In the 1980s, Sun Microsystems coined the trademark “The Network is the Computer” to herald the days of distributed computing. National Instruments (Austin, TX), purveyors of the popular LabVIEW™ instrumentation programming environment, built on the meme, trademarking “The Software is the Instrument” to signal the dawn of virtual instrumentation. Today, microscopy’s vanguard has charged beyond the realm of Abbe, Nachet, Janssen, and the other originators of the field.1 Automated image acquisition and reconstruction, clever optical strategies, intensive databasing and analysis, and resolutions below the Rayleigh criterion are the new frontiers,2 with early settlements emerging in the form of imaging suites crafted by pioneering technologists (Table 1). Increasingly, the imaging suite is the microscope.
Table 1 - The post-Rayleigh era of microscopy

Software, the driver
Thus commences the next phase of the laboratory’s personal computer revolution, first spotlighted in American Laboratory in annual purchasing surveys in the mid-1980s when the personal computer became the largest laboratory budget category for the first time. Today, imaging suites that control the microscope, camera, focusing mechanism, and sample positioning stages do not just serve the microscope—They define its capabilities and that of the application, and the suites are growing increasingly vertical in their focus. Examples include Metamorph and MetaFluor (Molecular Devices, Sunnyvale, CA), μManager (Vale Laboratory, University of California at San Francisco), ScanImage (HHMI Janelia Farm, Ashburn, VA), and SlideBook™ suite (Intelligent Imaging Innovations, Denver, CO), all of which support an impressive array of hardware from manufacturers committed to users’ quick productivity.
This has increased market awareness of software as not only an enabler for industrial and academic research, but also as a pacing item for instrumentation manufacturers. Generally speaking, microscopy users must prioritize quick productivity and ease of use; thus low-level connectivity of the instrumentation is of little utility outside of the most exotic hinterlands of the field, such as single-molecule biophysics, where each setup is still unique and researchers are developing the foundations of tomorrow’s platforms and writing their own code. Instead, the majority of today’s microscopy applications are increasingly well-served by imaging suites that offer plug-and-play support of popular subsystems, and microscope manufacturers and distributors offer configuration services (and sometimes their own proprietary platforms) that allow users to devote their attention to their real work. In this way, subsystems have taken on a role reminiscent of common office peripherals like printers and scanners: Users expect them to “just work” without a lot of low-level engineering on their part.
High hurdles for manufacturers and innovative responses
The challenge for subsystem manufacturers is how to support both this expanding mainstream of sophisticated applications suites, with their plug-and-play prerogative, and the engineers and scientists immersed in developing tomorrow’s techniques and writing their own code. At the same time, subsystem manufacturers must keep pace with the increasing importance of high-speed acquisition and processing. This has driven a cascade of developments that have included:
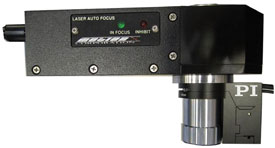
Figure 1 - Laser autofocus sensor with fast piezo focus positioner and objective (courtesy of PI [Physik Instruments] L.P. [San Jose, CA] and Motion X Corp. [Santa Barbara, CA]).
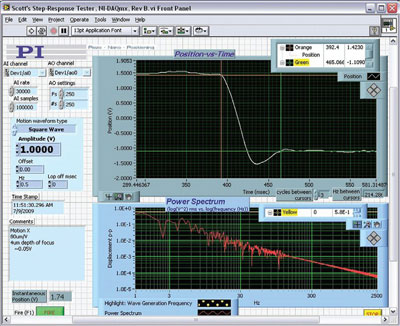
Figure 2 - Sixy-millisecond capture of focus demonstrated by laser vibrometer independently measuring PIFOC® piezo objective scanner (PI) position vs time.
- Advanced interface techniques that offer microsecond-scale synchronization between motion and optical processes
- Novel motion devices with extended travels, resolution capabilities and stabilities, new sensors, and command sets with backward and forward compatibility as new controls are developed
- Digital nanopositioning controllers of extraordinary capability but that undercut traditional analog controls in price due to semiconductor developments
- Innovative control techniques that address fundamental limitations in motion system bandwidths, for more accurate scanning and acquisition.
For example, the need for precise focusing mechanisms (either piezo objective positioners or piezo Z scanning stages) to instantly acquire focus and keep it locked in despite structural drifts and specimen motions has outstripped the capabilities of previous-generation probe-based sensors that could compensate for only some drift mechanisms. The industry has responded with both image- and sensor-based autofocus approaches that meet these emerging needs and that leverage sophisticated new interfacing capabilities. In particular, laser autofocus sensors coupled with fast nanopositioning controllers can now acquire and lock in perfect focus in milliseconds, even starting from many hundreds of microns out of focus (see Figures 1 and 2).
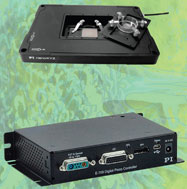
Figure 3 - The value trend enjoyed by consumers has now evolved to nanopositioning, with the introduction of cost-effective digital controllers for a fraction of their former price and which support popular imaging suites. XYZ piezo stage for super resolution (SR) microscopy is shown in the background.
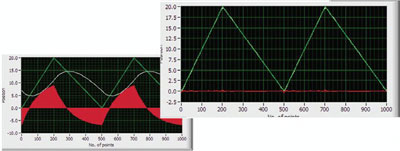
Figure 4 - Dynamic Digital Linearization (DDL) (PI) is an in-controller technology for eliminating following errors (red). Green: commanded, white: actual, red: following error. Left: without DDL; right: with DDL. The green and white traces are indistinguishable.
Similarly, the need for high applications throughput has also driven the demand for larger-area scanning capabilities for sample positioning stages. In turn, these new requirements for fast motions place a premium on coarse-positioning stage stiffness and stability. The industry’s response has been to develop new types of drives that eliminate the primary drift mechanism of common microscopy substages.3 Meanwhile, the skyrocketing functionality-to-cost ratio of modern microelectronics has seen the introduction of digital nanopositioning controllers at a fraction of the former cost of such instruments (see Figure 3).
Tomorrow’s imaging applications are growing, some leveraging optical tweezers and atomic force probes to image almost unimaginably small structures. These applications depend on the utmost in instrumentation performance and interfacing capabilities.4 Applications are just starting to take full advantage of advanced technologies such as the ability of some nanopositioning controllers to virtually eliminate the following error present in rapid actuation. This allows faster scanning without loss of localization accuracy (see Figure 4).
An exciting future
The mash-up of advanced optics, novel illumination and fluorescence techniques, new sensors, and advanced nanopositioning subsystems is just beginning to unfold. At the same time, the promise of automating sophisticated setups to leverage the speed, analytical power, and data handling prowess of today’s computers and software architectures is just beginning to be realized. It is safe to say that the microscopy of 2035 will bear as much resemblance to today’s microscopy as a personal computer bears to the first PCs that topped the American Laboratory budget surveys just 25 years ago.
References
- Parmentier, J. The History of the Microscope—An Introduction to Microscopy; www.microscopy-uk.org.uk/intro/histo.html.
- Geisler, C. Dissertation—Fluorescence nanoscopy in three dimensions; http://webdoc.sub.gwdg.de/diss/2010/geisler/geisler.pdf.
- Jordan, S.; Anthony, P. Design considerations for micro- and nanopositioning: leveraging the latest for biophysical application. Curr. Pharm. Biotechnol. 2009, 10, 515–21; www.bentham.org/cpb/sample/cpb10-5/0008G[1].pdf.
- Churnside, A.B.; King, G.M. et al. Improved performance of an ultrastable measurement platform using a field-programmable gate array for real-time deterministic control. In Instrumentation, Metrology, and Standards for Nanomanufacturing II; Postek, M.T.; Allgair, J.A., Eds. Proceedings of the SPIE, 2008, Vol. 7042, pp 704205-704205-7.
Mr. Jordan is Director, NanoAutomation™ Technologies, PI (Physik Instrumente) L.P., 6537 Fall River Dr., San Jose, CA 95120, U.S.A.; tel.: 949-679-9191; fax: 949-679-9292; e-mail: [email protected].