A rapidly growing number of corporations are moving their information structure toward a more centralized, enterprise-wide model in which all the key information about their business can be readily accessed with a few keystrokes from anywhere in the world. From the purchase of raw materials through the delivery of the finished product, the availability of the data, facts, and figures is key to being able to compete in the fast-paced marketplace of today’s business environment. The chemical industry is no exception.
Many of today’s most competitive businesses have incorporated this type of centralized, enterprise-wide, multifaceted information system to handle all aspects of their business. One such system is SAP™ (SAP AG, Waldorf, Germany). While the implementation of the system can encompass all aspects of a business, the topic discussed here will be the implementation of the quality module of SAP into a quality assurance/control laboratory.
SAP and other enterprise-wide software systems, by their very nature, require a highly structured series of data entry steps in a rigid work flow in order to perform smoothly. Adapting such a rigid work flow was challenging in an existing, mature chemical business that 1) makes bulk chemicals for inventory (no customer identified initially) or 2) responds to customer requests that at times provide only 48 hr lead time. The case study presented here describes one laboratory’s solution to these manufacturing scenarios incorporating the use of SAP for finished product data storage and reporting as a part of enterprise-wide strategy and the continuing use of an existing LIMS for in-process testing as well as other key tasks still required following implementation of the system.
A needed change
As is the case for many businesses in today’s rapidly changing corporate climate, Bayer MaterialScience LLC (New Martinsville, WV) determined that it had to improve its logistical system to give it an edge in meeting corporate needs and those of its customers. Better control of inventory, information, and financials were required. After extensive study, SAP was chosen as the tool to provide this needed improvement. The use of the system ties together the many, varying facets of the business. It provides for improved tracking and coordination of the diverse yet intertwined areas that comprise a business the size of Bayer MaterialScience LLC. An in-depth description of the system and its reach is well beyond the scope of this article; suffice it to say that all areas of the corporation were impacted by the system. The implementation of such a farreaching and invasive system into the infrastructure of any corporation would be very complex and involved. Bayer was no exception. Years of planning and work went into the insertion of the program, and years of debugging and debottlenecking have followed. At this point, the focus of this article shifts to the effects of this tool on the QA/QC laboratory and its true product, information, and data management.
Background
The Bayer laboratory is no stranger to data management systems. It has 20 years of LIMS experience as well as seven years of experience in system-to-system electronic data transfer. It runs on a 0 backlog system, 24 hours a day, 365 days a year. It services five unique production areas and performs all the raw material, in-process, finished goods, and environmental testing for the site. Roughly 72,000 samples with multiple tests are analyzed annually. Also, the laboratory is ISO 17025 certified and A2LA accredited. These standards and customer performance goals could not be lost in the face of the new system.
While other areas in the corporation were completely converted to SAP, it was decided that the quality module would only encompass finished goods testing. This testing makes up only one-third of the sample load on the laboratory. Not included then by the system were the in-process, environmental, and raw material testing, as well as accreditation/certification and instrument maintenance. Nearly 66% of the laboratory-generated results were ignored by Bayer’s installation of SAP.
These tasks, however, still had to be completed and a system was still needed to do it. It was obvious that even with SAP in the mix, the LIMs had to stay. It was already customized and set up to handle all the laboratory workload on these tasks; thus it had to remain and handle the majority of the testing work. With this decision made, the efforts then turned to bringing in the new system.
Adapting the system
Upon examination of this system it was found that it lacked the flexibility required by Bayer. SAP is designed more for item or part manufacture. It is ideal where individual quality is black and white. As a manufacturer of volumes of product, Bayer has a different situation. Its products are sold against bulk properties, not molecular properties. The product needs homogeneity. Nonconforming material can be blended or adjusted to specification. The off-specification material can be corrected. SAP, however, does not lend itself to that type of operation. Adjustment, retesting, and adding data are not easily accomplished.
This is quite different than the customized LIMs, which was set up to handle these production scenarios pre-SAP. It easily took care of the retesting, adjusting, and blending of the material before final certification of the product. SAP would be very cumbersome in this role and could bottleneck the system if used as is.
As the plans for the system integration took shape, it became obvious that since the flexible LIMs had to remain to handle the other testing, it could also work with SAP to provide better service to the quality system as a whole. SAP would be the depository and keeper of the final data, and LIMS could handle the flux before final product disposition.
Making the system work
The goal at the start was to design a system that utilizes the benefits of both systems—the flexibility of LIMS and the SAP integration of the corporate logistical system. To do so, it was necessary to look at how both systems would handle the tasks required.
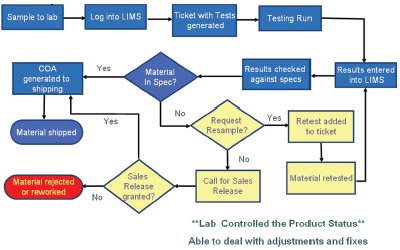
Figure 1 - Laboratory work flow—pre-SAP.
Figure 1 illustrates the flow of the testing and data acquisition in the LIMs. The flow chart shows where the addition of testing is made, material is resampled, and adjustments can be made. These changes are performed easily within the system and are trackable and traceable. The LIMs generates the certificate of analysis that would go out with the shipment. It then stores the data and can be accessed by other systems that are able to make use of the data.
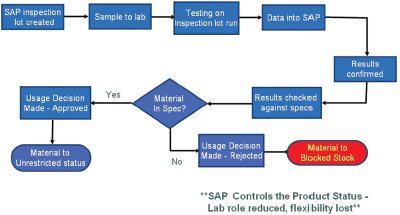
Figure 2 - Laboratory work flow—SAP.

Figure 3 - SAP and LIMs—creation of the hybrid.
Figure 2 illustrates the flow of the data utilizing strictly SAP. The detours on the way to “approved” or “rejected” status are absent here. As stated above, the system is more cut and dried. Either the part is good or it is bad. This strict approach would be very problematic for Bayer’s industry, and the flexibility needed to be added back in. In order to do this both simply and efficiently, a linear approach was used to combine the two into one. Figure 3 demonstrates the point of union to form the new system. The system was designed by utilizing the flexibility up front to handle the product until production was finished in combination with the power of SAP at the end as the final approver and keeper of the finished data.
Implementation
Due to the nature of the system, SAP would be in control. It monitors inventory, checks orders, schedules production, requests the data, stores the data, and generates certificates of analysis to the customer. LIMs needed to be a step on the road to provide these data to the system. The key to success for this hybrid would be communication. In this setup, SAP would schedule the production and testing of the product. It would contact the laboratory with the required testing, which in turn would run the testing and enter the results into LIMS until the product was completed. Since these were two autonomous systems, the data had to be transferred between them at the junction. Manual transcription of the massive amount of data (72,000 samples/year) involved was unacceptable. There would be too many opportunities for error. Automation would be required. This was accomplished through an interface in which SAP would contact LIMS and tell it what testing was required. The LIMs would generate the worksheets in the laboratory and accumulate the data. Once the testing was complete and the product deemed finished, the data would be copied electronically back through the interface from LIMS to SAP. The results would then be checked for accuracy and the sample approved in SAP.
Completion
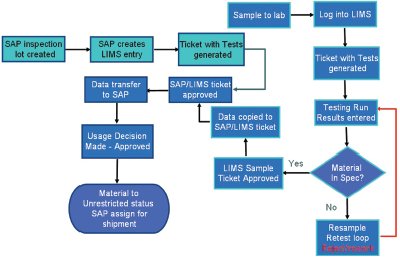
Figure 4 - Laboratory work flow—hybrid.
Figure 4 shows the final combined flow of the system. The design provided the versatility in meeting both the laboratory’s needs as a service provider and Bayer’s needs as the service recipient. The production schemes can proceed as before, and the corporation can integrate its product data into the whole, massive, intertwined SAP environment. The laboratory can continue to meet the individual requirements for raw material/in-process testing, preventative maintenance, and certification/ accreditation requirements. Through innovative thought and a “can do better” approach, the goals of all three entities were accomplished, and SAP was successfully implemented into the Bayer MaterialScience LLC QA/QC system.
Mr. Zacherl is Operations Supervisor, NM PLS, Bayer MaterialScience LLC, Quality Assurance Laboratory, State Rte. 2, New Martinsville, WV 26155, U.S.A.; tel.: 304-451-2247; fax: 304-451-2696; e-mail: [email protected].