Current separation and purification processes are multistep, batch-type separations that generally use packed-column formats. Large-scale process purification systems are extremely expensive and work predominantly in a batch-mode process. This requires equilibrating the column, loading the sample onto the column, eluting the target compounds with larger quantities of stronger solvent, and collecting multiple fractions containing the compounds of interest. The column is then cleaned, sterilized, and reequilibrated back to the starting conditions and the process is repeated. This overall procedure becomes quite expensive due to the cost of the hardware; the separation media used; and the many volumes of solvent required to elute, clean, and reequilibrate the column. In large-scale purification processes, many older, less-effective techniques are still employed, such as liquid–liquid extraction, distillation, recrystallization, and adsorption.
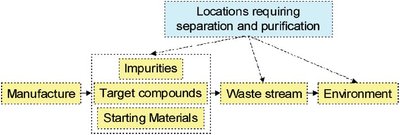
Figure 1 - Selective Capture Technology can be applied in a continuous selective capture, release, and discrimination mechanism, uniquely configured to an industry- or user-specific target compound.
Better separation technologies and processes are a global need. The separation and delivery system described in this article overcomes many of the current separation and purification challenges through novel application of Selective Capture Technology (Prime Separations [PSI], Woburn, MA). The technology can be applied in a continuous selective capture, release, and discrimination mechanism, uniquely configured to an industry or customer-specific target compound (see Figure 1). The continuous-mode mechanism and target specificity clearly differentiate the technology from other systems and contribute directly to significant cost savings due to increased purity at capture, reduction of multistep purification processes and input costs, and reduced overall purification time. Applicability of the technology has been demonstrated in large, growing markets such as biotechnology, biomass, pharmaceutical/chemicals manufacturing, precious metal recovery, and environmental remediation.
Process and chemistry
Selective Capture Technology is leveraged with problem-specific engineering to develop unique separation and purification solutions. The technology works through adsorption of a targeted compound from its aqueous environment, then timely desorption and discrimination of the targeted compound (see Figure 2).
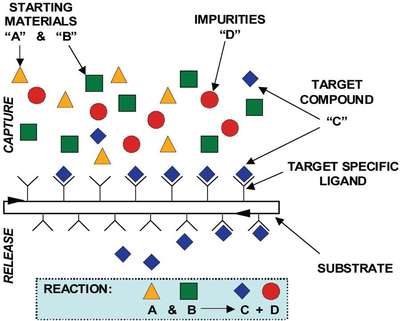
Figure 2 - Selective Capture Technology works through adsorption of a targeted compound from its aqueous environment, then timely desorption and discrimination of the targeted compound.
The capture environment is a thin layer of a functionalized polymeric material that is chemically interactive with one or more target molecules. The functionalized polymeric material, applied to a substrate material and immobilized, can exhibit a high affinity and specificity for the target product of interest. Other generic interactive chemistries may also be employed. The functionalized polymeric material can be highly customized, meaning it is developed exclusively for the desired target product, i.e., molecular recognition. The target product specifically and efficiently interacts with and binds to the custom ligand, leaving the other materials behind. The binding between the desired products and the functionalized polymeric material occurs through a broad range of potential phase interactions, lending additional flexibility. The technology’s target specificity, multiple phase capabilities, and continuous mode mechanism clearly differentiate it from others.
There have been several attempts in the past decades to develop continuous belt separation systems using chromatographic media, gels, and membranes.1 From a practical point of view, none of these methods found commercial success due to mass transfer problems of the target molecule into and out of these environments. Thin chromatographic films allow for rapid sorption/desorption kinetics, therefore permitting higher linear velocities of the chromatographic film, which translates into increased productivity of product capture, mass/unit time, versus standard media.
Conventional wisdom focuses on surface area as the defining element for “dynamic capacity” when determining product throughput employing conventional chromatographic media. Independent studies have shown the capture of copper averaging at 200 mg/m2 using the manufacturer’s chromatographic film. When one calculates the capture of copper using polymer beads employing the same capture chemistry, the capacity values are .22 mg/m2. This is obviously due to the very high surface area of 340 m2/g and the capacity for copper capture, 65 g copper/kilo.
With PSI chromatographic film, methods development becomes a straightforward process. Separation conditions for capture, release, and discrimination can be obtained by simply dipping a functionalized film into any fluid containing target molecules, washing extraneous material from the film, and then subjecting the film to various desorption buffers. Analysis of the desorption fluids indicates whether one has obtained capture, release, and discrimination of the molecules of choice. In some situations, particularly with metals, analysis of the chromatographic film using X-ray fluorescence (XRF) will provide the same information. Once the separation method is developed, product throughput data are generated using a PSI 6-in. laboratory unit, and provide the basis for a linear process scaleup.
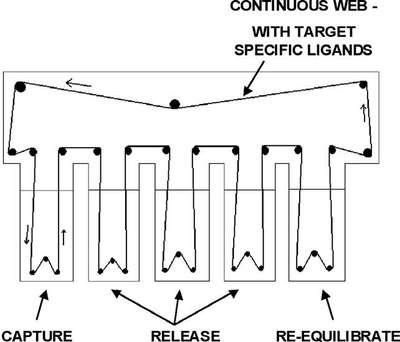
Figure 3 - Selective Capture Technology demonstrated continuous mode of the capture, release, and discrimination mechanism.
The chromatographic separation web is a continuous adsorption mechanism that can first be passed through the sample reaction vessel, then passed through product desorption and film reequilibration tanks. It is in the desorption tanks in which the captured materials release from the web and are collected, and the method is then repeated (see Figure 3).
Alternatively, the web may be taken up on a rewind roll and stored for continued processing at a subsequent time to process the captured material. Separation and purification may take place in the presence of debris, which eliminates the need for any preconditioning of the sample, and capture of target molecules from dilute solution negates any sample concentration step.
The separation challenge
The separation and purification needs of the market and specific customer requirements are unique, demanding multiple processes and significant infrastructure to support. Selective Capture Technology can be applied through multiple mechanisms to deliver the appropriate solution to provide unique solutions. It can selectively target specific compounds, by-products, and/or contaminants for capture, release, and discrimination, significantly reducing the costs for conversion; increasing the purity and concentration of the target; and reducing the total time required.
For example, the biotechnology market uses enzymes or microorganisms to convert feedstock to the desired products, i.e., proteins or other important chemicals. In some biochemical processes, removal of the desired product from the reaction vessel during fermentation will increase the product yield by reducing the concentration of the self-terminating material. In other processes, it is desirable to remove by-products and contaminants to improve efficiency and yield of the target molecule.
In the biomass market, there are substantial efforts being sponsored by the U.S. government and many industrial firms to produce basic chemical building-block materials from renewable sources such as trees, agricultural products, and waste materials. A primary focus of this effort is to minimize the use of petrochemicals to produce these chemicals, thus reducing our dependency on foreign and domestic oil sources. Selective removal of the target compound, or by-products and contaminants during reaction, will increase efficiency and provide significant value to biochemical manufacturers.
The manufacture of pharmaceuticals and chemicals, to include industrial, agro, flavor, and pharmaceuticals, includes costly separation and purification processes and techniques. The purification is completed with inefficient batch-type processes, resulting in high degrees of impurities in the target, and the need for multiple purification steps and large amounts of expensive solvents. Today, post-production waste streams continue to deliver significant amounts of contaminants and toxins to the environment, adversely affecting humans and the ecosystem. Due to prohibitive costs to meet current environmental standards, some domestic manufacturers are forced to move offshore or shut down operations.2
Unfortunately, there are many contaminants and toxins in the environment that continue to be released in ever-increasing quantities; their removal requires extreme in situ and ex situ remediation processes. The discharge of toxic chemicals, dating back to early global industrialization, has left a legacy of contaminated property throughout the world. Due to a growing global awareness and concern of risks to public health and the environment, there is tremendous pressure to prevent further destruction of the environment and to remediate contaminated soil and groundwater at these sites. These contaminated sites include industrial and DoD installations, and all parties are looking for new remediation technologies to improve these difficult and costly efforts.
Throughout the world, the mining industry has successfully exploited the removal of metals from the earth, employing older, inefficient processes with little regard for the environment. PSI views this as an opportunity to apply its technology to base metal, slag piles, and the platinum group metal streams. There are acute problems for which PSI’s technologies will provide economical solutions to protect the environment, replace older absorption technologies, and capture valuable assets from toxic aqueous environments.
Continuous separation process solution
Selective Capture Technology, marrying chemistry and engineering, will generate significant value because of the simplicity of the solution. It is applicable across many industries, is able to operate in multiple modes, can be applied in a continuous mechanism, and can be targeted to be compound specific in design. In experiments to date, the capture, release, and discrimination have been demonstrated within the following addressable markets:
- Biotechnology—proteins directly from fermentation broths
- Biomass—isolation of commercially significant building-block chemicals from fermentations
- Pharmaceutical/chemical
- Precious metal recovery—E-waste (end of life electronics); mining ores
- Environmental remediation— remediation of industrial waste streams; groundwater.
References
- Powell, P.E. U.S. Patent 5,256,298. Continuous-Belt Separator/Reactor and Method.
- Pollution Rules Seen Stifling Jobs. Boston Globe, Feb 17, 2005.
Mr. Cooley is President, and Mr. Kolesinski is Vice President and CTO, Prime Separations, Inc., 25 R Olympia Ave., Woburn, MA 01801, U.S.A.; tel.: 910-794-1038; e-mail: [email protected].