There has been a huge increase in
the use of biodiesel fuels. Biodiesel
oil is biodegradable, nontoxic,
does not contain aromatics, and
does not contain sulfur, which
avoids sulfur emissions. Basically,
biodiesel is made by the transesterification
of vegetable/animal
waste cooking oils. The pure product,
called B100, is added to normal
diesel fuel in varying amounts.
The “B” number designates the
percentage of biodiesel in a biodiesel/petroleum diesel blend (e.g., B20 is 20% biodiesel/80% petroleum diesel).
Glyceride residues in biodiesel and
blends can foul engine injectors
and form deposits on essential parts
in the diesel engine. Also, the shelf life of fuels depends on the
level of glycerin. It is essential
that accurate, efficient methods
for quantifying glycerin and
glycerides are available to the
biodiesel
industry.
The American Society for Testing
and Materials (ASTM)
and the European Method
Deutsches Institutfür Normung
(DIN) describe the primary
physical and chemical
testing methods for biodiesel
oil. Gas chromatography is
ideal for measuring important
parameters such as total glycerin,
fatty acid methyl esters
(FAMEs), and methanol levels
in biodiesel
fuel. Methods such as
ASTM D-6584 and EN14105 are
industry standards for testing
total glycerin and glycerides in
biodiesel oil. In these methods,
the column recommendation
is listed as a 10 m × 0.32 mm
i.d. column with a 0.1-μm film
of 5% diphenyl/95%
dimethyl
polysiloxane. This column is
connected with a retention gap
to make the on-column injection feasible. The methods allow the use of fused silica as well as metal as tubing material.
The 0.53-mm MXT®-Biodiesel
TG solution with integrated
Integra-Gap™ retention gap
(Restek Corp., Bellefonte, PA),
as discussed here, will hopefully
trigger a timely review of these
methods, to make triglycerides
analysis more practical.
Unbreakable column
solutions
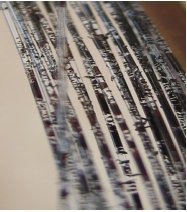
Figure 1 - Result of high-temperature application to polyimide-coated capillary: oxidation of the protective coating.
Fused-silica columns are generally
very temperature stable and are usually
the first choice for GC analysis.
However, when operating at temperatures
exceeding 350 °C, fused-silica
columns rapidly become black
due to oxidation of the protective
polyimide coating. This coating is
in place to protect the fused-silica
column from mechanical damage.
Any damage to the outside coating
will make the lifetime of the column
very unpredictable.
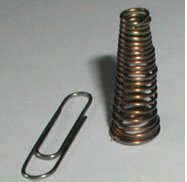
Figure 2 - MXT metal columns can be made to fit in any dimension.
Even fused-silica columns with special high-temperature (HT)
polyimide coating (HT equivalents)
become unpredictable and
break down relatively quickly.
Figure 1 shows the impact of long-term exposure at 430 °C: The polyimide
hardens, becomes black, and
eventually disappears completely.
Even in an early stage of this process,
the risk of column breakage
increases. To overcome this problem,
a stabilized metal column line
was developed: MXT®-Biodiesel
TG columns are deactivated using
Siltek® gap deactivation technology
(Restek Corp.). This technology
not only deactivates but also
stabilizes the stationary phase,
making the column extremely stable.
The columns virtually do not
degrade, even under temperatures
up to 430 °C. Thus, it is possible
to “bake out” any residue eluting
out after the triglycerides without
damaging the column. This process
keeps the analytical system
clean, so subsequent injections do
not have carryover from previous
samples. Metal columns are virtually
unbreakable and can therefore
be used in difficult environments
such as high-temperature GC, process applications, space missions,
and miniaturized solutions
(Figure 2).
Injection techniques for biodiesel
To measure the high-boiling
triglycerides
at low levels, it is
essential to have a good injection
setup that allows quantitative
measurement of triglycerides.
The best technique
is cold on-column, where the
sample is introduced as a liquid into the capillary column.Other techniques, such as splitless and programmed temperature
vaporization (PTV),
will show a significant degree
of discrimination.
In order to obtain a good on-column
injection, it is necessary to
use a retention gap1,2 to make sure
there is a band-focusing mechanism
in place. The retention gap is
usually 2–3 m nonpolar deactivated
capillary tubing with
an inside diameter of 0.53 mm to
allow most on-column
injections.
The mechanism of the retention
gap is described below and illustrated
in Figure 3.
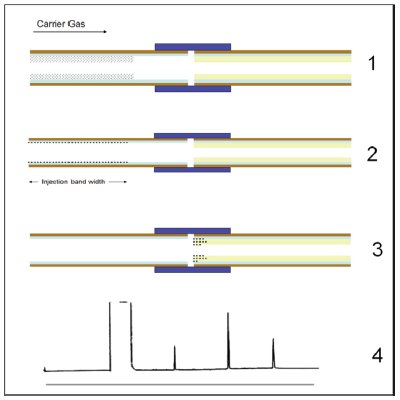
Figure 3 - Mechanism of a retention gap (see text).
- When applying on-column
injection, the solvent with
analytes will be distributed
over a section of the retention gap. The length of this section depends on the
injection speed, the carrier
gas flow, the type of solvent,
and the temperature. The
solvent must be distributed
evenly over the retention
gap. This will only happen if
the wettability of the surface
of the retention gap allows
it. Practically, for nonpolar
solvents such as heptane
and cyclohexane, nonpolar
(polydimethyl siloxane)
deactivated retention gaps
are used.
- During and after injection, the
solvent will evaporate and the analytes will deposit on the
retention gap surface. This is
the initial bandwidth, which can
be significant depending on the
injection parameters.
- Starting the temperature program
will move the analytes toward
the column, where they will concentrate
in the stationary phase,
focusing the broad initial injection
band.
- The result is correct chromatographic
peaks: no peak splitting or
peak broadening.
If a retention gap is not used and
the sample is injected straight onto a “coated” capillary, the initial
bandwidth, as shown in Figure
3 (line 2), will not be focused,
resulting in unpredictable peak
broadening and peak splitting. The retention gap “fixes” the injection error that is always made when performing the liquid on-column injection. Retention
gaps are commercially available
with different deactivations. If
not offered as a “retention gap,”
one can also purchase 0.53-mm-i.d. deactivated fused-silica or MXT tubing and use that as a retention gap.