The
volume of HPLC mobile phase
(MP) purchased and discarded each year
is about 20,000,000 L, or enough to fill
two rail trains each with 100 tank cars.
On average, each of the 200,000 active
HPLCs pump about 2 L of MP per week.
QC instruments pump 10 L each. The
purchase cost for solvents is about $20/L.
Disposability, assuming it is done properly,
adds at least $30/L for a total of
$50/L. Thus, the total cost to the global
society of mobile phase for HPLC is one
billion dollars. If the MP is prepared
manually, as is often the case, then a few
hours of labor, including QC time and
overhead, can be added to the $50/L.
This is a significant amount of money,
especially in facilities with many HPLCs.
On a per-instrument basis, an instrument
that runs for one shift per day uses
about 125 L per year for a cost of
$6000/yr. An instrument in QC running
24/7 is about 500 L for an annual cost of
$24,000. Recycling of the MP reduces
these costs by 50–90%. Plus, recycling
reduces the environmental burden. It is
in the interest of all to reduce the burden,
but firms such as contract analytical
laboratories and column manufacturers
need to worry about being classified as
contributors. Should a problem arise at a
disposal site, all contributors can be held
financially responsible, although typically
the minor players bear much less of
the financial responsibility.
Development of MP
recycling
MP recycling has been used almost since
the beginning of HPLC, particularly for isocratic separations, which account for
about half the assays performed. The trail
was blazed by the process analyzers developed
by firms such as Applied Automation
(Bartlesville, OK), which reduced
the net mobile phase consumed by
returning the column effluent to the
pump reservoir. Samples were seldom
larger than a few micrograms, which were
diluted in at least 500 mL (~500 g) of MP
for an increase in concentration of impurities
of a few ppb/sample. It took many
injections to have any measurable effect
of the recycling of the mobile phase.
In the laboratories, the trend was to place
the column out in the ambient air. Any
small changes were obscured by other factors,
including uncontrolled variations in
column temperature. MP recycling was frequently
used for instruments left running
over weekends to reduce the downtime
associated with start-up and shut-down.
Some manufacturers advised users to never
turn off the pump, except for repairs.
Total recycling works provided the concentration
of the analytes in the sample is
much higher in detector response than the
background signal from the contaminated
mobile phase. However, in total recycling,
the recycled analyte will slowly accumulate
in the MP. With concentration-sensitive
detectors such as UV-VIS, RI (refractive index), and fluorescence, the first clue
to excessive accumulation will be mysterious
peaks (often negative) that arise from
the vacancy effect.1 In fact, if the concentration
of analytes in the sample is equal to
the concentration in the MP, no signal is
detected. To avoid these problems, total
recycling is rarely used today. Sometimes,
however, it is still employed for instruments
that cannot be shut down.
First-generation MP
recyclers
As automation improved in HPLC, MP
recyclers appeared and were adopted
when the instrument was sufficiently useful.
These split the column effluent
between waste and recovered eluent that
is free from the sample. The first products
(ca. 1970) used timers that relied on the
run-to-run reproducibility of retention
time windows. While time-based control
can work well in many applications, retention
time can vary for many reasons,
including changes in column temperature,
partial failure of pump seals, column plugging,
as well as stripping of the volatile
components due to helium sparging. To
prevent contamination of the recycled
mobile phase by the sample, the window
for elution of the peak needed to be about
±15% wider than the peak width at baseline.
This was a wide window for long
runs, which reduced the potential savings.
Second generation
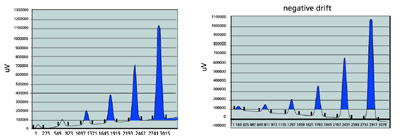
Figure 1 - Threshold detection for recycling of mobile phase. The large peaks exceed the threshold
level and are routed to waste. The remainder is recycled to the MP reservoir. Small peaks may not be
detected since they are below the threshold. Lowering the threshold can cause problems when the
baseline drifts. Drift higher than the threshold routes all MP to waste. Drift down from the threshold
increases the risk of not detecting peaks, which ultimately contaminates the recycled MP.
Second-generation mobile phase recyclers
generally employed threshold peak sensing (Figure 1). These recyclers
often successfully recovered most of the
pure mobile phase. However, for some
samples, the threshold could not be set
low enough to see small peaks without
getting lost when the baseline drifted.
If the threshold was too high, then peak
detection was delayed. Upon each injection,
the delay in detection sent a small
fraction of the leading edge of the large
peaks back to the reservoir. In addition,
small peaks were not detected. If the
threshold was too low, the savings was
never realized since the recycling valve
never reset. This was probably the worst
outcome of all since the reservoir was
rapidly depleted, terminating the run
sequence. Many found the anticipated savings
difficult to achieve in practice. Others
were frustrated with the awkward controls
required by the transistor-transistor logic
(TTL) implementation of the controls.
Third generation
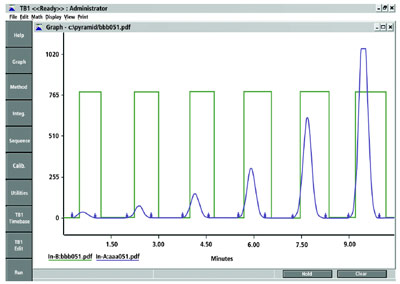
Figure 2 - Chromatogram showing the placement of valve actuation for recycling of pure mobile
phase. The tick marks at the beginning of the peak indicate peak detection. The ticks on the trailing
edge show the peak end by returning to baseline. The square trace shows the actual operation of the
recycle valve (waste is high; recycle is low). Note the valve actuation is delayed by 10 sec, which is
the transit time from the detector to the recycle valve. Peak detection and valve delay are used to
optimize the MP recycler to the particular separation.
A few years later, TTL electronics began to
be replaced by microprocessors, and
sophisticated, well-proven peak detection
algorithms became available from the digital
integrators. Threshold setting was
replaced by simple input of the width of
the widest peak. A segment of a chromatogram
obtained by injecting increasing
aliquots of a single component sample is
shown in Figure 2. The tick marks in the
chromatogram show the actuation of the
recycle valve superimposed on the detector
output. The marks are so narrow that they
are rejected by the data station as noise.
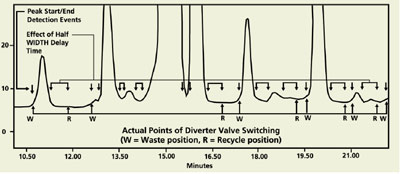
Figure 3 - Illustration of peak detection used to select segments of the chromatogram suitable for
recycling the mobile phase. To ensure that the material from tailing peaks is not recycled, the program
uses a user-selectable RTB delay (see text).
The microprocessor enables the rapid
detection of peaks and baseline in real
time, as shown in Figure 3. Note the presence
of several small peaks between some
that are large to very large. Also, the peak
shapes are not ideal. To compensate for
nonideal shapes, the algorithm, as incorporated
in the SolventTrak mobile phase
recycler (Axxiom Chromatography,
Moorpark, CA), permits the user to
select a return-to-baseline (RTB) delay
time to make sure that the baseline is
really achieved. Typically, the RTB delay
is set at half the peak width.
This works as follows. At about 10.5
min, a peak is sensed and the valve is
diverted to waste. The peak end is
detected at about 11.25 min, but the
valve is not returned to recycle until
almost 12.0 min because of the RTB
delay. This RTB delay for a well-shaped
peak provides added assurance
that only pure mobile phase is
returned to the reservoir.
A small peak is detected at about 13
min. The peak slope detector shows
peak end about 1⁄4 min later. However,
before the RTB period expires, a new
peak is detected. This also happens at
approx. 13.6, 14.0, and 15.75 min. The
valve is set for recovery at about 17 min.
The scenario is similar for the next two
peaks—a peak is sensed at around 17.5
min, and the peak end is around 17.9
min, but before the RTD timed out, a
new peak was sensed at 18.5 min, etc.
One can argue that little MP is recovered
in a busy chromatogram such as Figure 3.
This is true, but many, perhaps most,
chromatograms are not so busy. This particular
segment of a chromatogram was
chosen to illustrate how the RTD works.
In practice, most HPLCs run simple samples
with high resolution, plus these are
often waiting for a sample to be injected.
For example, QC laboratories often dedicate
one instrument to a particular analysis.
The instrument waits on recycle until
a sample is ready for a stat analysis. After
the run is complete, baseline is sensed and
it returns to recycle and waits for the next
sample, which might be hours later. In
this case, the savings is obvious and large
(often over 90%), which corresponds to
tens of thousands of dollars per year.
Regulatory compliance
Method validation often includes
requirements for fault detection. The
microprocessor supporting memory and
bi-directional communication of the SolventTrak
facilitates recoding and reporting
of the valve status for each run. With
this, one can go back and examine the
trail to ensure that the problem is correctly
diagnosed and solved.
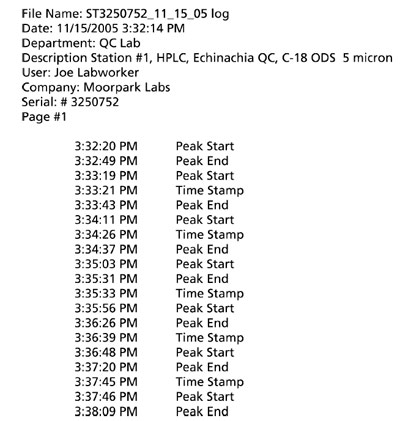
Figure 4 - Typical event table showing the time of changing the valve position. This can be useful
in the initial setup of the MP recycler or troubleshooting.
The SolventTrak has built-in capability to
send peak detection and fault activity
information to a PC program in order to
produce a log file for future audit needs.
The SolventTrak system will include a
free logging program in the future. Figure 4
depicts an example of a log file report. The
log file will contain events such as peak
start and end times, periodic time stamps,
communications problems, and operator
intervention. Logging will be automatic
and require no user intervention. These
log files should serve to demonstrate that the system has been doing its job of peak
detection and recycling from day to day.
Economic justification
MP recovery is usually justified on the
basis of saving money. One study
shows a savings of 88–96% of MP and
a dollar savings of 81% (~$1000/yr).2 The potential savings is greatest when
an instrument has a low number of
peaks per hour or day, either due to
very simple chromatograms or low
sample load, or both.
Even though samples may be infrequently
injected, expediency dictates that the systems
be running continuously (i.e., in
“ready” mode) so that the operator need
only make the injection and read the
response. In these situations, solvent recyclers
reduce the cost of MP by more than
90% since the real run time may be only
an hour per day. Thus, the recycler monitors
the mobile phase and conserves it
between samples. At 1 mL/min, the percent
savings is at least the waiting time
per day in minutes/1440. Additionally, if
the chromatograms provide only a peak
or two, the recycler will recover the baseline
regions as well.
The benefits of MP recycling can be calculated
by creating a simple spreadsheet
and comparing the operation with and
without MP recycling. In many cases the
instrument pays for itself in a few months.
Some fear that recycling will be too much
trouble. However, chromatographers are
generally accustomed to using similar
algorithms in setting up the automated
integration to prepare a report. The first
time it may take an hour or two. The second
setup will require much less time.
Environmental justification
The environmental justification involves
tangible cost savings, risk reduction, and
intangibles, including reputation of the
firm, management, and employees. Reputation
is an intangible, but it can be
evaluated by the cost of replacement
when the reputation is damaged. A
major problem can decrease the market
capitalization of a firm by 20–50%, sometimes
more. Also, firms seek to compete
for human talent on the basis of being a
good place to work. Acting responsibly is
one of the qualities often cited in ranking
potential employers.3
On the tangible side, reducing the waste
burden for the solvent directly reduces
expense for disposal, which is more than
half the estimated cost of ownership,
including disposal, of about $50/L. In
smaller firms, particularly ones that use
many HPLCs, such as contract laboratories,
risk is classified by the level of output.
Automated cleaning
Over the last decade, the automation of HPLC instruments has improved dramatically,
unattended operation is routine,
and 24/7 operation is relatively common.
System suitability tests can trigger column
regeneration routines or purge prior to
shutdown. The SolventTrak can take
over and switch a second valve to provide
a second mobile phase to the pump for
purging and column cleanup. After the
cycle is completed, the SolventTrak signals
completion with a contact closure
during the cleanup cycle, and all column
effluent is sent to waste.
When not to use an MP
recycler
MP recyclers make the most sense for isocratic
separations, but not all of them. Separations
with small baseline periods are not
good candidates. This is especially true for ion chromatography and steric exclusion
chromatography (SEC). SEC has a very
limited elution window, essential up to a K′
of 1 or a little more for the trailing peaks.
Ion chromatography with suppression
essentially destroys the mobile phase chemically
to improve detection. Recovery
makes no sense. Plus, the chromatograms
are generally very busy, with a very low percentage
of the total run time spent on baseline.
However, in the case of Reagent- Free™ IC (RFIC™), as developed by
Dionex (Sunnyvale, CA), baseline segments
of the column effluent may be pure
enough to recycle, even if a gradient is used.
Of course, even SEC is an attractive
candidate if there are long periods
between injections. In contrast, chiral
separations often consist of only
two peaks, plus the injection peak.
Further, the MP can be expensive if
a chiral selector has been added.
Column diameter has an effect. Capillary columns do not use sufficient MP
to justify cost reduction, but preparative purification with large-diameter
columns is probably the other extreme.
Gradient separations are generally not
suitable for MP recycling, unless the
wait between runs is long. Recovery of
mobile phase from gradient runs
involves more effort, but spinning band
distillation can recover more than a
liter per hour of organic solvent, including
methanol. Recovery of ethanol or
acetonitrile is a bit more complicated
since these form azeotropes with water.
References
- Abreu, O.; Lawrence, G.D. Analytical
reliability of mobile-phase recycling
in liquid chromatography. Anal.
Chem.2000, 72(8), 1749–53.
- Sheth, R.O. Closed loop recycling of
solvents used in high pressure liquid
chromatography (HPLC) analysis. www.denix.osd.mil/denix/Public/ Library/PRO97/709hplc.html.
- Gwynne, P. Top employer survey. Science
2005, 309, 2242–50.
Mr. Welch is Vice President, Director of
Product Development, Axxiom Chromatography,
11968 Challenger Ct., Moorpark,
CA 93021, U.S.A.; tel.: 805-523-
8888; fax: 805-523-7900; e-mail: [email protected].