Commercial testing laboratories that offer services for trace metals analysis have realized a variety of potential growth opportunities given the current passing of various local and international regulations aimed to minimize environmental and consumer exposure to certain metals. However, these opportunities do not come without their own set of challenges, since laboratories must maintain competitive analysis fees while addressing increased throughput demands and developing methods to successfully prepare and analyze a wide variety of sample matrices.
A well-recognized and effective technique employed by testing labs for trace metals analysis requires acid digestion of samples in a closed-vessel microwave system followed by elemental analysis by inductively coupled plasma-optical emission spectroscopy (ICP-OES) and inductively coupled plasma-mass spectrometry (ICP-MS). Compared to more traditional digestion techniques, such as hot plate and hot block, microwave technology enables chemists to perform acid digestions of a variety of matrices at much higher temperatures and pressures. These factors maximize data quality and minimize sample turnaround time.
New approach to microwave sample digestion
Traditional microwave digestion systems using individual pressurized reactors are utilized by various laboratories and industries across the world. However, new advancements in microwave technology can greatly improve the sample preparation process for commercial testing labs and positively impact sample throughput and work flow efficiency. This technology will enable laboratories to eliminate cleaning, minimize sample handling, process difficult sample types, digest large sample sizes for detection or homogeneity purposes, and run completely mixed samples and chemistries together.
Single Reaction Chamber (SRC) technology, which is utilized in the UltraWAVE microwave system (Milestone Inc., Shelton, CT), allows the processing of up to 22 samples simultaneously at extremely high temperatures (up to 300 °C) and pressures (up to 199 bar). SRC eliminates many of the bottlenecks in commercial testing labs and facilitates complete, high-quality digestions of almost any matrix.
At the heart of the system is a single, pressurized, stainless steel chamber containing a microwave absorbing base load (usually a mixture of water and hydrogen peroxide) into which the samples are placed. This chamber also acts like a microwave cavity. The base load absorbs the microwaves, heats up, and transfers the heat to the samples by conduction. Acting like a heat sink, the base load uniformly heats all the samples to the same temperature, thus eliminating the need for heavy rotors. In other words, the temperature of the base load, monitored by a temperature probe, represents the temperature of all the samples. At the end of the digestion cycle the chamber is automatically depressurized in a controlled manner, and the gases produced during digestion are vented through the exhaust line (see Figure 1).
Figure 1 – Flow diagram of SRC operation.Sample preparation procedure
Samples can be directly weighed into disposable glass, autosampler type vials with the appropriate acid mixtures; no minimum acid quantity is required. Quartz and TFM vials can also be used, depending on the user’s application. This minimizes acid handling and transfer steps, and reduces errors due to contamination and the chemist’s exposure to acids. Also, it completely eliminates the need to clean, assemble, and disassemble vessels used in conventional microwave systems, while lowering the expenditure on consumables.
SRC technology enables the user to pre-pressurize the reaction chamber to 40 bar of pressure before microwave heating. This pre-pressurization prevents the acids from boiling and spitting, which in turn prevents cross-contamination and loss of volatiles. The sample vials are covered by loose-fitting caps that prevent condensation from the roof of the chamber from dripping into the sample. The caps ensure pressure equilibrium on either side of the vials, which makes it possible to use inexpensive, disposable glass vials at high pressures. Also, the caps eliminate the need to torque down or seal vessels, which are commonly seen in closed-vessel systems, consequently eliminating vessel assembly and disassembly steps.
Commercial testing labs often encounter samples such as polymers, oils, and pharmaceutical products that have a high organic content and generate pressure due to the formation of CO2 and NOx gases in large quantities. In closed-vessel systems, digestion of such samples requires special rotors and vessels capable of withstanding pressures up to at least 100 bar. The high-pressure capability of the SRC microwave allows much higher sample weights to be digested in small amounts of acid.
A typical microwave program for the SRC systems involves a ramp to 240 °C over 20 min and a hold at that temperature for another 20 min. After completion of the digestion run, a cooling line that surrounds the reaction chamber rapidly cools the samples, as opposed to air-cooling mechanisms adopted by conventional closed-vessel systems. This drastically reduces the time between two digestion cycles.
Figure 2 – Results from a digestion run.Figure 2 shows an actual run performed on the UltraWAVE SRC microwave system. The red line denotes the temperature profile of the run with the actual temperature data, monitored 20 times per second, superimposed on it. The yellow line represents the power delivered by the magnetron. Power is automatically fluctuated using advanced proportional integral derivative (PID) controls from 0 W to 1500 W with 1-W increments to adhere to the temperature profile set by the user. The blue line indicates the pressure profile of the system, and the green line the external temperature of the reaction chamber.
Turnaround time calculation for samples takes into consideration the times required for vessel assembly, disassembly, cleaning, digestion cycle, and cooling times.1Figure 3 illustrates a run time comparison of high-density polyethylene (HDPE) digestions in a high-pressure rotor of a closed-vessel microwave versus the UltraWAVE and number of samples processed in each system in an 8-hr shift. It is evident from the figure that the UltraWAVE is twice as productive as the high-pressure rotor due to the complete elimination of the assembly and disassembly steps and much faster cool-down times. Figure 4 shows the same data for plant material digestion performed in a high-throughput, 24-position rotor versus the UltraWAVE. Despite the higher-capacity closed-vessel rotor, the UltraWAVE is still 1.5 times more productive.
Figure 3 – Polymer samples (time comparison + number of sample comparison – high-pressure rotor versus UltraWAVE).
Figure 4 – Plant material (time comparison + number of sample comparison – high-pressure rotor versus UltraWAVE).
Figure 5 – 15-position rack with glass vials.Table 12 illustrates the analytical data obtained after digesting 0.5 of St. John’s wort tablet in 4 mL HNO3 and 1 mL HCl and 1 g of fish oil gel cap (entire capsule) in 10 mL HNO3 and 1 mL HCl. For the digestion, 15 samples were digested simultaneously using 15-mL disposable glass vials (see Figure 5). Note that since different matrices are digested in the same run, the temperature required to digest the most difficult matrix was selected as the operating temperature for the run. Clean product was obtained after the run, and was diluted to 100 mL and analyzed for As, Cd, Pb, and Hg using an Agilent 7700x ICP-MS (Agilent Technologies, Palo Alto, CA).3
The ICP-MS was validated and operated in the helium collision mode.1 To test for recoveries, duplicate quality control samples were run and the third aliquot was spiked. A reagent blank was also spiked (laboratory fortified blank). The quantitative data, 3-sec detection limits, and QC data are shown in Table 1.
Table 1 – Analytical data and spike recoveries for St. John’s wort and fish oil capsules
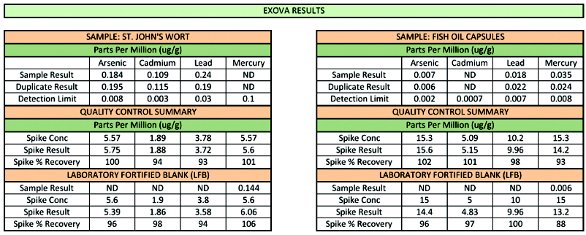
The values (expressed as μg/g or ppm) shown in Table 1 indicate that good spike recoveries were obtained. The pre-pressurization of the reaction chamber prevents cross-contamination, boiling/spitting of acids, and loss of volatile elements. This is evident from the high recoveries of Hg obtained during the process.
Conclusion
SRC microwave technology will be an extremely effective tool in a commercial testing lab environment that receives hundreds of different samples per day. Its ability to process multiple samples, irrespective of its matrix simultaneously at high temperatures and pressures, significantly increases productivity. The use of inexpensive disposable glass vials eliminates the need to clean, assemble, and disassemble vessels, which is required with conventional closed-vessel microwave systems. Autosampler type disposable vials also eliminate handling and transfer steps and the chemist’s exposure to acids and reagent blanks. High digestion quality and convenience of use make SRC microwave technology an intelligent choice for sample preparation.
References
- Michel, T. Am. Lab. 2010, 42(11), 32–5.
- Michel, T.; Hussain, S. Spectroscopy Supplement: Application of ICP & ICP-MS Techniques for Today’s Spectroscopists Nov2012, 4.
- Hussain, S.; Liba, L. et al. Spectroscopy Supplement: Application of ICP & ICP-MS Techniques for Today’s Spectroscopists, Nov2011, 14.
Sumedh Phatak, M.S., is Applications Chemist, Milestone Inc., 25 Controls Dr., Shelton, CT 06484, U.S.A.; tel.: 866-995-5100; e-mail: [email protected].