Element determination in solids is a multiple-stage process comprising sampling, mechanical sample preparation, and acid digestion procedures that completely convert the analytical materials into solution so they can be transferred to the analytical determination step (e.g., inductively coupled plasma–atomic emission spectroscopy [ICP-AES], ICP-MS, atomic absorption spectroscopy [AAS], or polarography) in liquid form. The goal of all digestion processes is therefore the complete dissolution of the materials being analyzed and the complete decomposition of the solid (matrix), while avoiding the loss or contamination of the analytical materials. Aside from this, the practitioner is also concerned that the digestion process is secure, reproducible, and simple, i.e., that it can be performed without excessive manual intervention.
Acid digestion processes employing various mineral acids (e.g., HCl, HNO3, HF, H2SO4, etc.), hydrogen peroxide, and other liquid reagents are carried out in either an open system (that is, at normal atmospheric pressure) or in closed vessels. Further, the solution can be heated either by convection or in microwave ovens.
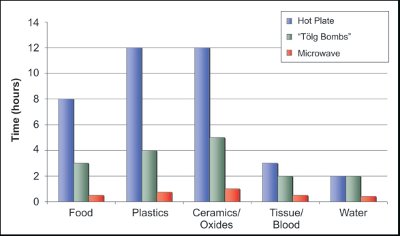
Figure 1 - Typical times required for digestion.
The advantage of this closed procedure in comparison with open digestion under reflux or with the traditional hotplate lies in the significantly higher working temperatures that can be achieved. While in open systems these temperatures are limited by the acid solution’s boiling point, temperatures in the 200–260 °C range can be typically achieved in sealed digestion vessels. This results in a dramatic acceleration of the reaction kinetics, allowing digestion reactions to be carried out in a matter of hours (pressure digestion using Tölg bombs1 [Figure 1], so-named for Prof. Dr. Günther Tölg, Max-Planck Institut für Metallforschung, Schwäbisch, Germany). However, these methods also make it clear that the temperature itself actually represents the most significant reaction parameter. It is the ultimate determinant of the digestion quality, but also results in a pressure increase in the vessel and thus in a potential safety hazard. Therefore, the pressure must also be ultimately considered.
Over the past years, microwave heating of digestion solutions has increasingly gained popularity. In this process, the wet-chemical digestions are performed in closed vessels made of chemically inert materials that are transparent to microwave radiation. Aside from the above-described acceleration in the reaction kinetics resulting from the use of a closed system, direct heating of the sample solution produces a further reduction in digestion times (see Figure 1). On the other hand, the physical and chemical nature of microwave heating also produces several problems that must be taken into account in the design or selection of such a system:
- Heating in the microwave field is dependent on the type of sample and the sample volume, etc. Only in rare instances will two samples behave in an identical manner. Therefore, for safety reasons as well as to ensure optimal reproducibility, the uneven heating of samples in the microwave field must always be taken into consideration.
- The rapid heating of the sample solution may induce exothermic reactions during the digestion process. For this reason, a wide variety of sensor systems have been developed to monitor pressure and temperature reaction parameters and thus possibly control the microwave output.
Only materials that are completely chemically inert against the employed mineral acids and reagents may be used in the construction of the pressure vessels. Particularly hard plastics (e.g., polyetheretherketone [PEEK]) have only limited microwave transparency and acid resistance and are therefore not suitable.
Pressure digestion in Tölg bombs
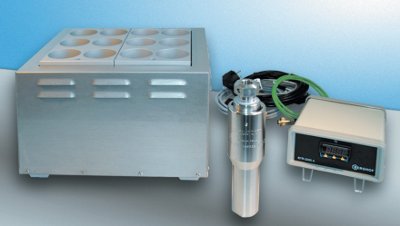
Figure 2 - Stainless steel pressure digestion system with a 12-sample heating block and temperature regulator.
More than 30 years ago, BERGHOF Products + Instruments (Eningen, Germany) introduced a series of products based on the pressure digestion method developed by Prof. Tölg.1 Since that time, the company has produced the stainless steel pressure digestion vessels with a TFM™ (Dyneon GmbH & Co. KG, Burgkirchen, Germany) PTFE liner under the trade name “digestec” (Figure 2). The vessels are available in a variety of capacities ranging from 25 to 250 mL, a maximum operating temperature of 260 °C, and a maximum operating pressure of 200 bar. In any case, safety is ensured by an appropriately dimensioned pressure relief device. For safety reasons, heating takes place in special heater blocks and not in a laboratory oven. Therefore, digestion is generally carried out at a specific external temperature. This leads, due to the thermal isolating effect of TFM-PTFE liners, to a slow, gentle, and therefore safe heating of the samples. Final operating temperatures are typically reached after 45–60 min.
Due to the high maximum operating pressure of 200 bar and the maximum operating temperature of 260 °C, the systems are capable of completely digesting nearly any sample and transferring it into solution. A decisive advantage of this methodology lies in its ability to extend the digestion period nearly indefinitely. This allows even the hardest samples (e.g., SiC and alpha Al2O3) to be completely dissolved (Table 1).
Table 1 - Application examples for pressure digestion in stainless steel pressure digestion systems
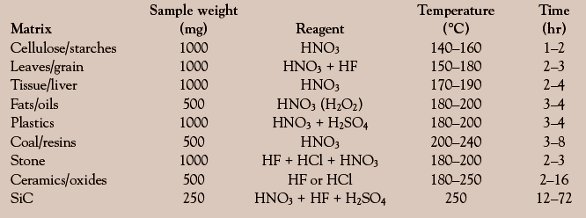
The digestec digestion system offers a very high level of flexibility and represents an economical alternative to microwave digestions, particularly for laboratories that process only a limited number of samples.
Pressure digestion with microwave heating
In contrast to the pressure digestion systems described above, samples in digestion equipment heated by microwaves are heated directly by the absorption of microwave radiation. This allows for extremely rapid, simultaneous heating of, typically, 8–12 sample solutions, which represents the actual “microwave effect” or advantage of microwave heating. Once the setpoint temperature is reached, the decomposition reactions proceed at the same rate as in conventionally heated stainless steel pressure digestion vessels. Thus, typical microwave digestions take merely 20–40 min (Table 2). The strength of microwave digestion lies in its significantly higher sample throughput, resulting from the decrease in the duration of digestion.
Table 2 - Application examples for pressure digestion in microwave pressure digestion systems
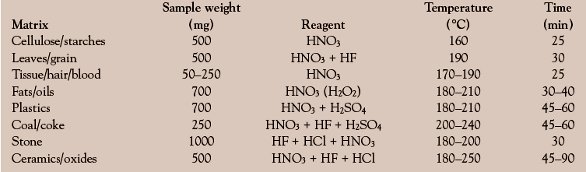
However, since this rapid heating is accompanied by an equally rapid pressure increase and, possibly, spontaneously induced exothermic reactions, the temperature progression of each sample must be continuously recorded and the microwave power must be regulated accordingly. From a safety aspect, it is therefore most practical that the pressure progression be recorded in parallel with the temperature, and that this measurement also be employed to influence power regulation. In this way, optimal process control can be achieved, particularly from the point of view of safety.
It was on the basis of these underlying considerations that the speedwave MWS-3+ microwave digestion system (BERGHOF Products + Instruments, Figure 3) was developed. Technologies specifically developed and patented to measure both temperature and pressure were implemented for this application. With the aid of a mid-IR thermometer, the temperatures of all sample solutions are measured directly, that is, without time delay and without contact, by measuring the development of the vessel wall temperature. The optional optical pressure monitoring permits the acquisition of the internal pressure of all vessels (also contact free). Neither technique requires the measurement of a reference vessel. Combined, temperature and pressure monitoring offer optimal process control, particularly from the point of view of safety.
Beyond this, the system’s top-loading design combined with vessels that consist of only a few components ensure that handling is as simple as possible. The digestion vessels themselves have been designed to provide a long service life.
Conclusion
In summary, it can be stated that today practically all sample materials can be digested with an appropriate pressure digestion system. In the majority of cases, microwave-heated systems represent the more economical solution due to their higher sample throughput rate over a given period of time. For samples that are extremely difficult to digest, or when high sample throughput is not required but a very high degree of flexibility is essential, the “old” stainless steel pressure digestion vessels continue to be the systems of choice.
Reference
- Kotz, L.; Kaiser, G.; Tschöpel, P.; Tölg, G. Z. Anal. Chem. 1972, 260, 207–9.
Dr. Gutwerk is Manager, Laboratory Technology, BERGHOF Products + Instruments, GmbH, Harretstraβe 1, 72800 Eningen, Germany; tel.: +49 7121 894 0; fax: +49 7121 894 300; e-mail: [email protected]; home page: www.berghof-instruments.de.