A novel inorganic/organic hybrid, highly temperature-resistant fluid loss agent PSA/Ca-MMT/CaCl2@SiO2 had previously been reported1 by the Drilling Fluid Laboratory of China University of Geosciences. However, Ca-MMT (calcium bentonite, lamellar structure) could not reduce yield point because of its lamellar structure. Also, the content of SiO2 was not sufficient to remain Na2SiO3 for appropriate viscosity.
SMA (copolymer of styrene and maleic anhydride), which has diverse applications,2,3 can be modified easily due to the presence of anhydride and aromatic functionalities. With granulated shape, CaCO3 is highly temperature-resistant and has lower resistance to movement than Ca-MMT.
Based on the above, an improved hybrid, high-temperature fluid loss agent with better rheological properties—SMA/CaCO3/CaCl2@SiO2 consisting of SMA, SiO2, CaCl2, and CaCO3—was prepared.
Experimental
Synthesis and characterization of SMA/CaCO3/CaCl2@SiO2
SMA was prepared by precipitation polymerization4: 0.7 g CaCO3 and 0.66 g KH550 were added to 20 mL ethanol in a flask equipped with a magnetic stirrer and reflux unit at 60 ºC for 3 hr; the solution was treated by ultrasonic wave at 60 ºC for 3 hr. Afterward, modified CaCO3 was centrifuged, and the precipitate was washed with ethanol three times to remove the excess KH550, which was absorbed on the CaCO3 surface. Finally, modified CaCO3 was dried at 110 ºC for 24 hr in vacuum.5 Graft polymer (containing CaCl2) of modified CaCO3 and SMA and encapsulation of graft polymer with silicon dioxide were prepared as PSA/Ca-MMT/CaCl2@SiO2.1
Next, SMA/CaCO3/CaCl2@SiO2 was attained. CaCO3, modified CaCO3, graft copolymer of modified CaCO3 and SMA, and SMA/CaCO3/CaCl2@SiO2 were characterized by FTIR spectra, thermogravimetric analysis (TGA), and transmission electron microscopy (TEM).
Evaluation of SMA/CaCO3/CaCl2@SiO2
Drilling fluid property tests were performed according to the specifications of the American Petroleum Institute.6 Formulation A = 3% bentonite + 0.75% sodium hydroxide + 100% H2O. Formulation B = Formulation A + 0.15% carboxymethylated cellulose (CMC) (by weight). AV and PV are associated with the viscosity of drilling fluid. YP is the yield value of the drilling fluid.
Results and discussion
The FTIR spectra of the process product and SMA/CaCO3/CaCl2@SiO2 are shown in Figure 1. There were two absorption bands at 3672 cm−1 and 1053 cm−1 for modified CaCO3 of Figure 1b assigned to –NH2 and silicon oxygen bond, suggesting that CaCO3 was modified by KH550.7
Figure 1 – FTIR: CaCO3 (a), modified CaCO3 (b), graft polymer of modified CaCO3 and SMA (c), and SMA/CaCO3/CaCl2@SiO2 (d).The absorption band at 3029 cm−1 of Figure 1c was assigned to –CH3 and the absorption bands of –CH2 were enhanced.8 Meanwhile, the bands centered at 623 cm−1, 1453 cm−1, and 3029 cm−1 in Figure 1c were stretching vibrations peaks of polystyrene within SMA. The bands appearing at 1660 cm−1 and 1570 cm−1 in Figure 1c were associated with peaks of amido bond. All of these indicated that hybrid polymers of modified CaCO3 and SMA were synthesized. Two strong bands at 1104 cm−1 and 800 cm−1 in Figure 1d corresponded to the Si–O–Si asymmetric vibration peak and silicon oxygen bond from the SiO2; moreover, other peak intensity became weak, which demonstrated that graft copolymer was encapsulated with silicon dioxide.
The TGA curves of graft polymer and SMA/CaCO3/CaCl2@SiO2 are displayed in Figure 2. From the curves of Figure 2a and b, the weight loss between 30 ºC and 200 ºC resulted from volatilization of water. The stage at 200–450 ºC was due to the loss of SMA, and at 450–750 ºC was ascribed to the disintegration of KH550. After 750 ºC, the remaining materials were CaCO3 (ash content: 20%) and CaCO3/SiO2 (ash content: 50.93%), respectively, suggesting that the wt% of silicon dioxide was 30.93%. However, the content of SiO2 within PSA/Ca-MMT/CaCl2@SiO2 was 10.91%.
Figure 2 – TGA: graft polymer of CaCO3 and SMA (a), and SMA/CaCO3/ CaCl2@SiO2 (b).
Figure 3 – TEM photographs: graft polymer of CaCO3 and SMA (a), and SMA/CaCO3/CaCl2@SiO2 (b).The TEM photographs of graft copolymer and YSW-1 are shown in Figure 3. SiO2 had a strong influence on the morphology of graft polymer since it was compactly deposited on graft polymer particle by particle from the photographs.
Tables 1 and 2 list the effect of SMA/CaCO3/CaCl2@SiO2 and PSA/Ca-MMT/ CaCl2@SiO2 on the rheological and filtration properties in Formulations A and B before and after aging tests.
Table 1 – Drilling fluid properties of PSA/Ca-MMT/CaCl2@SiO2 and SMA/CaCO3/CaCl2@SiO2 in Formulation A before and after thermal aging tests (200 ºC)*
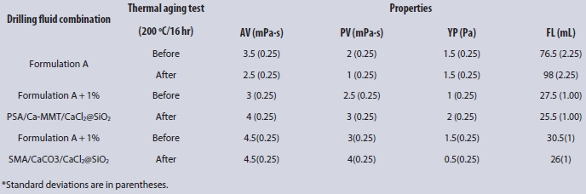
Table 2 – Drilling fluid properties of PSA/Ca-MMT/CaCl2@SiO2 and SMA/CaCO3/CaCl2@SiO2 in Formulation B before and after thermal aging tests (200 ºC)*
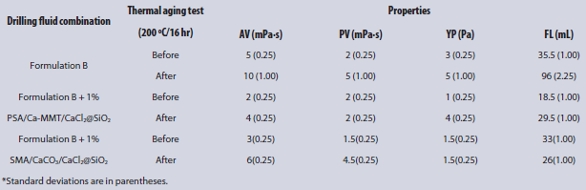
As shown in Table 1, the influence of SMA/CaCO3/CaCl2@SiO2 and PSA/ Ca-MMT/CaCl2@SiO2 on the rheological properties was minor, but the effect on filtration properties was significant at room temperature, in contrast to Formulation A. The filtration loss of SMA/CaCO3/CaCl2@SiO2 was approximately the same with PSA/Ca-MMT/CaCl2@SiO2. At room temperature, a minimal amount of SiO2 was released from PSA/Ca-MMT/ CaCl2@SiO2 and SMA/CaCO3/CaCl2@SiO2 in alkaline solution. They then all reacted with Ca2+ to generate CaSiO3 (calcium silicate); thus the filtration loss was almost the same.
After the thermal aging tests (200 ºC), the effect of SMA/CaCO3/CaCl2@ SiO2 on the AV, PV, and YP was greater than PSA/Ca-MMT/CaCl2@SiO2, but the fluid loss was larger than PSA/Ca-MMT/CaCl2@SiO2. At 200 ºC, SiO2 had released from the surface of PSA/Ca-MMT/CaCl2@SiO2 and SMA/ CaCO3/CaCl2@SiO2. However, the drilling fluid of SMA/CaCO3/CaCl2@SiO2 had higher viscosity because there was residual Na2SiO3 due to more SiO2. Plus, it had a lower yield point due to the rounded CaCO3.
Compared with Formulation B, SMA/CaCO3/CaCl2@SiO2 and PSA/Ca-MMT/ CaCl2@SiO2 had a significant effect on the rheological properties and filtration properties (Table 2). The fluid loss of PSA/Ca-MMT/CaCl2@SiO2 was less than SMA/CaCO3/CaCl2@SiO2 as a result of the network structure of CMC and more CaSiO3 (filling effect) generated from PSA/Ca-MMT/CaCl2@ SiO2, but the viscosity was also smaller than SMA/CaCO3/CaCl2@SiO2 since the latter had more Na2SiO3.
After the thermal aging tests (200 ºC), SMA/CaCO3/CaCl2@SiO2 and PSA/ Ca-MMT/CaCl2@SiO2 had considerable impact on the rheological properties and filtration properties. Fluid loss decreased noticeably because the inner graft polymer powder (occlusive filling effect and network effect of long chain of polymer), CaSiO3 (filling effect), and Na2SiO3 (film effect) worked together to reduce the fluid loss. The fluid loss of PSA/Ca-MMT/CaCl2@SiO2 was greater than SMA/CaCO3/CaCl2@SiO2 for the degradation of CMC. SMA/CaCO3/CaCl2@SiO2 had higher viscosity because there was residual Na2SiO3. It had a lower yield point due to the granulated CaCO3.
In conclusion, the rheological properties and filtration properties of SMA/CaCO3/CaCl2@SiO2 were superior in freshwater-based drilling fluid and CMC-based drilling fluid at 200 ºC. In addition, the viscosity and yield point of SMA/CaCO3/CaCl2@SiO2 in drilling fluid was better than PSA/Ca-MMT/ CaCl2@SiO2.
Figure 4 – Photos of SMA/CaCO3/CaCl2@SiO2 in drilling fluid before (a) and after (b) thermal aging tests (200 ºC).SMA/CaCO3/CaCl2@SiO2 in drilling fluid before and after thermal aging tests (200 ºC) are shown in Figure 4. Film from Na2SiO3 was clearly visible after thermal aging tests.
Table 1, Table 2, and Figure 4 show that the excellent rheological properties and filtration properties are related to inner graft polymer powder (occlusive filling effect and network effect of long chain of polymer), CaSiO3 (filling effect), and Na2SiO3 (film effect). These all worked together to reduce the fluid loss. The mechanism of action is shown in Figure 5.
Figure 5 – Diagram of mechanism for SMA/CaCO3/CaCl2@SiO2.Conclusion
SMA/CaCO3/CaCl2@SiO2 was synthesized. At 200 ºC, the filtration properties of SMA/CaCO3/CaCl2@SiO2 were outstanding in freshwater-based drilling fluid and CMC-based drilling fluid due to the occlusive filling effect and network effect of long chain of polymer of inner graft polymer powder, filling effect of CaSiO3, and film effect of Na2SiO3. The viscosity and yield point of SMA/CaCO3/CaCl2@SiO2 in drilling fluid were better than PSA/Ca-MMT/CaCl2@SiO2 because of more Na2SiO3 generated from SMA/ CaCO3/CaCl2@SiO2.
References
- Zheng, X.H.; Yang S.W. et al. Synthesis, characterization, and evaluation of a fluid loss agent for high-temperature drilling fluid. American Laboratory 2013, 45(10), 22–5.
- Prinos, J.; Tselios, C.H. et al. Properties of miscible blends of polyglutarimide with poly(styrene-co-maleic anhydride). Polym. 1997, 38, 5921–9.
- Lazzara, T.D.; Whitehead, M.A. et al. Linear nano-templates of styrene and maleic anhydride alternating copolymers. Eur. Polym. J. 2009, 45, 1883–90.
- Wang, M.T.; Zhu, X.G. et al. Surface pattern in thin poly (styrene–maleic anhydride) films. Polym. 1999, 40, 7387–96.
- Shen, W.; He, H.P. et al. Grafting of montmorillonite with different functional silanes via two different reaction systems. J. Colloid Interface Sci. 2007, 313, 268–73.
- Recommended Practice. Standard Procedure for Field Testing Drilling Fluids, 12th ed.; American Petroleum Institute: Washington, DC, 1988.
- He, W.; Liu, Z.X. et al. Analytical application of poly {methyl (3-(2-hydroxy-3,4-difluoro)phenyl) propyl siloxane} as a QCM coating for DMMP detection. Talanta 2008, 76, 698–702.
- Al-Sabagh, A.M.; Noor El-Din, M.R. et al. Styrene-maleic anhydride copolymer esters as flow improvers of waxy crude oil. J. Pet. Sci.Technol. 2009, 65, 139–46.
Xiuhua Zheng is with the Drilling Fluid Laboratory, School of Engineering and Technology, China University of Geosciences, Beijing, PR China. Shiwei Yang is with the Drilling Engineering Research Institute, Sinopec Xinan Oilfield Service Corp., No. 699, Jinshajiang West Road, Deyang, Sichuan Province, 618000, PR China; e-mail: [email protected]. Zhongli Lei is with the Key Laboratory of Applied Surface and Colloid Chemistry, School of Chemistry & Materials Science, Shaanxi Normal University, Xi’an, PR China.