Liquid handling as a whole, regardless of throughput, demands precision and accuracy to minimize experimental variation and produce reliable experimental data. In addition, when dealing with small volumes, accuracy becomes more difficult to achieve. If minute volumes are retained on the dispensing tip, or are not fully aspirated, then this will significantly impact the downstream data. Since the magnitude of error is directly proportional to the volume pipetted, a small inaccuracy can have a large impact. In addition, an increasing number of laboratories are moving toward automation to maximize experimental throughput for a more efficient and cost-effective process. However, the user needs to have a degree of assurance that the experimental data obtained are still as accurate and precise as possible. Modifying several minor parameters within the automated liquid handling procedure can result in vastly improved performance and more accurate experimental results.
In general, the performance of the automation platform, as well as the inherent experimental variables, will govern the success of the liquid handling protocol. Since these variables will differ between protocols, they are especially difficult to predict and control. However, the efficiency of an automated platform can be evaluated by users prior to purchase in order to assure them that highly accurate downstream data will be obtained. This article explores the various parameters that can be modified on an automated liquid handling instrument to help the user achieve optimal liquid handling results.
Dispense mechanisms
Although the optimization of operational parameters is an extremely important process, the type of dispensing mechanism used also plays a pivotal role. There are two different pipetting mechanisms that are generally used on automated liquid handling platforms: positive displacement (syringe based) and air displacement (tip based). The compatibility of these liquid handling mechanisms varies with different experimental requirements. As such, positive displacement pipetting can result in a greater level of accuracy when used with nonaqueous liquids and solutions at volumes lower than 0.5 μL. Conversely, air displacement pipetting is compatible with most aqueous solutions at volumes of more than 0.5 μL, and can be used with disposable tips to eliminate the risk of liquid carryover, which can cause cross-contamination.
The choice between these two mechanisms should be considered in conjunction with the desired transfer volume range, throughput, and other application requirements. The optimization parameters discussed in this article are applicable for both mechanisms.
Methods
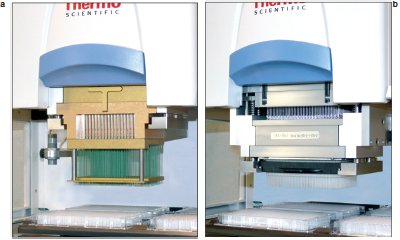
Figure 1 - a) 384-channel, 0.1–50 μL positive displacement pipetting head. b) 384-channel, 0.5–30 μL air displacement pipetting head.
All dispensing was performed using the Thermo Scientific PlateMate 2x3 or PlateMate Plus (Thermo Fisher Scientific, Hudson, NH) (Figure 1) with 384-channel air and positive displacement pipetting heads. All reagents were dispensed directly into dry microplates. The positive displacement head was used to dispense 200 nL and the air displacement head 500 nL. All dispensed reagents were fortified with 10% dye in order to obtain a colorimetric reading; 50 μL of water was added to the dry dispense microplates and the absorbance was recorded at 412 nm after 1 min of orbital shaking and 1 min of 1750-rpm centrifugation.
Parameters for optimization
There are a number of different parameters that can be optimized, depending on various experimental protocols that are being performed. These include:
- Air gap: In combination with a blowout, this will ensure complete aspiration of the liquid volume.
- Blowout: Moving the pipetting head piston past the zero volume dispense point pushes out a small volume of air after the liquid. This aids in pushing any liquid on the outer orifice of the tip into the labware, for a complete liquid dispense.
- Aspiration and dispense speeds: In general, thick and viscous liquids require a slower aspiration and dispense. The common occurrence of adherence to the side of the tip, and hanging drops, can be eliminated by much slower dispense speeds.
- Dwell times: This is the amount of time that the tip remains in the dispense/aspirate location after moving the liquid. This allows for the pressure to equalize in all 384 pistons.
- Neat versus incremental dispense: Neat dispensing was used here, where a sample was aspirated from a source and dispensed directly into the labware. An incremental cycle can also be performed, which involves an aspiration with a dispense prior to dispensing into the labware.
- Overstroke: This involves the aspiration of the reagent and dispense back into the source. This is routinely used in incremental dispensing.
- Tip heights: Tip height and placement in the labware well is an important factor in achieving optimal automated liquid handling performance.
- Tip touch: Touching the tip to the side of the well can remove droplets that adhere to the pipet tip after an aspirate or dispense.
- Offset move command: This allows stage adjustments in the X-Y planes for optimal positioning of labware.
- Volume correction: The ability to adjust pipetting head piston movements and timing for viscosity and specific gravity of solutions used in liquid handling procedures.
Performance with four reagent types
Four different reagents with varying liquid properties were used with each pipet head:
- 90% Dimethyl sulfoxide (DMSO) with dye—commonly used in compound screening experiments
- 10 mM Tris HCl, 1.5 mM MgCl2 (buffer A) with dye—commonly used in PCR reactions
- 20% glycerin with dye—a common viscous liquid
- Water with dye—used as a control.
A standard yellow dye was used to measure the pipetting performance in each case. A comparison of nonoptimized, minimally optimized, and fully optimized conditions demonstrates the improvement in accuracy and precision that can be achieved with minimal adjustments.
Results
Table 1 - Randomized versus optimized conditions
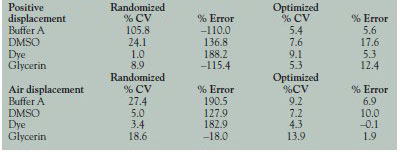
In order to understand the complete impact of optimization steps, data obtained before and after various optimization processes were compared. Nonoptimized data were obtained using randomly set parameters for all commands on the Thermo Scientific Control-Mate software (Thermo Fisher Scientific), which was used to manage the PlateMate instruments. Optimized data were obtained through the introduction of optimal parameters, based on an empirical knowledge of automated liquid handling. Furthermore, the parameters were adjusted according to the reagent under study. As a result of this optimization, a significant improvement was observed, as seen in Table 1.
Table 2 - Optimization parameters for the four reagent types
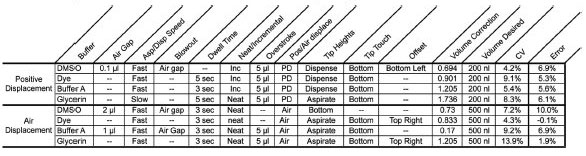
Each of these reagents was optimized with regard to all 10 previously discussed parameters. As shown in Table 2, this has a significant effect on the accuracy of the data obtained.
Performance consistency
One major advantage of using automated platforms is the consistency with which results can be generated after several cycles. In order to address experimental variation, resulting from either the automated liquid handling system or in downstream processes, each experiment was performed 50 times using the dye solution. Periodic recordings were taken and comparable results were observed for all dispenses. This indicates that consistent results can be achieved using automated liquid handling equipment.
Conclusion
Optimization of both aspirating and dispensing parameters in automated liquid handling can significantly enhance the performance of an automated liquid handling platform, such as those in the PlateMate range. Several parameters can be optimized in the instrument programming interface to ensure that accurate volumes are pipetted each time, to achieve precise experimental data. As demonstrated using the PlateMate instruments, different liquid properties require a variety of parameters to be optimized for accurate performance. It is therefore important to fully understand such information to ensure precise pipetting with every experiment.
Mr. Hewson is Applications Scientist, Thermo Fisher Scientific, 22 Friars Dr., Hudson, NH 03051, U.S.A.; tel.: 800-345-0206; fax: 603-595- 0106; e-mail: [email protected].