Since the laboratory microwave digestion system first became commercially available in the 1980s, sample preparation has become mainstream, and the preparation of samples for atomic spectroscopy has been updated. Over the years, enhancements to the instrumentation have made the systems safer and more effective, especially for digestions of complex samples. Hundreds of microwave methods have been developed for routine analysis, with several found in government official methodologies. Today, several manufacturers produce systems that range from simplistic to more sophisticated.
Most of the current systems share all or most of the following common traits:
- They are batch processes
- They use pressure containers to contain samples that must be assembled
- For control, they rely on the user to group together samples of similar reactivity
- Each sample in a run is treated identically using the same sample method
- Temperature and/or pressure are control functions, with measurements confined to one or a limited number of samples in a run.
While rotors for an increased number of sample vessels have been introduced in the last few years, the actual digestion process has not changed significantly, i.e., batch process, pressure containers that require time and patience to load and unload, and sample grouping to ensure good control because of the single temperature/pressure control, etc., have been retained. Although the existing systems were suitable for the digestion of a restricted number of samples, their use was limited in mainstream, busy analytical laboratories. Other systems, namely, multisample, graphite block digestion systems that can produce good results in slightly longer total digestion and processing times, are more economical.
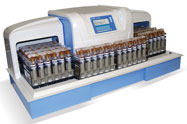
Figure 1 - NOVAWAVE microwave digestion system.
The NOVAWAVE microwave digestion system (SCP SCIENCE, Baie D’Urfé QC, Canada) (Figure 1) was developed for laboratories that handle a large number of samples. These laboratories demand specific features that are not all found in existing systems. The NOVAWAVE microwave digestion system was conceived with the following objectives: full automation, stat samples, simplicity of operation, sample identification throughout the process, significant reduction in human interaction, attention to all safety issues, and ability to abide by existing official methods.
In 2006, company engineers, technicians, and chemists started to develop the technologies needed to create NOVAWAVE in response to the objectives stated above. By 2010, these objectives were reached and six patents have been filed. An additional patent-pending feature is that each sample in a rack can have its own method. This is especially important with the model SA system, in which samples of varying reactivity requiring different methods can be run simultaneously in the same rack. This is a major time-saver for a laboratory with a varied workload.
The following section details how these objectives were achieved.
Full automation
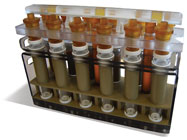
Figure 2 - Twelve-position rack for 50- and 75-mL tubes, equipped with autolock/release mechanism, safety lock, vessel venting system, and 12 microcavities with extensions.
Samples are placed in a 12-vessel rack that travels with up to 14 racks into a tunnel where dynamically formed minicavities are formed (see Figure 2). The doors close and the appropriate method(s) are performed on the samples. After digestion, the rack exits the tunnel and proceeds to the autocooling area where three turbo fans draw air around the vessels and rack. Heat and any fumes exit through a built-in ducting system. After cooling, the rack moves to the autoventing position where the sample temperature is read. If the temperature meets the threshold temperature set in the method, the autoventing process is allowed to proceed. When the rack moves to the next position, it can be removed and samples sent for analysis or allowed to accumulate until all sample racks have been processed.
Stat samples
Stat samples can be placed in a rack which in turn can be inserted in the position directly preceding the tunnel entrance. This ensures that the stat samples will be next in line for processing. Sample digestion data can be transferred immediately to the selected output.
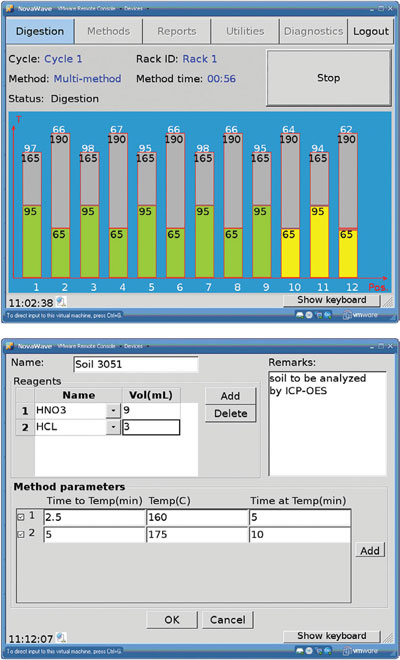
Figure 3 - The most widely used U.S. EPA and DIN methods are preinstalled in the NOVAWAVE software package.
Simplicity of operation
- The software invokes permissible levels of use providing the operator, management, and service personnel access to different areas of the software (see Figure 3). The standard software is supplied with several built-in methods, including many widely used U.S. and international methods, and permits the user to create new copy and/or modify built-in methods. Assignment of methods can be made quickly in one of three ways: by cycle, wherein all samples in all racks in a run are assigned the same method; by rack, in which each sample in a rack follows the same method; or by sample, where samples in a rack can be treated by the different methods. The system stores the following results for each sample: sample identification, method selected, maximum temperature achieved, sample temperature profile during digestion, digestion time, sample weight, and type and volume of each acid/reagent used. This information can be sent automatically to an external computer or LIMS or simply offloaded into a flash memory device.
- Method creation has been greatly simplified; one need only deal with temperature. The user simply programs the temperature to rise to a particular level and holds the temperature for the entire digestion, or holds at a given temperature for a dwell time to allow samples to gradually outgas, and then increases the temperature again. In the latter case, multiple time-to-temperature and time-at-temperature levels can be created for the same method. It is important to note that only temperature and time are necessary to create a method. The user does not have to be involved in power calculations and lengthy temperature calibrations. Each vessel has its own magnetron, continuously variable power supply, and infrared temperature sensor, creating an automatic temperature control and feedback system. Each channel is able to supply continuously variable, on-demand temperature control, without the inconveniences and inaccuracies of older-generation duty cycle systems.
Sample identification throughout the process
Built into each rack is a separate transport rack that enables the user to remove the vessels from the base rack and transport the 12 vessels to a balance to weigh and load samples for each vessel. All 12 positions in the transport rack are identified and correspond to a sample position in the completed rack. To avoid confusion, the transport rack fits only one way into the base rack. For laboratories employing systems that maintain sample identification, a printout of sample identification in bar-code format allows assignment of ID to each vessel position in a rack. IDs can be automatically loaded to the appropriate rack in the software and the sample results followed throughout the process and into reports. After the samples are digested, cooled, and vented, they can be bulked up in the same vessels using the Class A 50-mL calibration line and transported to a special autosampler rack designed for each manufacturer’s ICP spectrometer. The samples are weighed, digested, and analyzed in the same vessel, and sample identification is never compromised.
Significant reduction in human interaction
In standard microwave digestion systems, there are two areas that involve labor-intensive tasks. The first involves the loading and assembling of digestion vessels and then the corresponding unassembling and unloading of the digestion vessels after the digestion process. The vessels are generally held in an outer containment device that is usually assembled and screwed together. The time to load, assemble, disassemble, and unload vessels from their housings typically takes considerably longer than the actual digestion process.
With NOVAWAVE, samples are added to each vessel, which is then inserted in the rack. In one motion, all 12 vessels are sealed using a patent-pending Safety Cap plate with an autosealing/opening system. With the autocooling and autoventing stations as part of the standard automation, these processes are handled automatically.
Safety considerations
Part of the original design considerations of the NOVAWAVE regarded safety. All pressure-related devices (vessels, rack assembly) have been tested for operation at 3× or more the rated pressure. For safety, the tunnel is constructed of 12-gauge Teflon (DuPont, Wilmington, DE)-covered stainless steel, and the Teflon-coated tunnel doors have been designed to blow out laterally in the case of an explosion. Each vessel has a Safety Cap positioned above it and is rated at 500 psi. If pressure greater than 500 psi builds up in a vessel, the Safety Cap will automatically vent, allowing excess pressure to release.
All NOVAWAVE components are made of corrosion-resistant plastic. Exposed metal parts are Teflon coated, and circuit boards are coated to protect the entire instrument from corrosive acid attack and prolong its life. If a tube is missing in a rack, or there is a cracked or ruptured vessel leaking, a detection circuit (patent pending) will sense the increase in the reverse power, causing the system to automatically shut down the individual channel and inform the operator in the resulting report.
Each sample in a rack can have a separate method
Each vessel in NOVAWAVE has its own minimicrowave cavity and includes all the elements of an individual microwave control system. Thus, in conjunction with the software, each channel operates as a separate instrument, allowing the operator to have separate control parameters for every channel. Therefore, separate methods are available for each sample position, providing high flexibility, especially when the instrument is operated as a standalone SA model.
Adherence to existing official methods
The U.S. EPA 3015, 3051, and 3052 microwave methods are built in and can be followed directly or alternatively copied and modified to suit a particular situation. An unlimited number of methods can be stored and utilized in any sample run.
With a capacity of 168 samples per run (or, measured differently, 265 samples per 8-hr shift weighed, digested, and analyzed), the NOVAWAVE FA has been built for the busy laboratory. The model SA, without the transporter, autocooling, and autoventing stations, is suitable for laboratories that have more limited sample workloads, but can be easily converted to the fully automated model FA by adding the transporter and additional racks and vessels.
The NOVAWAVE new-generation microwave digestion system will provide laboratories with large sample workloads access to high-speed, high-throughput microwave digestion.
Mr . Chan is Marketing Manager , SCP SCIENCE, 348 Rte. 11, Champlain, NY 12919- 4816, U.S.A.; tel.: 514-457-0701, ext. 116; fax: 514-457-4499; e-mail: [email protected].