A company long associated with research and development and growth through constant evolution, General Electric (GE) opened its first industrial R&D laboratory in the United States in 1900, a small facility in the backyard barn of scientist Charles Steinmetz. Those humble beginnings could not in any way hint at the company’s current collection of world-class research facilities, notably its Global Research Center (GRC), a multidisciplinary technology center spread over 525 acres in upstate New York (Niskayuna, NY). With more than 1900 employees at the site, including chemists, physicists, biotechnicians, electrical and electronics engineers, microbiologists, metallurgists, and information technologists, it is critical that its facilities run smoothly and efficiently. Because of this, General Electric turned to Strobic Air Corp. (Harleysville, PA) for its Tri-Stack™ laboratory fumehood exhaust systems as part of a total $100 million renovation to the Niskayuna campus, including a new building wing for state-of-the-art wet chemical laboratories and to house GE’s emerging bioscience and nanotechnology research efforts (see Figure 1).
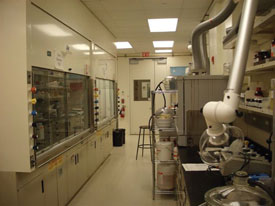
Figure 1 - Laboratory interior.
The GRC (www.ge.com/research) is one of the world’s largest industrial research facilities, providing technology for all of the company’s diversified businesses. In addition to the Niskayuna campus, GRC operates facilities in Bangalore, Shanghai, and Munich, as its organization of nearly 1000 Ph.D.-level researchers strive for breakthrough innovations in a wide range of areas, including energy, molecular imaging, nanotechnology, propulsion, and security technologies. Researchers throughout GRC practice the mantra, “What we can imagine, we can make happen.”
As part of the major renovations at Niskayuna, GRC looked for improved efficiency from its laboratory fumehood exhaust systems. Affiliated Engineers, Inc. (Madison, WI), which had previously worked with GE on such construction projects, was brought in by GRC’s management to outfit the new chemistry research facility. While GE had no prior experience with the use of mixed-flow-impeller technology for exhausting its laboratory workstation fumehoods, Affiliated Engineers staff had used such systems on other projects and was therefore well-positioned to meet the demanding laboratory exhaust requirements of the new facility.
GE staff involved with the new construction project had some experience with centrifugal fans in other facilities on the large campus, and were aware of the importance of maintaining adequate exhaust pressure to eliminate reentrainment of exhaust fumes back into the laboratories and into surrounding buildings. The company understood the importance of selecting an exhaust system with enough built-in redundancy to ensure reliability under all conditions. Affiliated Engineers was familiar with the issues involved with exhausting laboratory workstations, in particular for applications sensitive to acoustical noise and vibration, such as in chemical and nanotechnology research.
The chemistry research facility was constructed in the center of the campus, surrounded by older buildings with rooftop exhaust systems. Most of the buildings within the GRC campus were constructed during the 1960s and ’70s, and were equipped with rooftop exhaust systems. Many of these systems employ single-hood, single-fan construction, with the single fan in each case mounted indoors, within a rooftop penthouse. Fairly recently (about 5–6 years ago), the facilities management at GRC decided against indoor fans, even within penthouses, since they wanted to eliminate the indoor, positive-pressure ductwork accompanying these fans. Thus, the laboratory exhaust fans were moved to the roof of each facility; the single-hood, single-fan systems remained, but the fan style was changed to eliminate the need for guy wires on the roof (which were cumbersome, unsafe, expensive, and would eventually weaken the roof structure). As a result, the older GRC laboratory buildings are equipped with a dedicated exhaust stack for every laboratory workstation. Each stack discharges exhaust by means of a single in-line fan.
The single-hood, single-fan exhaust approach was maintained for one of the first of the new buildings constructed during the GRC renovation. For this building, called the C-Wing, the single-hood, single-fan approach was used because the International Mechanical Code (IMC) at that time did not allow for manifolds with the exhaust systems. Midway through the construction project, however, a supplement to the applicable IMC was published that allowed manifolded exhaust systems for the laboratories. Therefore, manifolded exhaust systems with vertically mounted in-line centrifugal fans were used. The advantages of direct-drive laboratory exhaust systems were explained to GRC staff, and these included a seven-year warranty on the drive motors of the Tri-Stack systems.
The laboratory exhaust systems employ low-maintenance, direct-drive fans (with bearing lifetimes, typically 100,000 hr) in contrast to exhaust systems based on belt-driven centrifugal fans, with parts that can wear out and that are often associated with tall exhaust stacks. These direct-drive exhaust systems use mixed-flow-impeller technology, by which contaminated exhaust air is diluted with as much as 170% outside ambient air via a bypass mixing plenum and bypass dampers. The direct-drive fan motors in these systems feature lower noise and vibration levels than centrifugal exhaust systems, with greater operating efficiency than centrifugal fan systems. The mixed-flow-impeller systems employ a unique exhaust nozzle design to increase stack outlet velocities to increase exhaust plume height to drive exhaust flow beyond the building boundary layer and eliminate reentrainment to the building and surrounding facilities.
In addition to their many performance benefits, mixed-flow-impeller direct-drive exhaust systems enable effective stack heights that yield more aesthetically pleasing rooflines than systems based on belt-driven centrifugal fans with their greater stack heights. For the GRC chemistry research facility, a number of different capacity exhaust fans—a total of 10 fans—were mounted on a single exhaust plenum manufactured from acoustical panels and basically built up like an air-handling unit.
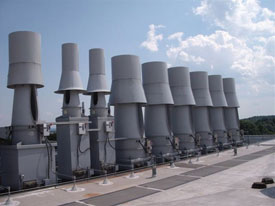
Figure 2 - Low profile of Tri-Stack laboratory exhaust systems presents an unassuming roofline.
In spite of the use of different fan types, for the laboratories within the new chemistry research facility, use of the custom plenum allowed each exhaust system and its stack extension to be mounted with the same height, forming an aesthetically pleasing line of sight for the building. The wind band extensions for the exhaust systems were extended as required to create a uniform roofline profile for the building (see Figure 2).
The mixed-flow-impeller laboratory exhaust systems provide effective and reliable exhaust functions for the new chemistry building without adding noise or creating vibration at the facility’s sensitive research laboratories. The mixed-flow-impeller technology powered by direct-drive fans allows the cutting-edge research to proceed at GRC while maintaining a low profile both inside and outside the building.
Mr. Tetley is Executive Vice President, Met-Pro Corp., 160 Cassell Rd., P.O. Box 144, Harleysville, PA 19438, U.S.A.; tel.: 215-723-4700; fax: 215-723-6758; e-mail: [email protected].