Mercury analysis, according to U.S. EPA Method 1631E,1 focuses on the monitoring of waste effluents at the lowest U.S. EPA Water Quality Certification (WQC) levels. Method 1631E has a prescribed analytical range of 0.5 ng/L Hg to 100 ng/L Hg. Determination of mercury in waste effluents to levels as low as 0.5 ng/L is not a simple task. In practice, every stage of analysis, including sample collection and transport, requires significant scrutiny in order to achieve successful mercury measurement by this method. With this in mind, specific instructions and recommendations for each of these stages are included in U.S. EPA Methods 1631E and 16692 in an effort to eliminate sample contamination and improve the quality of results obtained.
For the purposes of this article, the author underscores the analytical techniques involved in U.S. EPA Method 1631E. In summary, samples are first oxidized using bromine monochloride (BrCl) in order to liberate and transform the mercury present into its inorganic (Hg2+), water-soluble form. Once the samples are completely oxidized, they are then treated with hydroxylamine hydrochloride (HONH3Cl), a mild reducing agent, to destroy free halogens. Then the samples are further reduced with stannous chloride (SnCl2), which transforms the mercury into its elemental (Hg0) and volatile state that can be easily removed from solution. The elemental mercury is collected onto a gold trap to isolate and concentrate the mercury. Subsequently, the gold trap is thermally desorbed to liberate the elemental mercury and the mercury is transferred through an optical cell for detection via atomic fluorescence spectroscopy (AFS).
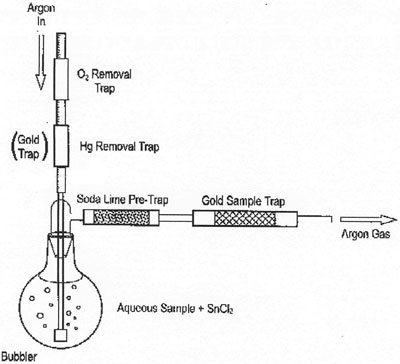
Figure 1 - Schematic of bubbler system (detector not included).
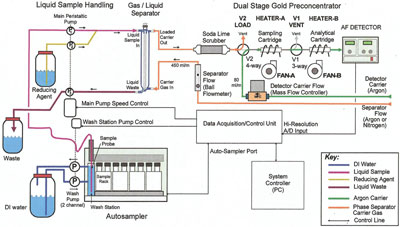
Figure 2 - Flow diagram of flow injection system.
U.S. EPA Method 1631E specifically notes two types of system for the determination of mercury: bubbler systems (Figure 1) and flow injection systems (Figure 2). Bubbler systems use direct purge of the reacted sample to liberate the elemental mercury into the carrier gas stream, in contrast to flow injection systems, which react the sample in a continuously flowing stream of reagents and then use liquid–gas phase separation devices to liberate the elemental mercury.
As detailed in U.S. EPA Method 1631E, bubbler systems are manual, single-sample configurations, while flow injection systems are automated with multiple sample capacity. The use of flow injection techniques is a common automation technique for a variety of analytes, and, while this technique offers some advantages, when an analytical method requires liquid–gas phase separation, there is no more efficient technique than the direct purge of the sample as performed with a bubbler system.
An automated bubbler system, the model RA-3000F Gold+ Mercury Analyzer (Nippon Instruments Corp., College Station, TX), was developed in an effort to simplify operation and improve performance in mercury analysis by U.S. EPA Method 1631E. The system maintains the simplicity and efficiency of the direct purge technique while providing the automation and multisample capacity of a flow injection system.
Procedure
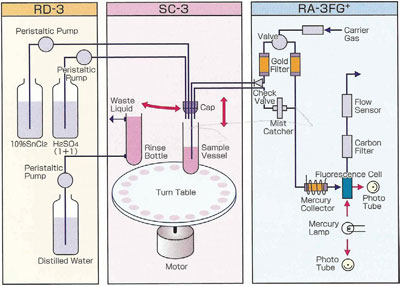
Figure 3 - Flow diagram of RA-3000F Gold+ automated bubbler system.
The RA-3000F Gold+ follows U.S. EPA Method 1631E very closely in operation and fully complies with the techniques and performance as prescribed in the method. The analyzer facilitates direct injection of reagents into the sample via an automated reagents addition module. This module is able to precisely introduce a known volume of reagent into each sample tube. After the reagent is introduced, the system seals the sample tube from above and then directly purges the mercury out of the solution, where it is collected onto a gold trap. Once the mercury is fully transferred onto the gold trap, it is thermally desorbed through an optical cell for determination by atomic fluorescence spectroscopy (see Figure 3).
After the analysis is completed on each sample, the cap and probe are washed in a rinse station prior to analysis of the next sample. This process is repeated automatically for all samples that have been queued in the sequence table of the software.
Results
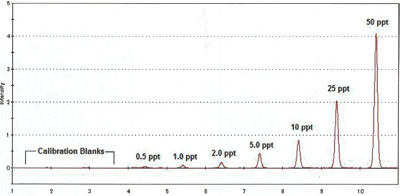
Figure 4 - Calibration peaks from blank to 50 ppt Hg.
Table 1 - QC report from data collected on RA-3000F Gold+
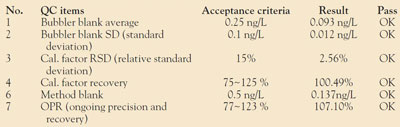
The RA-3000F Gold+ automated bubbler system employs a very simple approach. Due to the greater efficiency of the direct purge versus flow injection liquid–gas phase separators, the analyzer requires only 5 mL of sample per analysis. With the reduced sample volume and the computer-controlled reagent injection, approximately 80% reduction of reagents and waste, versus flow injection systems, is achieved without any sacrifice in performance.
The RA-3000F Gold+ is capable of fully complying with the stringent quality control mandated by U.S. EPA Method 1631E. Figure 4 shows the peak responses for a typical calibration curve.
The Quality Control Report for the analyzer’s software includes all of the QC samples required by Method 1631E. Table 1 shows a QC report from data that were collected on the RA-3000F Gold+. All QC samples were well within the required acceptance criteria.
Conclusion
The model RA-3000F Gold+ provides many advantages for simplifying the determination of mercury in wastewaters according to U.S. EPA Method 1631E. The analyzer significantly reduces reagents and wastes produced, and provides full compliance with Method 1631E. Other key features in the automated bubbler system include the use of mass flow control for optimal carrier flow stability, gold filters placed in-line to eliminate potential mercury contamination from the carrier flow path, 1631E software functions with automatic QC acceptance control, and the ability to automatically add the hydroxylamine hydrochloride to each sample.
In summary, the use of an automated bubbler system offers multiple advantages over flow injection systems for mercury analysis by U.S. EPA Method 1631E. The model RA-3000F Gold+ Mercury Analyzer offers simple operation, decreased sample volume, reduced reagents/wastes, and improved performance, making it a simple, environmentally friendly option for mercury analysis by U.S. EPA Method 1631E.
References
- Method 1631E, Mercury in Water by Oxidation, Purge and Trap, and Cold Vapor Atomic Fluorescence Spectrometry; U.S. Environmental Protection Agency, Office of Water, Office of Science and Technology, Engineering and Analysis Division (4303), Washington, DC; Aug 2002.
- Method 1669, Method for Sampling Ambient Water for Determination of Metals at U.S. EPA Ambient Criteria Levels; U.S. Environmental Protection Agency, Office of Water, Office of Science and Technology, Engineering and Analysis Division (4303), Washington, DC; Apr 1995 with Jan 1996 revisions.
Mr. Gray is Product Manager, Nippon Instruments North America, 1511 Texas Ave. S. #270, College Station, TX 77840, U.S.A.; tel.: 877-247-7241; fax: 979-774-3807; e-mail: [email protected]. The author thanks the following groups for their input, commentary, and evaluations: Test America (North Canton, OH, U.S.A.), U.S. EPA Region IV (Athens, GA, U.S.A.), and Florida DEP (Tallahassee, FL, U.S.A.).