It is well known that measuring the rheological properties of materials contributes to the development of better products and helps predict end-use performance as well as the physical properties of a product during and after processing. The choice of instrument for these analyses depends on individual objectives, for instance, whether this is purely to measure viscosity as a function of shear rate, or to determine more complex rheological properties. This paper explores some of the considerations involved in making the decision to purchase a simple viscometer or a more sophisticated rheometer. While a viscometer can offer the solution for material, process, or production tests that require simple flow measurements, the performance of a rheometer allows more detailed characterization of flow and deformation behavior.
Most viscometers normally operate by rotating a spindle in the sample, allowing determination of viscosity through measurement of resistance to this rotational force. In comparison to rheometers, they are relatively simple instruments, and it is this simplicity of design and operation that makes them easy to use and especially useful within a busy QC environment. A point to note is that although temperature control is an important parameter in ensuring data consistency, this is not a built-in function for most viscometers. Some (such as the Visco 88, Malvern Instruments, Southborough, MA) offer optional controllers suitable for fluids testing.
The movement of the spindle in a viscometer is in one direction, and this allows measurement of viscosity. Rheometers, however, can apply oscillatory and rapid step changes in stress and strain, enabling the determination of viscoelastic as well as flow properties. Such data provide information on the structural properties of the sample.
The mechanical bearing used in viscometers tends to limit the speed and torque capabilities of the instruments, with residual friction posing problems in measuring low-viscosity materials. Some of the latest viscometers use a variety of measurement geometries. This permits them to cover broader viscosity ranges and makes them suitable for many fluid applications.
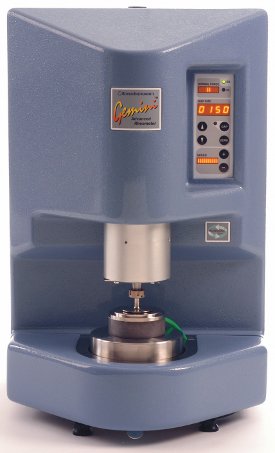
Figure 1 - Bohlin Gemini rheometer.
Rheometers
Rheometers tend to be more costly than viscometers, but are more versatile and offer a much wider dynamic range for control and measurement parameters. In a typical stress and strain controlled rheometer such as the Bohlin Gemini (Malvern Instruments) (Figure 1), a temperature control unit (TCU) is an integral part of the instrument. Several interchangeable TCUs cover different temperature ranges, and each is optimized for the best control and performance.
The use of a low-friction air bearing allows measurement of even low-viscosity samples, while the inherent stiffness of the bearing also provides the capability to measure solids. With true stress and true strain control operating modes, a complete range of rheological tests (including creep, stress relaxation, and multiwave oscillation) can be performed with full control of sample strain history.
Viscosity measurement
Rheometers function across a very wide range of shear rates . This allows simulation of real processes that occur over vastly different time scales, such as sedimentation and spraying. Table 1 shows the shear rates of processes that commonly require rheological measurement. Spraying, for example, is between 104 and 105 reciprocal seconds (sec–1) and pumping is around 1–103 sec–1. Typically, a viscometer can measure in the range of about 0.1–103 sec–1, while a rheometer extends the measurement range from 10–6 to 105 sec–1. Processes such as sedimentation are best suited to analysis with a rheometer because of its low torque capabilities. The high-speed control of a rheometer also enables the analysis of very high shear rate processes, such as spraying.
Table 1 - Shear rates of different processes
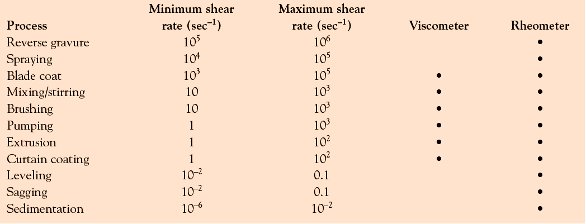
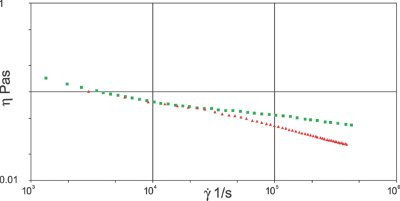
Figure 2 - Measurements at high shear rate on two pressure-sensitive adhesives that are applied by roller coating.
Figure 2 illustrates the usefulness of the extended measurement range of a rheometer. This example is for roller coating and shows a good roller coating sample (red) and a poor one (green). At shear rates below 104 sec–1, both coatings have a similar viscosity. A viscometer would find no differences between these coatings.
Yield stress and normal force
Yield stress is the force required to make a sample start flowing. This force must be overcome when a pump is switched on; it holds paint in position after application, and it can also influence a product’s shelf life and structure perception. In yogurt, for example, yield stress is an important factor in providing a thick and creamy mouth feel, but a balance must be achieved because the yield stress also has a significant effect on the pumping requirements during processing.
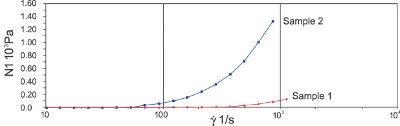
Figure 3 - Normal force measurements for paper coating samples.
When a sample is sheared, elasticity can create a force perpendicular to the direction of shear. This is normal force and is common with polymeric materials. Normal force testing can identify differences that may occur when a material is processed.
Figure 3 shows two paper coatings. These are applied to the paper surface using a blade-coating process with a narrow gap, which generates high shear rates. One coating sample has a high normal force, which acts to push the application blade away from the paper, resulting in a coating that is too thick. The other has a lower normal force and coats well. The viscosities of these samples are the same; only normal force testing showed any difference between them.
Dynamic measurements
Most materials show elastic as well as viscous properties. Measurement of viscoelasticity can provide information not given by viscometry alone. Tiny movements (small strain oscillations) can be used to measure viscoelastic properties without destroying the sample structure. Oscillatory testing generates a mechanical spectrum for the material, and this provides a unique behavior fingerprint.
The measuring geometry is oscillated sinusoidally about a fixed position, and stress and strain responses at different frequencies are recorded. The elastic and viscous components of the sample are measured and, over different time scales, the viscous and elastic nature of the sample changes. For applications such as pouring and spraying, sample elasticity is critical since it relates to snap-back properties and droplet formation. For polymers, dynamic measurements can provide details of molecular architecture, molecular weight, and molecular weight distribution.
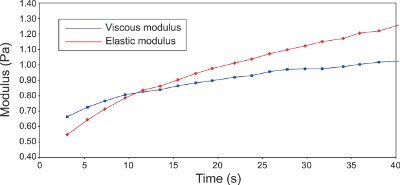
Figure 4 - Rebuild time for an ink after high shear rate deformation.
In addition to frequency sweeps, time and temperature sweeps provide important information such as curing profiles and thixotropic rebuild. Thixotropic samples (such as sauces, paints, and inks) exhibit time-dependent shear thinning followed by recovery of structure. Figure 4 depicts an ink that has been subjected to a high shear rate to simulate application by a print head. The time for structure rebuild in the ink is critical for dot retention and definition. This sample returns to a stable gel state (elastically dominated) after 12 sec.
Summary
Rheological measurements are essential for formulation, process, and material control across all industries and applications. A viscometer is a low-cost instrument that is simple to use and can offer portability for remote or field testing. It is highly suitable for quality control testing and for on-line process control.
Rheometers are a greater investment, but are essential to simulating real processes and ensuring comprehensive material characterization. High versatility and performance make rheometers excellent tools for research, product and process development, and quality control testing.
Both instruments are complementary, and it is not uncommon to find viscometers used for QC testing on products that have been developed using a rheometer.
Dr. Carrington is Product Manager, Rheology Systems, and Ms. Langridge is Applications Specialist, Malvern Instruments Ltd., Enigma Business Park, Grovewood Rd., Malvern, Worcestershire WR14 1XZ, U.K.; tel.:+44 1684 892456; fax: +44 1684 892789; e-mail: [email protected].