The modern manual pipet has been a laboratory
workhorse for several decades, providing researchers
with a convenient tool to transfer liquids from one
vessel to another with high levels of confidence in
the reproducible precision of the associated volume.
Development of the fundamental technology has
included an expansion of the available volume to
cover sample volume ranges from 0.1 μL to 20 mL;
in parallel there has been the introduction of multichannel
versions for higher-throughput requirements.
During the technology development process,
it was recognized that pipetting had become such a
well-used laboratory tool that continuous use of the manual pipet was likely to place a strain on the muscles,
tendons, and ligaments of the hands and wrists
of each researcher. In fact, many researchers literally
suffered for their work.
Ergonomics and pipets
Enter the era of ergonomic pipet development, a
period of designing the pipet to enable the researcher
hours of use without the risk of repetitive strain
injury (RSI). All parts of the pipet were assessed for
their contribution to the loads associated with RSI,
including tip-ejection forces and plunger forces associated
with the various steps involved in pipetting.
Careful design of the plunger/springs and micrometer
were critical to maintaining precision and reducing
forces associated with the aspirate, dispense, and blow-out steps. Alternative mechanisms for moving
the plunger and piston were developed for the
first electronic pipet, removing any requirement for
manually pushing a plunger. Researchers could now
choose between a manual pipet and an electronic system that could be programmed to automatically
perform multiple pipetting steps.
Manual pipets have continued to be popular systems
of choice due to their lower cost and the ultimate
control that the user has in choosing how to manually
push the plunger down. Manual systems, however,
lack any form of feedback in terms of exactly
where the plunger is positioned and hence the actual
volume being aspirated or dispensed.
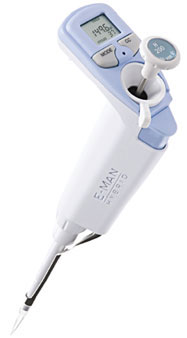
Figure 1 - E-Man Hybrid Pipet.
The E-Man Hybrid Pipet (Figure 1) (Rainin Instrument,
LLC, Oakland, CA) represents an important
step in manual pipet development in that it retains
the control and feel of a traditional, ergonomic manual
pipet with the additional advantage of being able
to determine the exact position of the plunger and
display this to the user. This technology (real-time
position sensing) enables an LCD to display, in real
time, the volume that is being aspirated or dispensed
by the pipet.
Real-time position sensing is a well-known technology
associated with many industrial systems. Common
industrial applications include control systems,
robotics, machine tools, and measurement equipment.
Besides industrial applications, position sensing
is often used in automotive steering, braking, and
throttle systems.
In many laboratories, equipment position sensing
can often be found in pump systems and in the
positioning mechanisms of larger liquid handling robot systems.
In the E-Man Hybrid Pipet, the real-time positioning
sensor is used to monitor the precise position of
the piston, and therefore the plunger. The position
of the plunger/piston, which relates directly to an
associated liquid volume, can be displayed directly
on the LCD. Current manual pipets with electronic
readouts only monitor the position of the upper
stop but cannot tell the user where the plunger (or
piston) is positioned.
This real-time sensing of the piston/plunger in the
E-Man Hybrid gives rise to a number of features that
currently have been unavailable in manual pipets.
- The pipet can display the amount of liquid being aspirated into the pipet tip, or it can display the amount of liquid being dispelled from the tip. For the first time, the user of a manual pipet can perform tasks such as titrating, diluting, multidispensing, and measuring an unknown amount of liquid.
- The E-Man Hybrid can determine whether acceptable pipet technique is being used by sensing whether a sample has been blown out correctly or if plunger movement is too rapid. This can be very beneficial for teaching new users.
- With electronic memory, the pipet can alert the user to when the next scheduled service is due, providing a unique GLP function in a manual pipet.
- The real-time sensing in the pipet allows multiple offsets to be placed into the calibration curve (like Rainin E1 and E3 electronic pipets) as opposed to a single offset in standard manual pipets. This optimizes the performance of the pipet.
- The user calibration feature also allows correction at more than a single point; up to 50 points can be entered.
- The real-time sensing in the pipet permits a real pipet cycle counter to be used. The cycle counter does not simply count plunger depressions, but only counts a pipetting cycle if it is a complete pipet cycle; mixing, etc., will not cause false cycles.
The E-Man Hybrid, by employing novel technology
within a familiar ergonomic manual pipet, brings
new capabilities for today’s scientists that will set the
standard for tomorrow’s research.
Mr. Petrek is CTO, Rainin Instrument, LLC, 7500 Edgewater
Dr., P.O. Box 2160, Oakland, CA 94621-0060,
U.S.A.; tel: 510-564-1600; fax: 510-564-1617; e-mail:
[email protected].