A tractor trailer tanker truck with a full load of toxic chemicals traveling over a mountain pass veers off the road to avoid an oncoming vehicle; 6700 gallons of toxins begin to spill onto the bank, oozing toward a nearby stream.
The new settling pond of a fracking operation begins to leak an undetermined amount of fine sand sediment through the protective berm and into a wetland area.
A gas station attendant in a rural area discovers that the storage tanks have been slowly seeping gasoline into the properties surrounding the station, with devastating impact to the soil and the neighboring wells.
Such is our world and the environmental impact of the way we live in it.
The soil police
The U.S. EPA Office of Solid Waste and Emergency Response (OSWER) was established to provide policy and guidance for these types of environmental challenges, whether for emergency response or for ongoing waste programs. They develop guidelines for the land disposal of hazardous waste and underground storage tanks, and also manage the Superfund program, which addresses active and abandoned hazardous waste sites and accidental chemical releases.
To that end, the OSWER also issues the relevant methods to test soils for volatile organic compounds (VOCs) for compliance with the Resource Conservation and Recovery Act (RCRA). The RCRA was established in 1976 to protect human health and the environment from the potential hazards of waste disposal, and to ensure that wastes are managed in an environmentally sound manner. RCRA regulates the management of solid waste (e.g., garbage), hazardous waste and underground storage tanks holding petroleum products or certain chemicals.
Table 1 – Calibration curves (response factors at each concentration) for system performance checka, calibration checkb compounds, and select compounds of interestc for EPA Method 8260B
Soil from contaminated Superfund sites also would be tested to determine the level of contamination and progress of remediation and cleanup under the Comprehensive Environmental Response, Compensation and Liability Act (CERCLA).
Soil and water testing: switching gears
Environmental labs throughout the U.S. are always on call to engage in testing soil and water for catastrophic events such as provided above, and helping the U.S. EPA and local authorities respond to environmental emergencies is a key service they provide. In addition to the emergency response activity, these labs typically rely on ongoing, rudimentary testing of water, sludge and soils as their bread and butter business activity. Labs will run hundreds of those tests a day for local municipalities and organizations. It is in switching gears from the ongoing daily tests to the rapid response required of environmental emergencies that these labs depend on the integrity and reliability of their instrumentation.
Environmental labs performing purge-and-trap GC/MS analysis of VOCs in soil, drinking water, wastewater, groundwater and sediment samples require a versatile and reliable automation platform to transfer samples to purge-and-trap GC/MS systems without sacrificing sample integrity or data quality. Sample requirements cited in U.S. EPA methods directly affect the design and performance characteristics of VOC analysis autosampler workstations to handle this transfer. One instrument that meets the pragmatic operational needs of environmental testing labs and also fulfills U.S. EPA hardware and quality control requirements is the 4100 Soil/Water Sample Processor from O.I. Analytical, a Xylem brand (College Station, TX).
The sample processor automates the handling and processing of up to 100 soil and/or water samples in 40-mL volatile organic analysis (VOA) vials for purge-and-trap analysis of VOCs in accordance with U.S. EPA methods.
Automating purge-and-trap sample handling: Getting it right
Perfecting the automation of purge-and-trap sample handling has been challenging over the years, with the inherent complexities of the process equally frustrating instrument manufacturers and environmental lab technicians alike. Preventing sample contamination, sticky vial labels and vial jamming or dropping have all contributed to the intricacies and challenges.
The 4100, when integrated with a purge-and-trap sample concentrator (such as the O.I. Analytical 4660) into a GC/MS platform, incorporates innovative technologies that improve sample processing reliability, analytical performance, laboratory operating costs and productivity. The digitally controlled linear drive rails and pneumatically actuated VOA Constrictor™ vial gripper combine to lift and transport 40-mL VOA vials to and from the sampling station with high reliability. The electronically controlled high-speed injection valves in the Standards Addition Manifold inject user-programmed volumes of standard with no excess overfill volume or waste that fixed-loop systems require to operate, significantly reducing operating costs for expensive standards.
Table 2 – Replicate performance at 50 ppb for the species in Table 1
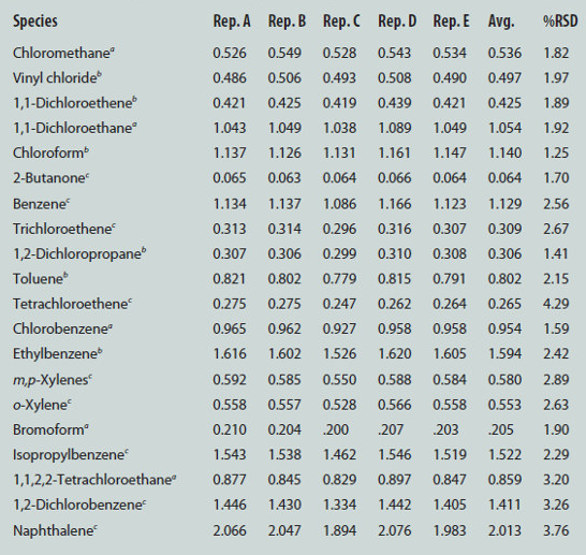
Operating the 4100 in a dual purge-and-trap configuration with a decreased purge time, enabling a total injection-to-injection cycle time of 12 min, results in a 40% time savings versus measurements with a single purge-and-trap, and would facilitate approximately 60 GC runs to be conducted in a 12-hr mass spectrometer tune time.
“For years, trying to find a consistent, dependable system was challenging at best,” explained Kirk Payne at Accurate Labs (Stillwater, OK). “The 4100 has been a workhorse in our department. Whether we’re running standardized testing of drinking water samples or I’m set up for emergency analysis of soil samples from a wreck of an oil truck, I can establish the parameters electronically through the interface, push the button and go. This product has far surpassed any of our expectations.”
Putting it to the test
Demonstrating the prescribed methodology—in this case U.S. EPA Method 8260B—prior to running actual soil samples is key to establishing instrument capability and effectiveness. The parameters used to judge the effectiveness are the response factor, the relative standard deviation (RSD) and the R² value (where appropriate). These give a statistical indication of how the system responds to changes in the concentration of the analyte of interest as the concentration changes from the bottom to the top of the calibration. In a perfect world, the response factor should be the same at each point if the response is linear. What is demonstrated in Table 1, as it relates to U.S. EPA Method 8260B, is the variation in that linearity as the calibration curve is covered. The RSD of the response factors indicates how linear and reproducible the calibration is across the whole range.
In order to meet the method parameters, the RSD of the compound response factors must be less than 15% (Group A). The exception to this is the RSD for CCCs (calibration check compounds), which must be less than 30% (Group B). As presented in Table 1, RSDs for the tested analytes on the system are all less than 10%, except for naphthalene and isopropylbenzene, which are both expected to have higher RSDs. Method 8260B accommodates these exceptions, and allows compounds that fail the 15% parameter to be analyzed using linear regression. These results are provided in Table 1 for naphthalene.
It is important to note that, in relation to the information provided in Table 1, results from an “actual sample from a Superfund site,” for example, would not add any value, as the results from a single analysis are unverifiable. The sampling and corresponding analysis process is such that the instrumentation calibration needs to be demonstrated to be within the acceptable limits defined by Method 8260B prior to actual samples being run. The instrumentation calibration data confirm and ultimately verify the 4100/4660 system as a competent and reliable tool that environmental labs can depend on for identifying VOCs in soil, sediment and other samples being tested from environmental challenges.
Listening to the market, to customers like Kirk Payne, O.I. Analytical made a concerted effort to hear what customers were saying. According to David Barclay, general manager of O.I. Analytical in College Station, TX, “We did a lot of research; we spoke to a lot of people. We ended up with a brand new product, built from the ground up. We certainly took advantage of some of the more sophisticated existing technology, but we were ruthless in eliminating the inferior traits of existing products and focusing our efforts on what the customer needs.”
Well suited for analyzing soil samples for CERCLA compliance during the remediation process of Superfund sites or from a local chemical spill, the 4100 is easily programmable for whatever the lab may need, because it was designed, developed, and built with the end user in mind.
Cynthia Elmore is GC Products Specialist, O.I. Analytical, a Xylem brand, 151 Graham Rd., College Station, TX 77845, U.S.A.; tel.: 979-690-5230; e-mail: [email protected]; www.oico.com