomer and initiator.
The formation of a thermoset can take
place between monomers with a functionality
of three or more. In the fully reacted
polymer network, practically all the constituent
units are incorporated covalently
in the three-dimensional
structure. At the gel point, the infinite network becomes
apparent for the first time.
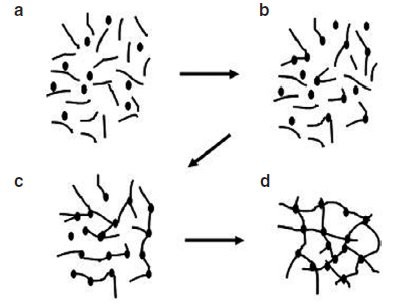
Figure 1 - Schematic diagram illustrating the steps involved in cross-linking: a) starting resin material with low-molecular-mass monomers (A-stage monomers); b) linear growth and branching (B-stage material or prepolymer); c) gelled, but still incomplete network; d) fully cured polymer (C-stage thermoset).
As shown in Figure 1, the reaction begins
(region a) with the formation of larger
molecules that may also already be
branched. This so-called prepolymerization
is a way to increase the molecular
weight of a polymer to some intermediate
value so that there are still enough
residual reacting sites to further react in
a curing environment. Some reasons for
prepolymerization
are to increase the
viscosity, decrease the toxicity, and
reduce reactivity for control of gelation
time.
Stoichiometric considerations are
important for optimum curing conditions.
However, in reality, the mixing
ratio may be adapted due to steric
hindrance of reacting species to come
together and react. Side reactions
and chain-stopping contaminants
may reduce the calculated number of
reactive sites. Cross-links are formed
between the chains via trifunctional
and multifunctional groups. An elastic
gel is then formed from the viscous
liquid through cross-linking. In
the gel, the cross-linking continues
until the network density is practically
complete or the reaction comes to a
stop due to vitrification.
When two or more polymer networks are
formed in a cross-linking reaction, the term "interpenetrating polymer network" (IPN)
is used. IPNs are combinations of two or
more entangled cross-linked polymers. Ideally,
only one glass transition is observed.
Time-temperature transformation
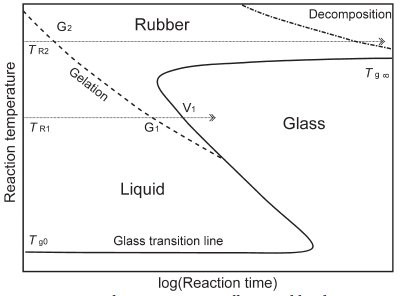
Figure 2 - The curing process illustrated by the TTT diagram. Shown are the three states of the material on curing: liquid, rubbery elastic material, and glass. The continuous S-shaped curve shows the time it takes for the resin to vitrify when the reaction is performed at an isothermal temperature, TR.
The three different physical states that can
occur in curing are usually displayed in a
time-temperature-transformation (TTT)
cure diagram (Figure 2). This is a plot of
temperature versus the logarithm of reaction
time. It shows the state of the resin after a
certain reaction time at a reaction temperature
TR. Below Tg0, the resin is in the glassy
state and the reaction is practically blocked.
At a curing temperature TR2, the gelation
line (dashed line) is reached after
a relatively short time, the material gels
(gel point G2) and is transformed to the
rubbery state, and cross-linking continues
until curing is complete. The curing
temperature is thus always higher than the
maximum possible glass transition temperature Tg∞. With longer reaction times,
decomposition can begin.
If a reaction temperature of TR1 is chosen, it takes
somewhat longer for the gel point at G1 to be
reached. Cross-linking continues in the rubbery
elastic material until vitrification occurs at V1.
The glass transition temperature increases due to
continued cross-linking until it reaches the reaction
temperature. At the transition to the glassy
state, the reaction stops. The material is hard, and
it seems as if curing is complete.
If the temperature TR1 of a thermoset cured in
this way is exceeded during use, softening occurs,
which can lead to a material defect. In the glassy
state, the reaction is not completely hindered but
can still proceed at a very low rate. The properties
of the material are clearly not stable.
The continuous S-shaped line therefore shows when
the resin vitrifies at an isothermal curing temperature.
Figure 2 thus characterizes a reactive resin system with
regard to reaction temperature and reaction time.
From a technical viewpoint, the gelation time, pot
life (processing time), and storage time at a particular
temperature are of great importance, irrespective of
whether cross-linking is started catalytically, through
exposure to light or temperature increase.
At the gel point, the viscosity increases markedly
(theoretically infinitely) and thereby ends the possibility
of using the resin (casting, coating, pumping)
(the B-Time according to DIN 16916).
The pot life is also related to the gel point. It characterizes
the time available to process a reacting
thermosetting resin formulation under normal conditions
after the start of the reaction before the mixture
becomes intractable or otherwise difficult to process
(e.g., residence time in a molding machine for trouble-free
molding and defect-free parts).
Shelf-life can mean an arbitrary time for practical
storage of a thermoset system, either a one-component
system or a system after mixing the components.
Shelf-life is also used to describe the storage stability
of unmixed components. For example, some curing
agents will lose reactivity due to the uptake of atmospheric
moisture.
As already indicated, the handling, processing, and
properties of a thermoset depend strongly on gelation
and vitrification. A resin in the previously reacted,
vitrified state can be easily stored and simply heated to
start curing. This simplifies the handling and processing
of resins because resin and hardener do not first
have to be mixed in the right proportions. The influence
of temperature on curing provides another practical
production control mechanism, the concept of
staging: In the A-stage, the thermoset is ready to react
(i.e., after mixing, but cross-linking has not begun); then it goes through the B-stage as time and
cross-linking
progress. Often, the process
is stopped by lowering the temperature sufficiently
to achieve an inactive period (up
to one year), for example, for reactive coating
powders or tacky adhesive tapes for easy
application. The C-stage represents the fully
cross-linked part in its final configuration.