A survey of pharmaceutical team leaders conducted in 2005 found that the three biggest challenges facing pharmaceutical manufacturing were standard operating procedures (SOPs) and training, quality management and testing, and documentation.1 All three of these challenges for pharmaceutical manufacturing revolve around adherence to government regulations, e.g., FDA 21 CFR Part 58, to ensure the efficacy and safety of their pharmaceutical products. In the past 5–10 years, most pharmaceutical companies began utilizing some type of Lean Six Sigma Process Manufacturing to improve overall operational efficiency.2
Migrating to an electronic documentation solution is an important strategy for improving efficiency in laboratories utilizing SOPs because it helps fulfill QC documentation requirements and reduces QC testing turnaround times. Although a number of electronic SOP worksheets are commercially available, the creation of these worksheets can be complex and time-consuming.
This article describes an electronic SOP form design utility called SDMS Form Designer (Waters Corp., Milford, MA) that provides a straightforward and standardized mechanism for creating compliant-ready SOP forms.
QC data and test result management
Before creating and using electronic SOPs, the QC data and test results need to be organized electronically. Scientific data management systems such as the Waters NuGenesis® SDMS solution provide a platform for standardizing QC testing raw data and paper documentation management in a centralized digital repository. The system’s file capture capability automatically captures and catalogs data originating from QC instruments into a searchable relational database, while its print-to-database capability automatically indexes printed test documents into the searchable database. The digital storage of QC test data and documents is the foundational step toward implementing an electronic SOP documentation and work flow system because it provides the content necessary to implement the SOP forms.
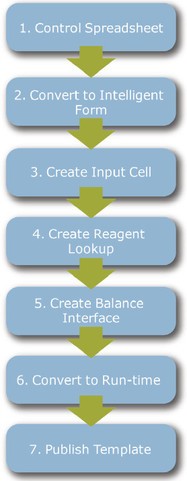
Figure 1 - Seven-step work flow utilized to create a functioning, intelligent SOP form. The individual steps are created by configuring the software within a form designer utility.
Electronic SOP and work flow system
Waters SDMS Vision Publisher™, the electronic laboratory notebook capability of NuGenesis SDMS, is available with an electronic form and documentation work flow system, the SDMS Intelligent Procedure Manager. Intelligent Procedure Manager provides an electronic SOP worksheet creation utility called SDMS Form Designer, which is the focus of this article. Figure 1 illustrates the steps involved in creating a typical electronic SOP form.
Controlling electronic forms
The first step in creating electronic SOP forms involves applying regulatory safeguards to Microsoft® Excel™ (Microsoft Corp., Redmond, WA) by incorporating a spreadsheet within the compliant-ready environment of SDMS Vision Publisher.
Converting a spreadsheet into an intelligent form
The next step in creating an electronic SOP worksheet involves activating the Form Designer functionality of Intelligent Procedure Manager (Step 2, Figure 1). Converting the Excel worksheet into an intelligent form starts by clicking Convert to Form, as shown in Figure 2. The electronic form then switches on additional functionality, such as the capability to interface directly with electronic balances and database tables.
Adding intelligence to a form
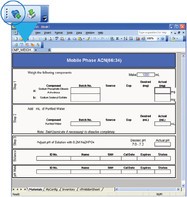
Figure 2 - Converting an Excel form into an intelligent electronic SOP form by clicking the Convert to Form button (item 1).
Converting a spreadsheet into an intelligent form, as shown in Figure 2, protects the entire worksheet from unauthorized input/editing, and applies 21 CFR Part 11 safeguards such as audit trails. However, in order for the form to accept user input, individual spreadsheet cells are selectively made editable during design time (Step 3, Figure 1). Functionality such as balance interfacing and input range validation can be added by selecting appropriate functionality from the cell settings menu, as shown in Figure 3.
The most basic type of cell functionality to add to a form is called an input field. This allows the user to manually type a value into a specified cell. For example, if the analyst wants to prepare a 1000-mL solution, he or she would key 1000 into the input field, and all subsequent calculations within the SOP form would automatically update based on 1000 mL. Next, during solution preparation, the analyst would select appropriate reagents to add to the solution. In most organizations, a database table holds an inventory of available chemical reagents. The SDMS Form Designer allows a form to directly retrieve reagent information from a reagent database, as shown in Step 4, Figure 1.
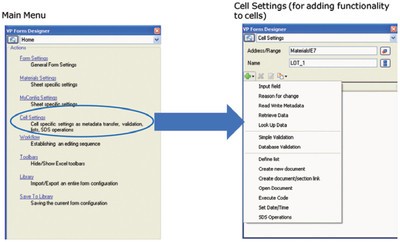
Figure 3 - Form Designer’s main menu (left) provides high-level functionality, such as overall form settings and work flow settings. The Cell Settings submenu adds functionality, such as input fields, to individual spreadsheet cells.
Direct transfer of balance measurements to a form
After specifying the solution volume and necessary reagents needed to prepare the solution, the analyst weighs the reagents on an analytical balance and records the results in a notebook. With Form Designer, it is possible to design a form that directly transfers reagent weights, as seen in Step 5, Figure 1, into the electronic form. The first step in designing a form that directly accepts weight information from an analytical balance is to establish an electronic connection between the form and the balance. This is accomplished by making use of the Waters Serial Device Support (SDS) application. This application serves as a software intermediary that handles communication between the electronic form and the balance. To add the reagent weighing functionality to the form, the SDS application is associated with a worksheet form at the cell level by adding the SDS Operations. Recording the balance name, serial number, and location is important for maintaining complete records, while adhering to GMP and ISO regulations.
Approving and publishing the form
Publishing the finalized form involves two steps: 1) converting the completed form to run-time mode (Step 6, Figure 1), and 2) approving the form within the SDMS Vision Publisher Template Editor. A finalized and approved form then becomes accessible to laboratory analysts and is ready for use (Step 7, Figure 1).
Conclusion
Migrating QA/QC data and records from paper to digital form offers the opportunity to improve overall operational efficiency in manufacturing environments that adhere to government regulations such as GxP and ISO. QA/QC records include not only raw data and printed test results, but also SOP documents. The SDMS Intelligent Procedure Manager is a compliant-ready solution for managing raw data and printed test results, and for intelligent electronic SOP worksheets.
The SDMS Form Designer streamlines the creation of intelligent electronic SOP worksheet forms. The forms in turn allow QC laboratories to increase productivity by:
- Error-proofing the information input by analysts
- Reducing transcription errors via a direct interface with analytical balances (error rates near 0%)
- Saving analyst time via a direct interface with reagent and solution databases
- Reducing review and sign-off time (average 50% improvement).
References
- Pharm. Man.2005; www.pharmamanufacturing.com/articles/2005/219.html.
- Conference: Operational Excellence for Pharmaceutical, Biotech, and Medical Devices; London, U.K.; Dec 8–9, 2009.
The authors are with Waters Corp., 34 Maple St., Milford, MA 01757, U.S.A.; tel.: 508-482-2000; e-mail: [email protected].