Safe solvent management and
storage are significant concerns
in the pharmaceutical industry,
particularly when purification
systems are run unattended and are
supplied by large volumes of organic
solvent. By the nature of the design of
such systems, there is the risk of continuously
pumping solvent in excess of
solvent waste container capacity due
to unanticipated error states, which in
turn results in overflow of solvent onto
instrument/laboratory benches or onto
the floor of the laboratory. To mitigate
the risks of possible spills involving
flammable or other hazardous liquids
utilized by unattended automated analytical
instruments, a Liquid Overflow
Prevention System (L.O.P.S.) safety
device was designed and deployed on
several instruments at Lexicon Pharmaceuticals
in Princeton, NJ.
Lexicon Pharmaceuticals, a biopharmaceutical
company located in The
Woodlands, TX, and Princeton, NJ,
discovers and develops treatments for
human disease using proprietary gene
knockout technology. This technology
has led to novel drug targets and turned
into multiple drug candidates currently
progressing through human clinical trials,
including treatments for irritable bowel
syndrome, carcinoid syndrome, rheumatoid
arthritis, and diabetes.
At the Princeton site, medicinal and process
chemistry groups work to discover
and develop drug candidates targeted to
unmet medical needs. Chemists utilize
open-access analytical instrumentation
to perform reaction monitoring as well as
purification and characterization of their
compounds. This environment allows
chemists to perform “walk-up” experiments
on analytical instruments employing HPLC, LC-MS, NMR (nuclear magnetic resonance), IR (infrared) spectroscopy, DSC (differential scanning calorimetry), TGA (thermogravimetric analysis), PXRD (powder X-ray diffraction),
and automated flash chromatography techniques,
rather than submitting samples to
the analytical chemistry team. This policy
allows experiments to be performed rapidly,
and experimental results to become
immediately available.
A significant part of the chemistry work
flow includes flash chromatography
for purification of final and intermediate
compounds. Flash chromatography
consists of solid stationary phase media
(often silica) packed into a cylinder
(column). Sample is loaded on top of
the media, and mobile phase solvents
(typically hexane, ethyl acetate, dichloromethane,
and/or methanol) are then
pumped onto and forced through the stationary
phase, washing the sample along
with it in order to obtain physical separation
of the desired compounds from
impurities and collect them as they elute
from the column. Several automated flash chromatography systems are commercially
available. These automated
systems allow chemists to mechanically pump solvent gradients over flash
columns with minimal supervision.
The Princeton facility has four automated
flash chromatography instruments
set up in two workstations
with two instruments per workstation.
These instruments, which utilize
positive displacement piston pumps,
are capable of two separate binary
solvent systems. In order to provide
ample solvent efficiently to two systems
per workstation, 56-L containers
of each of the four solvents were
selected, rather than using 4-L glass
bottles, which would require frequent
replenishment since the instruments
can each consume up to 100 mL/min
of a given solvent.
The 56-L Stainless Steel Pressure Dispense
System (SSPDS) solvent containers
currently used in the facility
are provided by Honeywell Burdick &
Jackson (Muskegon, MI) and deliver
high-purity solvents in a safe, environmentally
responsible, and convenient
package that ensures product stability
over time. These features are accomplished
by utilizing inert materials of
construction, safety devices meeting
NFPA30 requirements, and inert gas
pressurization to eliminate oxygen, which
would degrade the solvents. Additionally,
there are no packing materials associated
with shipping these containers, helping to
eliminate disposal costs.
Due to the quantity and hazardous nature
of the solvents being used, safety precautions
have been engineered into the physical
configuration of these workstations; the
instruments and all containers are electrically
grounded to prevent sparking due to
static buildup, and containers are kept in a
separate, highly ventilated “solvent room.”
The instrument waste containers are all
ventilated and are themselves housed in
secondary containment.
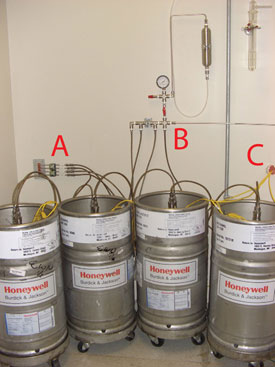
Figure 1 - SSPDS in an adjacent laboratory are plumbed
through the wall (A), supplied with a constant nitrogen blanket
(B), and have their solvent levels monitored remotely (C).
The SSPDS reservoirs are stored in rooms adjacent to the analytical
laboratories where the automated flash instruments are located that
meet Class I, Division II requirements, enabling storage of over 200
L of flammable solvent. Nitrogen is fed over the solvents within the
SSPDS and out through a silicon oil bubbler. This configuration prevents
the generation of either a vacuum or high pressure within the
SSPDS, regardless of whether the instrument is withdrawing solvent
or not. This constant nitrogen blanket also prevents the solvents
from being exposed to atmosphere during use (Figure 1).
These solvents are pumped by each instrument through the walls
of the storage room into the adjacent laboratories through stainless
steel tubing to feed the two instruments stationed there.
Downstream of the pumps, the solvents move through a disposable
flash column, a detector, and into a Factory Mutual (FM)-approved safety waste container utilizing stainless steel quick-disconnects
and laboratory system ventilation. On this system, if
the waste container overfills, the resulting liquid waste overflow
is channeled into the waste container’s secondary containment.
The application of four 56-L solvent reservoir containers connected to
two instruments, with a 20-L waste container per instrument, allows
for the possibility of overflow of both the waste container and its associated
secondary containment. An overflow or waste container leak
could create a hazardous environment that requires laboratory evacuation/isolation and emergency response. This risk can be reduced by
using larger waste containers (and associated secondary containment)
or smaller solvent reservoirs, or redesigning the system.
Decreasing the volume of solvent reservoirs would increase the
frequency of instrument solvent replenishment. More frequent
changing of solvent reservoirs would increase instrument down time
(decreasing overall laboratory efficiency) and reserve container storage
(removing space-saving and cost advantages provided by the
SSPDS). Both points are considered suboptimal for the facility’s
open-access environment. Increasing the volume of the waste containers
would become problematic for waste management, effectively
increasing satellite waste accumulation beyond the allowable limits
set forth in 40 CFR 262.34(c). In addition, this solution increases
the footprint required for the waste containers within the laboratory,
congesting areas frequented by users of these instruments.