The 35th International Symposium on Capillary Chromatography (ISCC) was one of three parallel
tracks featured at the Joint Congress 2011. The
meeting was organized by CASSS and was held May
1–5 in San Diego, CA.
Instrumentation has a life cycle. Gas chromatographs are mature, so the
cycle is probably 10–12 years. The Agilent 7890 gas chromatograph (Agilent Technologies, Palo Alto, CA) is over four
years old, so the product planners are probably
only starting to think about a replacement.
This is the appropriate time for the
technical leaders to offer advice. After all,
when the 6890 replaced the 5890, backflushing
was not offered.
Prof. Milton Lee (Brigham Young University,
Provo, UT) chaired a session that was attended
by approximately 100 gas chromatographers
and meant to distill features and attributes that
should be considered. As examples, Prof. Lee
listed resistively heated columns, multidimensional GC, integrated (on-line) sample prep,
smaller footprint, and smarter instruments that
generate quality results, even when operated
by nonspecialists.
Then Prof. Lee asked a panel of four experts (two vendors and two
users) to make short presentations. Dow Chemical is the world’s
largest user of gas chromatographs, with over 1000 active chromatographs.
Thus, Prof. Lee selected the company’s Associate Technology
Director & Global Separations Leader, Jim Luong (Dow
Chemical Co., Fort Saskatchewan, Alberta, Canada) to report on a
survey of GC users at Dow. Luong asked his colleagues to point out
opportunities for inclusion in next-generation instruments. The list
included:
-
Continuous development of planar microfluidics devices
such as Agilent’s CFT and SGE’s (Ringwood, Victoria,
Australia) wafers
- Separation improvements
1) The column is the heart of chromatography and we are not
at the level of inertness we should be
2) “It can’t be done” should not be a barrier
- Reduced to the practice of multidimensional gas chromatography
(2DGC and comprehensive 2DGC)
- Advanced sample introduction system
- Selective detectors (e.g., sulfur chemiluminescence
detector,
nitrogen chemilumisence detector, elemental combusion system
for CHNOS [Costech, Valencia, CA], and Differential
Mobility Detector [Agilent])
1) Little has changed on the status of GC detection for many years
- Advances in miniaturization—articulating
the needs is important
- Software that is stable and improved over previous generations
- Wizards to aid in setting up applications.
Luong quickly expanded on each of these points. When he mentioned
the need for selective detectors, I thought about how different
the world would be if the element-specific detectors, such
as thermionic and photometric, became established before mass spectrometry grew dominant.
The second panelist was Dr. Hans-Gerd Janssen of Unilever
(Vlaardingen, The Netherlands), who reported on the
state-of-the-art in GC (Table 1). The current GC technology
is not robust by contemporary standards. Columns age
and MS filaments need replacement. Injectors and other
fittings start to leak with temperature cycling. The instruments
are slow, with cycle times in tens of minutes. Dr.
Janssen is aware that cycle times can be reduced by 90%
with modern technology. Other criticisms included difficulty
to use, inflexibility, and lack of a clean interface
between sample prep and the GC.
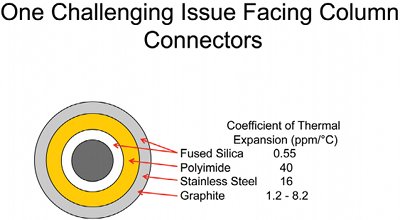
Figure 1 - Coefficients of thermal expansion for various materials in
gas chromatography. Repeated thermal cycles from repeated temperature-programmed
runs slowly accumulate stress and resulting movement, leading to
leaks during repeated runs. (Courtesy of Brian Jones, Restek.)
Representing the column vendors, Brian Jones of Restek
(Bellefonte, PA) followed with a
thoughtful review of current needs. He
cited an article in LC·GC from 14 years
ago on the same topic,1 and added “Rugged,
reliable separations that are tolerant
of dirty samples. Reliable and easy connections
for columns etc., especially in
the hot zone; faster cycle times; faster
detectors; true plug-and-play operation;
columns with a higher Tmax; and more
sensitive detection.” Brian went on to
explain that leaks in the hot zone probably
arise from the huge difference in
thermal expansion of the components
(Figure 1).
Stan Sterns, President of Valco Instruments
Co. (Houston, TX), finished out
the panel by showing examples of separations
using the best of today’s technology,
which includes temperature ramps
of 1200 °C/min. Further, the temperature
accuracy and reproducibility can be
held to better than 0.2 °C. Run times are
90% shorter than big-box technology and
more reproducible. One example showed
a chromatogram of biodiesel in less than
2 min and pesticide residues in 40 sec (Figure 2). Cooldown
was complete in 1 min, so the cycle time is less than 4 min
injection-to-injection.
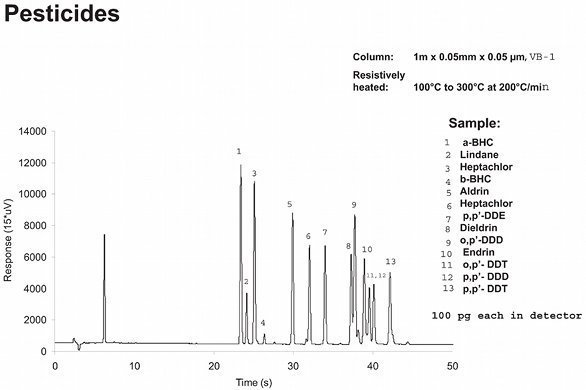
Figure 2 - Separation of pesticides using a 50 μm × 1 m VB-1 column and mini pulsed discharge detector.
The column uses resistive heating. Cold spots are eliminated with Valco center tap technology. (Courtesy of
Stan Sterns, Valco.)
Consumption of carrier and makeup gas and electricity is
reduced by similar factors. A typical big-box GC consumes
about 2 kW/hr. Air conditioning adds another 3 kW/hr. Over a
year, this is 43,000 kW/hr. At $0.15 kW/hr, the electrical cost
of a GC is about $6000/year. This does not count the cost of the
operating gases for column flow and detectors, which probably
adds another $1000/yr. Stan estimates that Valco’s technology
reduces the operating cost per run by at least 90%.
Finally, Prof. Lee opened the discussion to the floor. The goal was
to distill even more needs and ideas. Comments from the audience
included:
The lecture by Prof. Robert Synovec (University of Washington,
Seattle) earlier in the day showed that one common big-box GC
was slow and inefficient for early-eluting peaks (Kʹ <4). Prof.
Nick Snow (Seton Hall University, South Orange, NJ) concurred
with the earlier presentation by Prof. Lee and Dr. Synovec, citing
the need for better injection technology. Indeed, injection technology
still seems to be a weak point, even after six generations of
instruments. The injection process needs to be reengineered
from
the ground up to improve performance across the board. Particular
needs included lower band broadening; robustness (leak free,
especially with temperature cycling); and ease of use, particularly
for column installation.
Resistive heating can suffer from cold spots due to nonuniform
metal thickness. Stan Sterns countered that if the metal
is correctly applied, cold spots are not a problem. Plus, one can use multiple zone heating to avoid creating cold spots at
injectors, column-switching devices, and detectors. He mentioned
center tap technology as a key design for heating the
subsystems of a GC, including detectors, injectors, columns,
and column switching.
Temperature programming inevitably entails trouble with
leaks in the hot zone of the GC. What can be done? Stan
responded with a description of a press fit connector made
from gold-plated nickel that is rated at 70,000 psi. This enables
quick, reliable, and robust connection of fused-silica tubing for
various applications.
Based on his experience at Dow, Dr. Luong pointed out that
the problems drive the solution, especially in mature market
segments. Chromatography is still the best tool. Dr. Janssen
commented that LC is now easier than GC, but both require
continuous improvements in technology to meet market needs.
Further, Dr. Janssen pointed out that despite that, the vast
majority of critical analyses are conducted using well-known,
mature techniques. In contrast, the emphasis of research in gas
chromatography is aimed at areas other than practical.
At this point, I noticed that the discussion tipped from an academic
recitation of technical needs and possible solutions to a session
driven primarily by frustrations. Even today, the instruments
are often more sophisticated than the average user, whether
he/she is a technician, graduate student, scientist, or principal
investigator using chromatography as part of the project.
Who is responsible for generating good data? Can the designs be
improved to increase data integrity?
If this is a problem with GC, I flashed back to a quote from Prof.
Colin Pool cited by Dr. Luong in his opening statement: “For any
problem that can be solved by gas chromatography, I see no need
to use any other technique but gas chromatography. For those
that cannot, that is unfortunate, but this is the basic reason why
we have, and need, a family of separations techniques.”
The next-generation GCs should address these concerns to
improve performance and reduce the cost to society, because we
need reliable numbers, quickly and economically.
Reference
-
Majors, R.E. LC·GC Int. 1989, 2(12), 13–15.
Dr. Stevenson is Editor of Separation Science, American Laboratory/Labcompare;
e-mail: [email protected]. Dr. Gras is Associate Analytical
Manager, Dow Chemical Co., Fort Saskatchewan, Alberta, Canada. Dr. Lee
is Professor of Chemistry, Brigham Young University, Provo, UT, U.S.A.