Examples of welds contaminated with small quantities of incorrect weld filler metal were recently discovered in fabricated assemblies. The presence of such impurities, which are not detectable using existing nondestructive inspections, can potentially be of major consequence in critical applications. The need to verify welds as free from improper filler metal necessitated the development of a technique that would reliably and nondestructively detect the presence of small quantities of incongruous elements in welds. As a consequence of developing this technique, the following benefits have also been realized:
- Full quantitative elemental analysis of a broad spectrum of weld and base material alloys
- Nondestructive sampling of the weld and/or base materials
- High degree of precision and accuracy for each element of concern
- Very low method detection limit for each element tested
- Acquisition of test results in a reasonable period of time
- Sufficiently straightforward so as to be independent of an analyst’s expertise
- Can be used in difficult-to-reach locations on installed components.
Description of Quantitative Abrasive Test (QAT)
The test is based on abrading a metallic surface with a small piece of very high-purity abrasive paper in order to transfer bits of sample material (on the order of 1–2 mg of material removed over the sample area) to the surface of the paper and return it to the laboratory for analysis. The abrasive paper used for the test was a 600-grit aluminum oxide abrasive on a polyethylene terephthalate backing. It was cut to size with ceramic (zirconium dioxide) scissors. The paper was then applied to a Dremel motorized contour sander (Racine, WI) or other suitable mechanized or manual tool to facilitate the sampling. After sampling, the abrasive paper was trimmed with the scissors to eliminate any trace of possible contamination around the edges where it was gripped by the tool holder, transferred to a 50-mL polyethylene HotBlock™ cup (Environmental Express, Mt. Pleasant, SC), acidified, digested, diluted, and analyzed by inductively coupled plasma-optical emission spectrographic (ICP-OES) techniques. The total number of milligrams of each of 15 elements was determined and totaled, and each element was calculated as a percent of the total.
Depending on the alloy, the total sample amount after trimming ranged from 0.5 to 3 mg of material. With the sample size being so small, it was not tolerant of small amounts of inadvertent metallic contamination from sources other than the actual sample. Therefore, the procedure uses many techniques to avoid outside contamination of the sampling media, such as gloves and scissors proven to be free of metallic elements that may be inadvertently transferred to the abrasive paper, and detailed procedures to limit the sample taken to the exact area desired without inclusion of foreign material from adjacent areas and the general environment.
Validation of QAT: Approach
To validate the technique, seven replicate analyses of five certified standards for each study alloy were performed. These data were then compared to the certified values of each standard for evaluation. The certified standards were purchased from Brammer Standard Co. (Houston, TX), Analytical Reference Material International (Golden, CO), and/or NIST (Gaithersburg, MD). Alloys included two stainless steel alloys (304 and 316), 70-30 copper-nickel alloy, 70-30 nickel-copper alloy, one high-strength steel, and two Inconel alloys (600 and 625) (Special Metals Corp., New Hartford, NY).
Further assessment was performed by sampling and analyzing production welds where reproducibility and compliance to the material’s specification requirements were considered. Fifty-six Inconel 625 production welds were sampled in multiple locations and along the weld and analyzed by the QAT method for a total of 260 determinations. Additionally, three stainless steel production welds were sampled in multiple locations for a total of 16 determinations and analyzed by the QAT method.
Lastly, three sets of welded test mock-ups were prepared where small quantities of several incorrect weld metals were intentionally deposited beneath the correct weld metal to verify detectability using QAT. The first set included six 304 stainless steel specimens contaminated with a controlled quantity of 70-30 copper-nickel alloy and covered with 1–6 beads of 308L stainless steel weld metal. The second set of mock-ups consisted of a series of five 304 stainless steel specimens welded with 308L stainless steel electrode with controlled additions of 70-30 copper-nickel in sizes ranging from small tack welds to full weld beads. The last set consisted of welded carbon steel mock-ups with controlled additions of 70-30 copper-nickel.
Test results
Test results demonstrate that the QAT meets or exceeds those benefits listed above. A discussion of each set of test results follows.
Certified standard testing
Table 1 - Sample QAT data from the analysis of certified stainless steel and Inconel 625 standards
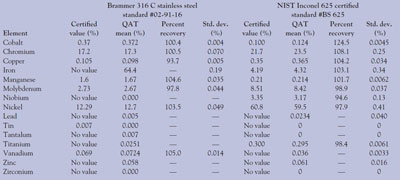
Certified standard testing demonstrates that use of the QAT is suitable for all alloys studied. Example test data are included in Table 1. For each alloy, seven replicate QAT samples were tested.
These results demonstrate that high percent recoveries and low relative standard deviations for the major compositional elements can easily be obtained. As would be expected, however, while the concentration of an element decreases, the percent recovery decreases and standard deviation increases. Nevertheless, even with elements having concentrations between 0.02 and 0.1%, QAT testing showed satisfactory results.
Production weld QAT testing
Table 2 - Sample QAT data for Inconel 625 and 304 stainless steel production welds
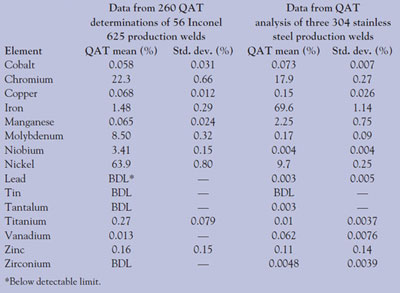
As shown in Table 2, 260 QAT determinations of 56 Inconel 625 production welds and 16 QAT determinations of three 304 stainless steel production welds exhibited very consistent results. This accomplishment is even more significant considering that these samples were taken from multiple welds that were fabricated using different lots of weld filler wire, which vary in chemical composition lot-to-lot.
Mock-up and MDL study: QAT testing
Test results from the analysis of mock-ups demonstrated, without exception, that deposition of a small amount of incorrect weld metal in several material combinations could be reliably detected, even when the small quantity of incorrect weld metal was covered over with six layers of correct weld metal. This result verified the value of the QAT method for nondestructive sampling and detection of small amounts of discrepant material in welds, and by extension, in other metallic items.
Method detection limit (MDL) studies for each element were also performed as part of this testing. To determine the MDL, seven portions of a standard near the estimated MDL were prepared and analyzed. The standard deviations were calculated from these seven sets of analytical results. From a table of one-sided distribution, the value of t for 7–1 (i.e., 6 degrees of freedom) was then selected. At the 99% level, this value is 3.14. The product 3.14 was then multiplied by the standard deviation to calculate the MDL for each element. In this case, a low-concentration synthetic standard was spiked seven times directly on separate pieces of abrasive paper and carried through the entire analytical process. The spike amounts, mean, percent recovery, standard deviation, and MDL values were determined. When calculated on a percent basis, less than 0.05% was easily detected for most elements and some as low as 0.01%. Copper, a major concern if added via use of an incorrect weld filler rod in welded stainless steel applications, can routinely be detected down to 0.013%. Testing resulted in somewhat higher MDLs for the elements tantalum and iron.
Conclusion
The quantitative abrasive test, as presented in this article, may be employed for a full quantitative analysis of a broad spectrum of nonaluminum bearing alloys. It has been shown to be accurate, precise, and amenable to the sampling and testing of production welds. Since this method employs an aluminum oxide paper, the QAT is limited to those alloys that do not contain appreciable amounts of aluminum. Diamond abrasive paper may be substituted for the aluminum oxide paper for the testing of aluminum bearing alloys. Since the development of this method, thousands of QAT samples have been taken in many hundreds of critical welded joints. The analyses derived from the sampling have been demonstrated to be accurate and, as a result, have allowed verification of properly welded joints in a nondestructive manner, avoiding costly and time-consuming destructive sampling and repair, or removal and replacement of suspect joints.
Mr. Dannecker is Supervisor of Chemistry, Mr. Fichtelberg is Principal Welding Engineer, and Mr. Knowles is Analyst, Electric Boat Corp., 75 Eastern Point Rd., Groton, CT 06340, U.S.A.; tel.: 860-433-3533; fax: 860-433-8909; e-mail: [email protected].