Softening and dropping point determination are established analytical tests that provide quality control for petrochemical products such as lubricating grease. However, to be accurate and comparable, manual/semiautomated quality tests prescribed in IP and ASTM and other standards must be performed in a standardized fashion. Unfortunately, manual processing bears inherent risks, including operator bias. These risks can result in processing inconsistencies that affect test repeatability, which in turn can negatively affect end-product performance.
This article sets out to explore whether modified automated methods, when appropriately applied, can provide enhanced process efficiency, at least equal repeatability, and comparable results to current standard automated methods for lubricant grease testing. To do so, a set of experiments were conducted to compare the effectiveness and repeatability of a modified automated dropping point testing against a common established automated dropping point standard.
The resulting study, Dropping Point of Lubricating Grease, evaluated the need for two controlled heating ramps as prescribed by the IP396 standard. Each standard’s individual repeatability was also reviewed.
As expected, the modified automated dropping point method including a faster, ballistic heating ramp to the start temperature for subsequent dropping point determination was shown to offer better efficiency than the original IP396 standard. Additionally, ballistic heating was shown to provide results comparable to those obtained using slower heating.
Because dropping point test results using ballistic heating were within standard deviations prescribed by IP396, it was concluded that dual controlled heating ramps are unnecessary for dropping point test accuracy of lubricating grease.
Figure 1 – Standardized dropping point cup.Lubricants reduce friction and wear in products like engines. Dropping points, ranging from 80 ºC to >300 ºC, depending on the composition and nature of the lubricant’s ingredients comprising base oil, additive, proportion and thickener, help establish the grease’s maximum usable temperature, typically set 50‒100 ºC below the dropping point.
The dropping point is the temperature at which the first drop of a melting liquid precipitates from a standardized vessel with a defined aperture under controlled test conditions. A standardized cup (Figure 1) is made from hard-chrome plated brass or aluminum and has a cylindrical shape that tapers downward, corresponding to ASTM D 556 shape/dimension requirements.
The automated dropping point detection principle used in the METTLER TOLEDO (Columbus, OH) dropping point DP Excellence systems is based on a patented video-image analysis, schematically presented in Figure 2. The automated process is captured in color video so that it can be followed live as well as saved for later review. Figure 3 shows a video snapshot of two samples being measured simultaneously.
Figure 2 – Detection principle view schematic.
Figure 3 – Dropping point video, event recorded at 276.3 ºC.Experiment setup and sample preparation
Lubricating grease dropping point comparison tests following IP396 were performed on a METTLER TOLEDO DP70. Aluminum dropping point cups conforming to ASTM D 556 with lids and disposable collecting glasses were used.
Sample cups were cleaned with toluene in an ultrasonic bath. Grease was packed using a spatula from the DP70 accessory kit. A metal rod corresponding to ASTM D 556 dimensions was penetrated into the grease sample from a smaller opening at the bottom to make contact at both upper and lower cup peripheries removing a conical section of grease. The smooth, reproducible film inside the cup eliminated undesirable temperature gradient between wall and midsection that form when a cup is filled, which typically leads to a higher drop point or no drop at all (Figure 4).
Figure 4 – Schematic of grease removal process.Comparative testing and results
Eleven commercially available lubricant greases with dropping points from 147 ºC to 280 ºC were tested, each using the methods described below to investigate the influence of pretemperature treatment.
Method A used a temperature ramp of 10 ºC per minute to heat the sample to a defined start temperature followed by a temperature ramp of 1 ºC (2 ºC, samples A‒C) per minute to dropping point. The 10 ºC/1 ºC dual ramp workflow corresponds exactly to IP396 standard requirements.
Method B used a ballistic heating ramp of about 30 ºC per minute to heat the sample to a defined start temperature followed by a ramp of 1 ºC (2 ºC, samples A‒C) per minute to dropping point.
Each test was repeated for 2‒6 softening points that were averaged. Standard deviation was calculated as well.
The comparative tests (Table 1) showed that overall repeatability achieved in the test series of each sample was less than the maximum allowed deviation as defined in the IP396 standard used to assess results. In all tests, no significant difference in repeatability was detected using either method A or B.
Table 1 –Dropping point results using two methods according to IP396
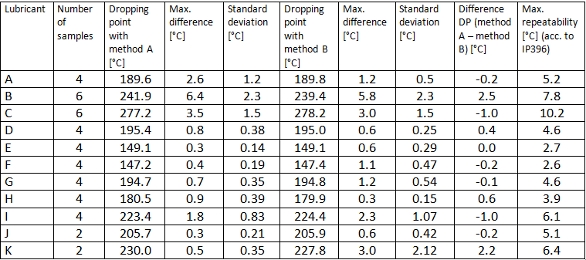
Additionally, there was no significant difference in determined dropping points using method A or B. Again, differences were within the maximum allowed deviation as prescribed by IP396.
Lubricant samples with dropping points >200 ºC showed comparatively higher results variation in the average dropping point achieved with both methods. Presumably, this was due to thermal decomposition.
Conclusion
Based on the results of the comparative testing, it can be concluded that lubricant grease dropping point testing does not require two different heating ramps for accuracy as currently demanded by IP396. A fast, ballistic heating and fully automated method provided comparable results to slower controlled heating. Therefore, automated ballistic heating accelerated processing without sacrificing accuracy and repeatability.
Automated methodology also removed tedious manual tasks, while unambiguous results analysis eliminated operator bias during data interpretation. Therefore, automated detection of the dropping point event itself can be presumed to enhance test accuracy, repeatability, and reproducibility while fostering improved results integrity.
Dr. Hans-Joachim Muhr is the Product Manager for the Melting and Dropping Point Instruments, Mettler-Toledo AG, Business Unit Analytical 8603, Schwerzenbach, Switzerland; e-mail: [email protected]; www.mt.com