In an environment literally covered in microorganisms, keeping cell cultures contaminant free is both challenging and essential. Cells being cultured can be rare, expensive, or both; media and related reagents are costly; the work involved in growing cells is important and time consuming; and keeping cultures free of contaminants is imperative to an experiment’s validity.
Beyond sterility, the stability of the environment in which cells grow is vital to the long-term success of any culture process. Chamber temperature, the percentages of gases and their distribution within the chamber, and pH are all interdependent and must stay within proscribed limits to keep cells healthy and proliferating.
Elimination of contamination
Complete sterilization is the only way to eliminate contamination from a CO2 incubator, and the method in which contamination is achieved is critical. CO2 incubators from BINDER Inc. (Great River, NY) provide built-in, true 180 °C sterilization, which exceeds all international standards.
The sterilization process is straightforward: At the end of a run, the user wipes up any spills that may have occurred; empties the water pan and replaces it; and, with the shelves still in place, closes the door, pushes three buttons, and walks away. After 9½ hr, the incubator is completely sterilized and ready for the next batch of cells.
Leaving the shelves in the incubator during the sterilization procedure means that there is no reassembly—a process in which the shelves are handled, sometimes by more than one person, and the door is left open; both situations present the possibility of contamination being reintroduced. It also means, of course, that the shelves are sterilized along with the rest of the interior.
By design, BINDER CO2 incubators do not incorporate HEPA filters. While somewhat effective at trapping airborne contaminants, HEPA filters then harbor the very contaminants that are trapped. They also add costs, primarily for filter replacement, which, because they retain contaminants, should be done after each run. Filter disposal costs can also add up, particularly if cultures contain highly infectious organisms. Finally, most contaminants are not airborne, and thus are not removed by HEPA filtration. It is important to note that decontamination and disinfection programs are not sufficient for sterilization, and that wiping the interior down is only as effective as the person trying to make sure that every surface is covered.
Other features that make the BINDER incubator a very effective and dependable housing for cultures include a one-piece, weld-free, deep-drawn interior that has only rounded corners, eliminating spots in which contaminants can lodge. The chamber interior is guaranteed to be condensation free, with excess moisture recondensing in the water pan.
Control of the environment
Culture plates are often located throughout the incubator—right front/top shelf, left rear/bottom shelf—and all points in between. The proliferation of healthy cells in all locations is dependent on environmental conditions remaining constant throughout the incubator over the length of the culture process. The way in which stability is accomplished, monitored, and maintained is integral to unit performance and vital to culture success.
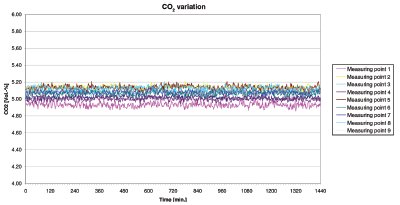
Figure 1 - A 5% CO2 setpoint is virtually drift-free over 24 hr.
Figures 1 and 2 detail CO2 levels in a BINDER CB series incubator. CO2 is a necessary gas for many cultures, but if CO2 percentages are out of balance, culture pH changes, resulting in an environment that is either too acidic, or one in which ammonia can form, either of which is deadly to cells. CO2 was monitored for the tests shown in Figures 1 and 2 using nine sensors placed throughout the chamber. The infrared sensors were dedicated to the measurement of CO2. The sensors operate independently of other gases and are not affected by humidity levels.
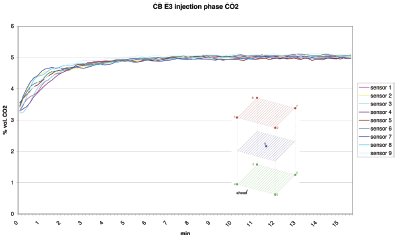
Figure 2 - CO2 recovery after a 30-sec door opening.
Figure 1 is a graph of a 5% CO2 setpoint, measured by nine sensors, and showing virtually drift-free conditions over a 24-hr period. Figure 2 depicts CO2 measurement in the chamber after a 30-sec door opening. CO2 distribution is homogeneous while it is being reintroduced, and recovery time is very fast once the door is closed.
A number of other features included in the incubators facilitate temperature uniformity. Foremost among these is the APT.LINE™ preheating chamber. Air in the chamber is blown over heating elements and around the culture compartment, allowing for uniform temperatures and fast recovery times. Because the heating elements never make contact with the walls of the unit, there are no hot spots in the chamber.
During manufacturing, BINDER uses a quality control process that adheres to the German Industrial Standard, or DIN, which is much more stringent than the ASTM standards used by most manufacturers. After heating a newly made incubator to steady state over a 2-hr period, temperature is sampled six times a minute at 27 points throughout the chamber. This means that scientists using a BINDER CO2 incubator can be confident in the unit’s performance and the environment provided for their cells.

Figure 3 - CO2 incubator in the BINDER CB Series. The unit’s double doors, seam and weld-free interior, perforated shelves, and water pan are visible.
A double-latch locking system tightly seals doors. This design facilitates quick return to setpoint for temperature and CO2, and is so effective that researchers report CO2 use dropping considerably when they switch to a BINDER incubator, reducing both costs for gas and the loss of this greenhouse gas. Figure 3 shows the interior of a BINDER CB Series CO2 incubator.
Summary
BINDER incubators offer such standard features as an LCD screen, real-time clock, self-diagnostics, computer interface, perforated shelves, and gas-mixing head. However, the environmental control and sterilization features truly distinguish the units. Weld-free, seamless interiors with integrated shelf support; condensation-free humidification; drift-free CO2 measurement provided by dedicated infrared sensors; and standard, compliant, 180° hot-air sterilization all combine to provide the most closely controlled environmental conditions for cell culture.
Mr. Craig is Senior Regional Sales Manager, BINDER Inc., 3500 Sunrise Hwy., Ste. D214, Great River, NY 11739, U.S.A.; tel.: 631-224-4340; fax: 631-224-4354; e-mail: [email protected].