An air-cooled tube in a laboratory furnace (crystallization shelf) that regulates the crystallization fronts and rates in columns of crucibles was described in a previous paper.1 This paper illustrates the development of the interior of an air-cooled tube (Figure 1), and a numerical study of new crystallization parameters (Figures 2–4). The improved cooler is simpler to build and handle, and features regulation of different paths and airstream rates, i.e., crystallization rate, and a different number of crucibles, i.e., crystallization testing (with the aid of modular and movable cylinders and tube [see Refs. 3 and 8 in Figure 1]). The cooler (cold comb) allows simultaneous crystallization tests (comb) of different crystallization parameters for the purpose of obtaining single crystals from a family of newly synthesized compounds with layered crystal structures (see Tables 3.1-5 and 3.1-8 in Ref. 2) using a laboratory furnace.

Figure 1 - Air-cooled tube (modular bilateral crystallization horseshoe comb) in a laboratory chamber furnace: 1) laboratory tube furnace, 2) fragment of tube in the shape of the letter ―"U" in a horizontal plane (horseshoe), 3) columns of modular and movable cylinders (crystallization skeleton key), 4) slide bars, 5) plugs with modular heads (cold comb), 6) columns of crucibles, 7) cross-section of cooler (crystallization key), 8) movable tube (crystallization telescopic key), 9) radial holes in a horizontal position ("O" thresholds) or vertical position ("I" threshold sockets), 10) movable mounting rings, 11) Tamman test tubes,2,3 and 12) cross-section of the cooler (crystallization threshold).
On the basis of the continuity and cross-section of the airstream, for the velocity of the airstream on the threshold wtr, the following expression is obtained:
Where wt denotes the average velocity of the airstream in the tube without threshold, and
in radian, dtr, and dt are the diameter of the threshold (hole) and tube, respectively (Figure 1b).
Based on the fact that the heat removed from the tube wall is equal to the heat accepted by the airstream, the following equation may be written:
Where dl is the elementary length of the tube (see Figure 1b), α is the coefficient of heat transfer from the cooler wall to the airstream (Eq. [2] in Ref. 1; p. 152 in Ref. 4], ΔT(l) denotes the difference between the temperature of the melt and that of the airstream at point l, ρa is the air density, ca is the heat capacity of the air, and dT is the difference in the temperature of the airstream between points l and l + dl. Integration of Eq. [2] within the limits from l = 0 to l = lp gives the following expression (integral equation):
Where ΔT(lp) and ΔT(0) are the difference between the temperature of the melt and that of the airstream at point l = lp and l = 0, respectively (Figure 1b).
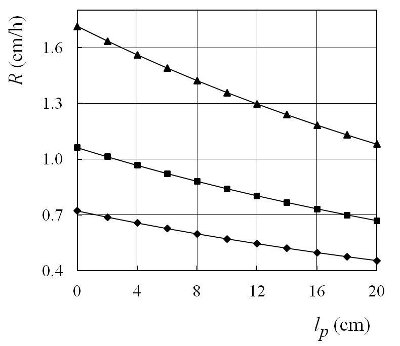
Figure 3 - Crystallization rate R as a function of the position of the plug along the cooler, lp, when ΔT(0) = 100 °C, δa = 0 cm: –▲– dtr = 1.4 cm, –■– dtr = 1 cm, –♦– dtr = 0.5 cm.
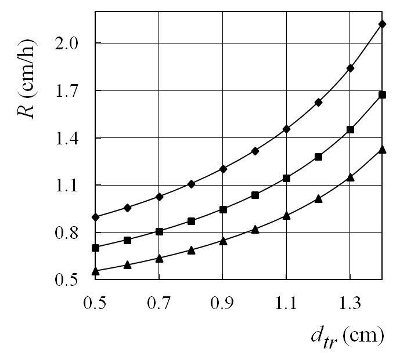
Figure 2 - Crystallization rate R as a function of the diameter of the threshold, dtr, when ΔT(0) = 150 °C, δa = 0 cm: –♦– lp = 10 cm, –■– lp = 20 cm, –▲– lp = 30 cm.
In accordance with Eqs. [1] and [2] in Ref. 1, and Eqs. [1] and [3] above, the authors obtained the numerical values of crystallization rate, R, as a function of dtr (Figure 2), lp (Figure 3), and δa (Figure 4). In the case of bismuth: Tmelt = 271 °C, λ = 52300 J/kg, ρ = 9800 kg/m3, and kc = 7.2 W/mK. In all numerical calculations, taken such that: kp = 0.756 W/mK (borosilicate glass, softening point ≈ 600 °C), ρa = 0.682 kg/m3, ca = 1.035 kJ/kgK, dt= 2 cm, wt= 1 m/s, δp= 0.5 cm, and δc = 0 cm (Figure 1b).
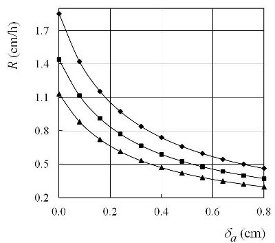
Figure 4 Crystallization rate R as a function of the distance of the plug head from the surface of the melt, δa, when ΔT(0) = 200 °C, dtr = 1 cm: –♦– lp = 10 cm, –■– lp = 20 cm, –▲– lp = 30 cm.
The shapes of the crystallization fronts in each crucible are regulated by the plug fronts, i.e., the plug head (crystallization seals, Figure 1a, and mushroom shapes, Figure 1b). The crystallization rate of each crucible can be regulated by the diameter of the threshold hole (Figure 2) by the position of the plug along the tube (Figure 3) and the distance of the plug head from the surface of the melt (Figure 4). The crystallization rate in the crucible can also be regulated by the temperature and velocity of the airstream at the entrance of the tube, and the height of the plug (Figures 2–4 in Ref. 1). The temperature gradient is regulated by the distance plug front from the upper (or lower) furnace wall h. Different temperature gradients in the crucibles can be tested simultaneously using an inclined tube.
Optimizing laboratory furnace usage
Cylinders and plugs (see Refs. 3 and 5, Figure 1a) of various numbers, shapes, and dimensions can be mounted (fineness of comb) and thus tested simultaneously. By varying the internal and external shape and dimensions of the cooler, a set of crystallization horseshoe combs can be modeled for tests over a wider range of crystallization parameters. The cooler can be installed in a crucible furnace in a horizontal position (or vertical position, shaped like a crystal drop earring) or molded into a rectilinear shape and installed in a tube furnace in the horizontal position (crystallization test bench). By using several different coolers (a family group of horseshoes in the chamber furnace), the crystallization tests can be expanded to several columns of crucibles. This increases the number of simultaneous crystallization tests of different crystallization parameters (using an air [molecular] body with multiple control options, i.e., they are easy to build and handle, and are modular, portable devices—crystallization skeleton key). This provides a rapid way to obtain crystals from substances with unknown crystallization parameters and make optimal use of space in the laboratory.
References
- Cabric, B.; Danilovic, N. et al. Am. Lab. 2011, 43(7), 18–9.
- Wilke, K.-Th.; Bohm, J. Kristallzüchtung. Verlag Harri Deutsch: Thun, Frankfurt/Main, 1988.
- Vilke, K.-T. Virashchivanie kristallov; «Nedra». Leningradskoe Odelenie: Leningrad, 1977 (in Russian).
- Schramek, E.-R. Taschenbuch für Heizung + Klimatechnik. Oldenbourg Industrieverlag GmbH: München, 2007.
Prof. Cabric and Mr. Danilovic are with the Faculty of Sciences, University of Kragujevac, P.O. Box 60, 34000 Kragujevac, Serbia; tel.: +381 34 300 267; fax: +381 34 335 040; e-mail: [email protected]. Mr. Janicijevic is with the Faculty of Technology and Metallurgy, University of Belgrade, Serbia.