Polymers and inorganic additives have been widely used in high-temperature water-based drilling fluids to transport rock cuttings, maintain well stability, control rheological properties, and minimize fluid loss. However, inorganic additives are lower in cost and offer superior temperature resistance, but their properties are generally not ideal. Organic polymer additives have outstanding properties, but their temperature resistance is as optimal as might be expected.
Hybrid materials have broad applicability; for example, they are used as drug delivery carriers, efficient catalysts, and photonic crystals. However, they are rarely employed in high-temperature drilling fluid. Research on inorganic/organic hybrid high-temperature resistance fluid loss agent, which has the outstanding properties of organic and inorganic materials, is therefore valuable.
The molecular structure of PSA (copolymer of styrene and acrylic acid) can be modified easily due to the presence of carboxyl groups; this commercial polymer has diverse applications.1,2 Silane coupling agent (KH550) can form a durable bond between organic and inorganic materials because it contains two types of reactivity in the same molecule.3 Silicon dioxide and calcium bentonite (Ca-MMT) are highly temperature-resistant materials. CaSiO3 can be generated via the reaction between Na2SiO3 and calcium ion.
Based on the above, a novel inorganic/organic hybrid, highly temperature-resistant fluid loss agent—PSA/Ca-MMT/CaCl2@SiO2 (named YSW-2)—consisting of PSA, silane coupling agent, silicon dioxide, calcium chloride, and Ca-MMT was synthesized, characterized, and evaluated.
Experimental
Synthesis and characterization of YSW-2
PSA was prepared by precipitation polymerization. 4 Ca-MMT was modified by silane coupling agent KH550.5 Graft polymer (containing CaCl2) of modified Ca-MMT and PSA was prepared as follows: 1) 1 g PSA was dissolved in 200 mL ethanol/toluene (70/30 by volume) solution with a magnetic stirrer at 95 °C. 2) One hour later, 2.5 g modified Ca-MMT powder was added to the mixture. Meanwhile, 0.2 g CaCl2 was dissolved in 10 mL ethanol solution (small beaker) and stirred magnetically for 0.5 hr. 3) Three hours later, CaCl2 solution was added to the flask. 4) Three hours after that, the products were synthesized. 5) The solvent was then removed and placed in a rotary evaporator for 1 hr at 90 ºC, and the products were dried at 60 ºC for 24 hr under vacuum.
Encapsulation of graft polymer (containing CaCl2) with silicon dioxide was done via the sol–gel method,6 and the final product, YSW-2, was attained. Ca-MMT, modified Ca-MMT, graft copolymer of modified Ca-MMT, and YSW-2 were characterized by FTIR spectra, X-ray diffraction (XRD), thermogravimetric analysis (TGA), and transmission electron microscopy (TEM).
Evaluation of YSW-2
Drilling fluid property tests were performed according to the specifications of the American Petroleum Institute.7 Regular drilling fluid (formulation A) was made up using bentonite, sodium hydroxide (to obtain sufficient alkaline conditions), and H2O (3:0.75:100 ratio by weight) and was then prehydrated for 24 hr. Polymer drilling fluid (formulation B) was prepared by adding 0.15% by weight carboxymethylated cellulose (CMC) to formulation A and was prehydrated for 24 hr. One percent by weight sulfomethal phenolaldehy resin (SMP), calcium bentonite, and YSW-2 were added to formulation A to test the drilling fluid properties. One percent by weight YSW-2 was added to formulation B to test the drilling fluid properties. Thermal aging tests were carried out in a roller oven for 16 hr.8
The rheological properties, i.e., apparent viscosity (AV), plastic viscosity (PV), and yield point (YP), were determined by viscosity measurements at 600 and 300 rpm with a ZNN-D6 type rotating viscometer (Qingdao Haitongda Dedicated Instrument Plant, China). AV is the total viscosity of drilling fluid in the flow process, PV is related to the solids content of the drilling fluid, and YP reflects the formation of drilling fluid network structure. Filtration loss (FL) tests were carried out by a ZNS medium-pressure filtration apparatus (Qingdao Haitongda).
Results and discussion
The FTIR spectra of the process product and YSW-2 are shown in Figure 1. The absorption band at 2933 cm−1 in Figure 1b can be attributed to –CH2 of the modified Ca-MMT, suggesting that Ca-MMT was modified by KH550. The transmission band at 3028 cm−1 in Figure 1c was assigned to –CH3, and the absorption band of –CH2 was enhanced.
Figure 1 – FTIR spectra: a) Ca-MMT, b) modified Ca-MMT, c) graft copolymer of modified Ca-MMT and PSA, and d) YSW-2.The bands centered at 623 cm–1, 1453 cm–1, and 1495 cm–1 in Figure 1c are stretching vibration peaks of polystyrene within PSA.9 The peak at 1367 cm−1 in Figure 1c resulted from the amido bond. All of these indicate that hybrid graft polymers of modified Ca-MMT and PSA were synthesized. The strong band at 1107 cm–1 in Figure 1d is associated with the Si–O–Si asymmetric vibration peak from the SiO2. Moreover, other peak intensities became weak, which demonstrates that encapsulating graft polymer with silicon dioxide was successful.
The TGA curves of graft polymer and YSW-2 are shown in Figure 2. It can be seen in the curves in Figure 2a and b that the weight loss before 400 ºC was caused by volatilization of free water. The stage at 400–450 ºC was due to the loss of PSA; at 450–750 ºC it can be attributed to the decomposition of KH550. After 750 ºC, the remaining materials were Ca-MMT (ash content: 69.73%) and Ca-MMT/SiO2 (ash content: 80.34%), respectively, suggesting that the weight percent of silicon dioxide was 10.91%.
Figure 2 – TGA: graft copolymer of a) modified Ca-MMT and PSA, and b) YSW-2.The XRD patterns of the process product and YSW-2 are shown in Figure 3. The crystal form of modified Ca-MMT and graft polymer changed minimally compared to Ca-MMT in Figure 3(1a), (1b), and (1c). The peak intensities of graft polymer weakened and the diffraction peaks at 19–25° (2θ) of YSW-2 corresponded to SiO2 from Figure 3(1d) and (2), indicating that graft polymers were encapsulated with silicon dioxide.
Figure 3 – XRD patterns: 1a) Ca-MMT, 1b) modified Ca-MMT, 1c) graft copolymer of modified Ca-MMT and PSA, and 1d) YSW-2. 2) 10–30° (2θ) of YSW-2.
Figure 4 – TEM photographs: graft copolymer of a) modified Ca-MMT and PSA, and b) YSW-2.The TEM photographs of graft polymer and YSW-2 are shown in Figure 4. SiO2 had a strong influence on the morphology of graft polymer since it was deposited on graft polymer particle by particle relatively homogeneously.
Tables 1 and 2 list the effect of YSW-1 on the rheological and filtration properties in freshwater-based and CMC-polymer drilling fluid before and after aging tests. As shown in Table 1, the influence of Ca-MMT (raw material of YSW-2), SMP (conventional fluid loss agent for 180−200 °C), and YSW-2 on the rheological properties was minor, but the effect on filtration properties was significant at room temperature, in contrast to formulation A. The filtration loss of YSW-2 was approximately the same with Ca-MMT and SMP.
Table 1 – Drilling fluid properties of calcium Ca-MMT, SMP, and YSW-2 in formulation A before and after thermal aging tests (100 oC)*
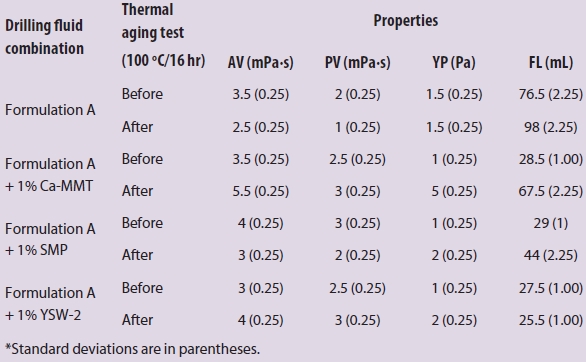
Table 2 – Drilling fluid properties of YSW-2 in formulation B before and after thermal aging tests (200 ºC)*
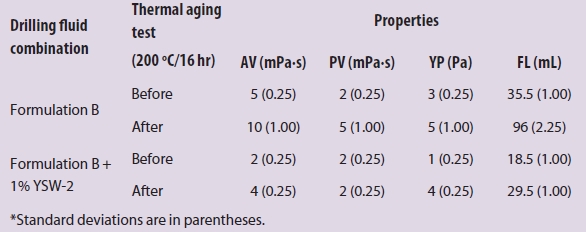
After the thermal aging tests (200 ºC), the effect of Ca-MMT on the AV, PV, and YP was greater than YSW-2 and SMP, but the fluid loss was larger than YSW-2 and SMP. The filtration properties of YSW-2 were best at 200 ºC. In conclusion, the rheological properties and filtration properties of YSW-2 were outstanding in freshwater-based drilling fluid at 200 ºC.
Compared with formulation B, YSW-2 had a significant effect on the rheological properties and filtration properties (Table 2), especially after the thermal aging tests (200 ºC). AV, PV, YP, and FL decreased noticeably. In conclusion, the filtration properties of YSW-2 were excellent and the viscosity decreased in CMC-based drilling fluid at 200 ºC.
From Tables 1 and 2 it can be concluded that Na2SiO3 is produced by the chemical reaction of the outer layer SiO2 of YSW-2 in aqueous alkaline solution, which was more intense with the increase in temperature. CaSiO3 was generated via the reaction between Na2SiO3 and inner calcium ion after SiO2 decreased to a certain extent. CaSiO3, graft polymer powder (filling effect), and CMC (network structure) then worked together to reduce the fluid loss.
The rheological properties and filtration properties of YSW-2 were superior in freshwater-based drilling fluid and CMC-based drilling fluid at 200 ºC. In addition, the viscosity of YSW-2 decreased at high temperature in CMC-based drilling fluid, and YSW-2 was an alkali-activated fluid loss agent.
Conclusion
The synthesis of a novel alkali-activated inorganic/organic hybrid high-temperature resistance fluid loss agent, PSA/Ca-MMT/CaCl2@ SiO2, was described. The decomposition temperature of YSW-2 was 400 ºC. At 200 ºC, the filtration properties of YSW-2 were exceptional in freshwater-based drilling fluid and CMCbased drilling fluid. Furthermore, the viscosity decreased in CMC-based drilling fluid.
References
- Zhang, B.; Cui, Y.L. et al. Cadmium iondoped magnetic poly (styrene-acrylic acid) nanospheres for sensitive electrochemical immunoassay. Biosens. Bioelectron. 2012, 35, 461–5.
- Marques da Silva, P.M.; Franco, C.V. et al. Synthesis, characterization and antibacterial activity studies of poly-{styrene-acrylic acid} with silver nanoparticles. Mater. Sci. Eng., C 2009, 29, 647–50.
- He, H.W.; Zhang, Z. et al. Compressive properties of nano-calcium carbonate/epoxy and its fibre composites. Composites Part B 2013, 45, 919–24.
- Silva, L; Silva, F.E. et al. Humidity and pH sensor based on sulfonated poly-{styrene– acrylic acid} polymer. Synthesis and characterization. Mater. Sci. Eng., C 2009, 29, 599–601.
- Shen, W.; He, H.P. et al. Grafting of montmorillonite with different functional silanes via two different reaction systems. J. Colloid Interface Sci. 2007, 313, 268–73.
- Deng, H.J.; Lei, Z.L. Preparation and characterization of hollow Fe3O4/SiO2@PEG-PLA nanoparticles for drug delivery. Composites: Part B 2013, 54, 194–9.
- Recommended Practice. Standard Procedure for Field Testing Drilling Fluids, 12th ed.; American Petroleum Institute: Washington, DC, 1988.
- Yan, L.L.; Wang, C.B. et al. Preparation of a novel amphiphilic comb-like terpolymer as viscosifying additive in low-solid drilling fluid. Mater. Lett. 2013, 1–4.
- Jiang, Z.Q.; Jiang, Z.J. et al. Preparation and characteristics of acrylic acid/styrene composite plasma polymerized membranes. Appl. Surf. Sci. 2010, 256, 6473–9.
Xiuhua Zheng and Shiwei Yang are with the Drilling Fluid Laboratory, School of Engineering and Technology, China University of Geosciences, Beijing 100083, PR China; tel.: +86 10 82321976; fax: +86 10 82322624; e-mail: [email protected]. Zhongli Lei is with the Key Laboratory of Applied Surface and Colloid Chemistry, School of Chemistry & Materials Science, Shaanxi Normal University, Xi’an, PR China.