Innovation is a respected attribute that many companies claim as a core business strategy. Apple, for example has shown to be an effective driver of business through technology innovation in the consumer goods segment. The pace of innovation spurred by technology such as smartphones, tablet PCs, and high-speed internet has changed the way we live our lives. Much of this was accomplished in the last decade, and as a result society has come to demand technical innovations that improve the quality of our lives.
A business model built on continuous innovation requires astute technical management. Companies that successfully sustain continuous innovation in the products they bring to market have certain common traits; they develop deep domain expertise in their core technologies, effectively manage talent, and foster a culture of “out-of-the-box” thinking. The management team is usually comprised of members who have risen through the technical ranks, which allows for seamless interaction with the engineers, and this simplifies the decision process. Since decisions center on the ability to predict the requirements that the current user is unaware that he or she needs, the challenge is to deliver innovations that delight both the early adopter as well as the mainstream user. While commercial success is dependent on effective execution, only a few firms gain the reputation of delivering innovation repeatedly.
Delivering innovation to the scientific instrumentation market
With technical products such as scientific instruments, innovation usually implies technical leadership. This is hard to measure for many reasons. However, peers are best able to recognize technical innovation compared to the general public. Thus, awards programs like the Pittcon® Editors Awards are recognized as providing juries of experts with training and experience to reward technical innovation in scientific instrumentation.
Successful firms know their core competency. Building an innovative product development organization requires a supporting core philosophy that motivates individuals to contribute and deliver. In highly technical products, innovators must also possess a keen sense of what is needed and why, combined with the ability to propose practical solutions.
In 2010, Bruker (Billerica, MA) acquired three product lines from Varian, including quadrupole mass spectrometers. Many industry leaders expected Bruker to quickly do a facelift and reintroduce the products under the Bruker brand. However, Bruker saw this as an opportunity to completely revamp the portfolio and introduce innovative products to a market that some believe had seen relatively few innovations in the preceding decade.
By adding new technologies such as detectors with high-speed acquisition for gas chromatographs, multilanguage touchpad consoles for GC operation, and dramatically reducing the instrument footprint of a GC-triple-quad (TQ) so that it occupied the same bench space as a previous-generation GC-single-quad (SQ), Bruker was able to deliver innovation to the market. This strategy avoided the trap of entering a mature market with products that offered little tangible user benefit, otherwise known as “me too” products. Rather, Bruker delivered an array of products such as the SCION 436 and 456 GCs, SCION GC-SQ and GC-TQ, Advance LC series, and EVOQ Elite and Qube LC-TQs, all within 28 months of acquiring the Varian assets.
With this background, I had an opportunity to interview Collin D’Silva, President of the newly formed Bruker Chemical and Applied Markets (CAM) division (Fremont, CA), to discuss how Bruker managed to accomplish this at such a blistering pace, his philosophy on innovation management, and its reduction to practice.
RLS: The acquisition of Varian’s three product lines is a tremendous opportunity, and also a need, since existing customers need technical support. How is it going?
CDS: We are very cognizant of the needs of the installed customer base. We moved quickly to integrate the staff and support programs as a primary obligation to them. This was a top priority.
RLS: What about product design? I recognize that Bruker enjoys a reputation of introducing innovative new products by pushing the technology envelope.
CDS: We knew that we had inherited a portfolio that was deep into their individual product lifecycles. Since the purchase price was low, we could afford to invest in R&D to leapfrog ahead. In short, we saw a once in a lifetime opportunity to reset the clock on the product lifecycles by significantly upgrading the product lines. We also were acutely aware of the talent pool and the gaps, which we rapidly filled, giving us the capability to bring innovation to this market segment.
RLS: There are many business models. How would you compare Bruker’s with other models?
CDS: Corporate cultures and associated business models are especially important in acquisitions. The key is to identify issues that limit performance, and then match these with innovative solutions. This process is ongoing. Other firms have similar philosophy, but Bruker excels in execution.
For example, over the last half-century, the R&D 100 Awards have highlighted innovations in laboratory technology. National laboratories were the top nine award winners. In Analytical Instruments, Bruker Corporation placed first with 18 awards out of 98 total for our segment. This year, the Photon 100 won an award for the first CMOS active pixel sensor (APS) detector for crystallography. This provides high-resolution images from high-flux X-ray sources.
Winning awards helps motivate our R&D staff by providing public confirmation of our development acumen. For investors, winning awards validates Bruker’s business model. Recognition of leadership in innovation execution is important competitively and builds customer loyalty.
LC-MS instrumentation
RLS: Recently, I attended a press conference announcing Bruker’s introduction of a new line of LC-MS instruments for quantitative analysis. Can you provide tangible examples of Bruker’s innovation philosophy?
CDS: Sure. We studied the performance of several LC-MS instruments in high-throughput analytical laboratories. We identified specific issues that delayed results and were inherently frustrating to routine high-sensitivity quantitative analysis. A big one was the bottleneck between high-throughput data acquisition and data review. Next on the list was the need to reduce the frequency of routine maintenance of the ion source, closely followed by the need to lower the total cost of ownership. We decided to alleviate these three pain points specific to the quantitative LC-MS user.
Figure 1 – The EVOQ LC-TQ uses a modular design to provide an LC-heated electrospray ionization (ESI)-triple-quad MS optimized for high-throughput quantitative analysis applications. The autosampler is on the left, the Advance LC is in the middle, and the EVOQ MS is on the right.Our R&D team addressed each one and proposed solutions. The result was the EVOQ LC-TQ, a highly optimized system that focuses on the business of quantitation. It addresses the needs of these labs for higher-capacity utilization per instrument and faster reporting, removing the downstream bottleneck. We adopted a modular design approach to provide options that best matches the required application such as HPLC or UHPLC (see Figure 1).
The MS ion source is another example where modular design is beneficial. The vacuum system can be optimized for performance but the increased vacuum requirement adds to the cost. Offering two models, the EVOQ Qube and the EVOQ Elite, solved this dilemma. The performance of the EVOQ Elite advances the state-of-the-art, while the EVOQ Qube provides performance competitive with the more advanced triple-quads currently on the market.
We solved the bottleneck between high-throughput data acquisition and data review by developing software called PACER, which uses Exception-Based Data Review to flag chromatograms that fail to meet preset method criteria. This allows the expert reviewer to focus on only those chromatograms that require further review, saving time between sample analysis and report generation.
RLS: Tell us more about the need and development of the PACER software.
CDS: High-throughput quantitation labs generate overwhelming amounts of data very quickly, and these data are only useful once they have been rigorously reviewed. While upstream automation delivered the required analytical throughput, the ability to review the large volumes of data was not addressed. So the bottleneck simply shifted downstream of the overall process of sample analysis to report generation. Consider a set of 50 pesticide residue samples screening for 100 potential pesticides. If you consider the use of internal standards, this data set will result in 10,000 potential chromatograms, each one requiring review. This is a lot to begin with, but what if there are several instruments running in parallel? The data review workload stretches human capability, and the chance of error typically increases. This is important, especially when the report is time-bound and needs to be error-free to safeguard the reputation of the lab.
PACER software is designed to alleviate the tedium of reviewing thousands of chromatograms, by using sophisticated algorithms to highlight the exceptions that fail the preset method acceptance criteria. These proprietary algorithms flag these unexpected results for expert review, appreciably improving the efficiency of the data review process. So rather than inspect over 10,000 chromatograms, the reviewer has to review only a fraction of that number, confident that the software has confirmed the veracity of those chromatograms that meet the preset method criteria. Using software to enable human efficiency is what PACER is designed to achieve, and it does it very well (Figure 2).
Figure 2 – PACER software examines each peak, including multiple reaction monitoring (MRM) results according to preestablished quality rules. Peaks with potential problems are flagged for further review.Ion sources
RLS: After 30 years, the design of ion sources still seems to be an opportunity for improvement. Please tell us more about the ion source for the EVOQ.
CDS: The atmospheric pressure interface (API) region remains the most active area of research in just about any company involved with LC-MS. Sensitivity improvements are a continuous research activity and these advances are made in the API area. The real challenge is designing an API ion source that can deliver sustained high sensitivity, ionize thermally labile compounds efficiently, and do all this at high flow rates while being continually exposed to harsh sample matrix.
For example, electrospray ionization (ESI) interfaces, which are the most popular subset of APIs, use hot tips that conduct heat up the tip of the interface. As thermally unstable analytes such as N-oxides transition this zone, they have time to heat up and decompose. Some peptides behave similarly. Bruker engineers designed a thin vacuum insert that impedes thermal conduction upstream from the tip. The result is an ESI probe that gives improved detection sensitivity of the parent analyte rather than the degradation product (Figure 3).
Figure 3 – A layer of vacuum between the ESI probe heater and capillary thermally insulates the column effluent. This reduces overheating and associated analyte degradation before the nebulization process, improving detection of N-oxides, etc.
Figure 4 – Ions from the ESI cloud are routed to the Orifice Interface and on to the Dual Ion Funnel, while the uncharged sample matrix races to the Active Exhaust.RLS: What about the ion funnel?
CDS: Bruker was one of the first to pioneer the use of ion funnels in commercial LC-MS, so there was a wealth of experience in our Bremen and Billerica development groups. That allowed us to push the design envelope by incorporating the advantages of existing ion funnels, while ensuring high-transmission despite continual exposure to harsh matrix. Our customers demand a robust LC-MS system, and the ion funnel technology enhancements were integral to meeting these requirements as they are closely coupled to the API improvements (see Figures 4 and 5).
Liquid chromatograph line
RLS: I see that Bruker has developed a new line of liquid chromatographs.
CDS: Our goal is to provide complete solutions to our users and central to that strategy was the acquisition of the Michrom LC business in April 2011. This allowed us to develop analytical flow liquid chromatographs to augment our LC-triple-quads at product launch. The fluid path engineering was well characterized as it was based off the successful Paradigm product from Michrom. This allowed us to develop LC systems with very low dwell volumes, which is important for high-throughput applications, as was the selection of the PAL autosampler.
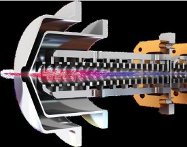
F
igure 5 – The single-axis design of the first-stage quadrupole and ion funnel facilitates ion transfer without tuning. This greatly reduces the need for tuning and response variability between instruments.In terms of developing solutions, the on-line extraction version, called the Advance UHPLC OLE, has an extra pump module within the same cabinet. The flexibility that such a system affords the user is significant because of the gain in productivity. They can use one LC-MS system to do preconcentration or to do on-line extractions without additional equipment. The instrument footprint remains, and developing instruments that are optimized for bench space is a basic design element of our products. You can see this in the SCION GC-MS family launched last year.
The future of analytical instrumentation
RLS: Where do you see analytical instrumentation in 10 years?
CDS: We have seen a trend toward more technologies being combined into a single platform, which requires a higher level of training of the users. However, as the emerging markets become a major segment of demand, we will need to provide simpler instrumentation with lower cost of ownership. Software innovation is key to making highly sophisticated scientific instruments easier to use, and the industry will have to adapt to deliver hardware as well as software solutions.
Robert L. Stevenson, Ph.D., is a Consultant and Editor of Separation Science for American Laboratory/Labcompare; e-mail: [email protected].