Vane rheometry continues to
become more well-known and
popular. Heterogeneous samples,
particularly those comprising
solid fillers, highly structured materials
that yield, and materials that slip,
are some general classes in which vane
spindles are useful when other geometries
do not provide acceptable measurements.
Although vanes may be inserted into
sample containers and tests run directly,
the shear rates may be undefined as material
behavior varies across large spindle-edge-to-container-wall gaps. Additionally,
some customer applications require small
volumes of sample. One such example is
the periodic testing of small amounts of
valuable pharmaceutical, gel-like products.
Therefore, the use of small vanes, in
small cylindrical containers, having both
a reasonably narrow gap for relatively well-defined
shear rates and conservation of
precious samples, is rheologically useful
geometry for rheological analysis.
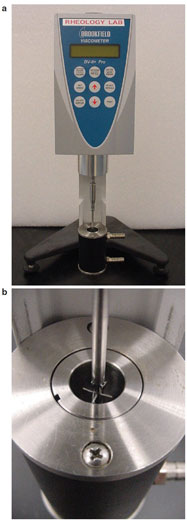
Figure 2 - Vane-in-cylinder configuration in a
small sample adapter. a) The accessory mounted
on the viscometer, and b) close-up of vane
immersed in water in the accessory.
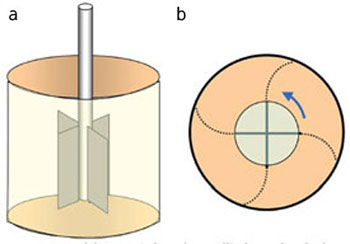
Figure 1 - Vane-in-cylinder geometry. a) Side-view schematic, and b) end-on view, showing how the
rotating four-bladed vane sweeps out a cylinder of sample material and deforms the rest of the bulk material.
Experimentalists—whether they are
technicians, chemists, engineers, or others—
often prefer to test small quantities
of materials. There are various reasons,
such as smaller amounts to clean
up, sample cost, and availability of limited
quantities. If viscosity is needed as
a function of shear rate, then an additional
constraint—well-defined geometry—is added. Viscosity-shear rate
curves are often required for pump and
process instrumentation sizing. Furthermore,
if the materials slip and/or have
yield behavior, then traditional smooth
geometries, such as coaxial cylinder, cone-plate, or parallel-plate, may have
difficulty obtaining meaningful results.
One possible solution is to use “vane-in-cylinder” geometry. The vane blades
stick out into and “grab” the sample.
The cylindrical sample chamber provides
a finite boundary. This well-defined
geometry permits shear rates to be calculated, at least to reasonable
approximations (see Figure 1a and b). In
one particular instance, pharmaceutical
samples, retained for aging stability
studies, are periodically taken and
tested over time. The use of a small
vane-in-cylinder geometry allows a
small sample quantity of precious material
to be tested while minimizing slip.
Thus, the remaining “retain” may be kept, well-sealed, in its original container,
such as a squeezable tube.
Figure 2a and b are photographs of one
vane-in-cylinder configuration used in
a small sample adapter. The vane spindle
is connected with a quick-connect
accessory to the viscometer/rheometer
coupling, and the sample chamber is
held in a water jacket. The jacket, in
turn, may be connected to a bath providing temperature control.
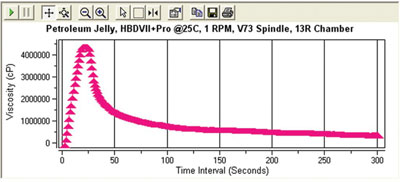
Figure 3 - Vane-in-cylinder results for petroleum jelly.
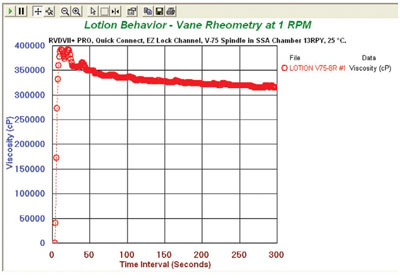
Figure 4 - Test results for a viscous lotion using vane-in-cylinder
geometry.
Petroleum jelly or petrolatum is a commercially
important material. It is often
sold neat, or used as a base for various
ointments or creams. These materials
often exhibit significant slip. Therefore,
vanes may provide better data than
smooth geometries. Figure 3 shows data
acquired by testing petroleum jelly.
The rising “viscosity” value actually
reflects increasing wind-up of the
instrument torque sensor as the motor
rotates, while the sample resists the
vane rotation. However , once the
torque reaches a maximum, the material
yields. The yield point is the point at which the solid-like material
begins to flow like a liquid,
that is, the sample structure
breaks down, and this results
in the viscosity decreasing
over time after the yield point.
This will therefore be referred
to as an apparent viscosity.
Figure 4 shows the behavior
of a viscous lotion tested with
vane-in-cylinder geometry
as well. The behavior of the
lotion is in some ways similar
to that of the petroleum jelly.
The material yields and the
measured viscosity decreases
over time as the structure
breaks down.
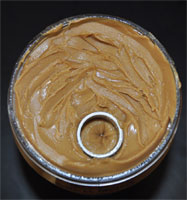
Figure 5 - Cut, disposable sample chamber
immersed in peanut butter.
The operator may be concerned
about irreversibly
destroying structure before
testing in some materials.
There is an alternative
to removing sample from
its original container and
scooping/packing it into a sample
chamber. The closed end may be
cut off from a disposable sample
chamber, for example, and this hollow
cylinder is then inserted vertically
down into the sample. The
spindle is then centered over this
area and lowered into the material.
This geometry again provides vane
rotation within a known, well-defined,
circular boundary. This in turn allows
testing at known shear rates. Figure
5 shows an example in which a cut
chamber is immersed in peanut butter.
Results from this type of test are shown
in Figure 6.
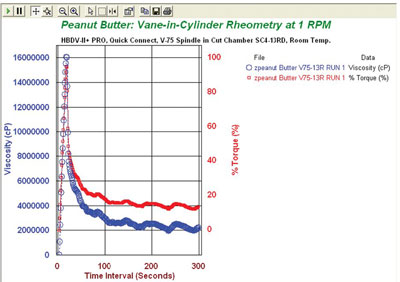
Figure 6 - Test results for vane-in-cylinder geometry
using a cut, disposable sample chamber immersed in peanut
butter.
Some materials have such severe
structural breakdown and/or slip after
yield that the apparent viscosity may
eventually become almost negligible
afterward. Other materials, such as
the lotion and peanut butter discussed
above, may have sufficient structure
after yielding so that their apparent
viscosity approaches a steady-state or
“nearly constant” value. This may be
referred to as the “steady-state viscosity
after yield.”
In sum, vane-in-cylinder geometry
proves useful for testing small amounts
of materials within a well-defined geometry.
It provides meaningful data for
materials that may exhibit slip and for
those that may yield.
Dr. Moonay is Sales Engineer—Rheology
Laboratory Supervisor, Brookfield Engineering
Laboratory, Inc., 11 Commerce
Blvd., Middleboro, MA 02346, U.S.A.;
tel.: 508-946-6200, ext. 144; e-mail:
[email protected]; www.brookfieldengineering.com. The author thanks
his colleagues, Luis Botelho (Sales Engineer) for
performing the experiments per his request, and
David A. DiCorpo (General Manager—Laboratory
Sales) for suggesting the cut-end disposable
chambers to provide a well-defined boundary.