There is an increasing demand for a dedicated, high-quality, and easy-to-use instrument to measure off-gas exhaust in laboratories and industrial settings during the fermentation process. Better monitoring of CO2 and O2 emissions helps to determine the fermentor’s respiration rate, which results in increased production efficiency—a critical requirement in today’s demanding laboratories. Further, by measuring hydrocarbons (e.g., ethanol in yeast processes) and other off-gases in the reactor, better insights into and control of the process can be achieved.
While traditional instrumentation provides data for control loops, thereby ensuring constant conditions, it is not well suited for the analysis of fermentation metabolism. Recent advancements in a technology originally invented by Alexander Graham Bell at the turn of the 20th century address the accuracy, ease of use, and stability issues that conventional methods have not. The combination of photoacoustic spectroscopy (PAS) and magnetoacoustic spectroscopy (MA) is providing laboratory scientists with the accuracy and stability needed to measure gas concentrations.
In many fermentation processes, small fermentation vessels are used during the development stages. The amounts of discharge gases (O2 and CO2) to be measured are also small. Therefore, measurement equipment that requires large samples is not appropriate. To address this issue, PAS/MA is used to measure carbon dioxide and hydrocarbons, and oxygen at very low levels.
Using PAS/MA, it is possible to construct a measurement system that has a measurement chamber with a volume of 0.15 cm3. This means that the instrument is “satisfied” with a continuous gas flow of 130 mL/ min, and reacts very quickly. The PAS/MA measuring system is integrated so that CO2/hydrocarbons and O2 are detected in real time by the same detector, which provides the correct time correlation between the gases.
The following issues need to be considered: What should laboratory scientists address when monitoring off-gases during the fermentation process? What is required from a fermentation monitor?
Accuracy and stability
The monitoring of fermentation processes is often based on the identification of small deviations from normal operation. Therefore, accuracy is critical to obtaining good results. Typically, fermentation processes take place over several days; thus the monitor must have minimal drift to avoid disturbance from repeated calibrations during operation. PAS/MA technology is very accurate and stable over long periods of time (calibration is only required every 6–12 months).
Rapid and synchronous response
To benefit from the information that may be obtained from combined oxygen and carbon dioxide analysis, it is necessary to have synchronous results since lack of synchronicity may produce artifact effects. Rapid instrument response is also important, since immediate response to deviations from ideal operation may be required. PAS/MA provides both rapid response and synchronous results.
Low sample volume
For laboratory fermentors, the gas volume needed for gas analysis may be important since low amounts of gas are available. As mentioned above, PAS/MA enables gases to be monitored at very low levels.
Low cost of ownership
In today’s laboratories, it is important that instruments are plug-and-play with minimal need for support and maintenance. Complex instruments generally require regular support from qualified personnel, in effect increasing the instrument’s total cost. Another running cost is the use of gas and other consumables. Compared to traditional technologies such as mass spectroscopy, gas chromatography, and IR transmission spectroscopy, PAS/MA is basically maintenance free and more cost effective. The instrument cost is naturally of concern, but the actual instrument cost is often secondary to the running costs. In addition, to reduce overall cost, many fermentation monitors are equipped with multiplexers, which allow sampling from several different fermentors. Integrated control of multiplexers is important when choosing instrumentation for fermentors.
Photoacoustic spectroscopy
Photoacoustic spectroscopy employs the sounds produced by a gas sample in a closed vessel while being subjected to modulated light to determine concentrations of the species in the gas. While the PAS principle was first observed by Alexander Graham Bell in 1880, it was not introduced in commercial instrumentation until the 1990s.
Infrared spectroscopy is based on the absorption of infrared light. When infrared light is radiated through a gas, the gas absorbs some of the light energy. The amount of energy absorbed is proportional to the concentration of the gas. To achieve a quantitative result of a specific gas in a mixture of gases, one can use optical filters, taking advantage of the fact that different gases absorb light differently at different wavelengths.
Traditional infrared spectroscopy measures the transmitted light through a sample gas cell and a reference cell, followed by subtraction of these two values. A low concentration of gases will result in high light transmission. Since noise is typically proportional to signal, this subtraction of two large values will be dominated by the noise on the large numbers.
Photoacoustic spectroscopy makes use of the fact that the absorbed energy is released immediately as heat, resulting in an increase in pressure in the closed vessel. When the light source irradiating the gas sample is modulated, i.e., routed on and off at a frequency of 4–350 Hz, the pressure in the vessel will rise and fall, creating a pulsating pressure wave. Microphones can detect the pressure wave as an acoustic wave. Since the signal detected is the absorption, small signals and large signals will have similar low relative noise. Furthermore, microphones have a far wider linear range and higher long-term stability than photodetectors.
Carbon dioxide, ethanol, and many hydrocarbons absorb light in the infrared spectrum, and therefore can be detected using the photoacoustic principle. Oxygen does not absorb infrared light, and thus has to receive energy from another source if a microphone is to be used to detect the acoustic wave from the gas.
The paramagnetic properties of oxygen must be considered here. When subjecting a gas mixture (oxygen, carbon dioxide, and ethanol) to a pulsating magnetic field, the oxygen molecules start to vibrate. This molecular vibration is transferred into heat, which is registered by the microphone pressure change, thereby giving an acoustic signal. This is called magnetoacoustics (see Figure 1).
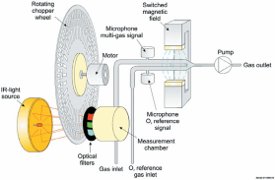
Figure 1 - Diagram showing a three-channel fermentation monitoring system.
Features of integrated photo/magnetoacoustics
The use of microphones as detectors in integrated PAS/MA imparts extraordinary stability to the instrument, with an interval between calibrations of 6–12 months. Due to the high inherent sensitivity of integrated PAS/MA, the measuring chamber can be made very small. This allows a rapid analyzer response and a low gas flow rate. Furthermore, the true integration of the measurements ensures synchronous responses of all gas concentrations. New designs permit a very simple installation procedure; for a complete system with multiplexer, installation can be carried out within 1 hr with minimal user training.
Alternative methods for fermentor discharge analysis
Two alternatives to integrated PAS/MA exist for fermentor discharge analysis. Mass spectroscopy is the most expensive routine measurement. This method has been in use for many years and is characterized by rather complex operation and consumption of a carrier gas. It has the benefit of very accurate measurements, which are comparable to those attainable with integrated PAS/MA, as well as the ability to measure a wide range of species.
While the potential to analyze many different species is a common argument, the dominant application of mass spectrometers remains discharge monitoring of O2 and CO2. Since the investment and running costs of mass spectrometers are high compared to a PAS/MA system, mass spectrometers should be the choice for fermentor discharge analysis only if there is a real need for the extra information from a spectrometer. Even in a case in which this information is desired, it may be advantageous to use integrated PAS/MA in combination with mass spectrometers to employ the high stability of PAS/MA.
A less-expensive alternative is a traditional IR analyzer in combination with paramagnetic or electromagnetic oxygen detection. The fundamental technology of measurement is well proven and the investment is lower than PAS/ MA. However, the analytical results are not as accurate, and the analyzers are designed for flow rates around 1/min, which is close to the upper limit for laboratory-scale fermentors. In addition, the use of two separate instruments has several drawbacks: From a service perspective it becomes more complex, and the results can never be truly synchronous from two separate instruments. Finally, such instruments may require daily calibrations, which do not fit well into the monitoring of fermentation (can take more than a week).
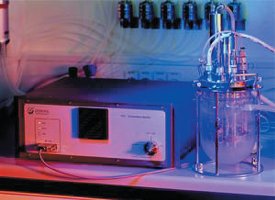
Figure 2 - Innova model 1313 Fermentation Monitor.
The Innova model 1313 Fermentation Monitor (Luma-Sense Technologies, Santa Clara, CA) measures O2, CO2, and a user-defined hydrocarbon (Figure 2). The instrument software is prepared for monitoring up to 36 fermentors by connecting up to three 12-channel multiplexers. Discharge gases from each fermentor are transported through Nafion® tubing (DuPont, Wilmington, DE) in order to equalize the water vapor with the ambient level. If one expects occasional overfoaming or some other liquid contaminants to be present, then Genie hydrophobic membrane separators (A+ Corp., Gonzales, LA) can be installed.
The Fermentation Monitor has analog outputs for each gas, and can, together with the Multipoint Sampler, be controlled from a PC, where the current gas values are stored. Using the application software that accompanies the monitor, real-time gas concentrations can be displayed on the PC. In addition, these data may also be interfaced to the major industrial process control communication protocols, as well as proprietary communication protocols of selected fermentation systems.
The manufacturer also offers a dedicated fermentation monitoring system that includes not only the monitor and a multiplexer, but all relevant tubing and connections with software and PC. The system can be mounted in an industrial 19-in. rack (see Figure 3).
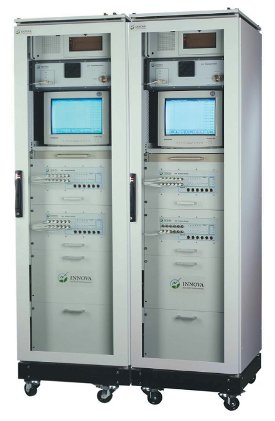
Figure 3 - Fermentation rack (LumaSense Technologies).
Conclusion
Compared to conventional methods for the analysis of fermentor discharge, integrated photoacoustic spectroscopy and magnetoacoustics is a highly accurate and lower-cost solution when factoring in running costs, simple operation, and calibration requirements.
Mr. Shaver is Senior Product Marketing Manager, LumaSense Technologies, 3033 Scott Blvd., Santa Clara, CA 95054, U.S.A.; tel.: 408-727-1600; fax: 408-727-1677; e-mail: [email protected].