The trend in many of today’s laboratories is toward high throughput and low-volume samples. Competition is driving the need to enhance productivity and efficiency. Many protocols also require the elimination of sample-to-sample cross-contamination, as well as operator protection from pathogens. To satisfy this trend, more and more laboratories are looking toward automation to help manage their sample load.
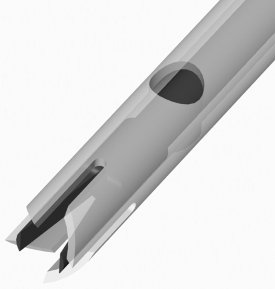
Figure 1 - Omni Tip plastic generator probe.
Rotor stator technology is a highly efficient method utilized by many laboratories to homogenize, disrupt, emulsify, and blend a broad range of samples, including tissue samples. When rotor stator homogenizers are used, sample processing times are generally very short, often requiring only 30–90 sec. However, stainless steel homogenizing probes can require an additional and tedious cleaning step of several minutes per sample, and even then, sample-to-sample contamination cannot be totally eliminated. This additional cleaning step can limit the number of samples processed by an individual technician to 10–15 samples per hour. When plastic probes such as patented Omni Tips (Figure 1) (Omni International, Marietta, GA) are used, batch cleaning or disposal of the probes is possible, thereby increasing the number of samples processed by a single operator in an hour to 30 or more. These plastic probes offer the additional benefit of clarity, thereby assuring that sample is not lost within the probe. Simple two-piece construction facilitates easy cleaning and reduced cross-contamination. Their low cost makes it practical to own large quantities of probes, which can be collected after processing and autoclaved or chemically cleaned in large batches, reducing cost to pennies per use. For critical samples, the probes can even be discarded after use. They are available in soft tissue versions for sensitive cell disruption, or in hard tissue versions, tough enough to process frozen tissue and for most applications that previously required stainless steel probes. Additionally, a broad range of sealing cap solutions are available to work with the probes.
Robotic systems are available that can increase the number of samples homogenized to 95 samples per hour. These systems are efficient, but can cost in excess of $30,000 and require a large amount of bench space. They utilize stainless steel probes, which require a between sample probe cleaning step, and therefore cannot process samples in sealed tubes, and also may not fit under most laboratory fumehoods.
The Omni Prep Programmable Homogenizing System (patent pending) (Omni International) is designed to eliminate this processing bottleneck, while also addressing the shortcomings of existing approaches to rotor stator homogenizing methods. The system is 400 mm × 200 mm × 300 mm, which makes it small enough to easily fit into a fumehood, and also preserves precious laboratory bench space. The system is designed around a rack system that allows six samples to be processed simultaneously. By utilizing a second rack, six more samples can be prepared while the first rack is processing. By continuously feeding, unloading, and loading racks, a single operator can process up to 250 samples per hour. Operator fatigue and repetitive motion injuries that can result from manually homogenizing a large number of samples per day are also eliminated, while a single technician can perform the work of eight.
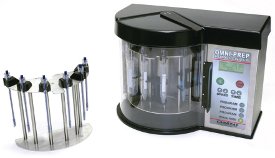
Figure 2 - Configuration of Omni Prep Programmable Homogenizing System.
The racks are designed to accommodate a broad range of sample sizes and tubes, ranging from 2.5 mL to 50 mL, and are supplied in fixed or movable configurations. The fixed rack is well suited for processing samples that require sealed tubes, while the moveable version is suitable for processing samples that require probe mobility within the sample. A cooling tray is also available to keep sensitive or frozen samples cold during the homogenization step. A clear plastic door protects the operator, and a fandriven positive airflow pattern moves air away from the front of the instrument for exhaustion into a fumehood or through a HEPA filter (Figure 2).
Mr. Jahn is President, Omni International, Inc., 1000 Williams Dr., Ste. 1024, Marietta, GA 30066, U.S.A.; tel.: 800-776-4431; fax: 770-421-0206; e-mail: [email protected].