In process manufacturing, a laboratory information management system (LIMS) implementation will deliver exceptional value if it eliminates redundant data transcriptions within the laboratory, processes data into information that is useful for the plant, and effectively communicates with the other critical systems throughout the enterprise. This article details how the specialty products plant of Ergon Refining Inc. (Vicksburg, MS) is recognizing this value from its implementation of the LABWORKS™ LIMS (PerkinElmer Life and Analytical Sciences [LAS], Inc., Shelton, CT).
Ergon Refining’s LIMS automates many formerly manual operations, including sample log-in, calculations, work flow approval, and report generation. Integration with both simulated distillation and plant operation systems eliminates manual data entry and associated errors. Report generation is fully automated and management has the ability to drill down and query for any information throughout the plant. The company is able to handle 20% more information with the same staff while substantially increasing the accuracy of its data.
The LABWORKS system was selected because of its proven ability to work in a refining environment, its versatile interfacing capabilities, and its track record for fast implementations.

Figure 1 - Refinery exterior.
At the company’s Vicksburg refinery (see Figure 1), select wax-free naphthenic crude oils are processed to produce distinctive specialty petroleum and asphalt products for niche markets worldwide. The refinery produces a wide variety of nonfuel, engineered products. They include naphthenic process oils, electrical insulating oils, naphthenic base oils, liquid asphalt cement, polymer-modified asphalt cement, and asphalt emulsions. Special processing technology, developed exclusively by the company in the Vicksburg hydroprocessing pilot plant, allows safe, efficient, clean refining of high-acid, high-sulfur crude oils that many competitors would not be able to process. Since its original start-up in 1978, the refinery has been expanded and modernized several times to attain its current configuration. The hydroprocessing unit, where the naphthenic base oils are produced, is the largest single-train naphthenic base oil processing unit in the world. Vicksburg was one of the first refineries in the U.S. to hold a full ISO 9000 certification for the entire operation. The refinery is now recertified to the new ISO 9001:2000 standard.
Past use of multiple systems
In the past, the information systems department developed separate systems to meet the needs of the individual units within the refinery. This approach was problematic because the department had to maintain each of these programs. As the systems’ architects and the authors who wrote them left the company, program maintenance became increasingly difficult. Also problematic was the plant’s requirement that reports cross unit boundaries to track overall refinery operations. This particular report was all but impossible to produce.
There was little opportunity for automation since it was difficult to justify the required custom programming for an application that only touched a single unit. It was also impractical to interface just a partial software package, which would require writing six custom interfaces: one for each of the unit systems. In addition, the custom programs did not provide an auditing mechanism and lacked many of the error-checking and security features offered by modern packaged software.
The LIMS selection process was originally performed by a sister refinery located in West Virginia. The sister refinery formed a selection committee that evaluated the leading LIMS applications. LABWORKS was chosen because its high level of configurability enables it to meet the complete requirements of large refineries without any expensive customization or consultants’ services. Without sacrificing capabilities, the implementation process is shorter and less expensive than with many other leading LIMS applications. LABWORKS also offers the ability to interface with many software packages used in refineries, including Plant Information (OSIsoft, San Leandro, CA) and Simulated Distillation (Sim-Dis, Envantage, Inc., Cleveland, OH). Ergon’s decision to purchase a LIMS came after a sister company had completed its selection process. The decision criteria were reviewed and it was discovered that the LABWORKS system met Ergon’s requirements as well as it met the other company’s, in addition to the benefits of using a common LIMS.
Simplified configurability
The configurability of the LIMS, and its ability to handle refinery operations without writing custom code, made it possible for the Ergon information systems department to implement the code themselves with minimal outside assistance. PerkinElmer was on-site for a few days to perform the initial installation and help the department map out the development process. The process began with the unit stream, moving downstream through the plant. Then the finished product side, the tanks, shipments, and certificates of analysis were addressed. Throughout the process, PerkinElmer served as a facilitating resource and was available to answer questions or provide additional help. There were financial benefits to the company being able to perform the implementation. Even more important, however, was that, because the company knows its own business processes much better than a consultant ever could, they were able to identify many opportunities to improve business processes during the implementation.
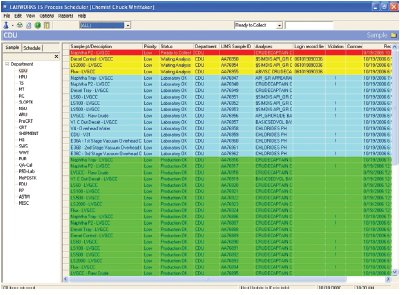
Figure 2 - Process Scheduler provides a comprehensive and current view to the end user in real time data. Critical decisions are expedited based on current data.
Ergon configured the software to streamline many laboratory operations. They set up the Process Scheduler to automatically log in all of the samples taken on a regular basis (see Figure 2). The only information that requires entry is the time and date the sample is taken. In the future, the refinery plans to install a bar-code system that will eliminate the need for even these two entries. The refinery uses a GC system to automatically generate the analysis and transfer the results into the LIMS. The LABWORKS calculation utility is used to automate calculations required as part of analysis. This utility integrates Excel (Microsoft, Redmond, WA) to perform the actual calculations. Any Excel calculation can be performed, simplifying the configuration process. The LABWORKS Review/Approval function is also configured to handle any needed approval steps.
Time-saving interfaces

Figure 3 - LABWORKS configurability empowers the user to easily provide solutions, such as automating the addition of typical data or certified data for a shipment sample.
Substantial time and accuracy improvements come from the ability of LABWORKS to interface with other key programs. Ergon uses SimDis to optimize product yields and operating margins by offering cut point control, stream process ability, and process mass balance. The LABWORKS interface accepts information such as the temperatures at which components come off the distillation stream. The advantage is that the technician does not have to type in all of those numbers. Equally important, the LIMS provides a permanent record of this important process information. Later, when the results are reviewed, the technician can check back into the application to, for example, analyze why a problem occurred. This helps in making adjustments that will improve yields and margins in the future. The interface also converts SimDis results into D86 format, a standardized distillation method. Another LABWORKS interface is used to communicate with the PI real-time performance management platform. LABWORKS has provided an additional interface to pass tank certification and shipment data to an existing blending system (see Figures 3 and 4).
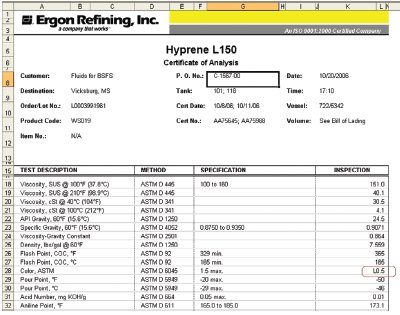
Figure 4 - LABWORKS COA program provides a real life solution when combining storage tank data with key parameter data on shipment samples by using multiple to produce the COA.
Ergon has developed many reports to automatically generate information that was previously much more difficult to obtain. One of the most important reports ties together the product test results to the shipment. Most of the testing is done while the products are stored in tanks awaiting shipment. Some basic tests are performed after the product is pumped into a container for shipment. The tank tests serve as reference when more detailed information is required. In the past, it was necessary to search through tank results, which took a considerable amount of time. With the new system, when the shipment tests are performed, the shipment is linked to the most recent tank certification. The use of Excel calculations simplifies the customization of tank results to the particular method used in the refinery. For example, analysts enter the color of the sample based on defined ranges. When the value is passed into an Excel template for a certificate of analysis, the logic within the spreadsheet automatically converts the number to the appropriate ASTM standard. Reports are generated every 12 hr, and operations personnel can access all of the information in the system at any point through the LABWORKS interface.
Conclusion
The implementation of the new LIMS provides substantial improvements at the refinery. Significant time savings are being realized at every stage of the quality control process. Samples are logged in automatically and only minimal data need to be entered after the sample is collected. Data entry is much faster than with the prior systems because spreadsheets have been set up that match the way the data come off the instruments. For example, multiple samples can be entered in adjacent rows of a spreadsheet rather than having to call up separate records for each entry. This has been a key factor in the refinery’s ability to handle a 20% increase in samples to approx. 40,000 per year without having to add any staff members. At the same time, the reduction in the amount of data entry and the automation of calculations has substantially improved the accuracy of the data.
Mr. Hudson is Director for Enterprise Software Solutions, PerkinElmer Life and Analytical Sciences, Inc., 160 Morris Ave., Mountain Lakes, NJ 07046, U.S.A.; tel.: 973-402-8822; e-mail: [email protected].