Various materials, typically gels or dispersions with a high concentration of suspended particles, can behave either as elastic solids or as liquids, depending on the degree of force or stress to which they are subjected. Yield stress is the rheological term used to define the point at which this transition occurs. At stresses above the yield stress, the material behaves as a liquid, and below it as a solid.
The yield stress value is of interest to various manufacturers because it is an important parameter for many commercial products. Butter, toothpaste, sealant, paint, and lipstick are just a few examples of materials that have a yield stress. This article considers the definition of yield stress, its practical relevance, and the merits and limitations of different measurement methods. Also examined are the concept of dispersion stability and the formation of particulate gels, industrially important systems that almost invariably show a yield stress.
Dispersion stability
When considering dispersion/suspension stability, it is important to realize that there are two different types of stability, which combine to determine overall system behavior. Colloidal or chemical stability is determined by interparticle forces within the system. If the net force between particles is attractive, then there will be a tendency toward aggregation, whereas if it is repulsive, particles will remain discrete. Interparticle forces can be manipulated by changing formulation chemistry.
Separation stability, on the other hand, describes the response of the system to gravitational forces. A system that has separation stability resists the effects of gravity, and the dispersed medium neither sinks nor rises to the top. Separation instability is therefore practically observed in the form of phenomena such as creaming and sedimentation.
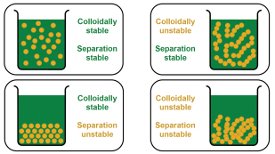
Figure 1 - The different types of stability encountered with concentrated dispersions.
In dilute systems, colloidal and separation instability tend to go hand-in-hand. If the system is colloidally unstable, then there is a tendency toward aggregation, and the formation of larger particles that either sink or float. In concentrated dispersions, however, things are not so simple (Figure 1), overall system behavior being a complex function of particle size, disperse phase concentration, and the nature and strength of interactions between particles.
Concentrated, colloidally stable dispersions are also stable with respect to separation if the physical properties of the system are such that it can resist the effects of gravity. Nanoparticles often form systems that exhibit this type of behavior. Dispersions with larger particles, however, may be colloidally stable, because the repulsive forces between particles are sufficient to keep them apart, but separation unstable because these forces are not sufficient to resist the gravitational pull.
A concentrated dispersion will be colloidally unstable if net interparticle forces are attractive. This may promote separation instability, as with dilute suspensions, but in some cases the attractive forces between aggregated particles are such that a stable, self-supporting gel network is formed. The system exhibits colloidal instability and separation stability, and the resulting particulate gels always have a yield stress.
Defining yield stress
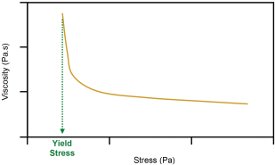
Figure 2 - Viscosity as a function of applied shear stress.
In descriptive terms, yield stress is the stress at which a material transforms from a soft solid to a shear-thinning liquid. Graphically, this is observed as a very dramatic fall in viscosity at some particular value of applied stress (Figure 2).
Strictly speaking, at stresses below the yield stress, viscosity should be infinite, but pragmatically it is often irrelevant whether viscosity is infinite or just very large. A sharp transition in viscosity is the defining feature when determining yield stress.
Bulk and wall yield stress
When a sample is held between two surfaces (walls), the particles will stick to one another and to the surfaces. As shear is applied, the dispersion may yield at the wall or “slip” before it starts to yield internally. There is a wall yield stress and a bulk or interior yield stress. With relatively smooth surfaces, the wall yield stress is lower than the bulk, and premature slippage is observed. With rougher surfaces, only a single yield stress will be observed. The relative importance of these two values is application specific (see example below).
Why is yield stress important?
In practice, yield stress can be thought of as a measure of a dispersion’s physical strength or ability to hold its shape. A material with a high yield stress will be difficult to move easily—to pump, for example— and will hold its shape well. Conversely, a material with a low yield stress may be easy to work or spread but may flow in an undesirable way in certain circumstances.
In terms of product quality, yogurt with a high yield stress will appear to be thick and creamy as opposed to thin and watery. For very different materials such as mortar or sealant, the yield stress must be optimized such that the product can be worked easily (i.e., is mobile when some stress is applied) but then holds its shape rather than slumping after application. The yield stress requirements for a coating product designed for use on a wall will be different from those of a material used on a floor; in both cases, however, yield stress can be used to determine the stable thickness of product that can be applied.
For other applications, there is a need to suspend coarse particles in a colloidal dispersion. An example of this type of system is drilling muds for oil exploration. Here, yield stress can be used to determine the size of particles that the dispersion can support.
Smay, Cesarano, and Lewis1 provide an interesting practical example of the use of yield stress data. Rheological studies were carried out in support of the development of a print system for producing 3-D structures. One of the design requirements was plug flow within the print system to ensure that the colloidal ink deposited on the surface was consistent in terms of composition and history.
A dispersion subjected to shear stress above the wall yield stress, but below the bulk yield stress values, will move in plug flow. Basically, since the material has not yielded internally, slippage occurs at the wall with no shearing of the material. In the example cited here, an optimal design for the printing system was therefore determined from measurements of wall and bulk yield stress.