Polystyrene (PS) continues to be used worldwide because of its excellent physical properties and low cost. PS and its related plastic products are nonbiodegradable in the natural environment.1 The conventional method for degradation and polymer recycling is pyrolysis. However, the use of this technique is hindered by the complexity of the process and by practical problems. Enhancement of the degradation rate is possible through the use of catalysts.2 The most commonly used catalysts in the catalytic degradation of PS are solid acids and bases,3–6 which are known for their ability to cleave C–C bonds for use in the petroleum industry.3,4,7 Lee et al.3,4 obtained a styrene yield of 60.1 wt% with HNZ and 62.6 wt% with HZSM-5 using PS degradation at 400 °C. On the contrary, Tae et al.5 reported low yield of styrene (<58 wt%) in PS degradation with acid-treated halloysite clays at 400 °C. However, relatively few studies have been performed using solid base and transition metal catalysts. Ukei et al.6 reported that solid bases, especially BaO, were more effective catalysts than solid acids (HZSM-5 and silica-alumina) for the degradation of PS to styrene monomer and dimer at 350 °C. Kim et al.8 used base-promoted Fe catalysts for the reduction of carbon oxide by a hydrogenation route and obtained 71.8 wt% of styrene with Fe-K/Al2O3 catalyst.
In the present study, the authors investigated the performance of base catalysts (MgO, BaO, and CaO) on the degradation of polystyrene to styrene monomer. Special focus will be placed on mixing the catalyst with polystyrene particles in a reactor to increase the rate of degradation.
Experimental
Materials and methods
The sample was produced from waste polystyrene. For catalytic degradation, representative samples of PS were rubbed and converted into small granules. The catalytic degradation of PS was carried out in a batch reactor. A mixture of PS and the catalyst was loaded into a borosilicate glass reactor and heated at 400 °C. The distillate from the reactor was collected in a cold trap over a predetermined pyrolysis time period. Heating was via an external electrical heater and the temperature was monitored using a thermocouple. The degradation of the PS gave off gases, liquids, and residues. The residue refers to the carbonaceous compounds remaining in the reactor and deposited on its walls. The condensed liquid samples were analyzed using a model 6000 Vega Series 2 GC (Carlo Erba, Milan, Italy) equipped with a flame ionization detector. Separations were carried out on an OV 210 3% GCAW (GC acid wash) packed column (Carlo Erba) of 1.8 × 0.4 cm i.d. with a mesh size of 100/120. The temperature was programmed from 35 to 45 °C at 1 °C/min, from 45 to 60 °C at 5 °C/min, and from 60 to 140 °C at 10 °C/min with a hold time of 5 min. Nitrogen was used as a carrier gas at a flow rate of 20 mL/min. The detector temperature was adjusted to 300 °C and the injector to 220 °C.
Liquid column chromatography was used to separate the different groups of hydrocarbons present in the derived liquid. Silica gel 60 (63–200 μm grain size, Merck, Darmstadt, Germany) was packed into a borosilicate glass column and the liquid from the degradation of PS was applied to the top of the column. The column was then eluted with n-hexane, benzene, and methanol to produce aliphatic, aromatic, and polar fractions of the pyrolysis oil, respectively.
Fractional distillation was carried out to separate different boiling point hydrocarbon fractions from the liquid derived from the catalytic pyrolysis of waste polystyrene. The liquid was distilled at a specific temperature until no more distilled products were collected. The fractions obtained by this method were characterized using density, refractive index, refractive index parameter (I), refractivity intercepts (RI), and molar refractivity (γM). The refractive indexes were calculated with an Abbe refractometer (model P20, Nikon, Warsaw, Poland).
Results and discussion
Yield of the pyrolysis products
Table 1 - Product distribution in the catalytic degradation of polystyrene at 400 °C
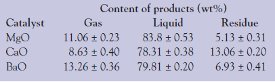
PS was degraded in the presence of base catalysts at 400 °C for 2 hr with MgO and 3 hr with CaO and BaO. The results are given in Table 1. The amount of gas products was calculated by subtracting the sum of weight for liquids, residues, and catalysts with coke from the total weight of PS sample, and the catalyst loaded to the reactor for degradation. Carbonaceous compounds adhering to the reactor wall were dissolved in n-hexane and measured as degradation residues. In all catalytic degradation processes with solid bases, liquid was the main product. MgO showed a higher yield of liquid compared to CaO and BaO for the degradation of PS, with a smaller amount of residue.
Table 2 - Distribution of hydrocarbon group types in the liquid derived from the catalytic pyrolysis of polystyrene at 400 °C
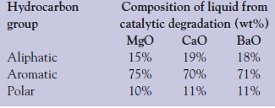
Separation of liquid on a silica gel column and analysis on a GC were carried out to determine the distribution of hydrocarbon type in the liquid (Table 2). The sample was eluted with n-hexane for aliphatic, benzene for aromatic, and methanol for polar hydrocarbons. The maximum number of hydrocarbons eluted with benzene was 75, 71, and 70 wt% using MgO, BaO, and CaO as catalyst, respectively. This shows that the major products are aromatic hydrocarbons in the liquid from the catalytic degradation of PS (fifteen weight percent of aliphatic hydrocarbons present in the liquid product derived from PS with MgO and 18 and 19 wt% with BaO and CaO catalysts, respectively). With MgO, BaO, and CaO catalysts, the amount of polar compounds in the liquid products is 10, 11, and 11 wt%, respectively.
Table 3 - Aromatic component distribution in the liquid product
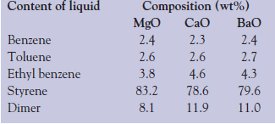
The main products, aromatic hydrocarbons, are identified and quantified by GC and UV-VIS spectrophotometric methods. Table 3 shows the distribution of aromatic hydrocarbons in the liquid. Catalytic degradation of PS with MgO shows the highest amount of styrene (83.2 wt%) and smaller amounts of benzene (2.4 wt%), toluene (2.6 wt%), and ethyl benzene (3.8 wt%).
Styrene was separated from the liquid by fractional distillation at 145 °C (bp of styrene). The refractive index (ηD20) and density (d20) measurements were used for the identification of styrene. The results are given in Table 4. As can be seen from the table, the refractive index and density of the liquid fraction collected at 145 °C is similar to the standard styrene monomer. Among the catalysts investigated, the properties of the liquid derived with MgO catalyst are in close agreement with the styrene monomer. The molar refraction calculated for styrene with MgO is 36.379 and for standard styrene monomer is 36.380, compared to CaO and BaO (36.358 and 36.368, respectively).
Table 4 - Physical parameters of the fraction at 145 °C from fractional distillation of the liquid derived from catalytic degradation of polystyrene

The main components in the liquid obtained by solid bases were styrene monomer. This shows that the catalytic degradation on solid bases may start with the formation of carboanions by the elimination of a hydrogen atom of PS adsorbed on base site, as shown in Figure 1.1
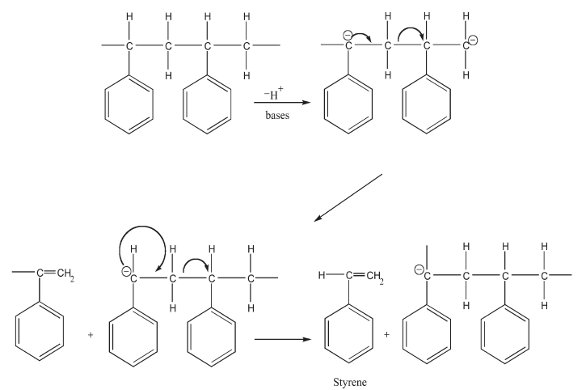
Figure 1 - Mechanism proposed by Zan et al.1 for the initiation and depolymerization of PS in the presence of base catalyst.
The depolymerization reaction proceeds automatically with the transformation of electrons through the carbon atoms of the polymer chain. The solid bases were found to be more effective for the recovery of styrene from PS. Among the solid bases used, MgO was the most effective, and more than 83 wt% of PS was converted into styrene monomer at 400 °C with 2 hr degradation time.
Conclusion
Solid bases are effective catalysts for the chemical recycling of polystyrene waste into styrene, and of the solid bases employed, MgO is the most effective catalyst, with minimum residue. Approximately 83 wt% of polystyrene was converted into styrene when MgO catalyst was used for the degradation at 400 °C for 2 hr.
References
- Zan, L.; Wang, S.; Fa, W.; Hu, Y.; Tian, L.; Deng, K. Polymer2006, 47, 8155.
- Karmore, V.; Madras, G. Adv. Environ. Polym.2002, 7, 117.
- Lee, S.Y.; Yoon, J.H.; Kim, J.R.; Park, D.W. Polym. Degrad. Stab.2001, 74, 297.
- Lee, S.Y.; Yoon, J.H.; Kim, J.R.; Park, D.W. J. Anal. Appl. Pyrol.2002, 64, 71.
- Tae, J.W.; Jang, B.S.; Kim, J.R.; Kim, I.I.; Park, D.W. J. Solid State Ionics2004, 172, 133.
- Ukei, H.; Hirose, T.; Horikawa, S.; Takai, Y.; Taka, M.; Azuma, N.; Ueno, A. Catal. Today2000, 62, 67.
- Ali, S.; Garforth, A.A.; Harris, D.H.; Rawlence, D.J.; Uemichi, Y. Catal. Today2002, 75, 247.
- Kim, J.S.; Lee, W.Y.; Lee, S.B.; Kim, S.B.; Choi, M.J. Catal. Today2003, 87, 59.
The authors are with the Institute of Chemical Sciences, University of Peshawar, Peshawar 25210, N.W.F.P. Pakistan; tel./fax: +92 91 9216652; e-mail: [email protected].