Analytical
chemists have long known
that closed-vessel microwave sample
preparation techniques are the most
reliable way to achieve high-quality
digestions—i.e., clear, precipitate-free
solutions with minimal dilution, no loss
of volatile analytes, and no contamination.
However, as with all things, there
are limits to the technology’s capability
The limits of today’s conventional microwave digestion systems are due to
the available reaction vessels (Figure 1).
The vessels used in these systems are made
from various microwave-transparent
materials, such as engineered plastics, and
are shaped in ways appropriate to the temperature,
pressure, and volume requirements
of particular applications. Due to
their limited mechanical strength and
temperature resistance, these vessels naturally
impose limits on the parameters of a
sample digestion procedure, including
temperature, pressure, process duration,
and sample size.
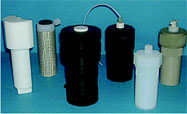
Figure 1 - Typical microwave reaction vessels.
Conventional microwave sample processing
is a mature technology.
Improvements in vessel performance,
or special multiple-vessel configurations
to maximize throughput, can produce
only incremental gains. The state
of the art has reached, if not a plateau,
then an increasingly gentle slope.
Removing the limits
The UltraCLAVE (Figure 2) (Milestone Inc., Shelton, CT) is an entirely
different approach to closed vessel
microwave sample preparation
and is based on high pressure autoclave design. At its
heart is a single large reaction
chamber. In operation, this sample-containing chamber is prepressurized
with inert gas, and
then heated by a microwave
field of uniform intensity. The
pressurized chamber in the system
serves simultaneously as the
microwave cavity and the reaction
vessel.
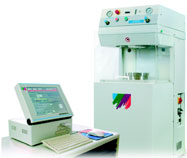
Figure 2 - UltraCLAVE system.
The individual sample containers
are not pressure vessels. This
approach changes the rules of
microwave sample preparation
by removing or greatly extending
the limits associated with
conventional microwave vessels.
Higher temperatures,
higher pressures, larger sample
masses, and greater batch quantities
all become possible. Even
the toughest sample matrices
can be digested by sustained
high temperatures and pressures
along with the correct chemistry.
Chemists can be assured of
identical temperature and pressure
conditions across any number of discrete
samples.
Larger volume
The UltraCLAVE reactor offers a
larger volume than other commercial
single microwave reaction vessels.
While it is not likely to be
a common use of the instrument,
it is possible to process a
single, very large sample in a
fluoropolymer liner fitted to
the entire reaction chamber
(Figure 3). The 3.5-L liner can
safely accommodate up to 25 g
of organic sample for acid
digestions and many times that
sample mass for solvent extraction
applications.
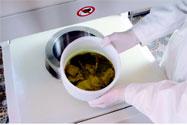
Figure 3 - Fluoropolymer liner for UltraCLAVE
reaction chamber.
Larger batch count
The individual sample containers can
be much simpler in design than in
conventional microwave vessel
assemblies. As a result, a higher batch
count of discrete samples can be
accommodated (Figure 4), and each
individual sample can be of a larger
mass than is possible in a conventional
sealed vessel. Another benefit is
the vastly reduced need for consumable
vessel components.
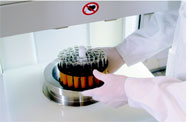
Figure 4 - Large vessel count for high throughput.
In normal operation, the combination of
prepressure nitrogen and partial pressure of
process vapors ensures that boiling never
occurs in individual sample containers.
Loose-fitting covers on each container
prevent loss of sample or cross-contamination
between adjacent samples.
Several standard racks for the system are
designed to hold 6–77 individual sample
containers made of glass, quartz, or
TFM™ (Dyneon GmbH & Co. KG,
Burgkirchen, Germany). Recognizing
that many laboratories have integrated
particular autosampler vials into their
routine sample handling, the manufacturer
can usually fabricate a custom rack
to accommodate customers’ vials.
Reduced acid use
The simplified sample containers in the
UltraCLAVE are not required to have
minimum volumes of process liquids merely to support accurate process
monitoring and control. As a
result, the system requires less acid
per sample than other microwave
labstations. In fact, acid volumes
can be reduced to minimum
quantities required to satisfy stoichiometry
and solubility. In addition
to considerable long-term
cost savings, this reduces the dilution
factor of the finished solutions,
and can improve detection
limits during analysis.
The power of mixed batches
The improvement in laboratory efficiency
provided by processing samples
at higher temperatures and pressures is
easy to understand. At a higher temperature,
decomposition takes less
time. However, in many laboratories,
this will not be the most significant
advantage of using the UltraCLAVE.
Traditional closed-vessel microwave processing
proceeds by monitoring and controlling
conditions in a single reference
vessel. The assumption is made that
these parameters can be duplicated in all other vessels that are processed simultaneously
along with the reference vessel.
In order for this to be true, the sample
type, sample mass, the volume of acid,
and the performance of all the other vessels
must be identical to that in the reference
vessel. In the UltraCLAVE, the traditional
process monitoring and control
strategy is not necessary, since no single
vessel is selected as the reference. Instead,
uniform temperature conditions are
achieved by positioning all the individual
sample vessels in a pool of microwave
absorbing fluid, a microwave “load.” It is
the effective temperature of this load that
is monitored and controlled throughout
the heating process in the system.
By eliminating the traditional process
control strategy, chemists are no longer
constrained to process batches of identical
samples using identical sample
chemistries. To the extent that all the
samples in a batch will process satisfactorily
under the same temperature conditions,
many dissimilar samples and
chemistries can be combined in a single
run in the UltraCLAVE. For example,
processing four different sample types—such as soil, cement, wood chips, and vegetation—would require four separate processing
cycles in a traditional microwave
labstation. For the reasons described
above, it requires only one cycle in the
UltraCLAVE. This transformation—of a
sequential process into a parallel one—may prove to be the greatest source of
increased efficiency in many laboratories.
The safety of a sealed, high-pressure
environment is ideal for processing dangerous
samples such as hazardous
waste, toxic substances, or radioactive
materials. Semiautomated operation
and complete computer control allow
the system to be adapted for remote
operation within special enclosures.
Simplicity of operation
The system engineers have operated on
the principle that great power need not
translate to great complexity. The UltraCLAVE is designed for clarity of interaction
and simplicity of use. Loading a rack
of samples into the chamber is the only
manual operation required and can be
done in a single motion. After that, methods
are initiated with push-button simplicity
(Figure 5) and automation does the rest
of the work, ensuring reproducible performance
from run to run. The reaction
chamber is sealed, pressurized, heated,
cooled, vented, and opened all under
computer control. As a result, the system reduces the need for labor compared to
conventional microwave systems.
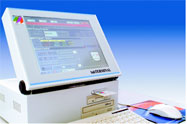
Figure 5 - LabTerminal. Reaction parameters are
entered via an intuitive touch-screen controller.
Sequence of operation
First, a rack of individual reaction containers
is secured to the reactor cover in a
single motion. (In an automated laboratory
environment, even this one manual
step could be adapted to occur without
operator involvement.) Then, under
computer control, the reaction chamber
lifts up to dock with the cover, creating a
pressure seal that is secured in place by
steel clamps. Once the chamber is sealed,
a high-performance compressor pressurizes
the system with nitrogen. A
microwave program, controlling temperature,
pressure, and/or microwave power
versus time, is then selected and initiated
via the control terminal (see Figure 6).
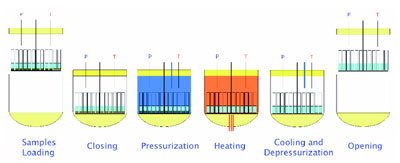
Figure 6 - UltraCLAVE operating sequence.
During the run, integrated sensors continuously
monitor and display the internal
pressure and sample temperature.
The UltraCLAVE software dynamically
adjusts the applied microwave power in
real time to precisely follow the defined
temperature profile.
At the completion of the heating process,
the reactor and its contents are cooled by
an integrated chilling unit, causing most
process vapors to condense in the reactor
chamber. Once the reactor is cooled, the
pressure inside the reactor is released, and
the remaining process vapors are safely
exhausted. Only after ambient pressure is
reached will the sealing clamps release.
The reactor body is then lowered, and the
finished samples can be removed.
Design details and specifications
The high-pressure steel reactor has an
overall volume of 4.2 L, and an effective
working volume of 3.5 L with the
PTFE liner installed. This is the
largest-volume single reaction vessel
available to microwave chemists.
Microwave energy from the system’s
magnetron is introduced into the
reactor through a patented microwave
port. The internal geometry of the
reactor is optimized for direct
microwave coupling to materials in
the reactor, with zero reflectance of
energy back to the magnetron. This
focused-multimode cavity design
ensures maximum sample heating efficiency.
Heat generated in the reactor
is removed by a recirculating coolant
system, and the stainless steel vessel
remains at approximately room temperature
throughout the entire
heating cycle.
Operating pressures up to 200 bar (2940
psi) and temperatures up to 280 °C can
be routinely achieved and sustained in
complete safety. Such performance can
resolve outstanding limitations in current methodology while continuing to
provide all the advantages of existing
microwave techniques.
Applications
- Materials testing. When testing materials
for RoHS Directive compliance,
the UltraCLAVE can accommodate
the entire range of sample types subject
to the regulation, due to its flexible
temperature and pressure capabilities.
Its large-volume reactor and
choice of sample holders make it
suitable for digesting components,
finished products, or raw materials.
Its ability to digest mixed batches
allows a variety of components to be
processed at the same time.
- Polymers. A fundamental part of polymer
QA/QC is the need to digest or
extract large sample masses, since the
polymer analyst typically wants to process
as few samples as possible while
still obtaining a representative analysis.
Larger samples inevitably mean
that higher pressures are generated in a
closed vessel. Traditional closed-vessel
techniques can successfully digest up
to 1 g of polymer sample in a highpressure
vessel; the most efficient
high-pressure rotors can accommodate
up to 10 such samples per processing
run. The UltraCLAVE can digest
25–30 g, distributed among multiple
vessels. As in a benchtop microwave,
magnetic stirring can be used to prevent
sample clumping and promote
complete, trouble-free digestions.
- Homeland security. The sooner analyses
can be completed in homeland security
applications, the sooner critical
decisions can be made. With the
Ultra CLAVE, varied materials such as
environmental samples, tissues, suspect
materials, and residues can all be processed
in a single run, and the speed of
the instrument used for analysis will
become the limiting factor, rather than
the speed of sample preparation.
- Remediation. On a cleanup site,
time in the field is money. But it is
not enough to increase the
turnaround time for just one type of
sample. Soils, sand, cement, organics,
and a host of other materials all
come into the laboratory at once to
be prepared for analysis. The Ultra-CLAVE can handle these samples
simultaneously—in batches of up to 77 mixed samples, with minimal
dilution, and rapidly.
- Clinical. In the cost-competitive world
of clinical analysis, every penny matters.
The push-button simplicity and
reproducibility of microwave methods,
the reduced usage and disposal of
acid, and the freedom from operator
exposure have always been attractive.
The UltraCLAVE provides these
advantages, and can simultaneously
digest multiple sample types (blood,
urine, feces, hair), reduce acid usage
even further, and process more samples
in less time, reducing a laboratory’s
daily operating costs.
- Environmental. In a busy environmental
laboratory, sample preparation is always
the bottleneck that determines how
much analytical work can be done. The
UltraCLAVE can handle large batches
of samples in a variety of types—soils,
vegetation, drinking water, wipes, and
swipes—with faster turnaround, with
no loss of volatiles and no vapor pollution
of the laboratory or environment.
Example
Goessler and Majeron1 have reported
their work processing environmental and
clinical Standard Reference Materials
(SRMs), demonstrating accuracy, precision,
and uniformity of results with large
batch processing (35 or more individual
samples) in the UltraCLAVE. Samples
were prepared with 250 mg sample mass
and 5 mL nitric acid in each sample vessel.
Figure 7 shows the graphical display of
the temperature–pressure–power versus
time profiles. Samples were brought to
the required target temperature of 250 °C
and digestion was completed in less than
1 hr heating time.
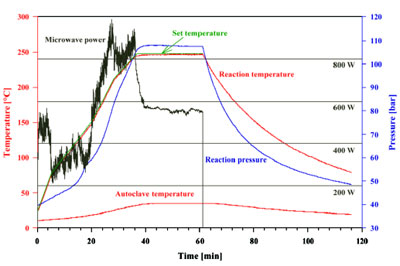
Figure 7 - Graphical display of the temperature–pressure–power versus
time profiles.
Figure 8 shows that the recoveries of the
elements of interest are in excellent agreement
with the expected values from a
National Research Council of Canada
(NRCC) SRM: Dorm-2. Of particular
note is the quality of the data for As, Hg,
and Se. One can see that there is no loss of
volatile elements or cross-contamination
in the UltraCLAVE when using the
loose-fitting vessel covers and prepressurization
technique.

Figure 8 - Recoveries of elements of interest.
Large batches of environmental samples,
at least 35 or more (up to 77) at a
time, can be effectively processed in the UltraCLAVE with very high quality.
Figure 9 shows the recoveries from a
GBW* SRM: Human Hair. Again, the
data for As, Hg, and Se are in good
agreement with the expected values.
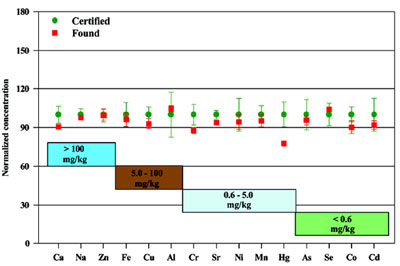
Figure 9 - Recoveries from a GBW SRM: Human Hair.
High-throughput clinical laboratories
can be assured of quality sample preparation
using the UltraCLAVE. It is also
of value to note that only 5 mL of acid
was used digesting each sample. This
minimized the dilution factor, decreased
the consumption of expensive acids,
and reduced the cost of waste disposal.
Conclusion
The UltraCLAVE performs beyond the
current limitations of traditional
microwave sample preparation. It offers
all the advantages familiar to microwave
users—speed, sample purity, reproducibility,
and no pollution of the laboratory
or environment—while overcoming
the restrictions that have forced some
laboratories to reluctantly use other
digestion methods. Chemists can digest
large sample masses (even of organics),
large batches of mixed sample types, and
difficult sample matrices requiring sustained
high temperatures. Cross-contamination
between samples does not occur.
Extremely high throughput can be
achieved. Reduced acid usage, consumables,
and need for labor all provide long-term
cost-savings. The instrument is safe
for hazardous samples and simple to operate.
It increases the capabilities of closed-vessel
microwave sample preparation.
Reference
- Poster presentation. “35 at Once! Mineralization of Biological Materials With the Milestone AutoCLAVE.” Goessler, W.; Majeron, G. Institute of Chemistry, KFU Graz, Austria.
Dr. Borowski is Application Laboratory Manager,
and Mr. Schoenfeld is a Marketing Associate,
Milestone Inc., 25 Controls Dr., Shelton,
CT 06484, U.S.A.; tel.: 866-995-5100; fax:
203-925-4241; e-mail: [email protected].
*GBW are reference materials produced
by the National Research Centre for Certified
Reference Materials.