It is no secret to researchers who homogenize
tissue samples as part of their regular laboratory
routine that the job can be messy and
loud, and produce results that are sometimes
inconsistent. To improve the laboratory work
experience, Omni International
(Marietta,
GA) took a fresh look at the factors that
matter most to those who use homogenizers.
These factors include sample processing
results, repeatability, ease of cleaning, cross-contamination
concerns, product noise, time,
ease of use, product weight (for handheld
applications), reliability, the need for sharing
equipment in the laboratory, and environmental
impact.
This analysis resulted in the creation of
Whisper
Drive Technology™, which is built
into the Omni THQ, UltraShear, and Omni
Prep product lines. The Omni THQ is a lightweight handheld tissue homogenizer. Omni
UltraShear homogenizers use magnetic drive
technology to process a variety of sample sizes. The
Omni Prep is a multisample homogenizer that can
homogenize up to six samples at a time. The products
make traditional rotor-stator homogenization
more productive and more comfortable for the user.
Tissue homogenization is most commonly and easily
achieved using mechanical shear homogenizers,
also known as rotor-stator homogenizers. They
generally consist of a motor and a processing probe
or generator probe. Rotor-stator generator probes
are usually composed of a tube and collar assembly,
shaft, knife, and an upper and lower bearing. The
rotating knife comprises the rotor portion of the
rotor-stator generator probe. The tube and collar
assembly attaches to the motor housing, but does not
spin, and is therefore called the stator. As the knife
spins within the stator, it creates a pumping action
that pulls liquid into the open end of the generator
probe. The probe then forces the liquid out through
windows in the stator portion of the generator probe.
The interaction of the knife with these windows sets
up a shearing action, much like a pair of scissors. It thereby works to reduce the particle size of sample
being forced through the windows.
The vast majority of today’s rotor-stator homogenizers
are powered by motors that require carbon
brushes to make them operate. This technology has
been around for many years, and while it is quite
suitable for occasional use, it has a number of drawbacks
when compared to Whisper Drive Technology
brushless motors.
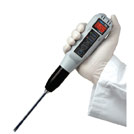
Figure 1 - Omni THQ digital tissue homogenizer.
Brushless motors are significantly more efficient than
their brush motor counterparts. For instance, the
Omni THQ (see Figure 1) with brushless Whisper
Drive Technology uses 80% less electricity to drive
a 7-mm generator probe than does the traditional
brush motor Omni TH model. The motor itself is
significantly smaller and lighter, allowing the THQ
to weigh only 10.8 oz (306 g), or 66% of the weight
of the standard Omni TH. These motors also run
much quieter, allowing the THQ to be 80% quieter
than the TH when both are running at 35,000 rpm.
This sound level is roughly equivalent to the sound
of a moderate rainfall. Furthermore, since no brushes
are used, no carbon dust is created. Like all of the
Whisper
Drive products, the motor is maintenance-free,
which makes it more convenient for the user
and results in a longer product warranty.
Another benefit of Whisper Drive Technology is
that the motor consistently runs at its set speed. A
brush motor’s speed will fluctuate as sample viscosity
changes, or as sample particle size varies, affecting
repeatability and accuracy. However, the Whisper
Drive motors are able to hold their speeds throughout
the entire operating cycle. Accuracy and repeatability
are ensured when the motors are coupled with
a digital speed readout, as with the THQ, UltraShear
M, and Omni Prep.
Another development that complements two of the
Whisper Drive homogenizers are the Omni Tip™
plastic generator probes (patent no. 6,398,402 and
6,863,431). Prior to Omni Tips, rotor-stator probes
were almost exclusively constructed from stainless
steel. These stainless steel probes can cost from
$700 to well over $1000. They can consist of six or more parts, including two wearable bearings
that require regular maintenance. Disassembly
for cleaning and subsequent reassembly
generally require one or more tools, and usually
take much longer than it actually takes
to homogenize the sample. This cleaning step
often has to be applied between each processed
sample. Omni Tips, on the other hand,
consist of only two pieces, have no bearings,
and disassemble and reassemble in seconds.
There are no hidden areas in which leftover
sample can hide. This not only facilitates
cleaning, but also reduces the potential for
sample loss during processing. To ensure that
the entire sample is fully recovered, the stator
portion of each probe is clear and the sample
always remains visible. Patented shaft geometry
further ensures that sample is not lost in
the shaft while processing. While Omni Tips
reduce cleaning time, and are in fact autoclavable,
there are some applications that simply
cannot tolerate any cross-contamination.
For these applications, the probes are inexpensive
enough to be disposed of after use.
In many research laboratories, equipment is shared
among a number of co-workers. As previously mentioned,
stainless steel probes are both very expensive
and very fragile. The fact that they are opaque
makes it impossible to determine if they are clean
without actually disassembling and reassembling the
probe. Lack of cleaning after use can actually lead
to product failure due to corrosion, and a dropped
probe can bend the stator, making it nonfunctional.
These problems are easily resolved when using Omni
Tip plastic probes. Since they cost less than 1% of
stainless steel probes, multiple users can own their
own probes, which can be autoclaved or chemically
cleaned for repeated use. In addition, if an Omni Tip
is dropped from a tabletop, it still works like new.
For laboratories that process five, ten, or more samples
per day, the tedium of cleaning between sample
processing can be completely eliminated. The low
cost of Omni Tips allows multiple probes to be purchased.
Rather than cleaning stainless steel probes
after each homogenizing step, all samples can be
processed, and the probes can be collected for batch
cleaning at the end of the work period.
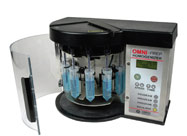
Figure 2 - Omni Prep multisample homogenizer.
The Omni Prep multisample homogenizer (see Figure
2) takes full advantage of the benefits of Omni
Tips. It uses Whisper Drive Technology to process
up to six samples simultaneously. Sample tubes and
Omni Tips are loaded onto a specially designed processing
rack, similar in concept to a centrifuge rotor,
and then processed all at once, again much like in a centrifuge. This saves time and significantly reduces
energy costs, since less than 10% of the power
required to process six samples individually with a
traditional brush motor homogenizer is required to
process six samples simultaneously with the Omni
Prep. The homogenizer is also suitable for sharing.
As with a multisample centrifuge, an Omni Prep in
the laboratory can elevate productivity and improve
work flow.
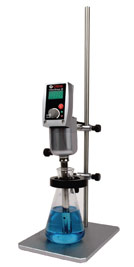
Figure 3 - Omni UltraShear M magnetic homogenizer.
While the THQ and Omni Prep are designed to
handle sample volume of 1.5 mL to 50 mL, the
UltraShear
M (see Figure 3) was designed to quietly
process up to 2 L of sample. Its patented drive
technology is not only brushless, but also magnetic.
The rotating shaft of the generator probe actually
becomes part of the motor itself. This magnetic
coupling eliminates all coupling noise or wear,
but most importantly makes the generator probe
a completely sealed assembly, ensuring that there
is no possible path for escape of sample or aerosol
for critical sealed sample processing. Also, like
other Whisper Drive products, the UltraShear’s low
power usage makes it more ecofriendly than traditional
homogenizers, while its quiet motor makes it
more researcher friendly.
Mr. Jahn is President, Omni International, Inc., 1000 Williams
Dr., Ste. 1024, Marietta, GA 30066, U.S.A.; tel.:
800-776-4431; fax: 770-421-0206; e-mail: [email protected].