Thermogravimetric analysis (TGA) is an established technique for
studying the thermal stability of
materials and for determining and
understanding their decomposition
profiles. While standard operating
conditions (10–15 mg samples ;
10–40 °C/min heating rates) are
commonly used, a growing need
exists for more advanced capability.
In biological and pharmaceutical
studies, analysts are increasingly
faced with trying to determine trace
materials (e.g., 1–5% of volatiles)
in 1–2 mg samples, which are difficult
or costly to prepare. This is
usually difficult or impossible with
current instruments. Many analysts
want improved laboratory productivity,
while others seek very high
heating rates for more specialized
analysis, such as studying energetic
materials . Naturally, all desire
advances in software and operational
convenience. Accommodating
these diverse needs in a single
instrument presents significant
technical challenges.
Design criteria
The ability to routinely detect very
small weight changes in TGA
requires minimizing baseline drift
and ensuring that it is reproducible
over the temperature range of the
experiment. Of the factors contributing
to TGA baseline drift,
the most critical is maintaining
good temperature control in the
balance chamber.
For decades, thermogravimetric analyzers
have employed resistance
wound furnaces, since they deliver
the stable and reproducible heating
rates (1–40 °C/min) required for quantitative weight change measurements.
However, their mass or other
design constraints have limited their
ability to provide significantly higher
heating rates without extensive temperature
overshoot. Clearly, a new
style of heating is needed to meet the
latest and diverse technical challenges.
In addition, improvements in
automatic sample processing, control,
and data analysis software, as well as
innovative user convenience features,
have also been requirements of a
next-generation, research performance
TGA as commonly requested
by users. These criteria are well met
by the Q5000 IR (TA Instruments,
New Castle, DE) (Figure 1).
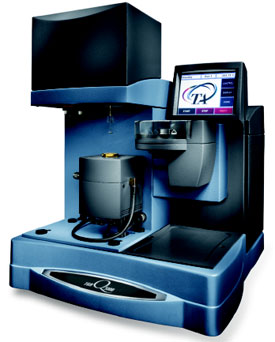
Figure 1 - Q5000 IR TGA.
Instrumentation
In this TGA, the electrically
grounded balance mechanism is
housed in a well-insulated, gas-purged,
temperature-controlled chamber, which is isolated from the
furnace. The furnace uses infrared
heating and delivers not only the heating rate accuracy and precision
needed for optimal analytical performance,
but also linear heating to
500 °C/min for rapid analysis, and
ballistic rates in excess of 2000
°C/min for specialty applications.
The furnace includes an integrated
electromagnetic coil that simplifies
Curie point temperature calibration.
The autosampler can process up to
25 samples in platinum, ceramic,
quartz, or aluminum pans in a
sequential or random manner. The furnace can be readily coupled to a mass spectrometer.
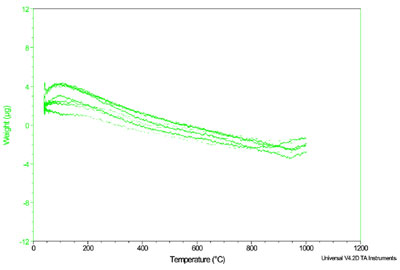
Figure 2 - Q5000 IR empty pan dynamic baselines.
Discussion
Baseline flatness
The Q5000 IR design has been found
to deliver extremely low levels of
baseline drift, due mainly to improvements
in balance chamber temperature
control. Proof of this has been
demonstrated in heating ramp experiments from ambient to 1200 °C,
where the chamber temperature varied
by less than 0.005 °C. Figure 2
shows an overlay of eight repeat
dynamic baselines performed at 20
°C/min from 40 to 1000 °C using
empty platinum pans. The raw data
indicate a worst-case drift of only 6 μg
over the temperature range and
demonstrate very good repeatability.
This level of baseline flatness is nearly
an order of magnitude improvement
in the state-of-the-art and makes practical
the detection of low or submicrogram
weight changes.
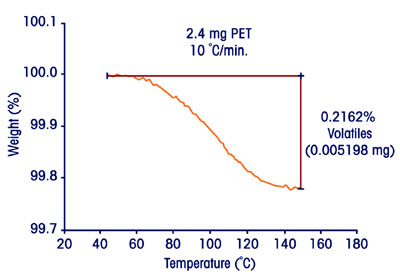
Figure 3 - High-sensitivity analysis of volatiles in a small sample.
Sensitivity for low-level weight change detection
The presence of unexpected volatiles
can be a problem in the production
and use of resin systems. When a plastic
formulation contains even small
amounts of water, solvent, or
monomer, it may produce bubbles or
imperfections during processing. Figure
3 depicts a high-sensitivity moisture
determination in a 2.4-mg sample
of polyethylene terephthalate (PET)
bottle-stock. The raw data show evidence
of 5.2 μg (0.21%) of moisture,
and indicate that lower amounts could
easily be detected.1
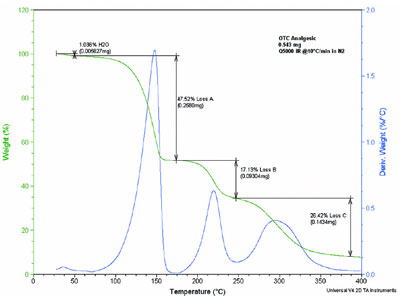
Figure 4 - TGA analysis of an OTC analgesic.
A second good example of sensitivity
and also resolution appears in Figure 4,
an analysis of a commonly used over-the-counter (OTC) analgesic. The
entire tablet (active ingredient,
binder/fillers, and coating) was ground
and a 0.543-mg sample was heated at
10 °C/min from ambient to 400 °C.
Individual analysis of the core tablet
and the outer coating reveals that the
first and third weight losses are from
the core tablet, and the second loss is
due to decomposition of the coating.
Of special note was the detection of
less than 6 μg of adsorbed moisture.
Heating rate reproducibility
An important need in all TGA experiments
is stability and reproducibility
in heating rate. Figure 5 displays a
triplicate analysis of the decomposition
of a proprietary elastomer that
produced a carbon black determination
within 0.1% of the expected
value. The method involved several isothermal and ramp segments, the
latter performed first at 500 °C/min in
nitrogen to decompose the elastomer,
followed in turn by an equilibration
at 330 °C, an automatic gas switch to
air, and finally a second 500 °C/min
ramp to 850 °C. The overlay of three
runs provides strong proof of the stability
and reproducibility of the infrared furnace, even at an elevated
heating rate.
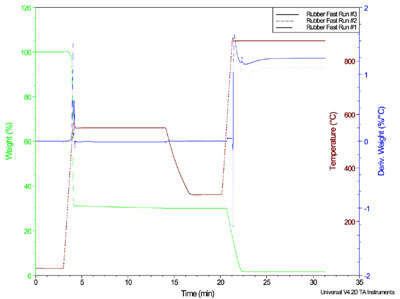
Figure 5 - Accurate and reproducible analysis of carbon black in an elastomer.
Another demonstration of the heating
rate stability and reproducibility from
the infrared furnace has been from the
well-known Detroit Diesel Soot Test.
This involves heating used diesel
engine oil to decomposition, initially
in nitrogen and then in air, to make a
measurement of the remaining “soot.”
Data reproducibility of better than
0.1% has been reported from different
laboratories in this analysis.
Capability for rapid analysis
Figure 6 shows two plots of the
decomposition of a 40% calcium
carbonate-filled polypropylene sample
at heating rates of 40 °C/min
and 500 °C/min, respectively. In the
latter experiment, the analysis time
was reduced (7×) with little or no
loss in resolution. This demonstrates
that the combination of
rapid heating, forced air cooling
(<10 min from 1200 to 50 °C), and
an automatic sample processor can
deliver significantly improved productivity
in routine sample analysis
where the resolution can be maintained
at the higher heating rates.
The furnace’s capability to generate
very high ballistic heating rates
(>2000 °C/min) has drawn high
interest from scientists wishing to
use the TGA to simulate actual
combustion processes (i.e., propellants,
tobacco, pyrotechnics).
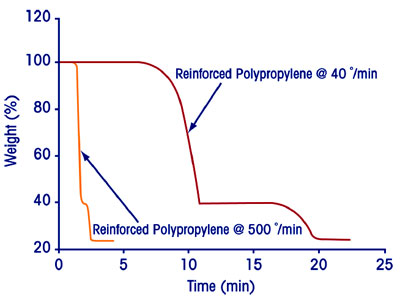
Figure 6 - Rapid TGA analysis.
Automatic sample processing
The capability for automatic sample
processing, analysis, and data reduction
in TGA experiments is a necessity
in busy thermal analysis laboratories.
It permits improved productivity,
minimizes operator error, and releases
staff for other tasks. Time-dependent
integrity of some materials while
awaiting analysis has been an issue
and is addressed in two ways. The first
is the ability to preweigh samples
awaiting analysis and then compare
the value with the weight recorded at
the actual time of analysis. This
allows detection of any sample weight
change while in the autosampler tray.
The second and more comprehensive
solution to the issue of environmentally
sensitive samples is encapsulation
in aluminum pans, which are
opened just prior to analysis. A key
advance in this autosampler is in the
mechanism for opening the sealed
pan. A stainless steel “punch” is used
that does not “pierce” the lid and thus avoids contact with the sample. This
eliminates the possibility of cross-contamination
of other samples
awaiting analysis.
Good laboratory efficiency requires
that the instrumentation be maintained
properly calibrated and ready
for use. This takes time and is often
postponed. A solution is now available
in which the autosampler and
Advantage software (TA Instruments)
combine in a way that automatically
ensures the operational
readiness of the analyzer. This allows
the user to schedule key performance
tests such as weight and temperature
calibration, verification, and system
diagnostics on the TGA and automatically
receive post-test notification
of the results by e-mail.2 Further
test sequences can be automatically
performed based upon the data
obtained. These operations can be
scheduled at quiescent periods, such
as overnight or on weekends. In
addition, a separate software program
permits the analyzer to assist
the user in complying with the U.S.
FDA regulations as specified in Document
21 CFR 11.
Summary
The above design features and many others
permit the Q5000 IR to set new standards
in performance and user convenience
in thermogravimetric analysis.
References
- Determining Volatiles in Polyethylene Terephthalate Using the Q5000 IR Thermogravimetric Analyzer. TA Instruments Applications Brief (TA326), 2005.
- Q5000 IR Features to Ensure and Maintain Optimum TGA Performance. TA Instruments Applications Brief (TA 327), 2005.
Dr. Dallas is Product Specialist, Thermal Products
Group, TA Instruments, 109 Lukens
Dr., New Castle, DE 19720, U.S.A.; tel.:
302-427-4000; fax: 302-427-4001; e-mail:
[email protected].