One of the most common reasons for purchasing a laboratory information management system (LIMS) is its ability to integrate with laboratory instrumentation and enterprise systems for better data management. Despite the fact that laboratories feel this integration is a requirement, it is not always achieved in practice. A worldwide market research study on LIMS users conducted by Strategic Directions International (SDi, Los Angeles, CA) determined that approx. 70% of the respondents manually enter instrument data into the LIMS. This study and others like it illustrate the clear gap between the integration a laboratory hopes to achieve and reality. The real or perceived complexity of linking these systems is one reason why this integration is currently not more prevalent. When an instrument is directly interfaced to the LIMS, the costly time, labor, and error introduction involved in the manual transfer of data are essentially eliminated. This is particularly evident with chromatography data, which account for approx. 80% of the data generated in the laboratory.
In fact, the only reason that chromatography data systems (CDS) and LIMS are separate systems to begin with is that they are each based on specific functionality instead of the actual business work flow of the laboratory. This lack of unification underscores the clear need and market demand to fully integrate data from disparate instruments into the LIMS for more secure and reliable data management. As a result, a paradigm shift is under way that breaks down these artificial restrictions and provides true enterprise integration that reflects the real work flow of the laboratory.
This article explains the benefits of seamlessly integrating a LIMS and CDS on a common platform. The authors also go beyond current LIMS and CDS data management capabilities and discuss how technology is leading the way for full instrument and enterprise system integration. Integration technologies that attempt to tackle such problems are nothing new, but the rate of data growth is far exceeding the coping ability of most current technologies. A coherent strategy that can integrate data from LIMS, CDS, and other sources (e.g., enterprise resource planning [ERP] and manufacturing execution systems [MES]) across the enterprise is a key business driver today.
Controlling the explosion of data
One of the key challenges faced by organizations today is their inability to turn the vast amount of laboratory data generated into useful information that enables them to make timely and effective decisions. With multiple applications across the enterprise generating reams of data that all sit in separate silos, aggregating and mining these data is a very real and complex problem.
Many companies use manual or inefficient processes for collecting and aggregating data, and use both structured and unstructured content; oftentimes the reports that distill this mountain of data into relevant information are extremely tedious to create. In addition, because data formats and applications are frequently inconsistent and not well integrated, there is no coherent way for scientists to aggregate all of their work in one place. This complexity is compounded even further when a laboratory manager or director has to manage multiple teams or groups of work. All of these are barriers to making effective business decisions and increasing return on investment (ROI).
LIMS applications have many touch points within the manufacturing process; therefore, integration of laboratory data should be as complete as possible in order to maximize both manufacturing and operational efficiency. The following sections highlight some of the key drivers for integration of LIMS with different levels of the enterprise information chain.
Integration of instrumentation
The benefits of instrument integration have long been recognized in all manufacturing industries. For example, in the recent SDi worldwide LIMS survey, petrochemical, oil, and gas LIMS users report an 85% adoption rate of instrument integration modules. Respondents indicate a significant disconnect between the number of users who have integration capability and the number who have achieved 100% integration. This highlights the fact that integration is beneficial, provided the technical challenges are not too difficult or too complicated. In many industrial laboratories, chromatography provides a significant amount of critical data, and so it is vitally important that all of these data are processed and made fully available as soon as possible in the LIMS.
Laboratories have always needed the freedom to choose the best instrumentation for their particular applications. Since instrumentation comes bundled with specialized workstation software, and laboratories typically use more than one type of instrumentation, supporting multiple software products can lead to an increased burden on IT. CDS was conceived as a standardized enterprise-wide solution to simplify this complexity and support multiple and diverse instruments. These systems have increased productivity and reduced costs associated with continuously implementing and validating multiple instrument-specific or laboratory-based software solutions. This is particularly true in laboratories that have to conform to stringent regulatory requirements, such as pharmaceutical companies. Unfortunately, selection of a CDS only addresses part of a laboratory’s integration requirements.
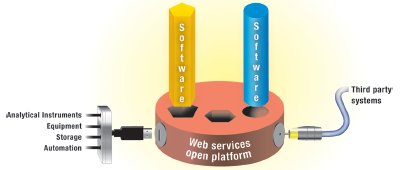
Figure 1 - A fully integrated laboratory will have taken advantage of the opportunities to marry its instrumentation to its LIMS, and further enabled the user base to access and aggregate data via .Net technologies across the enterprise. This integration will yield a greatly enriched user experience that allows individuals and organizations to not only manage and capture their data more efficiently and securely, but also to simplify their daily work flow and communicate more effectively. At a higher level, integration allows management to make decisions based on the current data and aggregated information from the entire operation.
Full integration of LIMS and CDS is the next evolutionary step in laboratory data integration and management. This reduces the complexity and expense of implementation, validation, maintenance, and training when compared to managing multiple software systems. Productivity gains are also achieved through the consistent reporting and sharing of data. A well-integrated LIMS and CDS is designed with the chromatographer’s work flow in mind, allowing multiple levels of user interface, intuitive and user-friendly operations, and automation of the flow of LIMS-generated work requests into the CDS and CDS results back into the LIMS (see Figure 1).
Integration of LIMS with ERP
The key step in any large-scale manufacturing process is the creation of a production order in an ERP system. This action cascades through the manufacturing operations and triggers activities within domain-specific systems such as LIMS and MES, in addition to updating product specifications, determining production quantities, etc. Having the ERP integrated with these subsystems means that there is a seamless handover of activity from the planning to the manufacturing stage. This ensures that new activities do not come as a surprise to anyone involved (greatly reducing any process bottlenecks), that product is produced as quickly as possible, and that quality standards are met.
As soon as the ERP triggers a change in manufacturing requirements, the LIMS is able to update sampling and testing schedules and specifications accordingly and the management of laboratory resources is immediately available for the new scheme of work. In addition, data do not need to be replicated in multiple systems, since this is the whole advantage of integrating a purpose-built LIMS in the manufacturing environment. This approach is not a one-way street with data only flowing from the ERP system. The ERP does not need the minutiae of analytical detail from the laboratory to release a material from manufacturing; thus it is often the case that the LIMS will deliver key results alongside a disposition decision back to the ERP. In most organizations, the quality assurance group is responsible for authorization of laboratory results as well as release of products, allowing their work to be completed using a single interface.
Integration of LIMS with MES to expedite decision-making
Making information available as soon as possible within a manufacturing operation plays a major role in making any production process efficient, particularly when that information indicates a change within the process performance. Timely and accessible data are vital to preventing product loss or the production of out-of-specification materials and reducing the likelihood of lost revenue.
In addition, on-line analyzers in the plant are employed to make key decisions as quickly as possible, and laboratory results are often used to verify data, especially if a parameter is out of specification. If a significant amount of time elapses before laboratory results become available to the plant operators, these results may be irrelevant or not representative of how the process is currently performing. Therefore, the rapid delivery of laboratory results is key to ensuring that the data are relevant. Having a direct interface between the LIMS and MES allows the production facility to track the status of its on-line results and make timely decisions.
Making laboratory results available, however, is not the only requirement of an integrated system, since it is often the case that the laboratory and the plant operators have different frames of reference and often refer to data using different terminology. Passing information from one system to another needs to be done in a way that considers all the original source parameters, in their sometimes different forms. Carrying out manual data calculations can lead to delay and potential errors. Therefore, shared information should also be formatted for its recipients as a function of the interface.
Regardless of the industry, the need to integrate information across the enterprise is clear. How this integration is achieved is the current challenge for many organizations and software vendors. One way is by adopting a service-oriented architecture (SOA) and taking advantage of the integration capabilities it can provide.
Higher-level integration
One of the benefits of an SOA is its ability to provide application-specific results and information to other applications on demand, much like an external application programming interface (API) does. The difference is that, today, SOAs are usually based on Web services, which use universal, well-known protocols for communication. By supporting this architecture, applications such as Thermo Scientific LIMS and CDS (Thermo Fisher Scientific, Philadelphia, PA) can access, via Web services, applications such as Microsoft (Bellevue, WA) BizTalk and SharePoint.
BizTalk, which has support for communicating between 400+ external product formats, goes a long way toward facilitating integration of disparate systems such as PeopleSoft Enterprise (Oracle Corp., Redwood Shores, CA), SAP (Newtown Square, PA), Enterprise One (J.D. Edwards, Denver, CO), and many more. Thermo Scientific integration technologies provide a bus-like, configurable, distributed communication pipe between any two systems. They support integration of both software systems, such as LIMS or CDS, and hardware systems, such as laboratory instrumentation. This integration is enabled by system-specific adapters (somewhat similar to BizTalk adapters).
In the future, these technologies will further integrate with BizTalk, so that any software or hardware that can communicate with Thermo Scientific LIMS and CDS will be able to comcommunicate in turn with any other product that BizTalk supports. This will open up Thermo Scientific software and hardware to the 400+ products that BizTalk supports, expanding customers’ capability to share and communicate. The ease of data mapping and integration will ensure a far easier, less labor-intensive flow of data across the enterprise.
Higher-level decision-making
The aforementioned integration allows data to move transparently between systems, but the piece of the puzzle that is still missing is the ability to aggregate and retrieve data that are relevant, enabling accurate and quick business decisions.
A user interface technique called composition may be used to aggregate and visualize data collected from back-end Web services and other data sources. This technique is frequently seen on the Web, where users may, for example, customize their home page by choosing what they wish to see. The resulting Web page is then essentially composed of parts, each of which has a specialized function that it knows how to execute.
This technique is readily extended to business applications, making it easy to (for example) retrieve chromatography data in a LIMS application. This enables easy integration of what are traditionally separate applications into a composite application. Users are given the flexibility to see what they want to see on their desktops.
The SharePoint platform has built-in support for creating such composite applications. It enables the development of portal-like Web sites, which allow data from multiple back-end systems (such as LIMS, CDS, ERP, MES, or any other system) to be converted to key business metrics or other critical information.
Conclusion
The world of laboratory informatics is changing. As laboratories look to streamline the flow of information, having multiple disparate systems with minimal to no integration is no longer an option. Fortunately, using products from Microsoft and technologies such as those from Thermo Scientific, vendors are able to provide composite applications that ensure better integration and simplified administration.
The shift to a laboratory fully integrated with the enterprise, such as the one described here, yields a greatly enriched user experience that allows individuals and organizations to not only manage and capture their data more efficiently and securely, but also to simplify their daily work flow. At a higher level, it enables management to make decisions based on current and pertinent information. This ability to turn large quantities of data from disparate sources into valid business knowledge is critical. Companies using these technologies and methods are the ones that will grow and gain a competitive advantage in today’s volatile business environment.
Ms. Meek is Director of Product Strategy, Life Sciences; Mr. Mac Conaonaigh is Director, Technology; and Mr. Thurston is Director of Product Strategy, Process Industries, Thermo Fisher Scientific, 1601 Cherry St., Ste. 1200, Philadelphia, PA 19102, U.S.A.; tel.: 215-964-6020; fax: 215-964-6021; e-mail: [email protected].