In life science laboratories and biotech firms, safety and environmental issues can be presented by the gases and cryogens utilized in the processes and controls. From simple oxygen deficiency that needs monitoring and controlling to toxic or flammable gas issues requiring special containment and controls, use of proper equipment and facility designs can ensure a safe working environment.
This article will detail the origins of specific areas that pose challenges and the type of gas systems and equipment that need to be employed to ensure a safe atmosphere for the staff and the work environment. The information will be presented in two sections. The first deals with the use of cryogenic gases, nitrogen, carbon dioxide, argon, and oxygen, and the second section with hydrogen and certain toxic gases that may also be flammable. Though the use of gases in today’s life science laboratory should always be considered in compliance to all of the regulations and standards that apply, as a whole there are specific hazards and several specific standards that address the unique properties and hazards of each gas.
Use of cryogenic gases
The use of cryogenic liquid nitrogen for its cryogenic “cold temperature” properties (liquid nitrogen boils at atmospheric pressure at –196 °C) has until now been the main reason to use cryogenic liquids in life science labs. Its use in cryopreservation in which biological specimens are frozen with and stored at liquid nitrogen temperatures has grown dramatically in the past 20 years, to the extent that large repositories supplied with liquid from bulk tanks are placed outside of the building. However, in smaller laboratories there has been equal growth in the number and size of both the freezers that hold the liquid nitrogen and the liquid cylinders that supply it. It is not uncommon to find four or five freezers with 6–10 liquid nitrogen cylinders in an anteroom or hallway of a life science laboratory. In National Fire Protection Association Code 55, Compressed Gases and Cryogenic Fluids, the minimum required ventilation for specific volumes of gases and cryogens is spelled out, though eventually all of the liquid will convert to gaseous nitrogen in that space. Under normal circumstances, this occurs rather slowly at a rate of perhaps 2–3% of the liquid contents per day.
During transfer operations, however, that rate is dependent on how insulated and how well the supply side of the operation delivers the liquid in a stable state, as well as how and where the liquid that vaporizes during the transfer is vented. Typically referred to as “hot gas,” because it turns to gas in order to cool down the hoses, piping, and control valves, it can take as much as 25% of what is actually transferred just to cool everything down. When you consider that the liquid-to-gas expansion ratio for nitrogen is 696:1, the volume of resulting hot gas, combined with what is normally vented daily, can pose an oxygen deficiency concern, even with acceptable air exchange in the area or room.
If you consider that each liquid cylinder of 230-L volume contains 5000+ cubic feet of gas at standard temperature and pressure and a typical cryogenic freezer may contain an additional 3000–5000 cubic feet of gas, it is imperative for any area to have an effective oxygen-deficiency monitoring system. An example of how a typical freezer area may be supplied with liquid is shown in Figure 1, while a schematic of how to integrate an oxygen-deficiency monitor with a remote display and audible horn and strobe is shown in Figure 2. The device shown in Figure 2 is well suited for continuous monitoring oxygen levels in areas in which inert gases or confined space may produce a hazardous reduction in the oxygen content of the air.
Figure 1 – Typical cryogenic freezer setup.
Figure 2 – Oxygen detector monitoring installation.There are many technologies available to detect the level of oxygen. One with a long-lasting sensor that can accommodate temperature and barometric changes without false alarms would be ideal as there are some technologies that require frequent calibration or sensor replacement. The transmitter and sensor with local audible and visual alarm should be installed in a location where gas buildup or leaks are likely to occur or where released gases may accumulate. It should be mounted no closer than 12 in. above floor level. Airflow within the monitored area, the characteristics of the gas (lighter or heavier than air), and the position of workstations and personnel should all be considered in determining the most suitable installation.
At the entry to the area, a remote display and audible and visual alarm or strobe should be mounted to warn of any hazard before entry to the space is attempted. All it takes is a few breaths of an oxygen-deficient atmosphere for someone to lose consciousness. Though nitrogen is certainly the most prevalent cryogenic liquid in a life science laboratory, the use of carbon dioxide for cell culture incubators, argon for instrumentation and blanketing of reactions, as well as oxygen for bioreactors, these gases can also present an oxygen-deficiency risk, or, in the case of oxygen, the risk of an oxygen-enriched environment that may cause normally nonflammable materials to ignite. In the case of oxygen-use areas, a monitor to detect when the oxygen level exceeds 23.5%, when it is no longer considered an inert atmosphere, may be advisable. Approximate gas-to-liquid volumes for each of the above gases in liquid cylinders with their expansion ratio are detailed in Table 1.
Table 1 – Approximate gas-to-liquid volumes for gases in liquid cylinders with their expansion ratios
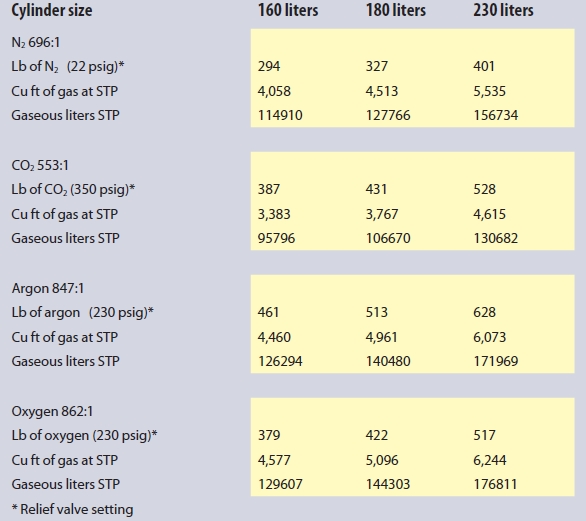
Use of hydrogen
The other hazard that should be addressed is the use and storage areas for flammable gases like hydrogen, as well as potentially toxic gases like hydrogen sulfide or carbon monoxide. In National Fire Protection Association Code NFPA 55, Compressed Gases and Cryogenic Fluids, specified Maximum Allowable Quantities (MAQ) are defined specifically for hydrogen and for toxic or highly toxic gases. For most toxic or highly toxic gases, it is readily understood that only limited quantities are allowed to be used in restricted control areas like fumehoods, and that anything more than a cubic foot or two requires a thorough engineered installation requiring gas cabinets, dedicated purging and exhaust system scrubbers, as well as hazardous gas leak detection and shut-down capabilities.
However, when it comes to smaller installations of hydrogen in which outside storage and control to line pressures of less than 150 psig are not available, it is not unusual to find greater than the MAQ for hydrogen in laboratories supplying hydrogen for instrumentation and/or chemical reactions like hydrogenation.
There are four main areas required by NFPA 55 for these types of installations: fire-resistance rating, ventilation, separation, and controls. Many laboratory staff and planners do not understand that, once there is more than a single cylinder of hydrogen on a system or designated area, the level of these requirements is such that you are limited to either constructing a dedicated hydrogen room or having the cylinders and their controls in a gas cabinet. In NFPA 55, the MAQ for a specific use or storage area would seem to allow a large amount of hydrogen to be used or stored.
However, within those MAQ, there are limits that, once crossed, require higher fire rating material, greater ventilation requirements, and strict implementation of separation distances. In general these requirements initiate when quantities exceed 250, 400, and 3500 cubic feet. Once the volume reaches 15,000 cubic feet, the area must be located in a detached building or outdoors.
1. Fire-resistance rating requirements set forth in NFPA 55:
a. Section 6.3.1.3.1 states that where flammable gases are stored or used in quantities in excess of 250 cubic feet, the area is to be separated from other occupancies by 1-hr rated construction.
b. Combustible material and hydrogen tanks must be separated by a 10-ft distance or a noncombustible wall that extends not less than 18 in. above and to the sides of the area used for combustible material.
c. Hydrogen tanks are to be separated from incompatible materials, e.g., oxygen, by a 20-ft distance or a noncombustible wall having a fire resistance rating of at least 0.5 hr that extends not less than 18 in. above and to the sides of the cylinders.
d. Areas in which a hydrogen system is located are to be permanently placarded as follows: WARNING: HYDROGEN—FLAMMABLE GAS—NO SMOKING—NO OPEN FLAMES.
2. Ventilation requirements set forth in NFPA 55:
Figure 3 – NFPA 55 compatible gas storage (separation).a. Section 6.16 states that indoor storage and use areas for compressed gases are to be provided with mechanical exhaust ventilation or natural ventilation, where natural ventilation can be shown to be acceptable for the materials used.
b. Section 6.16.1 states that where mechanical ventilation is provided, the system is to be operational during the time the building or space is occupied.
c. Section 6.16.3 states that the mechanical ventilation rate is to be at a rate of not less than 1 ft3/min/ft2 of floor area over the area of storage or use.
d. Section 6.16.4 states that systems are to operate continuously unless an alternate design is approved by the code official.
e. Any required mechanical ventilation, alarm, detection, or other electrically operated systems are required to be provided with an emergency or standby power system, unless an approved fail-safe engineered system is installed.
f. Section 6.16.7.1 states that the exhaust ventilation system design is to take into account the density of the potential gases released.
g. Section 6.16.7.3 states that for gases that are lighter than air, exhaust is to be taken from a point within 12 in. of the ceiling.
h. Section 6.16.9 states that exhaust ventilation is not to be recirculated within the room or building if the cylinders, containers, or tanks stored are capable of releasing hazardous gases.
i. Section 6.16.10 states that ventilation systems are to discharge a minimum of 50 ft from intakes of air-handling systems, air-conditioning equipment, and air compressors.
j. Section 6.16.11 states that use of compressed gases is to be located not less than 50 ft from air intakes.
3. Separation requirements set forth in NFPA 55:
Figure 4 – Single-cylinder installation.a. Section 7.1.6.2 states that flammable and oxidizing gases are to be separated by 20 ft.
b. Section 7.1.6.2.1 states that the 20-ft distance is permitted to be reduced without limit when separated by a barrier of noncombustible material at least 5 ft high that has a fire resistance rating of at least 0.5 hr.
c. Other separation distances are shown in Figure 3.
When you consider that the above requirements for installations of up to four hydrogen cylinders can be met by using appropriately rated gas cabinets with appropriate ventilation and gas controls, the prospect of what is installed is less daunting to the researcher or laboratory manager. An example of a single-cylinder installation is shown in Figure 4.
Larry Gallagher is Specialty Gas Products Manager, CONCOA, 1501 Harpers Rd., Virginia Beach, VA 23454, U.S.A.; tel.: 800-225-0473; fax: 757-422-3125; e-mail: [email protected]; www.concoa.com