The level of greenhouse gases such as CO2 is believed by scientists to have a dramatic, unfavorable impact on worldwide climate change. In recent years, many individuals and organizations have analyzed how the overall use of energy and its by-products contribute to the generation of greenhouse gases. Subsequently, new approaches have been developed to reduce the contribution of these gases to the atmosphere. While the long-range reduction of greenhouse gases will likely be achieved by the development of new approaches to power generation and broad changes in energy consumption (e.g., transportation), in the short term, significant reductions in the generation of greenhouse gases can be obtained by analyzing energy consumption patterns and implementing alternative techniques that reduce the amount of energy consumed by various processes.
The generation of nitrogen gas for the laboratory is an excellent example of how a significant reduction in the generation of greenhouse gases can be brought about by selecting an alternative process that performs the desired operation while consuming less energy. Nitrogen gas is commonly used in a broad range of applications in the laboratory; typical applications include gas chromatography, liquid chromatography with mass spectroscopy detection, Fourier transform infrared spectroscopy, inductively coupled plasma spectroscopy, glove boxes, and blanketing of reactions that require an inert atmosphere.
High-purity nitrogen gas for laboratory applications is normally obtained by the fractional distillation of air. This process requires a considerable amount of energy since the air must be compressed and chilled to below the vaporization point of nitrogen (–195.8 °C at 1 atm) to liquefy it. The liquid nitrogen is then vaporized to produce nitrogen gas. Since the gas is usually generated at a facility that is somewhat distant from the site at which it will be used, it is then stored in bottles or tanks and transported to the end user’s facility. Once the gas has been consumed, the empty bottle must eventually be transported back to the distillation site to be refilled. The overall energy that is required to operate the fractional distillation facility and to transport the tank to and from the end user’s site is a significant contributor of greenhouse gases such as CO2 in the atmosphere.
An alternative approach to the generation of nitrogen gas in the laboratory uses a hollow fiber membrane to separate the desired gas from air with a high degree of purity. The only power that is required by a system that uses a hollow fiber membrane is the electrical power needed to operate a compressor to deliver the air to the membrane.
This paper compares the various approaches for the generation and delivery of nitrogen gas to the laboratory; discusses the energy considerations that are required for each operation in the two processes; compares the greenhouse gas emissions; and shows how the use of a membrane-based system to supply nitrogen gas provides a safer, lower-cost, and more convenient, effective approach to providing nitrogen in the laboratory.
Nitrogen generation by fractional distillation of air
Commercially, the fractional distillation of air producing nitrogen and oxygen is an energy-intensive process that is normally performed on a continuous basis on a large scale. Typically, commercial facilities are designed to generate hundreds or thousands of tons of the gases per day. While each fractional distillation facility is specifically designed to meet the needs of the customer base and the nature of the available energy input, the following is a general description of the various operations required to obtain nitrogen from air:
Table 1 - Composition and boiling points of the components of dry air

- Air is withdrawn from the atmosphere using a compressor
- The compressed air is chilled to approximately 10 °C and passed through a moisture separator; an oil absorber; and molecular sieves to remove water vapor, oil, particulate matter, and other contaminants
- The dried, purified air enters a multipass heat exchanger and then a Joule-Thompson type expansion engine to cool and liquefy the air
- The liquefied gas is vaporized and purified (if necessary); nitrogen boils and vaporizes before oxygen (see Table 1)
- The purified nitrogen gas is pressurized and stored in bottles or tanks
- The nitrogen bottles are transported from the distillation site to the end user.
A number of small-scale liquid nitrogen generators based on the fractional distillation approach for operation in the laboratory are available. These systems operate in a similar manner as the large-scale commercial systems, or use a pressure swing absorption technology, employing carbon molecular sieves. These smaller systems can generate on the order of 50–100 L of liquid nitrogen per day. Once the liquid has been generated, it is allowed to evaporate, producing gaseous nitrogen. While these systems eliminate the transportation issues, they still require significant energy input. Because the volume from such a system is smaller than the large “industrial-scale systems,” economies of scale suggest that these are even more energy-intensive than the large systems normally used. In addition to the significant energy input required to liquefy the gas, the user should consider the possibility of personal injury from contact with the liquid.
Nitrogen generation using an in-house hollow fiber membrane system
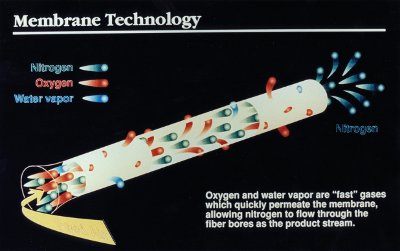
Figure 1 - Hollow fiber membrane bundle separates nitrogen from air. Oxygen and water vapor permeate the membrane, allowing nitrogen to flow through the tubes (reproduced with permission from Parker Hannifin Corp., Haverhill, MA).
Pure nitrogen for laboratory use can be readily obtained from air using an in-house hollow fiber membrane system. The membrane module, which is the heart of the system, is designed to preferentially allow oxygen and water vapor in the air to quickly permeate the membrane wall (Figure 1) while nitrogen travels through the hollow fiber out the end.
The processes involved in the in-house generation of nitrogen using a hollow fiber membrane system include:
- Air is withdrawn from the atmosphere using a compressor
- The compressed air passes through a high-efficiency coalescing filter to remove water vapor and particulate matter
- The clean, dried air passes through an activated carbon filter, removing hydrocarbons before entering the separation module
- The stream passes through hollow fiber membranes to separate the oxygen and any remaining water vapor from the nitrogen-enriched gas stream (see Figure 1)
- The nitrogen passes through a final filter, which contains coalescing or activated carbon, if required, based on the application to ensure a clean, commercially sterile supply of high-purity nitrogen
- The nitrogen supply passes directly to an outlet port of the system that is directly connected to the device in which the gas is required.
The hollow fiber has a small internal diameter, and thousands of fibers are bundled together to provide a large surface area to provide the desired flow of nitrogen. In a typical system, a high-purity gas greater than 99.5% N2 at a flow rate up to 467 L/min at an outlet pressure of 100 psig can be obtained. A schematic diagram of a typical system for the generation of nitrogen is shown in Figure 2.
Additionally, the hollow fiber membrane technology can be used to dry air. If desired, a nitrogengenerating system can be combined with a dryer membrane module to supply individual streams of dry air, source exhaust, air, and nitrogen (e.g., for an LC-MS system).
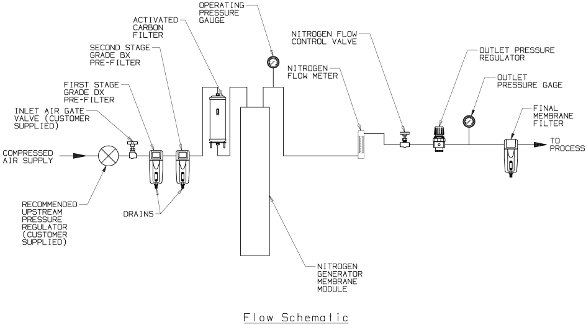
Figure 2 - Schematic representation of Parker Balston N2-14 nitrogen generator (Parker Hannifin Corp.) (reproduced with permission from Parker Hannifin Corp.).
Energy considerations for obtaining nitrogen using the fractional distillation of air
Obtaining nitrogen using the fractional distillation of air is a very energy-intensive process because it is necessary to condense the ambient air into the liquid form by cooling it and compressing it. While the amount of energy that is required clearly depends on the dynamics of the system used, it is apparent that a considerable amount of energy must be expended. Once the nitrogen has been separated from the air, it is necessary to employ additional energy to purify it to the desired level and fill the bottle.
In addition to the energy required for the fractional distillation process, a significant amount of energy is required to transport a bottle of gas from the distillation site to the end user. The amount of energy required to transport the bottle is dependent on the distance from the plant to the end facility. If, for example, the gas bottles are delivered by a truck that travels 10 miles/gal and must travel 50 miles to deliver 100 bottles to the end user’s facility, an energy consumption of 0.05 gal of fuel per bottle is required to deliver the bottle, and 0.05 gal of fuel to return the bottle to the distillation site, for a total energy consumption of 0.1 gal of fuel per bottle (this can be significantly higher if the tank is delivered to a severely congested area).
Energy considerations for obtaining nitrogen using a hollow fiber membrane system
When a hollow fiber membrane system is used for the generation of nitrogen, the only energy that is required is the energy used to power the compressor that supplies air to the system. Assuming a 3-hp compressor is used with a 50% duty cycle, the equivalent of five 9000-L tanks of nitrogen can be generated per day at an approximate power expenditure of 25 kWh (kilowatt-hour). Since the nitrogen system is normally directly connected to the instrument, no energy is required for transporting the gas.
Comparing the greenhouse gas contribution for the generation of nitrogen by fractional distillation and a hollow fiber membrane
Clearly, the amount of greenhouse gas that is generated by providing nitrogen gas to the laboratory is dependent on the mode of generation as well as the manner of delivering the gas to the end user. In addition, the manner in which the expended energy is created is a critical issue. The energy employed for fractional distillation and operation of the compressor is very dependent on local considerations (fossil fuels, nuclear, wind, biomass, etc.), while the energy required for transport of the gas to the end user is clearly derived from fossil fuels. The use of a hollow fiber membrane for the generation of nitrogen utilizes significantly less energy and hence generates less greenhouse gas than fractional distillation. Additionally, less energy is required for the isolation of the gas, and no transportation of heavy bottles is required.
Comparing the cost of bottled nitrogen and nitrogen obtained via a hollow fiber membrane system
Table 2 - Annual costs; in-house generation versus high-pressure tanks (in $U.S.)*
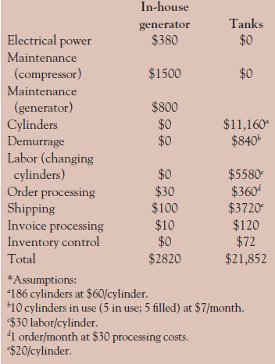
An in-house hollow fiber membrane system can provide a significant economic benefit compared to the use of bottled nitrogen, in addition to the environmental benefits. As a conservative example, the cost of the two approaches is compared for a facility that has an LC-MS system that uses a flow of 20 L/min (slpm) of N2 for 4 hr per day. Over the period of one year (250 days), 1,200,000 L of N2 will be consumed, equivalent to 186 standard 9 × 56 in. cylinders. An estimate of the various costs for the use of the gas generator versus the use of tanks to deliver the gas is presented in Table 2. It can be seen that considerable savings can be obtained using a nitrogen generator. Since the capital expenditure for the compressor and gas generator is approximately $18,000, and the annual cost savings is $19,032, the payback period is slightly more than one year. The payback period will vary depending on the local situation. Some LC-MS systems use in excess of 50 slpm of nitrogen and operate 24 hours per day, 7 days per week. In these situations, a quicker payback will be realized. In addition, the price of electrical power, labor, and gas tanks will vary for each facility.
Conclusion
The in-house generation of nitrogen gas using a system that employs hollow fiber bundles is environmentally friendly and an effective, energy-efficient approach to providing pure, clean, dry nitrogen gas to laboratory instrumentation. Since considerably less energy is expended to generate the gas, less greenhouse gas is created.
In addition, using in-house generation of nitrogen in the laboratory is a convenient, safe, and cost-effective approach to the problem of supplying the gas. The gas can be readily generated on an as-needed basis at pressures and volumes that meet the needs of typical instrumentation. A significant benefit of the membrane approach is that considerably less energy is required, thereby reducing the generation of greenhouse gases and helping to protect the environment.
Dr. Froehlich is President, Peak Media, 10 Danforth Way, Franklin, MA 02038, U.S.A.; tel./fax: 508-528-6145; e-mail: [email protected]. Mr. Cardarople is a Senior Engineer, Parker Hannifin Corp., Filtration and Separation Division, Haverhill, MA, U.S.A. The authors would like to thank Pat Kriwoy, District Manager, Canada, Parker Balston Analytical Gas Systems, for support in the preparation of this paper.