Suppliers of compressed gases go out of their way to deliver gas products that meet customer requirements for purity, mixture accuracy, and other specifications. Most gases are delivered in conventional high-pressure cylinders, while other gas products are delivered in bulk or small bulk containers and dewars. Whatever the means of delivery and storage, these gases are handled, regulated, and distributed by the user. In the process, the gases are exposed to different equipment and systems that can either maintain or degrade gas purity.
End-user gas handling systems can be as simple as a regulator, valve, and tubing; or as complex as a site-wide gas management system. They can also be a combination of the two. Whatever the configuration, the impact of the delivery system on gas quality is often underestimated, or worse, sometimes not even considered.
In addition, the use of hazardous gases such as acetylene, hydrogen, and chlorine can create an unsafe condition if the proper equipment is not used. Further, failure to consider the consequences of crossover usage of hardware with flammables, oxidizers, and corrosives can lead to serious problems.
This article focuses on gas pressure regulators. Materials of construction, selection criteria, general precautions, and other issues are discussed in the context of safety and gas purity. Other articles by the authors deal with additional system elements.
Regulators
Regulators are used in gas delivery systems to reduce the pressure from a high-pressure source to a working pressure for use. The right regulator will maintain gas purity and deliver the gas safely to downstream gas delivery components, and ultimately to the point of use. Many different criteria need to be taken into account when selecting the right regulator for an application.
Purity
The first step in choosing a regulator is to consider the purity level that is required for the application. Typically, requirements fall into three categories: 1) general purpose (4.0 or 99.99% pure or lower), 2) high purity (5.0 or 99.999% pure), and 3) ultrahigh purity (6.0 or 99.9999% or higher).
If, for example, an application requires high-purity gas, the use of general-purpose regulators should be avoided; only high-purity (or better) regulators should be used. As a minimum, regulators used in delivery systems should be cleaned (by the supplier) for oxygen service to CGA G4.1/ASTM G93 guidelines. This will ensure both a minimum level of cleanliness and safe usage with high-pressure oxidizers such as oxygen and nitrous oxide. (Note that economy-grade regulators and gases are not suitable for laboratory use, and are not considered in this article.)
Body type
Regulator bodies may be forged or machined from barstock. Forging is used only with brass, whereas barstock is used for brass, stainless steel, and other materials. Barstock bodies are preferred for higher-purity applications for the following reasons:
- Smaller internal volume: easier to purge, facilitating removal of moisture and impurities
- Smoother internal surfaces: do not retain as many contaminants, such as oxygen and moisture
- Tight grain structure of metal: The cold drawing process produces a very tight grain structure that is more resistant to adsorption of moisture and impurities.
Materials of construction
Brass is the most common material used in pressure regulators. Other materials, notably stainless steel, are used when gas compatibility with brass is an issue, or in higher-purity applications.
Inert gases and flammables are generally compatible with brass and most materials. Gases that have corrosive properties may require corrosion-resistant materials for all wetted parts. The most common corrosion-resistant material used for these applications is 316 stainless steel, although Monel (Special Metals Corp., Huntington, WV), Elgiloy (Elgiloy Specialty Metals, Elgin, IL), and Hastelloy (Haynes International, Inc., Kokomo, IN) are also sometimes used. Most gas companies have material compatibility charts on their Web sites (see Figure 1).
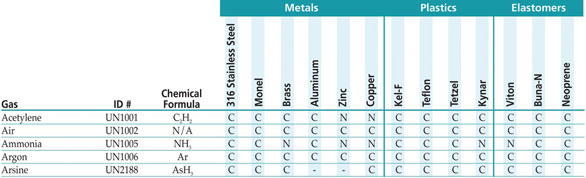
Figure 1 - Example of a material compatibility chart (Figures 1, 2, and 3 courtesy of MATHESON, Montgomeryville, PA; source: MATHESON Gas Catalog.) Kel-F®: 3M Co. (Maplewood, MN); Teflon®, Tetzel®, and Viton®: DuPont (Wilmington, DE); Kynar®: Arkema, Inc. (Philadelphia, PA).
Forged brass bodies are typically used in the lowest-cost regulators, and are suitable for use with the lowest-purity gas, 4.0–4.5, depending on the type of diaphragm (neoprene or metal).
Brass barstock bodies have smaller internal volumes, and smoother internal surface finishes, in the 25-Ra range. Brass barstock bodies with stainless steel diaphragms can maintain 5.0 purity of noncorrosive gases.
Stainless steel should be chosen for semicorrosive or corrosive gases or mixtures, or for higher-purity requirements. Stainless steel regulators are made from barstock material, and can be machined from a standard of about 25 Ra down to 10 Ra or lower for ultrahigh-purity (UHP) requirements. Purity levels of 5.0–6.0, depending on the type of connections, can be expected.
For highly corrosive gases, Monel or Hastelloy may be used. These materials provide a higher degree of corrosion resistance, but at a higher cost. While these materials are more corrosion resistant than stainless steel, they cannot be supplied at the lowest Ra surfaces finishes, and are not normally used for 6.0 purity or better.
Delivery of highly corrosive gases at ultrahigh purity is a challenge to the materials. Downstream purification may be used. One’s gas supplier should be consulted.
Regulator diaphragm
In lower-cost regulators, the diaphragm is an elastomer, typically neoprene. A regulator with a neoprene diaphragm should not be used when it is important to maintain purity levels of 4.5 or better. Elastomers can adsorb and diffuse contaminants, and may not be compatible for use with some gases. Metal diaphragms (stainless steel) provide a more secure metal-to-metal seal, are more broadly applicable, and are less prone to adsorption and diffusion of contaminants.