The story of biofuels begins with biomass. Simply stated, biomass is any plant or animal material of recent origin, as opposed to plant or animal material that, over millennia, has transformed into oil, coal, tar sands, natural gas, or other petroleum products. Biomass materials are remarkably versatile, and have been used throughout the history of civilization. Early humans, for example, used wood biomass as a fuel for fire, and clothes have been made from cotton fiber biomass for centuries.
Today, however, biomass is taking on a truly revolutionary role, inspiring new industries dedicated to providing the energy we need without harming the environment. Fuels made from a variety of biomasses are already viable supplements—or alternatives—to petroleum-based fuels, which continue to increase in price and rely on a dwindling supply of crude oil. The basic process for this emerging industry is illustrated in Figure 1.
Figure 1 – Generic biofuels production process.Although governmental interest in biofuels can be traced back to the oil embargo of the 1970’s, the current story begins with the 2007 State of the Union Address of President George Bush, where he introduced his vision for taking America toward energy independence with his “Twenty-in-Ten” initiative aimed at reducing gasoline consumption by 20% in 10 years. Congress acted on his plan by passing the Energy Independence and Security Act of 2007, which provided a federally supported structure meant to foster creation of a commercial biofuels industry. The law establishes a renewable fuel standard (RFS), which mandates that the fuel supply contain 36 billion gallons of biofuel per year by 2022 while capping corn ethanol at a maximum of 15 billion gallons; this leaves a gap of about 21 billion gallons to be filled by cellulosic ethanol or other advanced fuels.
In effect, Congress mandated into law a $20–30 billion industry that did not exist and for which the technology required to produce the product had not been developed! To support the legislation, the Department of Energy began issuing research grants to create the required technology; some of the biofuels supported by these grants are shown in Table 1.
Table 1 – Biofuels supported by Department of Energy grants
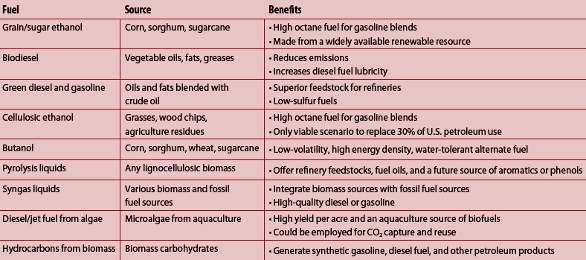
The commercial ethanol industry
According to the National Renewable Energy Laboratory, more than 80% of the first-generation corn ethanol used as fuel is made by a dry milling process in which the entire corn kernel is ground into flour referred to as “meal.” Water, enzymes, and ammonia are then added to form a slurry for conversion of the starch to dextrose. The mixture is processed at high temperatures to reduce the bacteria levels and is then cooled in fermenters prior to addition of the yeast to convert sugar to ethanol and carbon dioxide. This entire process takes between 40 and 50 hours, during which time the mash is kept cool and agitated in order to facilitate yeast activity. After fermentation is complete, the mixture is transferred to distillation columns, where the ethanol is removed and dehydrated to near 200 proof using a molecular sieve system. A denaturant such as gasoline is added to render the product undrinkable, after which it is quality certified for shipment to gasoline retailers or terminals. The solid material that remains is processed into livestock feed.
Second-generation biofuels made from lignocellulosic feedstocks can be produced by either a biochemical process or a thermochemical process. The biochemical process uses enzymes and microorganisms to convert cellulose and hemicellulose to sugars prior to fermentation to produce ethanol. A biological, physical, chemical, or a combination pretreatment process is required to expose the cellulose and hemicelluloses for subsequent enzymatic hydrolysis. The pretreatment process is a major cost component of the overall process and is the focus of much of the current R&D. A key goal for the efficient production of lignocellulosic ethanol is that all C5 (pentose) and C6 (hexose) sugars released during the pretreatment and hydrolysis steps are fermented into ethanol. Currently, there are no known natural organisms that have the ability to convert both C5 and C6 sugars to produce high ethanol yields, although progress has been made in engineering microorganisms for the co-fermentation of these sugars. Thermochemical processes employ pyrolysis/gasification technologies to produce a synthesis gas (CO + H2) from which a wide range of long-carbon-chain biofuels such as synthetic diesel, aviation fuel, or ethanol can be reformed using the Fischer–Tropsch conversion.
The commercial biodiesel market
The process for production of biodiesel involves three basic steps—feedstock pretreatment, transesterification, and product purification. The first step simply removes dirt, charred food, water, or other contaminants that could interfere with the reaction process. The clean feedstock is then mixed with sodium or potassium hydroxide and either ethanol or methanol, where it undergoes the transesterification reaction that converts lipids to biodiesel and glycerol. If the feedstock oil has a high acid content, acid-catalyzed esterification can be used to react fatty acids with alcohol to produce biodiesel, but this process is much rarer. In either case, the reaction produces not only biodiesel, but also byproducts such as soap, glycerol, excess alcohol, and trace amounts of water. All of these byproducts must be removed to meet the fuel standards prior to sale.
Emerging technologies
While biodiesel and ethanol made through well-established technologies currently dominate the industry, companies using novel approaches are appearing. Many of these companies are based on synthetic biology, which is the application of engineering principles to biology by cataloguing DNA sequences and assembling them into new genomes to tailor organisms for fuel production. LS9 of San Carlos, CA, is one such company that uses microbes to make fuel and then excrete it as a one-step conversion of sugar to fuel that can then be processed by standard refinery operations. Gevo (Englewood, CO) uses an engineered E. coli microbe to produce isobutanol.
Another technology under development utilizes chemical processes for conversion of biomass to biofuel. Virent Energy Systems (Madison, WI) has a joint venture with Royal Dutch Shell (The Hague, The Netherlands) to convert sugars to nonoxygenated hydrocarbons using a catalyst/reactor system. Codexis of Redwood City, CA, customizes enzymes to perform chemical processes not found in nature using a process known as molecular breeding.
Biofuels laboratories
Laboratories supporting the commercial biofuels industry generally perform three functions—evaluate biomass quality, provide data for control of the transformation process, and certify quality of the finished product.
The quality of the biomass feedstock often determines the market value as well as the processing conditions required for conversion to fuel. Lab reception testing may determine fat or oil content, sugar, protein, or other aspects of the material needed to determine fair market value or to defi ne processing strategy. In-process testing tracks the state of the conversion to fuel by monitoring reactant and product concentrations at various points in the process. For example, chromatography might be used to determine the concentration of the various sugars released in the pretreatment of the biomass as well as track concentrations in the fermentation or other conversion process.
Finally, before a biofuel can enter the nation’s fuel supply, it must be certified to meet quality standards to ensure that it does no harm to vehicles. The primary standard for ethanol is ASTM D4806, “Standard Specifi cation for Denatured Fuel Ethanol for Blending with Gasolines for Use as Automotive Spark-Ignition Engine Fuel.” For biodiesel, ASTM D6751, “Standard Specification for Biodiesel Fuel Blend Stock (B100) for Middle Distillate Fuels,” as well as a number of European standards, are applicable.
Conclusion
The biofuels story is an old one but is still just at the beginning. The storyline revolves around an interesting convergence of emerging science, public policy, and entrepreneurship. The way this story unfolds over the next several years will ultimately determine the future of energy in this country and touch the life of every citizen. So, stay tuned for the next chapter.
Wayne Collins, Ph.D., is World-Wide Marketing Manager, Energy & Chemicals, Agilent Technologies, Chemical Analysis Group, 2850 Centerville Rd., Wilmington, DE 19808, U.S.A.; tel.: 281-750-1763; e-mail: [email protected]; www.agilent.com.