The combined pressures of continuing miniaturization, higher packing densities, and rigorous quality assurance means that the physical size of particles capable of adversely affecting industrial processing and product quality is diminishing rapidly, and their identification is becoming more difficult. Similarly, pressure to optimize the quality of cast components requires a means of examining large, polished sections for both large and small defects. Likewise, it is common practice for many manufacturing companies to identify scale wear particles in lubricated systems, and to verify the absence of contaminating particles, particularly in food stuffs and pharmaceuticals.
The above examples emphasize the wide ranging role of the microscope in modern industrial processes. Indeed, many sectors, including the pharmaceutical and automotive supply industries, need to document their complicity with guidelines and standards, such as FDA 21 CFR Part 11 and ISO 16232. However, miniaturization and increasing quality standards mandate the use of analysis systems that are able to rapidly detect, measure, and categorize increasingly small particles on the order of a few micrometers while still being able to handle large particles or fragments.
The problem for users is that the data volumes involved in acquiring high-resolution images of these increasingly small particles within a large and heterogeneous sample field overwhelm the available memory in even high-specification computers and workstations. Until now, the only answer has been to measure twice—at high resolution for small particles and separately at lower resolution for larger particles. A fast and accurate method to characterize the whole population of particles and their possible origins would boost product confidence and company revenues, through decreased production downtime and quality assurance.
Designed to keep pace with increasingly rigorous quality standards, the Carl Zeiss Particle Analyzer (Hertfordshire, U.K.) images complete samples in a single step, measuring particles of all sizes, allowing automatic classification of particle types, and delivering fully resolved images on demand. Support for national and international norms, such as ISO 4406, ISO 16232, and VDA Vol. 19, is included, and company-specific standards or demands outside the standards may also be implemented easily by the user. Also, the directives of the FDA can be employed for applications in the pharmaceutical industry and medical technology sector (Table 1).
Table 1 - Conformity with international standards
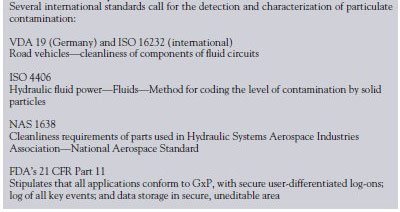
In this study, the Carl Zeiss Particle Analyzer was used with either the SteREO Discovery range of stereomicroscopes for particles larger than 25 µm, or the Axio Imager range of upright microscopes for particles down to 2.5 µm (Figure 1). The systems (both from Carl Zeiss) offer motorized polarization and offer a rapid, one-step method of distinguishing between metallic and nonmetallic particles using a specially integrated segmentation function. Until now, this was another procedure that required two scans of the sample—with polarized light being used to identify the particles, and bright field to determine the degree of reflection. The procedure is automatic and secure, and eliminates the need for manually applied corrections, with all the measurement parameters and system configurations stored with the results to ensure consistent quality of measured results from batch-to-batch, regardless of a change in user.
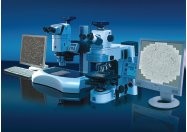
Figure 1 - The Particle Analyzer delivers increased reproducibility for automatic quality inspection.
The Particle Analyzer does not rewrite the laws of physics and is still bound by the memory constraints of modern PC workstations. It overcomes the problems of imaging large samples at high resolution in a single step by using the mosaic-image technique exclusively across the entire particle size range and combining that with a novel approach to image storage and display.
Mosaic-image technique
In order to acquire images of the smallest particles of interest in any given sample, it is inevitable that only a small part of the total sample will be captured by the camera image, and therefore multiple images will be required—possibly many hundreds. For the user with a software-controlled, motorized microscope, this is not a problem. The sample is automatically moved by the motorized stage, high-resolution images are recorded at each position, and a mosaic image of the entire sample is put together by combining all the partial images. The Particle Analyzer automatically uses the mosaic image technique to accurately capture and measure all particles, whether they are a few microns or millimeters in scale. If the software detects that the reproducibility of the stage movement is too low for the particle size (i.e., a higher number in microns than the pixel scaling), overlapping image acquisition with a software stitching step is automatically implemented. The software will also implement auto focus between partial images.
This method of image capture results in data volumes up to the order of gigabytes, and until now has limited image processing and measurement of mosaic images to one image at a time. The Particle Analyzer takes an original approach to handling the large images. Rather than holding the complete overall image in the computer's random access memory (RAM), a reduced-resolution form is stored, and only the relevant subregion is loaded for display on the monitor. This means that the computer's memory is only burdened with the current frame of interest, allowing the remainder to be utilized for analysis, where measurement is performed on the fully resolved image.
Crossing boundaries
The technique itself is not new, and its applications have been well-documented on the Internet. However, it has not been applied previously for the processing and measurement of composite microscope images. Therefore, it is now possible to carry out a full analysis on images that are larger than the available RAM.

Figure 2 - Particle cutoff when acquiring single images.
In particular, particles that straddle the boundary between partial images can now be measured automatically in their entirety rather than in two or more sections, and then added together manually (Figure 2). Importantly, users are assured that a single measurement process captures, displays, and measures all particles. Moreover, the reproducibility of the image acquisition and evaluation process is guaranteed. With the Particle Analyzer, a complete set of instrument parameters is stored with every image, including zoom setting (from a stereomicroscope), objective magnification (from a compound light microscope), illumination settings, contrasting technique, scaling factors, autofocus settings, and camera settings. If a sample needs to be reanalyzed, all of these parameters can be reactivated without user intervention. Similarly, this degree of automation provides nonsubjective results with minimal user involvement for repetitive sample analysis. In addition, automated focus, calibration, and diagnostic procedures ensure results accuracy and system stability.
Putting the technique into practice
The tool selected should make it convenient to complete the task, no matter how complex. From entering the project data, acquiring and processing the image, measurement and data analysis through creating and archiving the data files (comma-separated values [CSVs]) and customizable reports (pdfs), the Particle Analyzer system is designed with speed and simplicity in mind. Authorized system administrators can quickly adapt the system to new test specifications and standards without requiring external support and additional programming. Typical applications are given below.
1. Residual dirt on filter membranes. Many laboratories analyze particles trapped on filter disks. In the automotive industry, for instance, test components are rinsed with a defined amount of fluid to wash off dirt or wear particles; the fluid is then passed through the filter disk to capture the particles for analysis. The goal is to obtain a representative distribution of particles of a given type, and the technician usually checks the result against defined maxima set out in international standards (Figure 3).
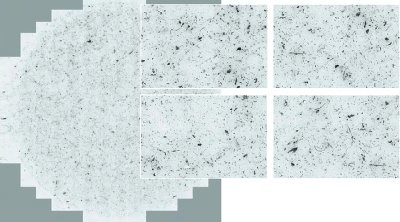
Figure 3 - Residual dirt particles on filter membrane. Mosaic image consisting of over 200 single images. Microscope: Axio Imager, objective: EC Epiplan Neofluar 5×/0.13, camera: AxioCam MRc (all systems and components from Carl Zeiss).
With the Particle Analyzer, the user can scan the filter disks completely and contiguously, analyze the mosaic images to size and grade the particles, and automatically compare and report the results against the set standard. The analyzer can also automatically characterize particles, for instance, to distinguish between reflecting and nonreflecting details to identify metallic particles. Again, these data are obtained with a single scan of the sample. The software also combines parameters such as area, form factors, circumference, and diameter to size-grade large numbers of different particles.
In addition to the automotive industry, this procedure is used in a very similar way to examine parental fluids in the pharmaceutical industry and at wind energy plants to check the service intervals of lubricants.
2. Crystalline forms in ointment. Quality control of ointments may involve measuring the amount of active substance in crystalline form. For example, fungicidal preparations for the skin and mucous membranes are tested for the suitable distribution of the active substance within the matrix material of the compound. Samples may be from new products in development or quality control samples of finished batches. To do this, ointment is smeared onto a slide and analyzed under polarized light using 10× or 20× objectives, where the crystals of the active substance are clearly visible as dark structures and can be assessed using image analysis. To validate the system, a circular standard area of 100 µm2 is measured every month, and the result is compared with a reference value.
Using the Particle Analyzer, large crystal agglomerates and small particles can be analyzed in a single step and the distribution compared automatically as specified in the Standard Operating Procedures (SOPs) (Figure 4).
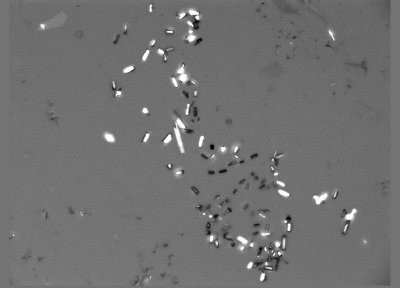
Figure 4 - Active substance in crystalline form in an ointment sample. Microscope: Axio Imager, objective: A-Plan 10×, camera: AxioCam MRm.
3. Casting defects. It is common manufacturing procedure to die-cast aluminum and magnesium components. Quality is fundamentally influenced by the casting and cooling processes, where cavities and gas pores are difficult to avoid. In an attempt to optimize the manufacturing process, many companies try to determine the area shares of fracture-prone casting defects and grade them according to size (Figure 5). Again, this can be achieved with a single scan with the Particle Analyzer without resorting to single image analysis.
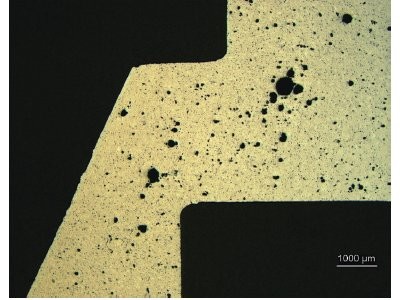
Figure 5 - Structural defects in die-cast components. Mosaic image of a total area of approx. 38 mm2. Microscope: Axio Imager, objective: EC Epiplan Neofluar 5×/0.13, camera: AxioCam MRc.
4. Plaque analysis. Many vaccines and sera are tested by setting out a dilution series of the agents in a 24-well plate together with virus particles and cells. After incubation, the wells are examined for the presence of plaques in the cell lawn caused by unneutralized viruses (Figure 6).
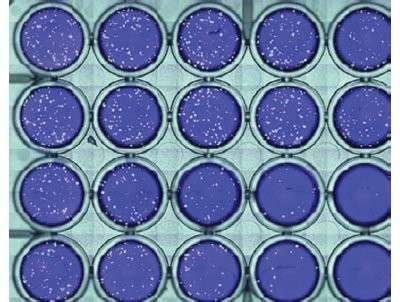
Figure 6 - Viral plaques in 24-well plate. Microscope: SteREO Discovery.V12, objective: Plan S 1.0×, camera: AxioCam MRc.
Using the Particle Analyzer, the entire plate can be scanned and the plaques automatically detected, separated, and measured, with artifacts below a specified minimum size automatically excluded. The measured data and original and result images of each plate are saved, and as an option the entire process may be validated in conformity with good practice quality guidelines (GxP).
Conclusion
The continuing integration of microscopy, digital camera technology, and computing power opens up exciting new analysis tools to relieve the tedious and repetitive tasks involved in many of today's materials analysis procedures, while profiting from the ability to meet future requirements. Above all, it is now possible to meet the seemingly contradictory requirements of characterizing whole populations of particles while simultaneously recognizing the smallest.
Mr. Lambert is Marketing Manager, Carl Zeiss Ltd., 15-20 Woodfield Rd., Welwyn Garden City, Hertfordshire AL7 1JQ, U.K.; tel.: +44 1707 871200; fax: +44 1707 330237; e-mail: [email protected].