For manufacturers of solid and/or
particulate products, particle size
is frequently a critical parameter,
and is one of the principal variables
routinely used to characterize their materials.
Finished product performance and
in-process
behavior often correlate with
particle size and/or size distribution, creating
a universal requirement for pertinent
information. Laser diffraction provides a
robust particle sizing solution for many
applications, and has become the technique
of choice in many industrial sectors.
The last decade or so has seen the development
of laser diffraction analyzers that
are increasingly flexible, easier to use, and
highly automated. Many users rely heavily
on such systems—in the laboratory for
development and QC, and in production
facilities for routine process monitoring.
The commercial availability of laser diffraction
technology for off-, at-, in-, or online
implementation enables its efficient use
throughout the product lifecycle.
Understanding the importance of laser diffraction
relies, in the first instance, on recognizing
the relevance of particle size data. This article
discusses how this vital technique continues
to evolve to meet industrial requirements.
Looking at the applications for laser diffraction
in different manufacturing environments,
there is clear commonality in
the reasons for measuring particle size.
Some of the most important aspects of performance
influenced or controlled by particle
size include:
Those designing fuel injection systems
and producing cement exemplify a group
of laser diffraction users who control particle
size to meet a required rate of reaction.
Engine designers control the size to
which fuel is atomized to modify both the
rate and efficiency of combustion; cement
manufacturers mill to a size specification to
control the rate of hydration of the product
during use, since this influences developed
strength. In either case, finer particles/
droplets present a larger specific surface
area and therefore react more quickly than
those having a coarser distribution.
In the pharmaceutical industry, the closely
related issue of dissolution rate is of prime
importance because of its impact on bioavailability.
That said, this is a sector that
routinely manipulates particle size toward
a number of goals: to achieve a stable (nonsettling)
suspension for oral dosage, for
example, or a high respirable fraction for
pulmonary delivery. Detergent and agrochemical
producers share the requirement
to tailor dissolution rate, while ease of inhalation
is frequently an issue for manufacturers
trying to reduce the risk of harm, and
many measure particle size to confirm that a
product cannot be easily inhaled.
Packing density, which is a function of
particle size and distribution, is closely
controlled in many industries to achieve
superior product quality. Those producing
components via mold-filling processes, for
example, from metal or ceramic powders,
manipulate particle size distribution to
achieve an efficient fill with little voidage,
thereby ensuring a strong, flaw-free product
postmelting/sintering. Powder coating
manufacturers similarly optimize size
distribution, aiming for a closely packed
layer of particles that will melt efficiently
at lower temperatures.
Particle packing is also an issue in the
production of suspensions with desirable
rheological behavior. For a given volume
fraction of suspended solids, increasing
polydispersity (the breadth of the particle
size distribution) reduces viscosity—an
effect that can be exploited to increase
the solids loading in, for example, a paint,
or ceramic suspension, without compromising
viscosity. The tendency of a
suspension to settle, or an emulsion to
coalesce, can also be modified through
efficient particle size control—smaller
particles, or droplets being less prone to
either phenomenon.
Finally, although many control particle
size for technical reasons, for others it is
customer perception that is the driving
force. With consumer products, food
being the prime example, particle size can
influence our enjoyment or perception of
quality, both of which are valuable commodities.
The particle size of coffee, for
example, impacts the flavor released during
brewing, while a fine particle size in
chocolate imparts a smooth mouth feel
that is superior to a grainy finish.
The preceding exploration of the links
between particle size and performance is far
from exhaustive, and not all of these requirements
are met by laser diffraction alone. The technique does, however, have several key
attributes that confer substantial appeal:
- Flexibility (ability to measure emulsions,
suspensions, dry powders, and sprays)
- Broad measurement range
- Speed of data acquisition
- Automated measurement
- Nondestructiveness.
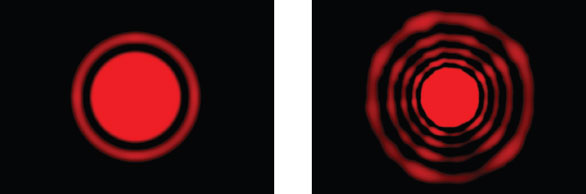
Figure 1- Examples of diffraction patterns caused by light scattering from a particulate sample.
Laser diffraction is an ensemble
technique, generating a single
result for the whole sample rather
than building up a size distribution
from measurements of individual
particles. A sample passing
through a collimated laser beam
scatters light over a range of angles
(see Figure 1). Large particles
result in a high scattering intensity
at relatively narrow angles to
the incident beam, while smaller
particles produce a lower intensity
signal at much wider angles. Laser
diffraction analyzers determine
particle size from the recorded
angular dependence of the intensity
of light scattered by a sample,
using an appropriate theory of light behavior.
The Mie theory is typically applied, as
recommended in the latest version of ISO
133201 (the ISO standard for laser diffraction),
for all particles in the size range over
which laser diffraction is used: 0.1–3000 μm.
The nondestructive nature of laser diffraction
is an inherent advantage of the technique.
Furthermore, because particle size
measurement by laser diffraction relies on the
laws of light behavior, calibration requirements
are minimal. The measurement range
over which the method is applicable is well
matched to many manufacturing applications,
and measurement times are short.
Over and above these attractions, however,
the adoption of laser diffraction has been
driven by instrument manufacturers harnessing
the technique’s intrinsic advantages in
reliable, easy-to-use systems. Developments
over the last 10–15 years have been pivotal.
Evolution of a favored
particle sizing technique
The practical realization of reliable systems
that can deliver across the full measurement
range accessible by laser diffraction
has required significant advances in optical
hardware. Early systems often employed
different lenses to measure over relatively
narrow size ranges. With such systems, the
associated switching of lenses and accompanying
realignment of the instrument
limit flexibility and/or productivity and
are especially disadvantageous when analyzing
samples across a very broad particle
size distribution. Today, improvements in
optical design have largely eliminated the
need for multilens systems, although they
remain in use: Their functionality is less
of an issue for anyone routinely measuring
closely similar samples within a well defined
size range.
At the same time, optical improvements
have delivered significantly enhanced resolution.
In simple terms, the precision of
particle size measurement relies not only
on detecting particles at either extreme
of the distribution, but also on accurately
resolving the population into size fractions.
This is an area of performance in
which even the most modern laser diffraction
analyzers vary considerably. Poor
resolving capability compromises the generation
of a reliable particle size distribution,
and the ability to accurately quantify,
for example, the amount of fines or coarse
particles present in a sample.