From research to manufacturing, the most commonly
used reagent in the biopharmaceutical environment
is purified water. Whether it is for a few
hours or a few days, downtime can cost companies
millions of dollars in lost manufacturing capacity
and research time. To avoid these costs, a maintenance
and support plan for purified water systems is
essential for any facility.
Although relatively simple to operate, today’s pure water systems incorporate complex purification and
monitoring technologies to ensure the systems meet
user and regulatory requirements. All such systems
require regular maintenance to optimize reliability
and water quality and to ensure a long life span.
Poorly maintained water systems affect quality in
biotechnology organizations at every level. Water
that fails to meet user specifications, for example,
with respect to undetected organic breakthrough or
bacterial buildup, can result in lost productivity; in
manufacturing settings, this can mean ruined
batches or loss of valuable material.
The sophisticated monitoring and control capabilities
of today’s water purification systems require
that they be maintained by an engineer who is proficient
in mechanical, chemical, and electrical systems.
Few organizations have access to in-house
experts who possess this breadth of capabilities
coupled with specific system knowledge. Since
maintaining a water system generally does not fall
within the core expertise of biotechnology companies,
a contract providing access to the vendor’s
service engineers makes sense for most end users.
Choosing a maintenance plan
Experience, extent of service, familiarity with one’s
specific water system, professionalism, and reactivity
are the most important factors in selecting a
maintenance service provider. Improper or unauthorized
service can adversely affect the performance
of the water purification system in addition to
being a breach of the manufacturer’s warranty.
Best-in-class plans include full documentation of
preventive maintenance, meter calibration while
permitting (if necessary) system qualification, and
U.S. Pharmacopeia (USP) suitability testing to meet
current and/or future users’ needs. Timely response
and global reach are essential for reducing downtime
and minimizing the impact of system failure.
Water system manufacturers enjoy the most comprehensive
access to parts, system engineering, and
knowledge of maintenance and operation. A manufacturer’s
access to consumables and testing equipment
ensures complete, seamless support. Another
benefit of manufacturer service providers is a clear
path to upgrading and easily expanding water systems
to meet the needs of growing companies.
Millipore Corp. (Billerica, MA) offers a total service
package for its entire range of water purification systems.
This service includes regular preventive maintenance
visits, cartridge changes, electromechanical
system checks, software system checks, and a complete
inspection of critical components such as
pumps and filter housings. All work is documented
thoroughly for system performance, testing, and
maintenance (Figures 1 and 2).
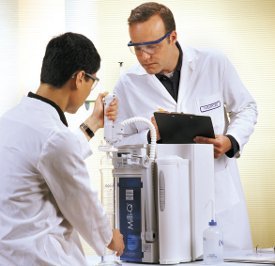
Figure 1 - Trained service engineers performing a routine validation check
on a laboratory system.
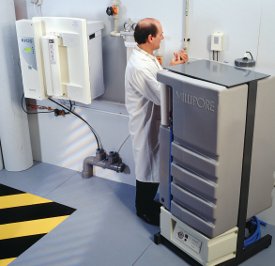
Figure 2 - Experienced laboratory technician conducting preventive maintenance
on a large system.
In addition to standard service contracts, the company
also offers extended warranties for most of its
systems. Extended warranties can be purchased as
part of a service contract and cover all electrical and
mechanical components of the system for repair or
replacement at no additional charge to the customer.
Other services include USP suitability testing and
calibration services of the total organic carbon
(TOC) and resistivity monitors.
Detailed qualification workbooks are available for
the majority of the laboratory and all central
purification and storage equipment. The qualifications
include Installation Qualification (IQ),
Operational Qualification (OQ), and preventive
maintenance procedures as well as a suggested
Performance Qualification (PQ) plan. For the past
eight years, Millipore has qualified systems at 19 of
the 20 largest pharmaceutical companies in the
world. The qualification workbooks are designed
for the systems and are executed by trained engineers.
The cost can be a small fraction of what a
private validation consultant would charge.
Additional benefits
While the primary goal of water system maintenance
is to prevent interruptions in pure water supply,
comprehensive service agreements offer substantial
regulatory benefits as well. Since
biopharmaceutical operations fall under multiple
regulatory guidelines (GMP, GLP, U.S. EPA, and
OSHA), a service provider should offer full documentation
for operation, installation, and qualification,
and compliance with all relevant regulations.
Maintenance service documentation must comply
with the appropriate regulations for each industry.
For water systems, this means system design, manufacturing
process, quality controls, traceability,
documented evidence, training for users and service
personnel, support for periodic maintenance,
qualification, and requalification considerations.
Although responsibility for complying with water
system standards rests with the end user, a comprehensive
validation and qualification service can
save companies time and money in both the near- and
long-term. Particularly in current Good
Manufacturing Practices (cGMP) settings, proper
maintenance and performance documentation can
save time and money for water system validation.
Conclusion
For the past two decades, biopharmaceutical companies
have evolved into specialty organizations
that concentrate on core competencies such as target
identification, fermentation, cell culture, and
clinical development. Today, more and more
organizations entrust manufacturers with vital
activities such as water system maintenance and
qualification. Working with a manufacturer provides
access to essential knowledge and expertise
when validating and maintaining important equipment.
As a research-based company, Millipore offers
a range of service plans for responding to the pure
water needs of its biopharmaceutical users.
Mr. Rossi is Worldwide Service Product Manager, and Mr.
Norris is Product Marketing Manager, Millipore Corp.,
Laboratory Water Div., 290 Concord Rd., Billerica, MA
01821, U.S.A.; tel.: 781-533-8662; fax: 781-533-3131;
e-mail: [email protected]