The global energy crisis
is starting to have a significant
impact on the
world economic climate.
Record-breaking prices of crude
oil have already been reached in
2011, with costs expected to soar
again due to demand in the summer
months. The impact of high
oil prices on the general public
and commercial trade could suppress
the economic recovery following
the global financial crisis.
Nuclear power can offer some
respite from the rising energy
demands and rapidly diminishing
fossil fuel reserves. However,
nuclear power will never be able
to overcome the societal stigma
surrounding the safety of nuclear
fission; the recent incident in
Japan is testimony to this. Never
before has the pressure to resource
and develop sources of sustainable
energy and fuel been so high.
Technological advances in the production
of renewable energies mean that they are
increasingly cost-effective and efficient,
but will do little to alleviate our immediate
fuel and energy concerns. Alternative
fuels, such as biodiesel, are a sustainable
and environmentally conscious solution to
supplement fossil fuel reserves and ease the
upcoming transition between fossil and
renewable energy sources.
Biodiesel is a vehicle and heating fuel generated
from vegetable and animal fats. The
industrial process for producing this has been
optimized to produce viable fuel; however,
the raw product contains a number of contaminants
that need to be removed. Therefore,
once processed, the fuel is required to
undergo extensive chromatographic-quality
testing to detect the levels of contaminants
and determine the fuel quality. Worldwide
public and environmental safety agencies
have produced a number of regulatory guidelines
to control the levels of potentially
harmful contaminants and ensure that the
fuel can satisfy engine performance requirements.
This article discusses the methods for
assessing the quality of biodiesel products,
and examines the possible work flow solutions
to make these analyses more efficient
and cost-effective.
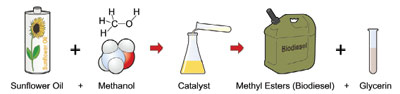
Figure 1 - Work flow diagram for the production of biodiesel.
Producing the fuel for the future
Biodiesel can be produced from a number
of virgin fatty acid sources, including soybean,
canola, olive, and other plant oils. It
may also be derived from recycled animal
and vegetable fats, and there is increasing
interest in using farmed algal species,
with inherent oil content of over 50%, as
the biodiesel oil source. The production of
biodiesel can be complicated by the presence
of impurities within the source materials
(see Figure 1). Charred foodstuffs and
solid particulates are filtered out and water
is removed by evaporation. Water in the
reaction mixture can lead to soap formation
(saponification). To maintain a cost-effective
yield, it is vital that excess water
be removed prior to the esterification of
fatty acids for the production of biodiesel.
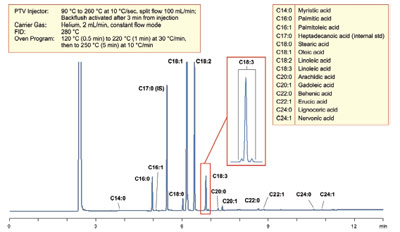
Figure 2 - Analysis of a biodiesel sample highlighting fatty acid contamination.
Feedstock samples are titrated with an alkali,
typically sodium hydroxide (NaOH), to calculate
the concentration of fatty acids (carboxylic
acids) within the source oil. The
calculated fatty acid concentration is used as
a basis for the addition of a sixfold excess of
alkalinated alcohol, typically ethanol
or methanol, to the oil feedstock
to drive the esterification of the fatty
acids to completion (Figure 2).
The esterification reaction is naturally
slow, and the addition of heat
or an alkali catalyst can increase the
rate of reaction to commercially viable
levels. Extensive heating of the
reaction is heavily energy dependent
and leads to an increase in the cost of
the end product. The base catalyzed
product is therefore most frequently
used since the addition of the NaOH
catalyst causes deprotonation of the
alcohol, increasing its nucleophilic
activity. Excess alcohol is used to
drive the reaction to completion,
and because of this alcohol is one of
the most significant contaminants in
the end product.
Contaminant quantification
The presence of excess alcohol can cause the
fuel to burn inefficiently and make it considerably
more volatile, reducing the flashpoint
to dangerous levels. For this reason,
regulatory protocols are in place to assess
the level of alcohol contamination, e.g., the
European Method EN14110 for methanol
assessment. Headspace gas chromatography
is required to accurately assess the methanol
contamination and can be coupled with
polar and nonpolar stationary phase chromatography,
typically a 100% dimethyl polysiloxane
phase such as the Thermo Scientific
TRACE TR-BioDiesel (M) (Thermo Fisher
Scientific, Runcorn, U.K.). When coupled
with a flame ionization detector, the system
is capable of measuring the level of methanol
contamination between 0.001 and 0.5%
m/m, which satisfies the regulatory limits set
out in EN14214:2003.

Figure 3 - Analysis of biodiesel for mono-, di-, and triglyceride content, in line with EN14105.
Fats and oils consist of high concentrations of
triacyl glycerides (TAGs) (Figure 2), which are based on a tri-ol (glycerine) backbone with three fatty acid side chains. Addition of
the NaOH causes hydrolysis of the ester bonds
between the glycerol and the fatty acid chains.
Glycerine is therefore the major by-product of
the reaction. Fortunately, the glycerine component
is significantly denser than the fatty
acid esters and can be separated by gravity.
Low concentrations of glycerine are required
to ensure good cold weather performance and
prevent injector port deposits from reducing
engine efficiency. The levels of glycerine
in the biofuel are carefully regulated for in
European Method EN14105 (Figure 3) and
American Society for Testing and Materials
(ASTM) Method D6751.
GC analysis for the concentration of total
glycerine requires a nondiscriminative cold
injection system that can transfer volatile and
heavy sample components to the column. A
5% phenyl polysilphenylene-siloxane
stationary
phase such as the Thermo Scientific
TRACE TR-BioDiesel (G) is coupled with
a flame ionization detector for the accurate
quantitation of the glycerine and glycerides
contained in the sample. A total glycerine
level of 0.25% m/m is permitted under
EN14214:2003 (Figure 3), and the analysis
must be capable of detecting levels of total
glycerine between 0.05 and 0.5% m/m.
Assessing fuel quality
The cetane number of a diesel fuel is a measure
of its ability to perform under compression
ignition. Cetane number is assessed by
comparing the ignition delay of a diesel fuel
with that of mixtures of cetane (hexadecane
[C16H34]) and isocetane (2,2,4,4,6,8,8-heptamethylnonane
[C16H34]). Regulatory
requirements for the cetane number of a
diesel fuel are legislated for by European
EN590 and U.S. ASTM D975.
Biodiesel may be used as a blending stock for
addition to petroleum-derived diesel fuel, or
as a pure biofuel known as B100. The cetane
number of B100 is dependent on the distribution
and availability of fatty acids within
the oils used in the initial esterification reaction.
Measuring the quantity of the fatty acid
methyl esters (FAMEs) and linolenic methyl
esters within B100 allows for an accurate calculation
of the cetane number of the biofuel.
Measurement of FAME concentration is
prescribed for by GC method EN14103 and
requires a split/splitless (SSL), or programmable
temperature vaporizing (PTV) injector,
to introduce fuel samples onto the column.
Accurate, sensitive detection and quantitation
of the FAME concentration is best
achieved on a polar GC column capable of
separating the esterified fatty acids and linolenic
methyl esters. GC analysis of a biodiesel
sample should provide verification that levels
of FAME within the sample exceed 96.5%
m/m, with the level of linolenic methyl esters
being <12% m/m. This GC method is suitable
for the separation of samples of B100 containing
FAMEs of chain length from C14 to C24.
Chromatography work flow
Sample testing such as that described above
is often an outsourced quality control measure,
with external companies providing the
chromatographic expertise. The outsourcing
analysis industry is a growing market,
with new methods and sample types being
added frequently. Establishing new chromatographic
techniques in a laboratory is expensive
in terms of the downtime and consumables
required for method validation (Figure
1). New techniques that conform to regulatory
standards can take as long as a month to
validate, during which time the instrument
and technicians are out of general service. In-house
analyses, performed by manufacturing
industries, are equally affected by the time
taken to develop new methods. A second
consideration is the consistency of measurement
between samples and column changes.
Biodiesel quality control analyses must
assess the levels of contaminating methanol
(EN14110; EN14214:2003) and glycerine
(EN14105), and meet the cetane number
requirements of ASTM directive D6751.
Although conformance to these regulations
is vital for public and environmental safety,
the expense of establishing and validating
these techniques adds to the production costs
of the fuel. In the interest of maintaining an
acceptable at-the-pump price and reducing
the impact of the energy crisis, it is essential
to keep production costs as low as possible.
To achieve this, work flow solutions that fast-track
sample analysis while maintaining the
quality of the data are needed.
One potential work flow solution is a series
of applications kits that provide all of the columns,
calibration solutions, derivatization
reagents, standards, syringes, and vials required
for the method. The Thermo Scientific ENBioDiesel
GC productivity solution and
Thermo Scientific ASTM GC productivity
solution are work flow adaptations for compliance
of biodiesel products with the European
and American regulatory guidelines. These
European and American productivity solutions
were responsible for generating the high-quality
data shown in Figures 2 and 3. The ability
to resource the method in this way, with all
the necessary consumables for validation of the
method and results, would allow the scientist
to provide data that satisfy all of the regulatory
standards in an efficient and cost-effective
manner. Biofuels will become an important
cornerstone of the energy economy of the
future. Use of work flow-enhancing products to
improve the accuracy and speed of the quality
control process will greatly assist in reducing
costs and ensure a secure energy future.
Mr. Wheeler is GC Applications Specialist,
Thermo Fisher Scientific, Chromatography
Consumables Division, Tudor Rd., Manor
Park, Runcorn WA7 1TA, U.K.; e-mail: [email protected].