Freeze-drying is a complex and not completely understood process that requires one to carefully balance product requirements with equipment capabilities. Regardless, it remains a proven preservation process for pharmaceuticals, foods, historical documents, plants, and animals. Freeze-drying relies on fundamental principles of physics and chemistry. However, even those well versed in the physical sciences are often unfamiliar with the interplay of the basic mechanisms at work in the lyophilization process.
The nature of water
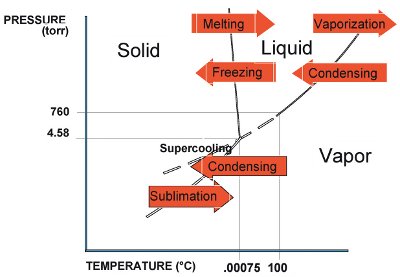
Figure 1 - Phase diagram of water.
Most freeze-drying involves the removal of water. (The same principles described herein apply, mutatis mutandis, to nonaqueous solutions.) Water, of course, exists in three states: solid (ice), liquid (water), and vapor (steam). The relative energy state in which a quantity of water exists depends not only on temperature, but also on pressure, as shown in the phase diagram of water (Figure 1). The lines between the states are known as phase transition lines. For freeze-drying, the most important of these lines is the one between the solid state and the vapor state. As can be seen, in order to change directly from solid to vapor (that is, sublimate), one must have conditions below 0 °C and 4.58 Torr. (A Torr is 1/760th of a standard atmosphere. Pressures observed during most freeze-drying processes are described in milliTorrs, or 1/760,000th of a standard atmosphere. An equivalent vernacular term for milliTorr is “micron.”) Furthermore, to change between states, one must add or subtract energy, known as latent heat. The latent heat of sublimation is 619 cal/g (1114 BTU/lb) for water.
Supercooling, depression of freezing point, and heat transfer resistance
The above does not mean that a freeze dryer merely has to achieve 0 °C. If the average person is asked at what temperature water freezes, he or she will say 32 °F (or 0 °C). In reality, though, this is not quite true. Although water can solidify at 0 °C, pure water likely will not. In fact, ultrapure water, such as Water For Injection (WFI, which is used for parenteral solutions), may not solidify until even below –18 °C, a phenomenon known as supercooling.
Beyond this, it is well known that adding solutes to water, such as NaCl, lowers the freeze point even further. Indeed, all solutions will exhibit either a eutectic point (for crystalline structures) or a glass transition point (for amorphous structures) that is well below 0 °C. Additionally, the heat transfer route between the product and the refrigeration system usually has much resistance. In order to freeze product in a vial, heat must travel out of the product, through the glass vial (which is an insulator), through the stainless steel plate of the shelf (stainless is a poor heat conductor), into a heat transfer fluid, and finally be removed at the refrigerant heat exchanger. Thus, in the end, a freeze dryer should be able to reach at least –55 °C shelf temperature to ensure that most formulations will freeze completely.
Cooling rates and ice crystal formation
However, freezing a product is not as simple as obtaining some ultimate temperature to ensure complete solidification. The rate of freezing affects water crystal size. In general, if one cools product quickly, the temperature distribution in the vial will be heterogeneous, i.e., cooler at the bottom and warmer at the top. When crystallization starts at the bottom, crystal growth upward will be slowed by the warmer volume above it. Slow crystal growth promotes large crystals. The opposite is true for slow cooling. Slow cooling promotes a uniform temperature throughout the vial. When crystallization begins, it tends to be quick because the entire volume is cool. Fast crystallization produces small crystals. The ultimate size of the ice crystals is important because of how it affects drying. When relatively large ice crystals sublimate, they leave behind relatively large pores, which provide less resistance for other ice crystals to sublimate and leave the product. On the other hand, small ice crystals leave small pores, which in turn increase resistance to drying.
Vapor pressure
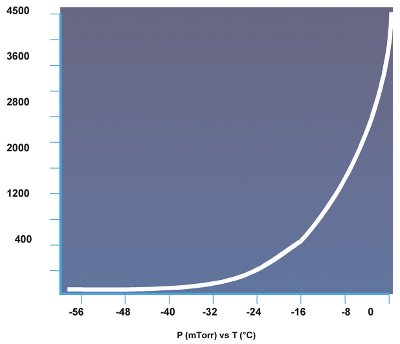
Figure 2 - Vapor pressure of ice.
Before describing the drying phases, it is important to understand the concept of vapor pressure, and the vapor pressure of ice in particular. Vapor pressure is the point at which the vapor of a substance is in equilibrium with its liquid or solid form. In practical terms, if the atmosphere surrounding a substance is below its vapor pressure, boiling (liquid) or sublimation (solid) takes place. Conversely, if the atmosphere surrounding a substance is above its vapor pressure, condensation occurs. Vapor pressure is temperature dependent only. Figure 2 shows changes in the vapor pressure of ice versus temperature.
Primary drying
Primary drying is the part of the freeze-drying cycle in which unbound solution is removed through sublimation. To effect primary drying, one must have frozen the product completely, reduce the pressure surrounding the product to a value below its vapor pressure, and add the latent heat of sublimation (619 cal/g). Most primary drying cycles are done at a pressure of 100–200 mTorrs. However, recall that pressure and volume are inversely related (the lower the pressure, the greater the volume). At 100 mTorrs, what would be a cubic foot of water vapor at standard conditions grows into 7600 ft3. Because standard vacuum systems cannot pump water vapor (since they use oil as a seal), the relative size of the vacuum system would be impractically large.
The most common solution is to condense the water vapor back into ice. Thus, freeze dryers will have either a tube or plate condenser with a surface area approximately equal to the shelf area. In fact, it is the condenser that actually provides the pumping action to move water vapor from the product to the condenser. Because the condenser is much colder than the product (–50 to –60 °C as opposed to –10 to –20 °C), the vapor pressure at the condenser is much lower than at the product. Water molecules that leave the product vial simply follow the pressure gradient.
A final but important caveat for primary drying is that one must never allow the product temperature to exceed its eutectic or glass transition temperature. If this temperature is exceeded, ice in the vial will begin to liquefy, a condition known as meltback. The liquefied solvent will form a skin over the product and trap moisture within it. The end result will be not only an unattractive product, but an unstable product.
Secondary drying
By the end of primary drying, most products have lost 95% of their moisture. However, the remaining 5% moisture is often enough to still support the biological or chemical activity that causes degradation. Therefore, it is necessary to remove some of the bound or adsorbed water clinging to the product. This is a process known as desorption. Desorption involves removing water molecules that cling to the surface of the product by means of Van der Waals forces. The process is much more energy intensive than sublimation. Typically, the shelf temperature is raised 20 or 30 °C above the final primary drying temperature. (Because all the loose water has been removed, there is no longer a danger of meltback.) Still, secondary drying usually takes about the same amount of time as primary drying.
Determining the final required dryness of a product largely comes down to empirical stability studies. The dryness of the product in the freeze dryer can be determined in several ways: observation of product temperature, measurement of the partial pressure of water vapor, a rate of rise test (only possible on systems that have a valve between the product chamber and the condenser), and finally, old-fashioned trial and error.
Conclusion
Freeze-drying research began more than 50 years ago in an effort to preserve blood plasma. Today, it is used to preserve a wide variety of medicinal products that otherwise would lose their efficacy in a relatively short time. Freeze-dried vaccines can be delivered halfway around the world with little worry of loss of efficacy or sterility. Research into the mechanisms of freeze-drying continues through the present, with more yet to come.
Dr. Dern is an Applications Engineer, SP Industries, Hull and VirTis Freeze Dryers, 937 Mearns Rd., Warminster, PA 18974, U.S.A.; tel.: 215-672-7800, ext. 1375; fax: 215-672-7807; e-mail: [email protected].