In many laboratories across a wide range of disciplines,
removal of solvent from dissolved sample is a
routine, daily procedure. The majority of the methods
employed to remove the solvent rely on the use
of vacuum to achieve low-temperature boiling, normally
to prevent damage to a temperature-sensitive
sample. This article demonstrates the importance of
paying sufficient attention to closely monitoring the
drying process and presents solutions to save time
and prevent sample loss.
Vacuum-assisted evaporators (i.e., rotary evaporator, centrifugal evaporator, vortex evaporator, or traditional
freeze dryer [or lyophilizer]) rely on boiling the
solvents away at low temperature. Low-temperature
boiling is achieved by pulling a vacuum on the sample
and the boiling point of the solvent decreases proportionally
to the pressure in the system (Figure 1).
The pressure in the system controls the boiling point
and therefore the temperature of the sample regardless
of the temperature of the evaporator water bath
or sample holders. In the case of the freeze dryer, a
high level of vacuum is used so that the solvents
begin to boil below their freezing point, causing the
sample to freeze; thereafter the solvents sublime until
dryness is achieved.
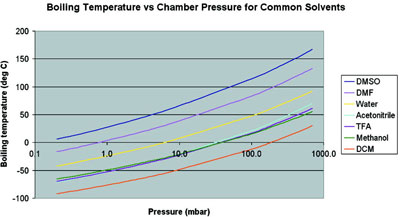
Figure 1 - Plot of boiling point versus pressure for some common solvents.
It can be seen from Figure 1 that to achieve low-temperature
boiling of high-boiling-point solvents (e.g., dimethyl sulfoxide [DMSO] or dimethyl formamide
[DMF]) better levels of vacuum need to
be achieved. Methanol may be boiled at –200 °C
using a pressure of 11 mbar. However, boiling
DMF at –20 °C would require a pressure of 0.15
mbar, which might be achievable, although with a
typical vacuum pump it is not possible to boil
DMSO at anything below about +6 °C (even
though it freezes at +18 °C).
Factors affecting speed of evaporation
Once a sufficient level of vacuum is achieved
to cause the solvent to boil, there are two
principal factors that affect the speed of evaporation—the specific latent heat of
vaporization of the solvent and the effect of
the dissolved sample.
The specific latent heat of vaporization of
the solvent is the amount of heat energy that
is required to boil one unit of a solvent.
DMSO has a relatively low heat of vaporization
(603 J/mL), whereas methanol requires
923 J/mL, and water, a massive 2441 J/mL.
Therefore, water takes more heat energy
than DMSO or methanol to boil and thus the samples
will normally take longer to dry.
The effect the dissolved sample has on the boiling
point of the solvent is highly variable. Some have
little or no effect; others have a massive effect.
The best known example is the use of common
salt on the roads in winter. Sodium chloride dissolved
in water boosts the boiling point but, more
importantly, as in this example, drops the freezing
point of water to approximately –15 °C. The problem
for most laboratories in assessing the likely
impact of these factors is the nature of their work
is such that different and often unknown samples
are processed each day.
Improving throughput
Efficiency savings are desirable in most laboratories—increases in throughput mean that more
work can be achieved with the same resources,
contributing to savings. While the use of fixed-length
sample drying methods is commonplace,
a notable exception is the rotary evaporator.
Research shows that typical rotary evaporator
users attend the sample during the drying
process to ensure that the operation is trouble
free. However, this is not good use of operator
time when multiple samples need to be dried. In
such circumstances, safe, unattended solvent
evaporation of multiple samples can be achieved
with a system such as the Genevac EZ-2 centrifugal
evaporator (Genevac Ltd., Ipswich,
U.K.) (Figure 2).
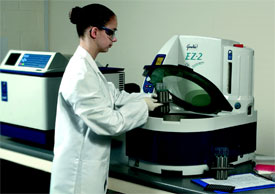
Figure 2 - Genevac EZ-2 centrifugal evaporator for parallel
drying of samples.
The problem with fixed-length drying methods is
that the drying time often varies between solvents
and between samples. Therefore, to ensure that
every sample is dry, users tend to overestimate the
drying time. By automatically stopping the evaporation
process when the samples are dry, the user can
gain significant time savings.
Working with a laboratory that produces libraries of
small molecules and undertakes many drying procedures
daily (drying many different solvents), the
effects on average drying time when switching from
fixed-time methods to the Genevac automatic end-of-method detection software were studied. Despite
the wide range of solvents used, the sample format is
standard across all protocols—up to 6 mL of solvent
in each of 24 vials per sample holder in an HT-12
series 2 evaporator (Genevac). This study was conducted
over two key locations, where the solvent
profiles differed significantly (Figure 3). The change
in average drying times is shown in Table 1. The
reduction in evaporation times achieved was significant
and has contributed to increased throughput
and productivity.
Table
1 - Change in average drying times

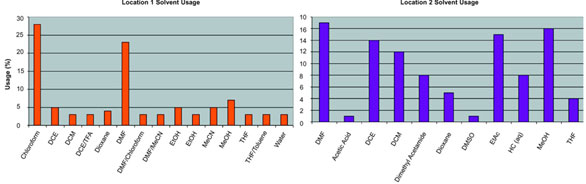
Figure 3 - Profile of solvents used in the two study locations.
Improving yield or reducing sample loss
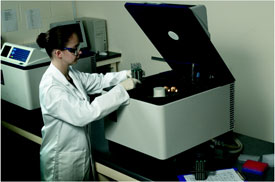
Figure 4 - HT-4X evaporator in Genevac applications laboratory
studying ibuprofen molecular structure.
Most samples can become volatile under the right
conditions. Generally, the smaller the size of a molecule,
the easier it is to volatilize—this is especially
true for organic molecules. A number of Genevac
users have reported that they have observed loss of
sample when the sample is of low molecular weight
(approximately 300 and below) and/or has high
volatility (for example, a straight-chain organic molecule
with few side groups).
Table 3 - Loss of ibuprofen during
evaporation
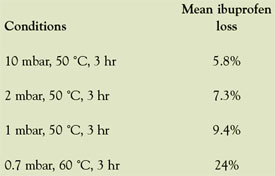
The company has studied the effects of this problem
on the common pharmaceutical ibuprofen in its
applications laboratory using a HT-4X evaporator
(see Figure 4). Ibuprofen has a molecular weight of
203, which is similar to many drug molecules or
intermediates produced in drug discovery chemistry.
However, ibuprofen may be far bigger than typical
molecules studied within metabolism; adsorption,
distribution, metabolism, and excretion (ADME);
drug metabolism and pharmacokinetics (DMPK); or
toxicology groups, which are usually looking for drug
fragments. Another growing area where this effect
may have impact is among the laboratories testing
for drugs of abuse, either as part of routine prisoner,
sports, or workplace screening or within forensic science
laboratories. Table 2 illustrates the molecular
weights of some common recreational and sporting drugs of abuse, demonstrating the potential problem
for testers who might easily use a suboptimal evaporation
protocol resulting in loss of some of the drug
or drug metabolite under investigation.
In the Genevac applications laboratory, dried samples
of ibuprofen were subjected to various levels of
temperature and vacuum and the weight loss of sample
was recorded (Table 3). Extrapolation of these
data to show the potential sample loss is shown in
Table 4 (note assumptions).
Table 4 - Sample losses due to overdrying at compound supply company*
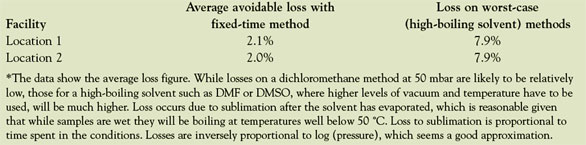
Conclusion
Fixed-length vacuum drying methods are typically
much slower than optimized procedures and, with
lower-molecular-weight organic molecules, may lead
to significant loss of the sample being dried.
Compound loss is commonly due to sublimation of
the dry compound following evaporation of the solvents
in which they were dissolved. Preventing sample
loss can be achieved by limiting the levels of vacuum
and temperature used. However, this may have
a knock-on effect in increasing drying times. Use of
the automatic end-of-run software can help prevent
overdrying and sample losses. In the authors’ case
study, the average evaporation times were reduced by
25% and 28%. In cases in which a laboratory does
not use such a system, it may be appropriate to revalidate
the drying methodology and particularly the
drying times used.
Mr. Griffin is Applications Engineer, and Mr. Darrington is
Business Development Manager, Genevac Ltd., Farthing
Rd., Ipswich IP1 5AP, U.K.; tel.: +44 1473 240000; fax:
+44 1473 742987; e-mail: [email protected].