As more research in science and
pharmaceutical development
is dependent on understanding
and controlling the growth of
cells and complex biochemical reactions,
accurate and traceable measurement and
control of the gases used in these processes
are needed. Measuring or controlling gases
such as carbon dioxide, nitrogen, and
air has typically been done using simple
variable-area flowmeters, which have limitations
in regard to accuracy, traceability,
and maximum allowable pressure.
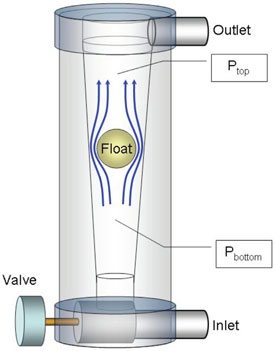
Figure 1 - Variable-area flowmeter.
These devices, which use differential pressure
to suspend a ball in a conical tube and
are typically calibrated for air as the primary
reference at room temperature and
pressure, must use correction factors for
any variation in temperature, pressure, and
gas used. By adding a metering valve at
the inlet or outlet, the height of the ball
can be adjusted and the flow of gas visually
read against the reference scale on the
tube (see Figure 1). This greatly limits the
accuracy and traceability of the devices,
and offers no method to capture or totalize
data other than by operator reading
and timed notation of a visual event. As
such, the accuracy of these devices is at
best between ±3% and ±5% of full scale,
with repeatability of perhaps no more than ±0.25% of full scale. Measurement and
control that are more accurate and traceable
to a known standard are required.
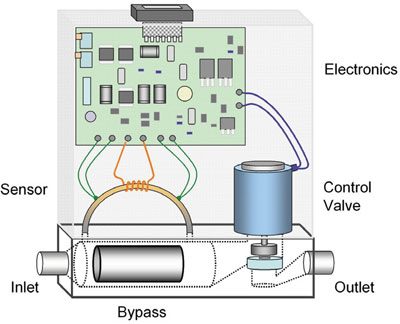
Figure 2 - Thermal mass flow technology.
MFM200 thermal mass flowmeters and
MFC202 thermal mass flow controllers
(CONCOA, Virginia Beach, VA) offer
higher accuracy and direct traceability
of flow measurement or control that is
not hampered and is minimally impacted
by changes in pressure or temperature.
As the name suggests, thermal mass flow devices use the heat transferred by a moving
gas to determine the flow of that gas.
As shown in Figure 2, the heat transfer
effect is measured in a capillary stainless
steel sensor tube with a heater at its center
and two temperature sensors arranged
symmetrically around the constant temperature
heater.
As the gas flows, it causes the temperature of
the downstream sensor to increase. The flow
is measured by comparing the difference in
the temperature sensors. Though the flowthrough
of the sensor tube is very small—at most 10 mL/min—by pairing the sensor
with a precise flow bypass or shunt that
splits the flow in a known proportion, higher
flow rates can be measured up to 20 L/min.
After assembly of each device to the respective
flow shunt, the entire unit is calibrated
against a NIST reference so that a precise
and traceable reference can be certified for
each unit against the full scale of the device.
Installation of a normally closed but highly
accurate solenoid valve with a feedback loop
creates a complete flow control device with
the ability to regulate flow and record data.
The thermal mass flow technique renders a
measurement that is essentially unaffected
by the gas pressure or temperature. The certificate
of NIST traceability is supplied with
each unit for nitrogen with specific correction
factors for air, carbon dioxide, hydrogen,
and helium (other gases are available
upon request). The accuracy of each
device is ±1% full scale, and repeatability is ±0.05% of full scale. With a maximum inlet
pressure rating of 500 psig, in comparison
to a typical variable-area flowmeter of 100–200 psig at most, these units can be used in
experiments and with systems that require
higher pressure than simple flowmeters.
The readings are directly proportional to
the 0–5 V return signal in the case of the
mass flowmeter units, and the flow is controlled
with the same input signal of 0–5 V
against the full scale of the mass flow control
units. Unlike variable-area flowmeters,
there is no visual interpretation. With mass
flowmeter and control units, all readings
and control points are traceable to NIST
by virtue of the certification supplied with
each unit. They can be used with a wide
range of gases and for most applications
since the material of construction is 316L
stainless steel, and with a broad range of
flows from 0–10 mL to 0–20 L/min.
The way to choose between these two dramatically
different technologies is determined
by the degree to which the experiment
or process needs to be automated, recorded, and traceable. If the process is fixed and requires less precision
and repeatability, then variable-area flowmeters are a prudent and
economical solution as long as the results do not require traceability.
If the process or experiment requires a highly precise measurement
or control with virtually identical repeatability, then thermal mass
flow is the technology that gives the highest precision with directly
traceable results to a known and recordable standard. As should
be expected, the technology comes at a cost that can be five- to
tenfold higher than the simpler variable-area technology. But by
offering thermal mass flowmeters and controllers that are versatile
and designed to be easy to use even for beginners to this type of flow
monitoring or control technology, the total cost can be justified
against the precision and traceability of the devices.
This technology, which was previously limited to the arenas of
manufacturing computer chips because of the units’ high cost balanced
against the need for precise control of the varied gases used
in that process, can now be employed in more routine processes.
A final important consideration is the ruggedness of the units. The
flowmeters and controllers can withstand high RF backgrounds
that may be found in process areas and university laboratories.
Mr. Gallagher is Specialty Gas Products Manager, CONCOA, 1501 Harpers
Rd., Virginia Beach, VA 23454, U.S.A.; tel.: 800-225-0473; e-mail:
[email protected].